- お役立ち記事
- Basics of acoustic emission (AE) method and application technology for diagnosis of rotating machinery equipment
月間77,185名の
製造業ご担当者様が閲覧しています*
*2025年2月28日現在のGoogle Analyticsのデータより
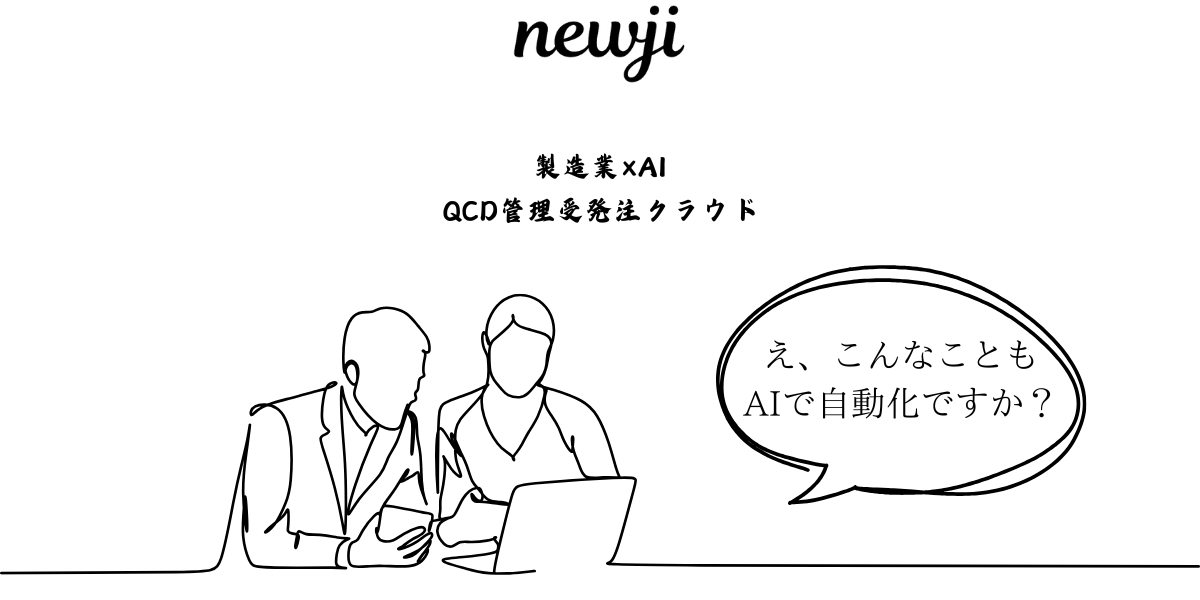
Basics of acoustic emission (AE) method and application technology for diagnosis of rotating machinery equipment
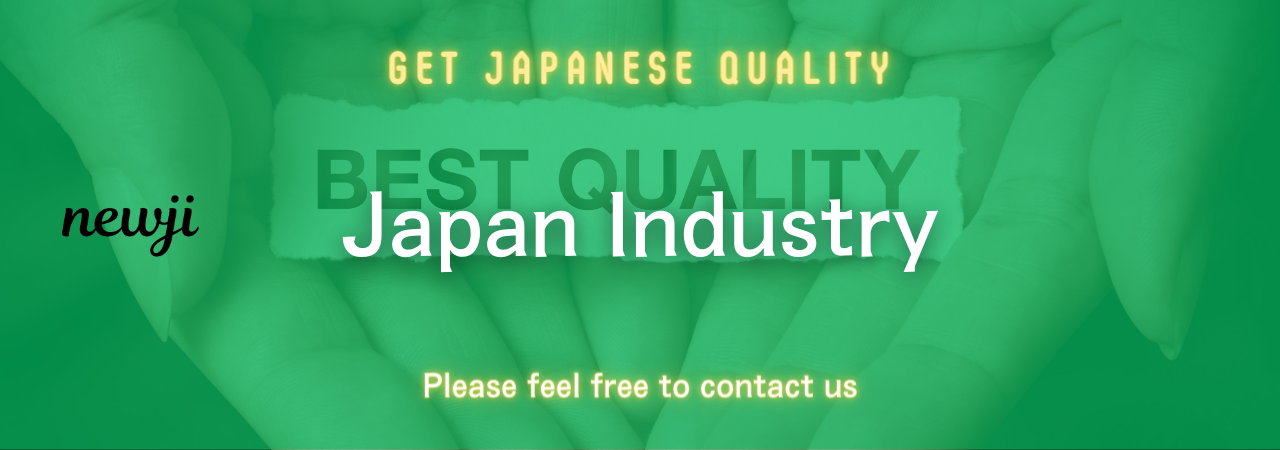
目次
Understanding the Acoustic Emission (AE) Method
The Acoustic Emission (AE) method is a non-destructive technique used extensively in the field of material and structural health monitoring.
At its core, this method relies on the detection of transient elastic waves generated by the rapid release of energy from localized sources within a material or structure.
Essentially, when a material experiences stress, it may emit acoustic waves as it attempts to release some of that stress.
These waves are then captured by sensors and analyzed for signals that indicate structural changes, damage, or the presence of defects.
AE differs from other traditional non-destructive testing methods primarily because it detects damage as it occurs rather than inspecting for existing damage.
This immediacy makes AE particularly advantageous in situations where continuous monitoring is necessary, offering the potential for real-time diagnostics and intervention.
Components of the AE Monitoring System
A standard AE monitoring system consists of several key components.
These include sensors, amplifiers, filters, data acquisition systems, and analysis software.
Sensors
AE sensors are the frontline in detecting acoustic signals.
These sensors are typically piezoelectric devices designed to be extremely sensitive to high-frequency waves.
They capture stress waves traveling through the material and convert them into electrical signals.
Placement of the sensors is crucial; they need to be positioned where transmission of crucial data is optimal.
Amplifiers and Filters
Once the sensors capture the signals, amplifiers boost these signals, making them strong enough for analysis.
Filters then come into play to sift through the noise and focus only on the relevant signal frequencies.
This ensures that unwanted background noise from the environment doesn’t skew the results.
Data Acquisition Systems
These systems collect the clean, amplified signals.
They typically use software interfaces to display the data, allowing for real-time observation and analysis.
Analysis Software
Advanced software analyzes the data to identify patterns, frequency, amplitude, and event occurrence rates.
This data helps experts assess the condition of the material or structure, and issues can be detected and diagnosed using models and algorithms specific to the AE method.
Application of AE in Rotating Machinery Diagnosis
Rotating machinery, such as turbines, compressors, pumps, and fans, are integral to many industrial operations.
Diagnosing issues in such machinery requires accurate detection methods because failures can result in substantial downtime and repair costs.
AE provides a unique advantage in these applications through its capability to detect early warning signs of failure.
Real-time Monitoring
One of the primary advantages of AE in diagnosing rotating machinery is the status of real-time monitoring.
Machinery operates under dynamic states, where loads and outputs can change rapidly.
Real-time monitoring facilitates immediate detection of anomalies, allowing operators to take corrective action before a catastrophic failure occurs.
Detection of Subtle Changes
AE enables the detection of subtle changes that may occur at an early stage of fault development.
For example, the method can detect minute changes like crack initiation in bearings, shaft misalignments, or small gear imperfections that other methods might miss until more substantial damage has occurred.
Broad Application Range
The versatility of the AE method allows it to be applied across different types of rotating machinery irrespective of size.
Its sensors can be attached to a wide array of components within the machinery, covering various materials and structural configurations.
Challenges and Considerations
While the AE method opens numerous possibilities for efficient machinery diagnostics, it is crucial to acknowledge the challenges inherent to its application.
Signal Interpretation
Interpreting AE signals can be complex and typically requires expert analysis.
Various factors, such as background noise, operational variables, and machine configurations, can complicate interpretation.
Training and experience are thus essential in deriving accurate conclusions from AE data.
Environmental Factors
The accuracy of AE signals can be affected by external environmental factors.
This includes external vibrations and temperature variations which may introduce noise into the signals, thereby affecting the reliability of the results.
Appropriate calibration and noise reduction techniques are necessary to mitigate these issues.
Integration with Existing Monitoring Systems
Integrating AE systems with existing monitoring frameworks can require significant initial investments in both time and cost.
In addition, operators must consider compatibility with other systems to ensure seamless data exchange and analysis.
The Future of AE in Machinery Diagnostics
The future for AE in machinery diagnostics looks promising, bolstered by advances in sensor technology, data analytics, and machine learning algorithms.
As sensors become more sensitive and data analysis techniques become more sophisticated, the potential for highly precise, automated diagnostics grows.
The integration of AE data with AI could lead to self-diagnosing machines that not only detect faults but also suggest corrective actions.
Conclusion
The Acoustic Emission method offers an efficient, real-time, and sensitive solution for the diagnosis of rotating machinery.
Its ability to detect even minute changes in the structural integrity of machinery ensures potential issues are addressed proactively.
Despite the challenges of signal interpretation and integration, the future of AE is bright as technology continues to evolve, offering even more robust solutions for industrial applications.
As industries strive towards greater efficiency, safety, and reduced downtime, the adoption of AE will undoubtedly grow, underscoring its importance in modern machinery diagnostics.
資料ダウンロード
QCD管理受発注クラウド「newji」は、受発注部門で必要なQCD管理全てを備えた、現場特化型兼クラウド型の今世紀最高の受発注管理システムとなります。
ユーザー登録
受発注業務の効率化だけでなく、システムを導入することで、コスト削減や製品・資材のステータス可視化のほか、属人化していた受発注情報の共有化による内部不正防止や統制にも役立ちます。
NEWJI DX
製造業に特化したデジタルトランスフォーメーション(DX)の実現を目指す請負開発型のコンサルティングサービスです。AI、iPaaS、および先端の技術を駆使して、製造プロセスの効率化、業務効率化、チームワーク強化、コスト削減、品質向上を実現します。このサービスは、製造業の課題を深く理解し、それに対する最適なデジタルソリューションを提供することで、企業が持続的な成長とイノベーションを達成できるようサポートします。
製造業ニュース解説
製造業、主に購買・調達部門にお勤めの方々に向けた情報を配信しております。
新任の方やベテランの方、管理職を対象とした幅広いコンテンツをご用意しております。
お問い合わせ
コストダウンが利益に直結する術だと理解していても、なかなか前に進めることができない状況。そんな時は、newjiのコストダウン自動化機能で大きく利益貢献しよう!
(β版非公開)