- お役立ち記事
- Basics of 5-axis machining center technology and measures to improve machining accuracy: Machining accuracy inspection technology and appropriate use of CAM
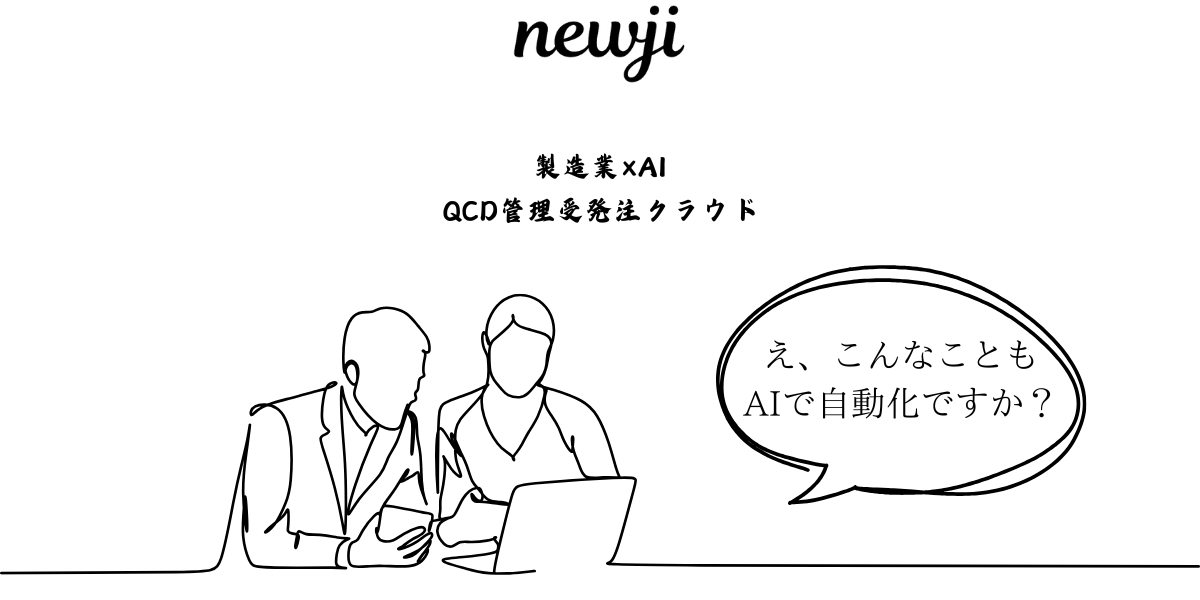
Basics of 5-axis machining center technology and measures to improve machining accuracy: Machining accuracy inspection technology and appropriate use of CAM
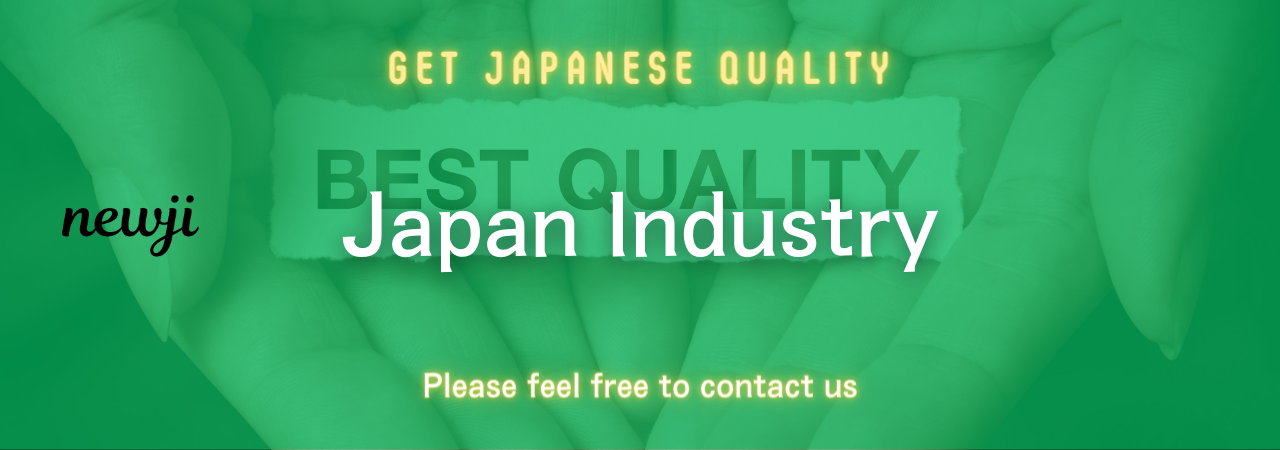
目次
Understanding 5-Axis Machining Center Technology
5-axis machining centers represent a pinnacle of precision engineering in the manufacturing industry.
These advanced machines allow for the production of intricate parts and components with superior accuracy and efficiency.
Unlike traditional 3-axis machines, which operate along three linear axes (X, Y, and Z), 5-axis machines introduce two additional rotary axes.
This added capability allows the tool to approach the workpiece from virtually any direction.
The key advantage of using 5-axis machining lies in its ability to perform complex geometries in a single setup.
This reduces time-consuming setups and enhances the quality of the parts produced by minimizing misalignments.
The additional axes facilitate contouring and surfacing, which is essential for industries such as aerospace, automotive, and mold-making.
As a result, manufacturers can produce high-quality products faster and with greater precision.
Components and Operation
A 5-axis machining center typically consists of a spindle that moves along three linear axes, and a table or a trunnion that tilts or rotates the workpiece.
The tilting table aligns itself in relation to the rotational axes, enabling the cutting tool to machine from any angle.
This configuration allows for a wide range of movements, giving manufacturers significant flexibility when crafting complex designs.
Operation of a 5-axis machine requires a sophisticated controller that synchronizes all five movements.
Machinists often rely on Computer-Aided Manufacturing (CAM) software to develop toolpaths and program the machine.
CAM software calculates the optimal path for the cutting tool, taking into account the rotational and tilting capabilities of the machine, ensuring efficient and precise machining.
Improving Machining Accuracy
The accuracy of a 5-axis machining center is critical, especially for industries where the smallest discrepancies can lead to costly errors.
Achieving high levels of precision requires a combination of technological measures and best practices.
Calibration and Maintenance
Regular calibration of the machine ensures that it operates within the desired tolerance levels.
Calibration involves setting the zero points and checking the alignment of the rotary and linear axes.
Using laser calibration systems, manufacturers can detect minute deviations and adjust them accordingly.
Furthermore, consistent maintenance schedules are essential for maintaining the machine’s accuracy.
This includes lubrication of moving parts, checking for wear and tear, and ensuring that the software and firmware are up to date.
Thermal Management
Thermal expansion is a significant concern in machining.
Temperature changes can lead to distortions in both the machine and the workpiece, affecting precision.
To counteract this, many modern 5-axis machining centers come equipped with temperature control systems.
These systems use cooling fluids or refrigerated air to maintain a stable temperature during operation.
Additionally, manufacturers may employ thermal compensation algorithms that adjust the machine’s settings in response to temperature fluctuations, ensuring consistent accuracy.
Tool Selection and Usage
Choosing the right cutting tools is crucial for machining accuracy.
The material of the tool, its geometry, and coating all contribute to its efficiency in cutting.
For 5-axis machining, high-performance tools with appropriate rake angles and sharpness are preferred as they provide better control and reduce chatter during operation.
Proper tool management, including regular inspection and replacement, prevents defects in machining and prolongs machine life.
It is also essential that operators use the tools at recommended speeds and feeds to prevent overheating and tool wear.
Inspection Technology
Inspection technology plays a vital role in verifying the accuracy of machined parts.
By comparing the finished product against design specifications, manufacturers can identify discrepancies and adjust processes accordingly.
Coordinate Measuring Machines (CMM)
CMMs are the most widely used inspection tools in manufacturing.
These machines use probes to measure the physical geometries of objects and compare them to digital models.
CMMs provide accurate data on dimensions, angles, and surface profiles, helping to identify deviations from design specifications.
Optical and Laser Scanning
In recent years, optical and laser scanning technologies have gained popularity for inspection purposes.
These non-contact methods allow for rapid data collection and analysis without physically touching the part.
Laser scanners are particularly useful for inspecting complex shapes and free-form surfaces, providing point clouds that can be converted into 3D models for comparison.
Appropriate Use of CAM
CAM software is integral to 5-axis machining, as it determines the toolpaths based on the CAD (computer-aided design) model.
Using CAM effectively can significantly enhance machining accuracy.
Optimized Toolpaths
CAM software is responsible for generating toolpaths that guide the cutting tool during machining.
For optimal accuracy, it’s crucial to use software that allows for multi-axis calculations and simulations.
Software should also provide collision detection and avoidance, minimizing the risk of damage to the tool and workpiece.
Simulation and Verification
Before machining begins, simulations can predict the outcome by replicating the toolpaths in virtual environments.
Operators can verify and modify these paths to avoid errors, reduce setup times, and ensure a successful outcome.
By combining simulations with real-time feedback and monitoring during the machining process, manufacturers can continually adjust parameters to enhance precision.
In conclusion, mastering 5-axis machining center technology involves understanding machine components, improving accuracy through calibrated methods, implementing advanced inspection techniques, and utilizing CAM software effectively.
These measures collectively enable manufacturers to produce high-quality parts with impressive accuracy and efficiency, remaining competitive in a demanding industry.
資料ダウンロード
QCD調達購買管理クラウド「newji」は、調達購買部門で必要なQCD管理全てを備えた、現場特化型兼クラウド型の今世紀最高の購買管理システムとなります。
ユーザー登録
調達購買業務の効率化だけでなく、システムを導入することで、コスト削減や製品・資材のステータス可視化のほか、属人化していた購買情報の共有化による内部不正防止や統制にも役立ちます。
NEWJI DX
製造業に特化したデジタルトランスフォーメーション(DX)の実現を目指す請負開発型のコンサルティングサービスです。AI、iPaaS、および先端の技術を駆使して、製造プロセスの効率化、業務効率化、チームワーク強化、コスト削減、品質向上を実現します。このサービスは、製造業の課題を深く理解し、それに対する最適なデジタルソリューションを提供することで、企業が持続的な成長とイノベーションを達成できるようサポートします。
オンライン講座
製造業、主に購買・調達部門にお勤めの方々に向けた情報を配信しております。
新任の方やベテランの方、管理職を対象とした幅広いコンテンツをご用意しております。
お問い合わせ
コストダウンが利益に直結する術だと理解していても、なかなか前に進めることができない状況。そんな時は、newjiのコストダウン自動化機能で大きく利益貢献しよう!
(Β版非公開)