- お役立ち記事
- Basics, applications, and practical points of statistical quality control (SQC)
月間76,176名の
製造業ご担当者様が閲覧しています*
*2025年3月31日現在のGoogle Analyticsのデータより
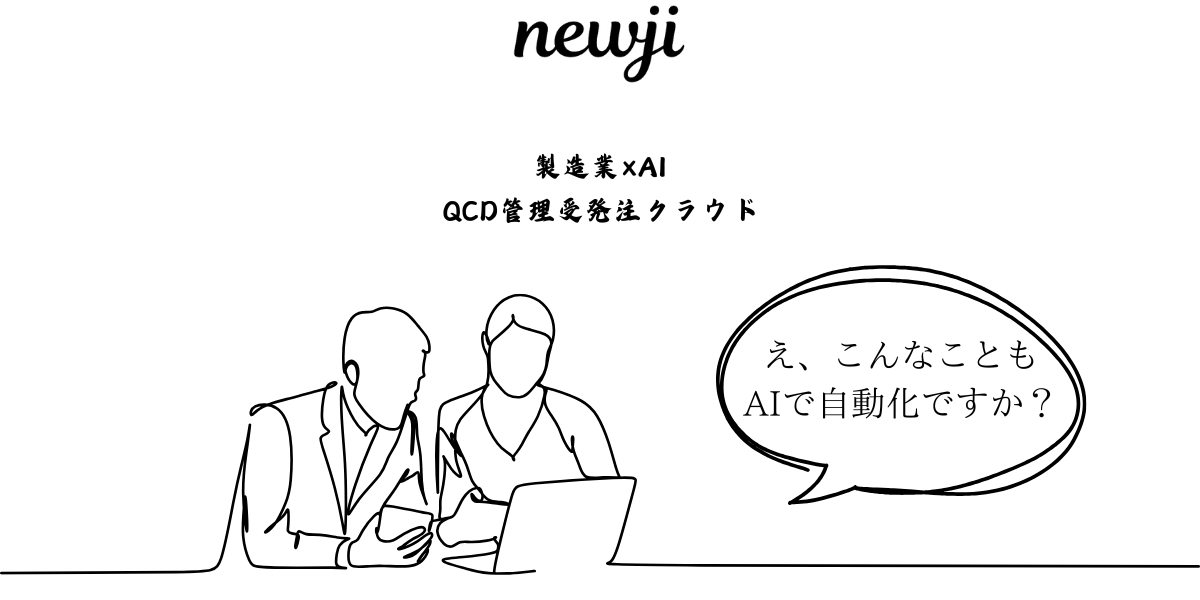
Basics, applications, and practical points of statistical quality control (SQC)
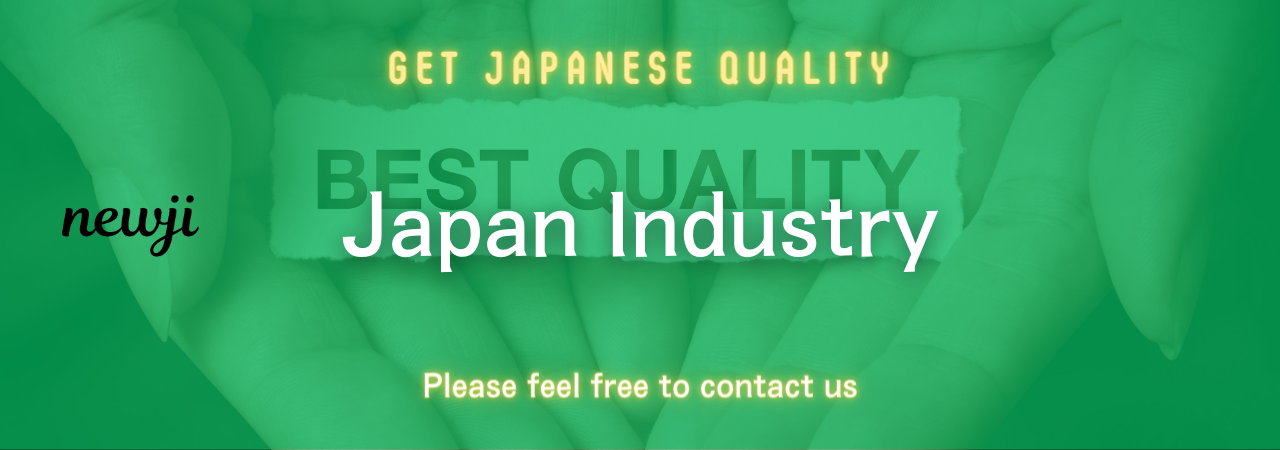
目次
Understanding Statistical Quality Control (SQC)
Statistical Quality Control (SQC) is a method used extensively in various industries to ensure the quality of products and processes.
SQC involves the use of statistical methods to monitor and control a process.
The aim is to identify any deviations from the normal process that could lead to defects or variations in the final output.
By maintaining consistency in the process, companies can achieve higher quality standards and improve customer satisfaction.
The Basics of SQC
At its core, SQC is about using statistics to manage quality.
It relies on the collection and analysis of data to understand the performance of a particular process.
The main components of SQC include descriptive statistics, control charts, and acceptance sampling.
Descriptive statistics help in summarizing data and provide an overview of what’s happening in the process through measures like mean, median, mode, and standard deviation.
Control charts are tools that graphically display data over time to monitor process stability.
They help in identifying trends or any signs of variation that needs immediate correction.
Acceptance sampling is a process where a random sample of goods is checked for defects as a decision-making tool for either accepting or rejecting a batch of products.
Applications of SQC
SQC is used in various industries to improve product and service quality.
In manufacturing, for instance, SQC methods are employed to keep production processes in check and minimize defects in products.
This becomes crucial for sectors like automotive, electronics, and pharmaceuticals where precision and reliability are paramount.
In the service industry, SQC can be applied to ensure customer service processes like call handling, ticketing, and support services remain efficient and consistent.
By using SQC in service industries, companies can enhance customer satisfaction by reducing wait times and error rates.
In healthcare, SQC is crucial to ensure the delivery of safe and effective services.
Through the analysis of patient data and hospital processes, SQC helps in reducing errors and improving patient care.
Practical Points for Implementing SQC
Implementing SQC in an organization requires some practical considerations.
First, it’s essential to establish clear quality objectives that align with the company’s goals.
The involvement of both management and employees is crucial, as the success of SQC depends on collective effort and commitment.
Selecting the right statistical tools and methods is another practical step in implementing SQC.
Different processes might require different methodologies, and it is important to tailor your approach to suit the needs of your process.
Training staff in SQC techniques is vital.
Employees should be well-versed in the statistical methods and tools of SQC so they can efficiently monitor and control quality.
Regular audits and reviews of the SQC processes should be conducted to ensure the methods applied are effective and achieving the desired results.
The data collected through SQC should be used to drive continuous improvement across all processes in the organization.
The Benefits of Using SQC
There are numerous benefits experienced by companies that implement SQC.
The most significant advantage is the reduction in the variability and defects in products.
By maintaining a consistent process, the organization delivers high-quality products, leading to satisfied customers and improved sales.
SQC also helps in reducing waste within processes.
By identifying and eliminating sources of variation, companies use resources more efficiently, which can lead to cost savings.
Moreover, organizations that implement SQC can make informed decisions based on reliable data.
This data-driven approach facilitates proactive measures to prevent issues before they occur rather than merely reacting to problems.
Challenges in SQC
Despite its benefits, there are challenges associated with SQC.
The most common challenge is reluctance to change.
Implementing SQC could mean significant changes to established procedures, and not all employees may embrace these changes readily.
Another challenge is the complexity of statistical tools, which may seem daunting to individuals unfamiliar with statistics.
The provision of adequate training and resources can mitigate these challenges and increase acceptance and effectiveness of SQC methodologies.
Lastly, maintaining updated and accurate data is crucial but can be challenging.
Organizations must invest in reliable data collection methods and technology to ensure the data used in SQC is relevant and precise.
Conclusion
Statistical Quality Control is a valuable practice that can transform the quality of products and services across industries.
By understanding the basics, applications, and practical points of SQC, companies can harness the power of statistics to refine processes, reduce waste, and enhance overall quality.
As with any methodology, the implementation of SQC requires commitment from all levels of an organization and a willingness to adapt.
The rewards, however, can be substantial, leading to better products, satisfied customers, and a stronger position in the marketplace.
資料ダウンロード
QCD管理受発注クラウド「newji」は、受発注部門で必要なQCD管理全てを備えた、現場特化型兼クラウド型の今世紀最高の受発注管理システムとなります。
ユーザー登録
受発注業務の効率化だけでなく、システムを導入することで、コスト削減や製品・資材のステータス可視化のほか、属人化していた受発注情報の共有化による内部不正防止や統制にも役立ちます。
NEWJI DX
製造業に特化したデジタルトランスフォーメーション(DX)の実現を目指す請負開発型のコンサルティングサービスです。AI、iPaaS、および先端の技術を駆使して、製造プロセスの効率化、業務効率化、チームワーク強化、コスト削減、品質向上を実現します。このサービスは、製造業の課題を深く理解し、それに対する最適なデジタルソリューションを提供することで、企業が持続的な成長とイノベーションを達成できるようサポートします。
製造業ニュース解説
製造業、主に購買・調達部門にお勤めの方々に向けた情報を配信しております。
新任の方やベテランの方、管理職を対象とした幅広いコンテンツをご用意しております。
お問い合わせ
コストダウンが利益に直結する術だと理解していても、なかなか前に進めることができない状況。そんな時は、newjiのコストダウン自動化機能で大きく利益貢献しよう!
(β版非公開)