- お役立ち記事
- Basics of Anodizing in Manufacturing and its Impact on Products
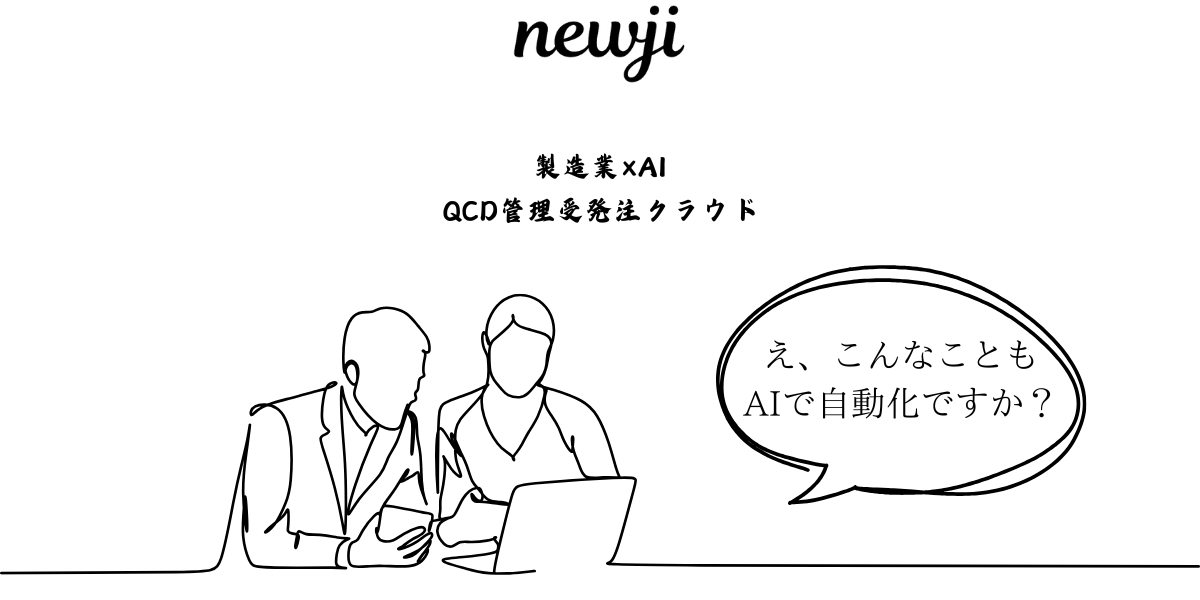
Basics of Anodizing in Manufacturing and its Impact on Products
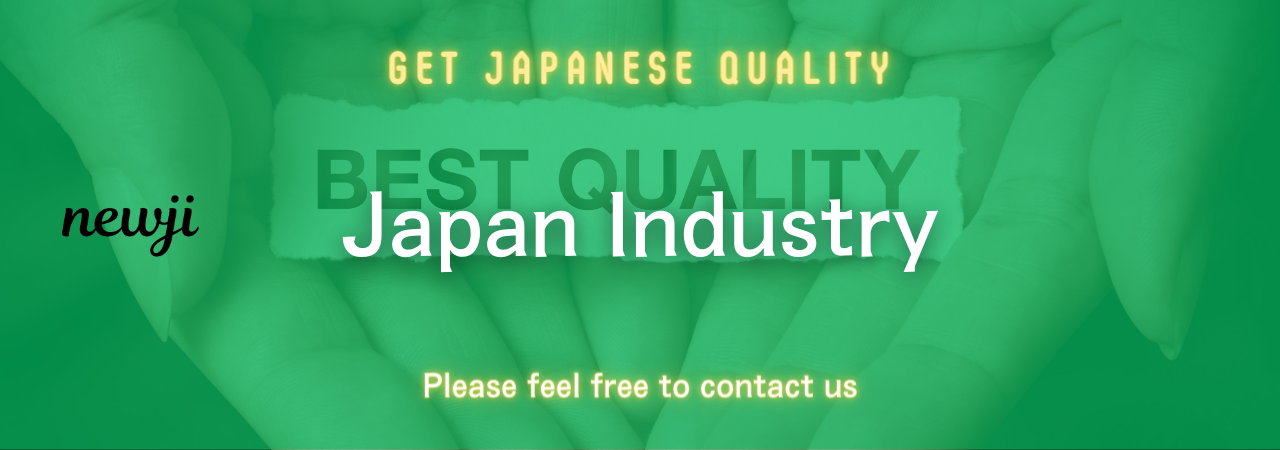
Anodizing is a widely used process in manufacturing that enhances the durability, appearance, and functionality of metal products, especially aluminum. Understanding the basics of anodizing and how it impacts various products can provide valuable insights for manufacturers, engineers, and consumers alike.
目次
What is Anodizing?
Anodizing is an electrochemical process that converts the metal surface into a durable, corrosion-resistant, anodic oxide finish. Unlike painting or plating, anodizing changes the surface of the metal rather than applying a coating to it. In this process, the metal acts as an anode in an electrolytic cell.
The Anodizing Process Explained
The anodizing process involves several key steps:
1.Cleaning:
The metal surface is thoroughly cleaned to remove any dirt, grease, or other contaminants. This ensures that the anodizing process can proceed smoothly and uniformly.
2.Etching:
The metal is then etched using an acid solution to create a rough surface. This helps improve the adhesion of the anodic oxide layer.
3.Anodizing:
The metal is immersed in an electrolytic bath, and an electrical current is passed through it. The bath contains an acid—usually sulfuric acid—that reacts with the metal surface to form an oxide layer.
4.Coloring (Optional):
After anodizing, the metal can be dyed in various colors. The porous nature of the oxide layer allows it to absorb dyes effectively.
5.Sealing:
Finally, the porous anodic oxide layer is sealed to enhance corrosion resistance and prevent fading of the dyed color. This step usually involves boiling the metal in hot water or steam.
Types of Anodizing
There are different types of anodizing, each suitable for specific applications and desired properties.
Type I: Chromic Acid Anodizing
This type uses chromic acid and produces a thin, soft oxide layer. It’s commonly used for aerospace and military applications due to its superior corrosion resistance.
Type II: Sulfuric Acid Anodizing
The most common type, sulfuric acid anodizing, provides a thicker oxide layer compared to chromic acid. It’s used in a wide range of applications, including architectural structures, automotive parts, and consumer goods.
Type III: Hard Anodizing
This method involves using sulfuric acid at lower temperatures and higher voltages to produce a very thick, hard oxide layer. It’s ideal for applications requiring wear resistance, like gears, pistons, and other mechanical components.
Applications of Anodized Products
Anodizing is employed across various industries, providing different benefits depending on the application.
Aerospace Industry
In the aerospace industry, anodized aluminum components are favored for their excellent strength-to-weight ratio and enhanced corrosion resistance. They are used in aircraft structures, engine parts, and other critical components.
Consumer Electronics
Many consumer electronics manufacturers use anodizing to create aesthetically pleasing and durable finishes on devices like smartphones, laptops, and tablets. It allows for a wide variety of colors and smooth, sleek finishes.
Architectural Applications
Anodized aluminum is frequently used in building facades, window frames, and roofing panels due to its long-lasting properties and resistance to weather conditions. It also offers an attractive and low-maintenance finish.
Automotive Industry
In the automotive sector, anodized parts include trims, wheels, and certain engine components. The process not only enhances appearance but also increases resistance to wear and corrosion, contributing to the overall longevity of the vehicle.
Advantages of Anodizing
Anodizing offers numerous benefits that make it a popular choice in manufacturing.
Durability and Corrosion Resistance
One of the primary benefits of anodizing is the increased durability and corrosion resistance of the metal. The anodic oxide layer acts as a barrier, protecting the underlying metal from environmental factors and extending its lifespan.
Enhanced Aesthetic Appeal
Anodizing allows for a wide range of colors and finishes that can be tailored to specific design requirements. This makes it an attractive option for both functional and decorative purposes.
Environmentally Friendly
The anodizing process is relatively eco-friendly compared to other finishing techniques. It produces minimal waste and uses substances that are generally less harmful to the environment.
Improved Adhesion
The porous nature of the anodic oxide layer improves the adhesion of paints, adhesives, and other coatings, making it an ideal base for additional surface treatments.
Challenges and Considerations
Despite its many advantages, anodizing also presents certain challenges and considerations.
Cost
The initial setup cost for anodizing can be relatively high, making it less cost-effective for small batches of products. However, for large-scale production, the benefits often outweigh the costs.
Process Control
Maintaining uniformity and consistency throughout the anodizing process requires precise control over various parameters, including temperature, voltage, and bath composition. Any deviation can result in defects or uneven finishes.
Environmental Concerns
While anodizing is generally eco-friendly, certain types involve chemicals, like chromic acid, that pose environmental and health risks. Proper disposal and handling of these chemicals are essential to mitigating their impact.
Future Trends in Anodizing
The field of anodizing continues to evolve, with ongoing research and development aimed at overcoming its limitations and expanding its applications.
Advancements in Anodizing Technology
Research is focused on developing new anodizing techniques and processes that offer improved performance and reduced environmental impact. For example, plasma electrolytic oxidation (PEO) is an emerging technology that provides enhanced surface properties compared to traditional anodizing.
Nanotechnology
The integration of nanotechnology into anodizing processes holds promise for creating metal surfaces with unique properties, such as superhydrophobicity, self-cleaning, and enhanced wear resistance.
In conclusion, anodizing is a versatile and valuable process in manufacturing that significantly impacts the durability, aesthetics, and functionality of metal products. By understanding its basics, types, applications, advantages, and challenges, one can appreciate the role anodizing plays in modern industry and envision its potential future developments.
資料ダウンロード
QCD調達購買管理クラウド「newji」は、調達購買部門で必要なQCD管理全てを備えた、現場特化型兼クラウド型の今世紀最高の購買管理システムとなります。
ユーザー登録
調達購買業務の効率化だけでなく、システムを導入することで、コスト削減や製品・資材のステータス可視化のほか、属人化していた購買情報の共有化による内部不正防止や統制にも役立ちます。
NEWJI DX
製造業に特化したデジタルトランスフォーメーション(DX)の実現を目指す請負開発型のコンサルティングサービスです。AI、iPaaS、および先端の技術を駆使して、製造プロセスの効率化、業務効率化、チームワーク強化、コスト削減、品質向上を実現します。このサービスは、製造業の課題を深く理解し、それに対する最適なデジタルソリューションを提供することで、企業が持続的な成長とイノベーションを達成できるようサポートします。
オンライン講座
製造業、主に購買・調達部門にお勤めの方々に向けた情報を配信しております。
新任の方やベテランの方、管理職を対象とした幅広いコンテンツをご用意しております。
お問い合わせ
コストダウンが利益に直結する術だと理解していても、なかなか前に進めることができない状況。そんな時は、newjiのコストダウン自動化機能で大きく利益貢献しよう!
(Β版非公開)