- お役立ち記事
- Basics of “5S activities” for new employees—Creating an orderly work environment sought by management
Basics of “5S activities” for new employees—Creating an orderly work environment sought by management
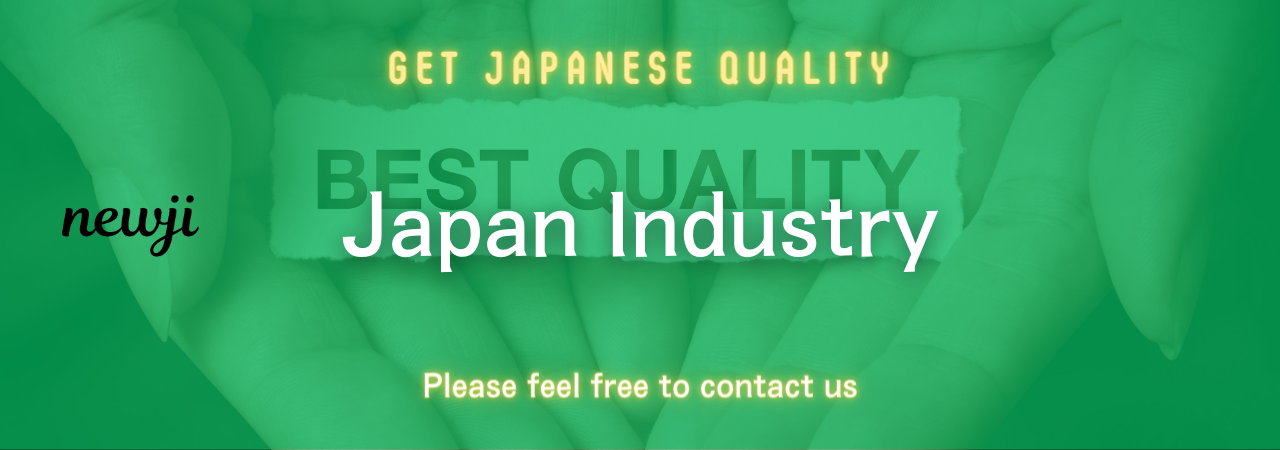
Creating an organized and efficient workplace is crucial for any organization looking to enhance productivity and employee satisfaction.
For new employees, understanding and implementing the basics of “5S activities” is an essential step in cultivating a disciplined and orderly work environment.
These activities not only improve workflow but also contribute to a safer and more pleasant workplace.
This article delves into the fundamentals of 5S activities and explains how they can be effectively applied by new employees for the benefit of both themselves and their organization.
目次
What Are 5S Activities?
5S is a methodology originating from Japan, primarily used in manufacturing but applicable to any environment, aimed at organizing and managing workspace efficiently.
The term stands for five Japanese words: Seiri, Seiton, Seiso, Seiketsu, and Shitsuke, which translate to Sort, Set in order, Shine, Standardize, and Sustain.
These principles focus on creating an organized workplace that emphasizes safety, efficiency, and productivity through systematic organization.
Seiri (Sort)
The first step, Seiri or Sort, involves separating and sorting necessary items from unnecessary ones.
New employees can begin by evaluating their workspace and identifying which tools, materials, and equipment are essential for everyday tasks.
Items that do not serve a current function should be discarded or stored away.
This process reduces clutter, frees up space, and enhances the overall efficiency of the work environment.
Seiton (Set in Order)
Once sorting is complete, the next step is Seiton, or Set in order.
This involves arranging important items in a logical order to optimize accessibility and workflow.
New employees should ensure that frequently used items are easy to reach and that their workspace promotes an effortless working process.
Labels and color-coding can be used to help maintain this order, creating a visually organized setup that saves time and minimizes errors.
Seiso (Shine)
Seiso, or Shine, revolves around cleanliness and maintaining a tidy environment.
This step encourages new employees to regularly clean their work areas, tools, and equipment to prevent build-up of dust and grime.
A clean workspace not only looks professional but also reduces the risk of accidents and equipment malfunctions.
Implementing a daily or weekly cleaning routine ensures a high standard of hygiene and keeps the environment conducive to productive work.
Seiketsu (Standardize)
Seiketsu, or Standardize, entails establishing standard operating procedures and protocols to ensure consistency in maintaining the first three steps.
New employees can benefit from clear guidelines and checklists that make it easy to integrate 5S activities into their daily routine.
Standardization helps prevent backsliding and ensures everyone in the organization follows the same procedures, fostering a culture of uniformity and discipline.
Shitsuke (Sustain)
The final step, Shitsuke or Sustain, emphasizes discipline and commitment to maintaining the 5S principles over time.
Sustainability requires continuous effort and dedication to uphold the established standards and routines.
Regular training sessions and audits can help reinforce the importance of 5S activities and encourage employees to consistently apply them.
Encouraging a sense of ownership and responsibility among new employees will help them internalize the 5S mindset, ensuring long-term success.
Benefits of 5S Activities for New Employees
Implementing 5S activities offers numerous benefits, especially for new employees as they adapt to a new work environment.
Firstly, an organized workspace improves efficiency by reducing the time spent searching for tools and materials.
This leads to quicker turnaround on tasks and projects.
A clutter-free environment also enhances focus and reduces stress, allowing employees to concentrate on their tasks without distractions.
Additionally, 5S activities increase safety by reducing hazards and accidents in the workplace, which is particularly important for new hires who may not yet be familiar with potential risks.
Enhanced Communication and Teamwork
5S activities promote better communication and teamwork among employees.
When everyone follows the same organizational principles, it creates a cohesive work environment that facilitates collaboration.
New employees can easily integrate into teams when they understand and apply the 5S methodology, leading to smoother coordination and improved team dynamics.
Professional Development and Growth
Engaging in 5S activities aids in professional development by instilling good habits and practices.
New employees who learn these techniques early in their careers can carry these skills forward, enhancing their professional growth and adaptability in different work settings.
Additionally, demonstrating proficiency in 5S principles can set them apart as valuable assets to their organization.
Implementation Challenges and Solutions
While the benefits of 5S activities are clear, new employees may face challenges in implementation.
Some may struggle with habitually maintaining the practices or encounter resistance from others who are not yet committed to the process.
To overcome these challenges, organizations should provide robust training and support for new hires.
Assigning mentors or 5S champions who can model and guide new employees through the process can be highly effective.
Regular feedback and recognition of effort can also motivate continuous improvement and adherence to 5S practices.
Conclusion
For new employees, embracing the basics of 5S activities is a crucial step in contributing to an organized and efficient workplace.
By understanding and implementing the principles of Sort, Set in order, Shine, Standardize, and Sustain, they can foster a conducive work environment that enhances productivity, safety, and communication.
The skills and habits cultivated through 5S methodologies not only benefit individual employees but also strengthen the overall performance of the organization, making it a valuable asset for success in today’s competitive landscape.
資料ダウンロード
QCD調達購買管理クラウド「newji」は、調達購買部門で必要なQCD管理全てを備えた、現場特化型兼クラウド型の今世紀最高の購買管理システムとなります。
ユーザー登録
調達購買業務の効率化だけでなく、システムを導入することで、コスト削減や製品・資材のステータス可視化のほか、属人化していた購買情報の共有化による内部不正防止や統制にも役立ちます。
NEWJI DX
製造業に特化したデジタルトランスフォーメーション(DX)の実現を目指す請負開発型のコンサルティングサービスです。AI、iPaaS、および先端の技術を駆使して、製造プロセスの効率化、業務効率化、チームワーク強化、コスト削減、品質向上を実現します。このサービスは、製造業の課題を深く理解し、それに対する最適なデジタルソリューションを提供することで、企業が持続的な成長とイノベーションを達成できるようサポートします。
オンライン講座
製造業、主に購買・調達部門にお勤めの方々に向けた情報を配信しております。
新任の方やベテランの方、管理職を対象とした幅広いコンテンツをご用意しております。
お問い合わせ
コストダウンが利益に直結する術だと理解していても、なかなか前に進めることができない状況。そんな時は、newjiのコストダウン自動化機能で大きく利益貢献しよう!
(Β版非公開)