- お役立ち記事
- Basics of building a quality assurance system in medical device manufacturing
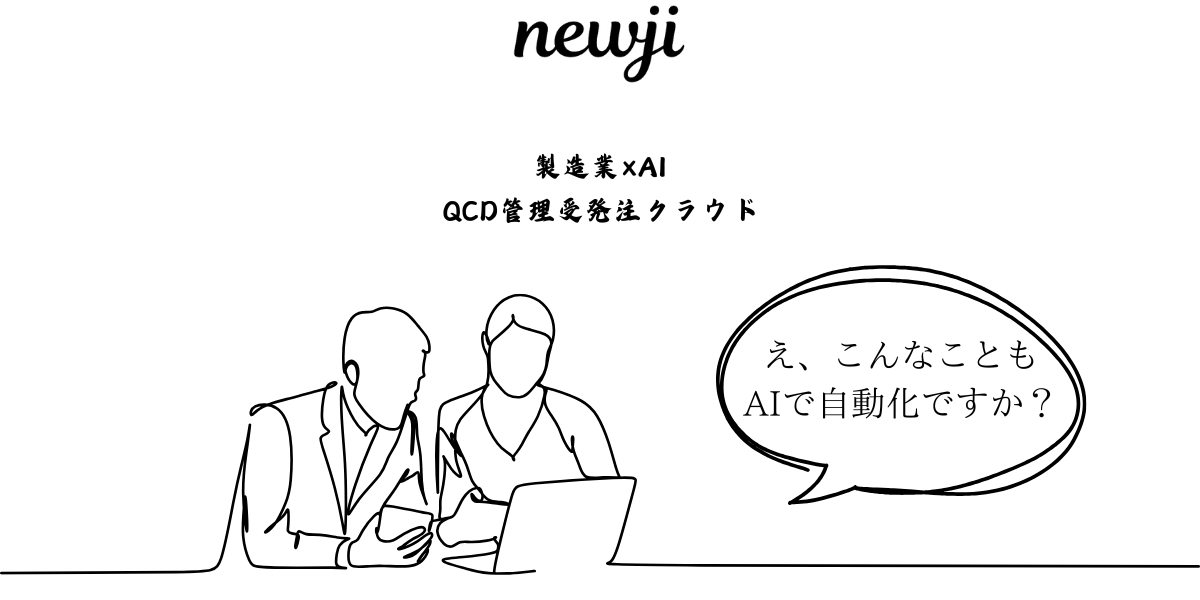
Basics of building a quality assurance system in medical device manufacturing
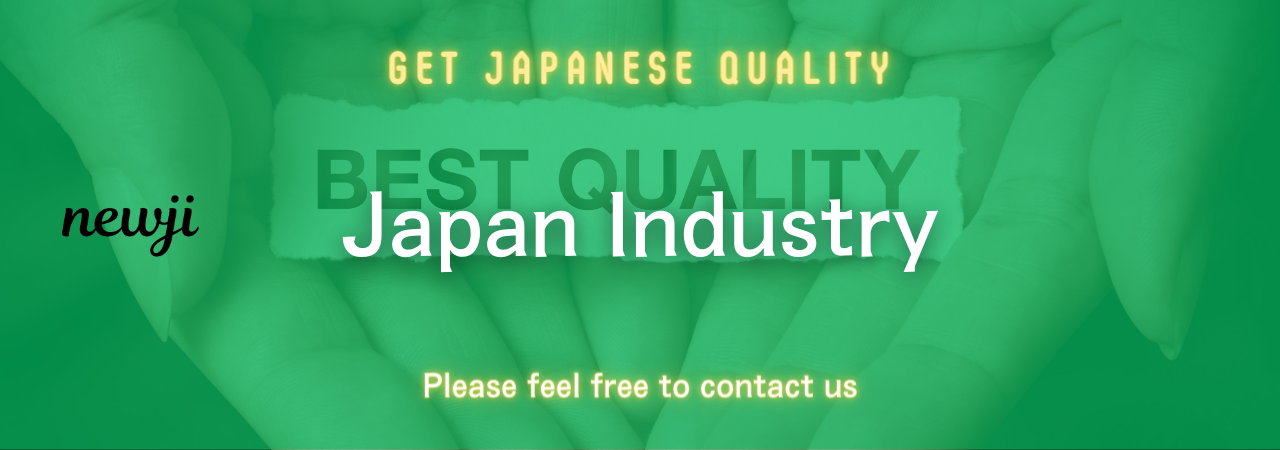
In the world of medical devices, ensuring that products are safe, effective, and of the highest quality is an absolute necessity.
As these devices are often critical to patient health, there’s no room for error.
This is where a robust quality assurance system comes into play.
Building an effective quality assurance system in medical device manufacturing involves several key elements that must be carefully considered and implemented.
目次
Understanding Quality Assurance in Medical Devices
Before diving into the specifics of building a quality assurance system, it’s important to understand what quality assurance (QA) actually means in the context of medical device manufacturing.
Quality assurance refers to the systematic processes implemented to ensure that products meet certain standards of quality.
It includes everything from the design phase of a product to its production and post-market monitoring.
The main goal is to ensure that each medical device is safe and effective for its intended use.
To achieve this, manufacturers must comply with stringent regulatory standards and guidelines, including those set by the FDA in the United States or the European Union’s Medical Device Regulation (MDR).
The Importance of Regulatory Compliance
For any medical device manufacturer, adhering to regulatory requirements is non-negotiable.
Regulations ensure that the products reaching end-users are of high-quality and don’t pose any risks to their health or safety.
Compliance with these regulations not only safeguards patients but also protects the manufacturers from legal ramifications and enhances their reputation in the market.
These regulations often require that manufacturers establish and maintain a comprehensive quality management system (QMS).
This system should address all aspects of the product lifecycle, including design, production, and distribution.
Key Elements of a Quality Assurance System
Building a quality assurance system involves multiple components, each playing a vital role in ensuring the product’s quality.
Here’s a closer look at these key elements:
1. Design Controls
Design controls are an integral part of the quality assurance process.
They involve systematic measures taken during the design phase to ensure that the product meets the necessary requirements.
These controls typically include designing input requirements, designing process verification and validation, and reviewing designs to identify potential issues early on.
Effective design controls help in minimizing risks and ensuring the device’s safety and functionality right from the start.
2. Risk Management
Risk management is a continuous process that helps identify, assess, and mitigate potential risks associated with a medical device.
The process involves hazard identification, risk estimation, and risk control measures.
By systematically managing risk, manufacturers can ensure that any potential issues are addressed before the product reaches the market.
A proactive approach to risk management significantly reduces the chances of recalls or legal issues post-launch.
3. Document Control
In the medical device industry, maintaining accurate and up-to-date documentation is crucial.
Document control refers to the management of documents throughout the product lifecycle.
A robust document control system ensures that all documents, including design plans, risk management records, and manufacturing processes, are properly maintained and accessible.
This not only helps in regulatory compliance but also serves as a point of reference in case of audits or inspections.
4. Post-Market Surveillance
Once a medical device is on the market, continuous monitoring is essential to assess its performance and safety.
Post-market surveillance involves collecting and analyzing data on the product’s usage and any adverse events reported by users.
This continuous process helps in identifying any issues that may not have been evident during the pre-market phases.
By promptly addressing these issues, manufacturers can ensure ongoing product quality and safety.
Implementing a Quality Management System
A Quality Management System (QMS) is a formalized system that documents the structure, responsibilities, and procedures required to achieve effective quality management.
Implementing a QMS is a major component of quality assurance.
The system should align with internationally recognized standards, such as ISO 13485, which is specific to medical device manufacturing.
A successful QMS covers all aspects of the product lifecycle and ensures continuous improvement in processes and products.
Developing Standard Operating Procedures
A vital part of a QMS is the development of Standard Operating Procedures (SOPs).
These are step-by-step instructions that detail how tasks should be performed to ensure consistency and compliance with quality standards.
SOPs are essential for training employees and ensuring that everyone is aligned with the company’s quality objectives.
They also provide a clear framework for measuring and improving process efficiency.
Training and Continuous Improvement
For any quality assurance system to be effective, it must be supported by a well-trained workforce.
Training employees on the importance of quality standards and their role in maintaining these standards is crucial.
Continuous improvement is another essential aspect.
Manufacturers should regularly review and update their processes, incorporating feedback and insights gained from post-market surveillance and other sources.
A commitment to continuous improvement ensures that the quality assurance system remains effective and responsive to changing needs and challenges.
Conclusion
Building a quality assurance system in medical device manufacturing is a complex but necessary endeavor.
By focusing on regulatory compliance, design controls, risk management, and post-market surveillance, manufacturers can ensure the highest quality of medical devices.
Implementing a robust Quality Management System, along with comprehensive employee training and a commitment to continuous improvement, lays the foundation for an effective quality assurance system.
Ultimately, these efforts help in delivering safe, reliable, and effective medical devices to those who need them most.
資料ダウンロード
QCD調達購買管理クラウド「newji」は、調達購買部門で必要なQCD管理全てを備えた、現場特化型兼クラウド型の今世紀最高の購買管理システムとなります。
ユーザー登録
調達購買業務の効率化だけでなく、システムを導入することで、コスト削減や製品・資材のステータス可視化のほか、属人化していた購買情報の共有化による内部不正防止や統制にも役立ちます。
NEWJI DX
製造業に特化したデジタルトランスフォーメーション(DX)の実現を目指す請負開発型のコンサルティングサービスです。AI、iPaaS、および先端の技術を駆使して、製造プロセスの効率化、業務効率化、チームワーク強化、コスト削減、品質向上を実現します。このサービスは、製造業の課題を深く理解し、それに対する最適なデジタルソリューションを提供することで、企業が持続的な成長とイノベーションを達成できるようサポートします。
オンライン講座
製造業、主に購買・調達部門にお勤めの方々に向けた情報を配信しております。
新任の方やベテランの方、管理職を対象とした幅広いコンテンツをご用意しております。
お問い合わせ
コストダウンが利益に直結する術だと理解していても、なかなか前に進めることができない状況。そんな時は、newjiのコストダウン自動化機能で大きく利益貢献しよう!
(Β版非公開)