- お役立ち記事
- Basics of Burr Prevention and Case Studies of SME Implementation
月間76,176名の
製造業ご担当者様が閲覧しています*
*2025年3月31日現在のGoogle Analyticsのデータより
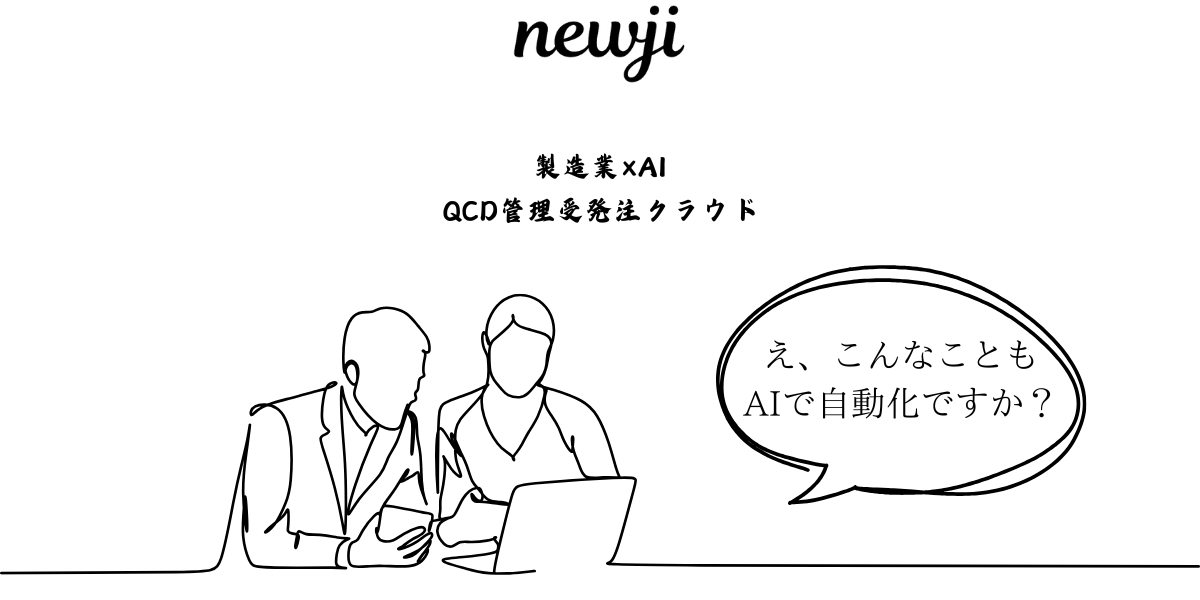
Basics of Burr Prevention and Case Studies of SME Implementation
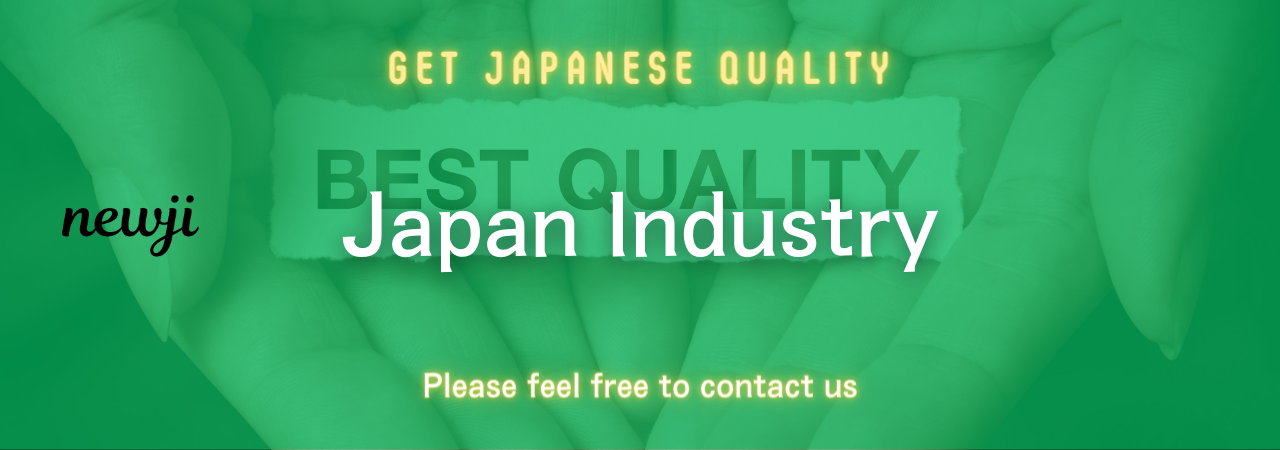
目次
Understanding Burrs and Their Impact
Burrs are small, unwanted pieces of material that can form on the edges of machined components.
These blemishes not only mar the appearance of the finished product but can also compromise its functionality, leading to potential safety hazards.
Understanding the nature of burrs is the first step towards effectively preventing them.
Burrs are most commonly observed in manufacturing processes such as drilling, milling, grinding, and turning.
These processes involve cutting, which can cause a fragment of material to remain attached to the workpiece.
In some cases, burrs can create alignment issues during assembly, damage neighboring components, or cause injuries due to sharp edges.
The Basics of Burr Prevention
Preventing burrs requires a comprehensive approach that includes both equipment settings and the choice of manufacturing operations.
Every manufacturing facility is unique, so strategies need to be customized according to specific needs.
Cutter Selection and Tool Design
Choosing the right cutters and tools is critical in minimizing burr formation.
For instance, using cutters with sharper edges and correct geometries can significantly reduce the occurrence of burrs.
Incorporating chamfered or radiused tool edges can help improve surface finish, minimizing burr creation.
Optimizing Machining Parameters
Machining parameters such as feed rate, speed, and depth of cut should be optimized to reduce burrs.
This often entails balancing the efficiency of the machining process with the quality of the edges being produced.
Slower speeds and lighter cuts may decrease burr size, but they also lengthen production times.
Material Selection and Conditioning
The properties of the material being machined play a significant role in burr formation.
Materials that are ductile tend to form larger burrs than brittle materials.
Pre-treating or conditioning materials, such as stress relieving or annealing, can reduce their tendency to burr during processing.
Case Studies of SME Implementation
Several small to medium-sized enterprises (SMEs) have successfully implemented burr prevention measures to enhance their production processes.
These case studies provide insights into practical applications of burr prevention techniques.
Case Study 1: Precision Aerospace Components
An SME specializing in aerospace components faced persistent quality issues due to burrs.
Initially, the company was spending significant time and resources on post-machining deburring.
To address this, they invested in newer, high-performance cutting tools and adjusted their machining parameters accordingly.
By conducting a detailed analysis of their machining processes and implementing these tailored solutions, they reduced burrs by 70% and lowered production costs.
Case Study 2: Automotive Part Supplier
Another SME in the automotive sector encountered similar challenges with burrs compromising component performance.
They focused on optimizing their aluminum machining process.
A comprehensive evaluation led to the adoption of advanced CNC machines and the integration of simulation software to optimize tool paths and minimize material wastage.
As a result, they not only managed to reduce burr formations significantly but also increased their overall production efficiency by 30%.
The Role of Technology and Innovation
The integration of technology and innovative practices has played a pivotal role in burr prevention.
Advanced CNC machinery, simulation software, and automation are revolutionizing how SMEs approach burr prevention.
Automation and Robotics
Automated systems and robotics are increasingly being utilized to maintain consistent machining processes, reducing the chances of burr formation.
The precision and repeatability offered by automated systems ensure that machining parameters are consistently applied across production runs.
Simulation Software
Simulation software enables manufacturers to model machining processes and predict outcomes.
These digital twins help in identifying potential issues, such as burr formation, before actual machining takes place.
By refining processes virtually, manufacturers can avoid defects and optimize quality.
Continuous Monitoring and Feedback
The adoption of real-time monitoring systems allows manufacturers to collect data throughout the machining process.
This enables continuous feedback and process refinement, ensuring components meet strict quality standards while reducing burr formation.
Conclusion: Moving Forward with Burr-Free Manufacturing
Preventing burrs is a critical aspect of modern manufacturing, requiring a blend of traditional techniques and innovative technologies.
For SMEs, the path to burr-free manufacturing involves understanding the nature of burrs, optimizing existing processes, and investing in cutting-edge solutions.
As technology continues to evolve, SMEs have the opportunity to adopt advanced tools and systems that uphold high production standards and ensure product quality, ultimately contributing to their competitiveness in the market.
資料ダウンロード
QCD管理受発注クラウド「newji」は、受発注部門で必要なQCD管理全てを備えた、現場特化型兼クラウド型の今世紀最高の受発注管理システムとなります。
ユーザー登録
受発注業務の効率化だけでなく、システムを導入することで、コスト削減や製品・資材のステータス可視化のほか、属人化していた受発注情報の共有化による内部不正防止や統制にも役立ちます。
NEWJI DX
製造業に特化したデジタルトランスフォーメーション(DX)の実現を目指す請負開発型のコンサルティングサービスです。AI、iPaaS、および先端の技術を駆使して、製造プロセスの効率化、業務効率化、チームワーク強化、コスト削減、品質向上を実現します。このサービスは、製造業の課題を深く理解し、それに対する最適なデジタルソリューションを提供することで、企業が持続的な成長とイノベーションを達成できるようサポートします。
製造業ニュース解説
製造業、主に購買・調達部門にお勤めの方々に向けた情報を配信しております。
新任の方やベテランの方、管理職を対象とした幅広いコンテンツをご用意しております。
お問い合わせ
コストダウンが利益に直結する術だと理解していても、なかなか前に進めることができない状況。そんな時は、newjiのコストダウン自動化機能で大きく利益貢献しよう!
(β版非公開)