- お役立ち記事
- Basics of battery management system (BMS) and key points for battery pack design and quality assurance
Basics of battery management system (BMS) and key points for battery pack design and quality assurance
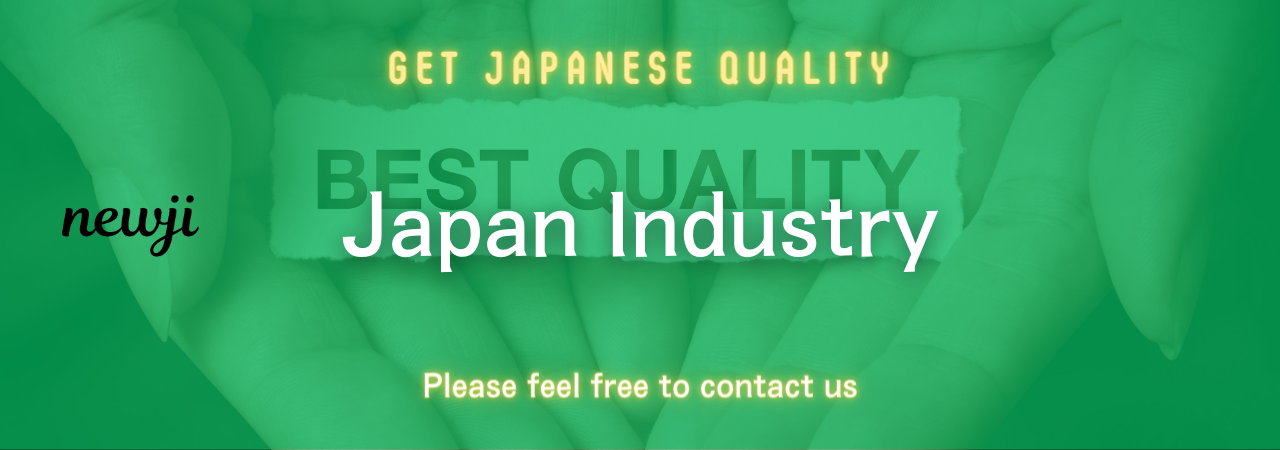
目次
Understanding the Basics of Battery Management Systems (BMS)
A Battery Management System (BMS) is an essential component within a battery-powered system that ensures safe and efficient operation.
Its primary function is to monitor and manage the performance of individual cells within a battery pack.
By tracking parameters like voltage, current, temperature, and state of charge (SOC), the BMS helps maintain the health and longevity of the batteries.
A ZBMS is critical in preventing overcharging, which can lead to battery failure or even hazardous situations.
Furthermore, it guards against deep discharging, effectively extending the lifespan of the entire battery system.
Key Functions of a BMS
1. **Cell Monitoring:** The BMS continuously monitors the voltage and temperature of each cell to ensure stability.
This helps detect anomalies early and address them promptly.
2. **State of Charge (SOC) Calculation:** Accurately estimating the SOC helps in understanding the available capacity and estimating the time left before a recharge is needed.
3. **Balancing:** The BMS ensures all cells are charged equally, so they operate in harmony, further ensuring maximum performance and longevity.
4. **Communication:** It provides valuable data to external devices, like a display or a linked computer, to inform users about the battery state and performance metrics.
Key Points in Battery Pack Design
Designing a battery pack involves careful planning and a deep understanding of both the application requirements and battery characteristics.
Effective design ensures optimal performance and reliability.
Choose the Right Chemistry
Selecting the right battery chemistry for your application is crucial.
Options include lithium-ion, nickel-metal hydride, and lead-acid, each with its unique characteristics.
Lithium-ion batteries, for example, offer high energy density and are widely used in consumer electronics and electric vehicles.
Size and Configuration
Determine the pack size and configuration based on the power and energy requirements of your application.
The physical size and shape should accommodate the intended space and ergonomic considerations.
Thermal Management
Temperature control is paramount in maintaining battery health.
Efficient cooling systems, like heat sinks or liquid cooling, mitigate heat build-up especially in high-drain applications.
Enclosure Design
The enclosure provides both mechanical and environmental protection.
It should be robust enough to withstand vibration, impact, and exposure to moisture or dust.
Electrical Design
Design your battery pack’s electrical layout with adequate insulation, circuit protection, and wiring connectors.
Careful selection of these components minimizes risks of short circuits and ensures operational safety.
Quality Assurance in Battery Pack Manufacturing
To guarantee safety and performance, rigorous quality assurance measures are vital during the manufacturing of battery packs.
Component Testing
Each element of the battery pack, including cells, circuitry, and enclosures, should meet high standards of quality and reliability.
Testing for capacity, voltage, and internal resistance ensures only components that meet specifications are used.
Functional Testing
Conduct thorough testing on the assembled battery packs to confirm that all components work seamlessly together.
This includes verifying voltage balance, charge and discharge cycles, and safe operating temperatures.
Safety Testing
Simulate extreme conditions to ensure that the battery pack can safely handle unusual or adverse situations.
This includes overcharge, short circuit, and impact tests to verify protective measures are effective.
Traceability and Documentation
Maintain detailed documentation of all testing processes and results.
Traceability is crucial in identifying any defects and understanding the performance history of battery packs.
Customer Feedback and Iteration
Integrate customer feedback into the design and manufacturing process to continually refine and improve battery packs.
Adapting to emerging technologies and user needs ensures your product remains competitive and reliable.
In conclusion, mastering the basics of Battery Management Systems, coupled with meticulous battery pack design and manufacturing quality assurance, fosters the development of efficient, reliable, and safe battery systems.
By prioritizing these elements in your design process, you contribute to the longevity and efficiency of battery-powered devices across industries.
資料ダウンロード
QCD調達購買管理クラウド「newji」は、調達購買部門で必要なQCD管理全てを備えた、現場特化型兼クラウド型の今世紀最高の購買管理システムとなります。
ユーザー登録
調達購買業務の効率化だけでなく、システムを導入することで、コスト削減や製品・資材のステータス可視化のほか、属人化していた購買情報の共有化による内部不正防止や統制にも役立ちます。
NEWJI DX
製造業に特化したデジタルトランスフォーメーション(DX)の実現を目指す請負開発型のコンサルティングサービスです。AI、iPaaS、および先端の技術を駆使して、製造プロセスの効率化、業務効率化、チームワーク強化、コスト削減、品質向上を実現します。このサービスは、製造業の課題を深く理解し、それに対する最適なデジタルソリューションを提供することで、企業が持続的な成長とイノベーションを達成できるようサポートします。
オンライン講座
製造業、主に購買・調達部門にお勤めの方々に向けた情報を配信しております。
新任の方やベテランの方、管理職を対象とした幅広いコンテンツをご用意しております。
お問い合わせ
コストダウンが利益に直結する術だと理解していても、なかなか前に進めることができない状況。そんな時は、newjiのコストダウン自動化機能で大きく利益貢献しよう!
(Β版非公開)