- お役立ち記事
- Basics of battery management system (BMS), battery pack design, and safe and appropriate quality control points
月間73,982名の
製造業ご担当者様が閲覧しています*
*2025年1月31日現在のGoogle Analyticsのデータより
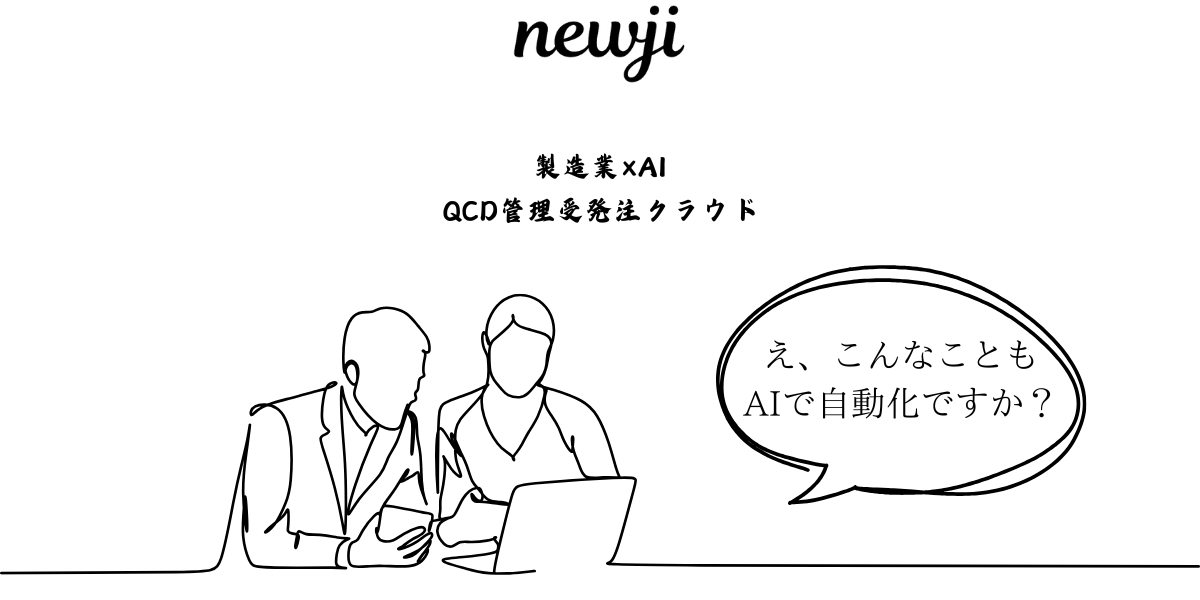
Basics of battery management system (BMS), battery pack design, and safe and appropriate quality control points
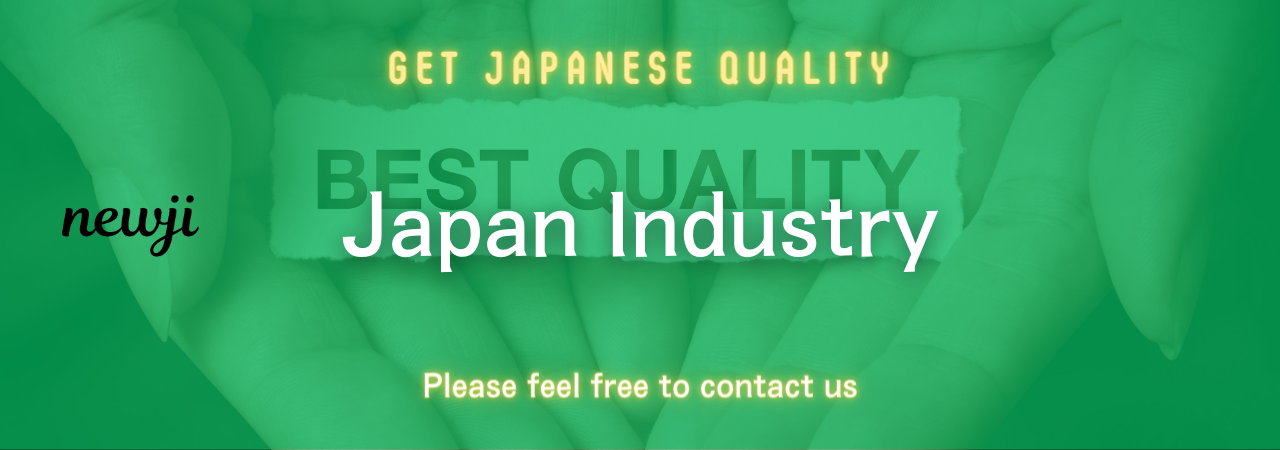
目次
Understanding Battery Management Systems (BMS)
A Battery Management System, or BMS, is an essential component in many modern electronic devices, especially those reliant on rechargeable batteries.
These include electric vehicles, smartphones, and renewable energy storage systems.
At its core, a BMS is designed to monitor and manage the performance of a battery pack, ensuring optimal usage and extending its lifespan.
The key functions of a BMS include monitoring the state of charge (SOC), state of health (SOH), and temperature of the battery pack.
It helps prevent scenarios such as overcharging, over-discharging, and overheating, which can compromise safety or damage the battery.
By maintaining the balance between cells in a battery pack, a BMS also ensures that each cell is neither overused nor underutilized.
The Components of a BMS
A robust BMS consists of several components that work in tandem to protect and optimize a battery pack.
These components include:
– **Battery Monitoring Units (BMU):** BMUs are responsible for gathering data from each cell or module within the battery.
They provide crucial information about voltage, current, and temperature.
– **Control Unit:** This is the brain of the BMS, processing data from the BMU to make real-time decisions on how the battery should be charged and discharged.
– **Communication Interface:** It facilitates communication between the battery pack and external devices or systems, ensuring the device can receive alerts or updates on battery performance.
– **Safety Mechanisms:** These are integral parts that trigger warnings or shut down the battery pack if unsafe conditions are detected.
Designing a Battery Pack
When designing a battery pack, there are several factors to consider to ensure safety, efficiency, and reliability.
Here’s a look at what goes into crafting a well-designed battery pack:
Cell Selection
Choosing the right battery cells is vital.
Different applications require different cell chemistries, such as lithium-ion, nickel-metal hydride, or lead-acid.
Each chemistry has its own advantages in terms of energy density, life expectancy, and safety.
The choice depends heavily on the intended application, be it an electric car, a smartphone, or an industrial machine.
Configuration
The configuration of the cells, whether in series or parallel, will impact the voltage and capacity of the battery pack.
Cells connected in series increase the voltage, while those in parallel boost the capacity.
The optimal configuration must consider the voltage and capacity requirements of the application.
Mechanical Design
The mechanical design of a battery pack involves creating a structure to house the cells while considering thermal management, protection, and weight distribution.
Proper thermal management is critical to prevent overheating, which can reduce battery lifespan and pose safety risks.
Electrical Design
Electrical design involves planning the circuitry that will safely manage the charging and discharging processes.
This includes incorporating overcurrent protection, cell balancing, and connections for voltage and temperature monitoring.
Quality Control in Battery Manufacturing
Quality control is crucial to ensure that battery packs are safe, reliable, and effective.
Several quality control points must be adhered to during the manufacturing process:
Testing
Testing is a cornerstone of quality control.
It involves checking battery cells for performance standards such as capacity, voltage, and internal resistance.
Testing also extends to the completed pack, which must undergo rigorous evaluations to ensure it meets safety and performance benchmarks.
Inspection
Inspection processes ensure that all components, from individual cells to the BMS, meet design specifications.
Visual inspections and automated systems can detect defects or deviations early, minimizing risks associated with faulty components.
Compliance
Adhering to industry standards and regulatory requirements is essential.
Compliance ensures that battery products are safe for consumers and suitable for their intended applications.
Manufacturers must stay informed about relevant safety standards and environmental regulations.
Documentation and Traceability
Maintaining detailed records of the production process provides traceability in the event of faults or customer complaints.
Documentation helps manufacturers identify and correct process issues efficiently and is crucial for accountability and continuous improvement.
Ensuring Safety in Battery Systems
Safety is a paramount consideration in battery management, design, and manufacturing.
Implementing comprehensive safety protocols minimizes risks associated with battery usage.
Thermal Management
Implementing effective thermal management systems within battery packs is crucial for preventing overheating and thermal runaway, both of which can result in catastrophic failure.
Designing for adequate ventilation, using cooling systems, and employing heat-resistant materials are critical approaches.
Overcharge and Overdischarge Protection
A well-designed BMS will have mechanisms to prevent overcharging and over-discharging, both of which can degrade battery cells and create safety hazards.
These mechanisms often involve disconnecting the power source or load when unsafe conditions are detected.
Regular Maintenance and Monitoring
Routine maintenance and the regular monitoring of battery systems ensure that any issues are identified and resolved before they escalate.
This includes checking for physical damage, corrosion, or unusual performance characteristics.
In conclusion, understanding the essentials of battery management systems, along with effective design and rigorous quality control, is crucial for developers and manufacturers.
Such knowledge ensures not only the maximization of performance and longevity of battery packs but also upholds the necessary safety standards that protect both users and the environment.
資料ダウンロード
QCD管理受発注クラウド「newji」は、受発注部門で必要なQCD管理全てを備えた、現場特化型兼クラウド型の今世紀最高の受発注管理システムとなります。
ユーザー登録
受発注業務の効率化だけでなく、システムを導入することで、コスト削減や製品・資材のステータス可視化のほか、属人化していた受発注情報の共有化による内部不正防止や統制にも役立ちます。
NEWJI DX
製造業に特化したデジタルトランスフォーメーション(DX)の実現を目指す請負開発型のコンサルティングサービスです。AI、iPaaS、および先端の技術を駆使して、製造プロセスの効率化、業務効率化、チームワーク強化、コスト削減、品質向上を実現します。このサービスは、製造業の課題を深く理解し、それに対する最適なデジタルソリューションを提供することで、企業が持続的な成長とイノベーションを達成できるようサポートします。
製造業ニュース解説
製造業、主に購買・調達部門にお勤めの方々に向けた情報を配信しております。
新任の方やベテランの方、管理職を対象とした幅広いコンテンツをご用意しております。
お問い合わせ
コストダウンが利益に直結する術だと理解していても、なかなか前に進めることができない状況。そんな時は、newjiのコストダウン自動化機能で大きく利益貢献しよう!
(β版非公開)