- お役立ち記事
- Basics of aluminum resistance spot welding technology and its application to joining dissimilar materials
月間76,176名の
製造業ご担当者様が閲覧しています*
*2025年3月31日現在のGoogle Analyticsのデータより
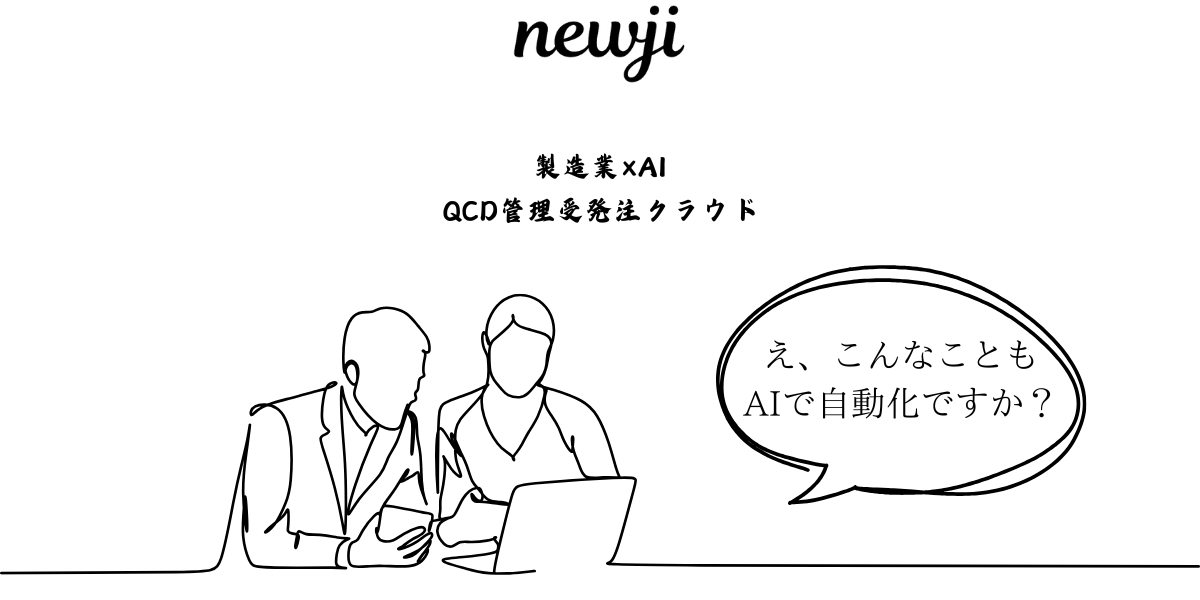
Basics of aluminum resistance spot welding technology and its application to joining dissimilar materials
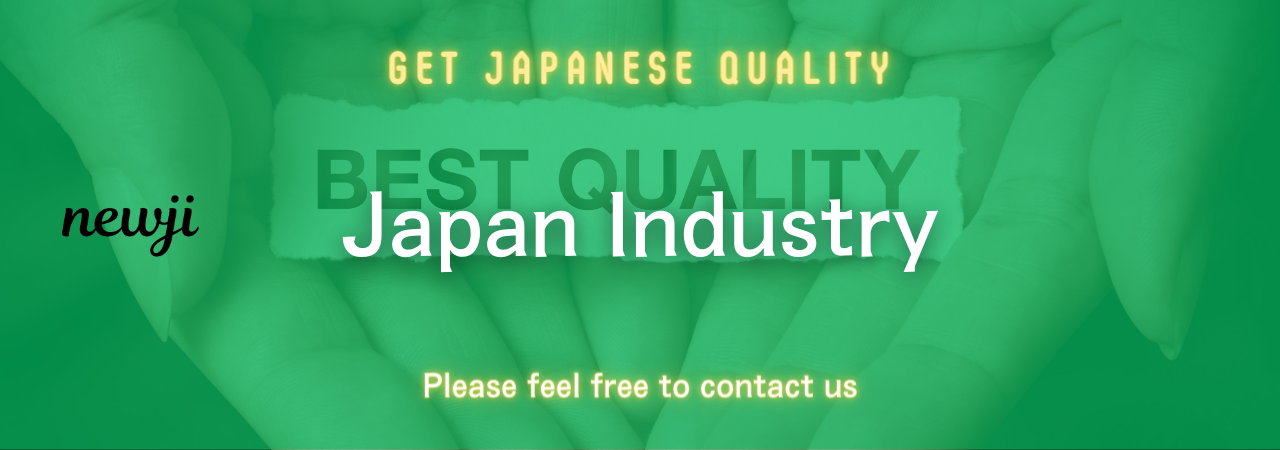
目次
Understanding Aluminum Resistance Spot Welding
Aluminum resistance spot welding (RSW) is a crucial process in various industries, including automotive, aerospace, and construction.
This technology entails joining sheets of aluminum by applying pressure and heat.
Unlike traditional welding methods, RSW doesn’t require filler materials, making it cost-effective and efficient.
The process begins with two electrodes clamping down on the sheets of aluminum.
An electric current then passes through the electrodes, generating heat at the contact points where the metal pieces overlap.
This heat causes the aluminum to melt and fuse, forming a solid nugget as it cools.
Several factors influence the success of RSW with aluminum.
These include the properties of the aluminum alloy, the thickness of the sheets, the design of the electrodes, and the parameters of the welding process such as current, time, and pressure.
Why Aluminum?
Aluminum is favored for its lightweight yet strong characteristics.
In industries like automotive and aerospace, this helps in reducing the overall weight of structures, leading to improved fuel efficiency and performance.
Furthermore, aluminum demonstrates good corrosion resistance, making it a durable choice for a wide range of applications.
However, aluminum’s high thermal and electrical conductivity presents challenges in RSW.
Unlike steel, which is more commonly used in resistance spot welding, aluminum requires higher currents for effective welding.
This is due to its ability to dissipate heat rapidly, making it more difficult to achieve the necessary heat concentration for welding.
Challenges in Aluminum Resistance Spot Welding
One of the primary challenges in aluminum RSW is its surface oxide layer.
Aluminum naturally forms a thin layer of oxide that is both thermally and electrically insulating.
This layer can hinder the welding process, preventing adequate heat generation for the weld to form.
To address this, the oxide layer must be disrupted or removed before welding.
Mechanical abrasion or chemical etching are common techniques used to ensure a clean surface.
Additionally, the welding current settings must be optimized to overcome aluminum’s high thermal conductivity.
Another challenge is the tendency for porosity and cracks to develop in welds.
Proper control of welding parameters such as time and pressure is crucial to prevent defects.
Too much pressure can lead to expulsion of molten material, while insufficient pressure may not hold the materials together adequately.
Electrode Design and Material
The design and material of the electrodes are also critical in aluminum RSW.
Copper-based electrodes are typically used, given their excellent electrical and thermal conductivity.
However, these electrodes tend to wear quickly when welding aluminum due to the high currents involved.
To extend the life of electrodes, they are often coated with specific materials, such as cobalt or a tungsten carbide coating.
The shape of the electrode tip also affects the quality of the weld, with dome-shaped or truncated cone designs common due to their ability to concentrate the welding current.
Applications of Aluminum Spot Welding
In the automotive industry, the quest for lighter vehicles with enhanced safety features is continuous.
Aluminum RSW has become integral in manufacturing car bodies and chassis, where it’s used to join aluminum sheets for doors, hoods, and other components.
In aerospace, where weight reduction is paramount, aluminum spot welding helps in assembling various parts of aircraft.
This includes fuselages, wings, and other structural components.
The ability to join aluminum without additional materials also reduces weight and potential weak points in the constructed elements.
In construction, aluminum is used for frameworks and paneling, where RSW helps in creating durable, seamless joins that withstand environmental stressors.
Joining Dissimilar Materials
With advancements in technology, aluminum RSW is also applied in joining dissimilar materials, such as aluminum to steel.
This is increasingly important in hybrid constructions seeking to take advantage of the strengths of different materials.
Joining dissimilar materials poses additional challenges due to differences in mechanical and thermal properties.
For example, the formation of intermetallic compounds at the interface can weaken the joint.
To overcome these challenges, various techniques are employed, such as using interlayers or transition materials.
These layers can mitigate the differences in properties, allowing for a more stable joint.
Advanced technologies like friction stir welding or laser welding are sometimes combined with RSW to enhance joint strength when dissimilar materials are involved.
The Future of Aluminum Resistance Spot Welding
The future of aluminum RSW looks promising with continuous research and development.
Innovations in electrode materials and design, better prediction models for weld quality, and improved automation technology are expected to enhance the capabilities and reliability of the process.
Laser-assisted RSW and hybrid welding technologies are also on the rise, addressing some limitations faced in traditional RSW, particularly with dissimilar materials.
Moreover, the development of more sustainable and environmentally friendly processes in response to global demands suggests that aluminum RSW will continue to evolve and be a key technology in manufacturing industries worldwide.
Understanding and mastering the basics of aluminum resistance spot welding, along with its challenges and applications, are crucial for engineers and manufacturers striving for lightweight, efficient, and cost-effective solutions.
As technologies advance, so will the opportunities to utilize aluminum RSW in new and innovative ways.
資料ダウンロード
QCD管理受発注クラウド「newji」は、受発注部門で必要なQCD管理全てを備えた、現場特化型兼クラウド型の今世紀最高の受発注管理システムとなります。
ユーザー登録
受発注業務の効率化だけでなく、システムを導入することで、コスト削減や製品・資材のステータス可視化のほか、属人化していた受発注情報の共有化による内部不正防止や統制にも役立ちます。
NEWJI DX
製造業に特化したデジタルトランスフォーメーション(DX)の実現を目指す請負開発型のコンサルティングサービスです。AI、iPaaS、および先端の技術を駆使して、製造プロセスの効率化、業務効率化、チームワーク強化、コスト削減、品質向上を実現します。このサービスは、製造業の課題を深く理解し、それに対する最適なデジタルソリューションを提供することで、企業が持続的な成長とイノベーションを達成できるようサポートします。
製造業ニュース解説
製造業、主に購買・調達部門にお勤めの方々に向けた情報を配信しております。
新任の方やベテランの方、管理職を対象とした幅広いコンテンツをご用意しております。
お問い合わせ
コストダウンが利益に直結する術だと理解していても、なかなか前に進めることができない状況。そんな時は、newjiのコストダウン自動化機能で大きく利益貢献しよう!
(β版非公開)