- お役立ち記事
- Basics of accelerated reliability testing and how to proceed efficiently
月間76,176名の
製造業ご担当者様が閲覧しています*
*2025年3月31日現在のGoogle Analyticsのデータより
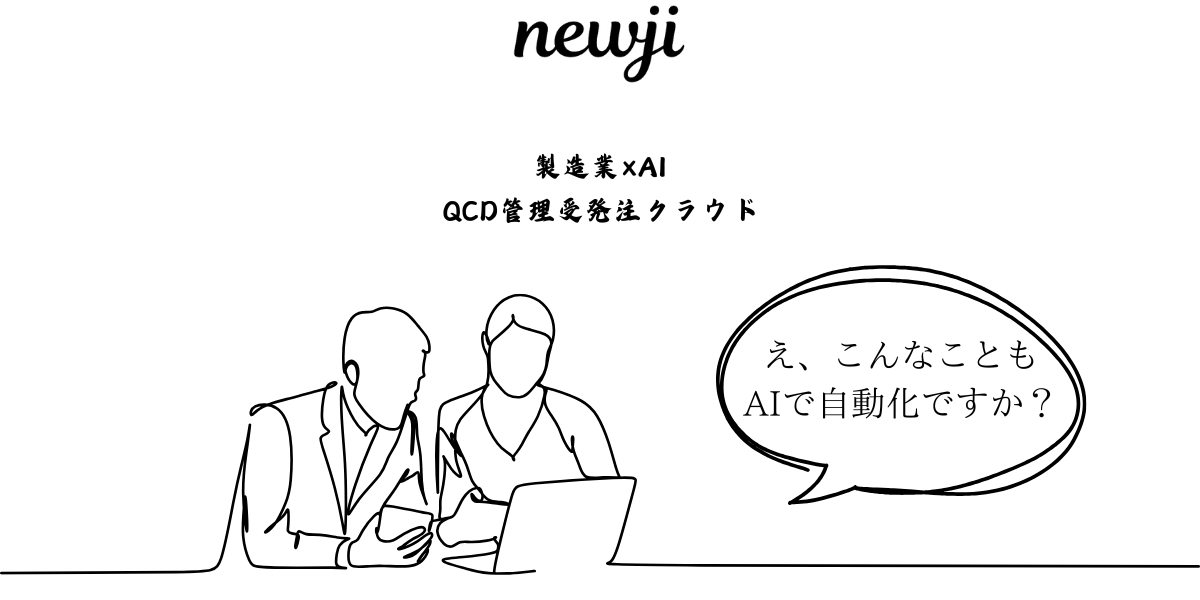
Basics of accelerated reliability testing and how to proceed efficiently
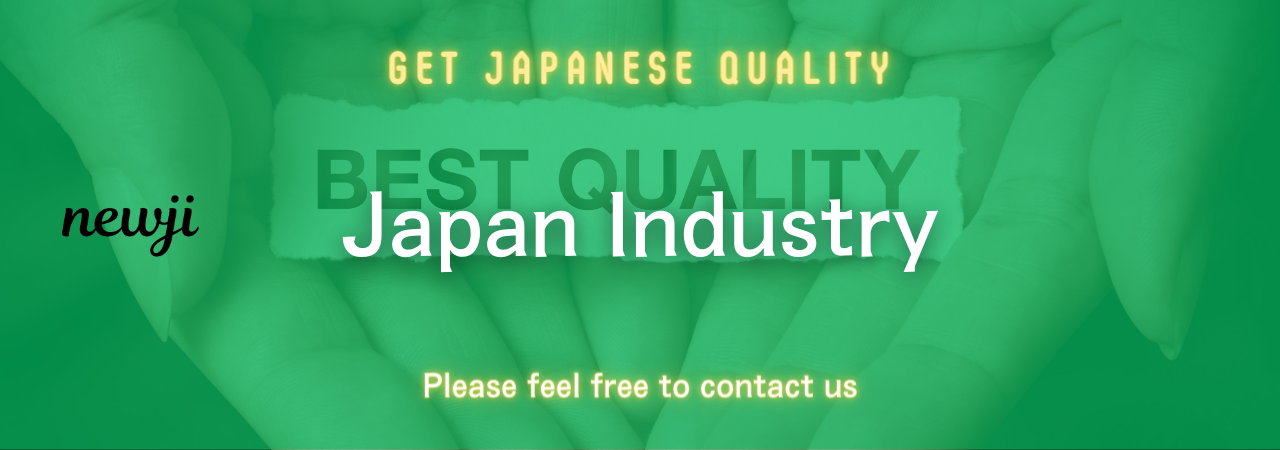
目次
What is Accelerated Reliability Testing?
Accelerated reliability testing (ART) is a crucial process used by manufacturers to ensure that their products will work reliably over time.
It involves putting products under stress to identify potential failures and weaknesses that might emerge during regular use.
This type of testing is especially important for any product expected to last a long time, such as electronics, vehicles, or industrial equipment.
Why is Accelerated Reliability Testing Important?
Reliability is a key factor for customer satisfaction and brand reputation.
If a product fails sooner than expected, it can lead to customer dissatisfaction, increased warranty costs, and harm to the company’s reputation.
By conducting accelerated reliability testing, businesses can catch potential failures early, make necessary improvements, and reduce the risk of widespread defects.
This approach helps companies save money and time in the long run by minimizing the need for recalls and repairs.
Different Types of Accelerated Reliability Testing
Accelerated reliability testing comes in various forms, each tailored to simulate different stress factors that a product might face during its lifecycle.
Understanding these types can help businesses choose the most effective testing methods for their products.
1. Accelerated Life Testing
Accelerated life testing (ALT) subjects products to increased stress conditions such as higher temperatures, pressures, or electrical loads.
This method speeds up the aging process and helps identify potential failure points before actual use.
It is widely used in industries like automotive and aerospace, where safety is paramount.
2. Highly Accelerated Life Testing (HALT)
HALT aims to find the limits of a product’s operating conditions.
It uses extreme temperatures, vibrations, and other stressors to see how much a product can endure before it breaks down.
HALT is particularly useful for spotting design flaws and understanding the ruggedness of a product.
3. Highly Accelerated Stress Screening (HASS)
HASS is used after design and development to ensure each production unit meets quality standards.
It involves testing a finished product under stress conditions but within tolerable limits.
HASS helps manufacturers confirm consistent quality across all products without causing damage.
Planning for Effective Accelerated Reliability Testing
To conduct successful accelerated reliability testing, careful planning is essential.
This involves several key steps and considerations to ensure that testing delivers valuable and actionable insights.
Define the Objectives Clearly
The first step is to establish what you want to achieve through testing.
Are you looking to identify the most common failure modes, or do you wish to test the overall durability of your product?
Clear objectives will guide the entire testing process and help in determining the appropriate testing methods.
Select the Right Tests
Based on your objectives, choose the types of tests that fit your goals.
Consider the typical operating conditions your product will face, and select stressors that accurately simulate these conditions.
Utilize methods like environmental testing if your product will face extreme weather or corrosion.
Understand the Product’s Environment
Knowing the environment in which a product will be used is essential for designing relevant tests.
Consider factors such as temperature, humidity, vibration, and dust since these can all impact product reliability.
Executing Accelerated Reliability Testing
Once planning is complete, it’s time to carry out the tests.
Efficient execution of accelerated reliability testing will involve aligning with industry standards and maintaining precision in the testing process.
Set Up Testing Equipment
Make sure you have access to the necessary equipment to simulate stress conditions accurately.
State-of-the-art testing labs often come equipped with everything needed, including environmental chambers, vibration tables, and thermal shock testers.
Follow Industry Standards
Adhering to industry standards ensures that results are credible and comparable to other products.
For example, professionals often follow ASTM or IEC standards, which provide detailed guidelines on testing procedures.
Collect and Analyze Data
Throughout the testing process, gather data meticulously.
Look for patterns, such as common failure points or stress levels that cause issues.
Analyze this data to make informed decisions about potential design changes or improvements.
Post-Testing: Utilizing the Results
The final step is to use the findings from accelerated reliability testing to enhance product quality and reliability.
Identify Failure Modes
Use test results to pinpoint common failure modes.
Understanding why and how products fail allows for targeted improvements in design and production.
Implement Design Improvements
Address any identified weaknesses by making necessary changes to product design.
Implementing these improvements ensures a more reliable product that will meet or exceed customer expectations.
Validate Changes
After making design changes, it’s important to validate these adjustments with further testing.
This ensures that modifications lead to the desired improvements in reliability.
Conclusion
Accelerated reliability testing is a vital practice for ensuring the longevity and performance of products in various industries.
Whether through ALT, HALT, or HASS, understanding the right methods and implementing strategic testing plans can vastly improve a product’s success in the marketplace.
By investing in effective testing, manufacturers can enhance customer satisfaction, reduce costs, and maintain their brand’s reputation for quality and dependability.
資料ダウンロード
QCD管理受発注クラウド「newji」は、受発注部門で必要なQCD管理全てを備えた、現場特化型兼クラウド型の今世紀最高の受発注管理システムとなります。
ユーザー登録
受発注業務の効率化だけでなく、システムを導入することで、コスト削減や製品・資材のステータス可視化のほか、属人化していた受発注情報の共有化による内部不正防止や統制にも役立ちます。
NEWJI DX
製造業に特化したデジタルトランスフォーメーション(DX)の実現を目指す請負開発型のコンサルティングサービスです。AI、iPaaS、および先端の技術を駆使して、製造プロセスの効率化、業務効率化、チームワーク強化、コスト削減、品質向上を実現します。このサービスは、製造業の課題を深く理解し、それに対する最適なデジタルソリューションを提供することで、企業が持続的な成長とイノベーションを達成できるようサポートします。
製造業ニュース解説
製造業、主に購買・調達部門にお勤めの方々に向けた情報を配信しております。
新任の方やベテランの方、管理職を対象とした幅広いコンテンツをご用意しております。
お問い合わせ
コストダウンが利益に直結する術だと理解していても、なかなか前に進めることができない状況。そんな時は、newjiのコストダウン自動化機能で大きく利益貢献しよう!
(β版非公開)