- お役立ち記事
- Basics of BOM (Bill of Materials) and its application to reuse and standardized design
月間76,176名の
製造業ご担当者様が閲覧しています*
*2025年3月31日現在のGoogle Analyticsのデータより
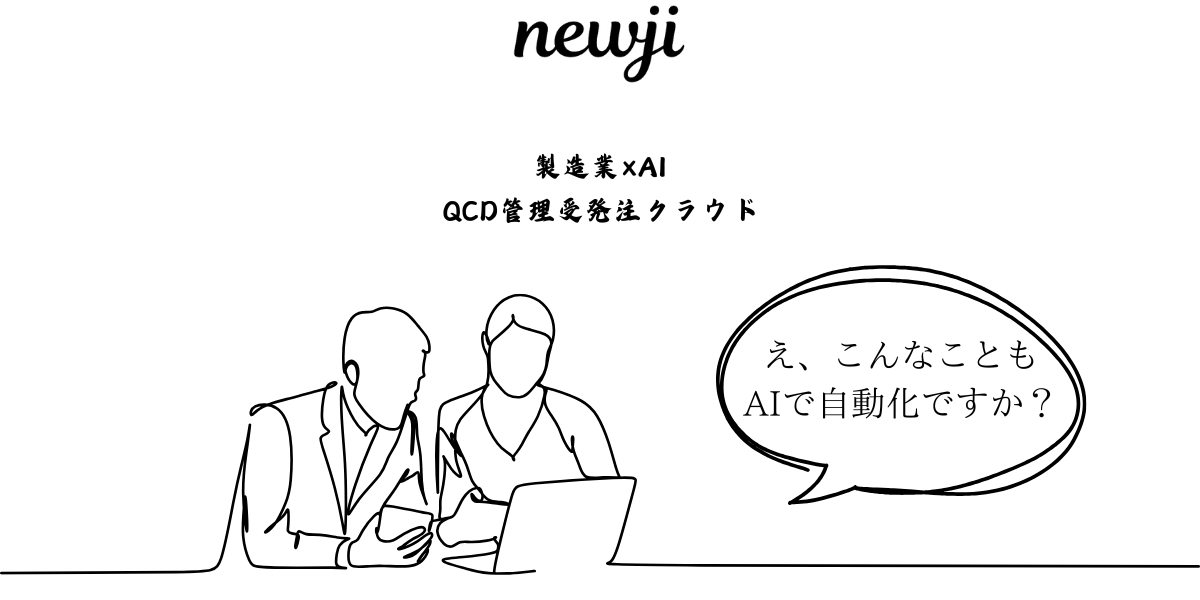
Basics of BOM (Bill of Materials) and its application to reuse and standardized design
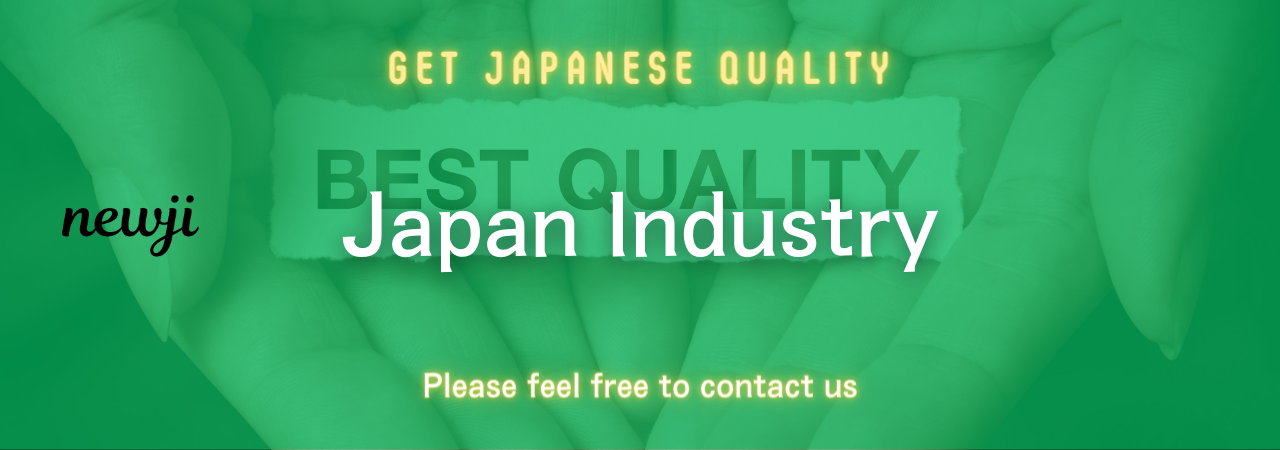
目次
Understanding the Basics of BOM (Bill of Materials)
A Bill of Materials (BOM) is an essential component in the world of manufacturing and production.
Simply put, it is a comprehensive list of components, items, materials, and instructions required to construct, manufacture, or repair a product or service.
Think of it as a recipe for your favorite dish, detailing every ingredient and step needed to prepare it.
In the context of manufacturing, having a precise and well-structured BOM ensures that the production process runs smoothly, reducing errors and enhancing efficiency.
Components of a BOM
A BOM is composed of several key elements.
Each element plays a crucial role in ensuring that the BOM serves its purpose effectively.
1. **Part Number:** Every component in a BOM is assigned a unique identifier known as the part number.
This helps in tracking and referencing components easily.
2. **Part Name:** Alongside a part number, each component will have a name that describes what it is.
This provides clarity, especially in complex assemblies where multiple parts may be involved.
3. **Description:** A detailed explanation of each component, including its specifications and characteristics.
The description can include information such as the material used, dimensions, and any special features.
4. **Quantity:** The number of each component required for the assembly of one finished product.
Ensuring the correct quantity is crucial for production planning and inventory management.
5. **Unit of Measure:** The measurement unit for each component, such as meters, pieces, liters, etc.
This helps in ordering and managing inventory accurately.
6. **Procurement Type:** Information on whether each component is purchased or manufactured in-house.
This aids in supply chain management and cost analysis.
Applications of BOM in Manufacturing
The Bill of Materials is a pivotal document in manufacturing, serving various applications that streamline production and enhance product quality.
Enhancing Production Planning
BOM serves as a roadmap for production planning.
It provides manufacturers with a clear understanding of the resources needed to produce a particular product.
This helps in scheduling production activities, ensuring that all components are available when required, and minimizing downtime.
Inventory Management
A well-structured BOM assists in effective inventory management.
By clearly outlining the quantity of each component needed, it helps prevent overstocking or understocking of materials.
This not only reduces storage costs but also ensures that production isn’t halted due to a lack of necessary components.
Cost Estimation and Control
BOM plays a critical role in cost estimation.
By detailing every component needed for production, it allows manufacturers to accurately estimate the cost of producing each unit.
Furthermore, it helps identify cost-saving opportunities by analyzing component procurement and usage.
Product Development and Design
In product development, a BOM is indispensable.
It aids in the design process by providing a detailed overview of the components involved.
This helps in identifying standard parts that can be reused across different products, reducing design time and costs.
Reusing and Standardizing Design with BOM
BOM not only facilitates efficient production but also plays a key role in promoting reuse and standardization in design.
Advantage of Reuse
Reusing components helps in reducing production costs and shortening time-to-market for new products.
By identifying commonly used components in the BOM, companies can leverage existing stock and purchase in bulk, thereby reducing procurement costs.
Promoting Standardized Design
Standardization in design is another major benefit of a well-structured BOM.
By analyzing the components used across different products, designers can identify standard parts that can be used in multiple offerings.
This not only simplifies the design process but also reduces complexity and variability in production.
Simplifying Maintenance and Repairs
Standardization and reuse also simplify maintenance and repair processes.
With standard parts being used across different products, it becomes easier to maintain and repair equipment.
This reduces downtime and ensures that products remain operational for longer periods.
Conclusion
The Bill of Materials is a fundamental document in manufacturing and production.
By understanding its components and applications, businesses can enhance their production processes, improve cost management, and promote reuse and standardization in design.
As companies strive for efficiency and cost-effectiveness, the strategic use of BOM will continue to play a vital role in achieving manufacturing excellence.
資料ダウンロード
QCD管理受発注クラウド「newji」は、受発注部門で必要なQCD管理全てを備えた、現場特化型兼クラウド型の今世紀最高の受発注管理システムとなります。
ユーザー登録
受発注業務の効率化だけでなく、システムを導入することで、コスト削減や製品・資材のステータス可視化のほか、属人化していた受発注情報の共有化による内部不正防止や統制にも役立ちます。
NEWJI DX
製造業に特化したデジタルトランスフォーメーション(DX)の実現を目指す請負開発型のコンサルティングサービスです。AI、iPaaS、および先端の技術を駆使して、製造プロセスの効率化、業務効率化、チームワーク強化、コスト削減、品質向上を実現します。このサービスは、製造業の課題を深く理解し、それに対する最適なデジタルソリューションを提供することで、企業が持続的な成長とイノベーションを達成できるようサポートします。
製造業ニュース解説
製造業、主に購買・調達部門にお勤めの方々に向けた情報を配信しております。
新任の方やベテランの方、管理職を対象とした幅広いコンテンツをご用意しております。
お問い合わせ
コストダウンが利益に直結する術だと理解していても、なかなか前に進めることができない状況。そんな時は、newjiのコストダウン自動化機能で大きく利益貢献しよう!
(β版非公開)