- お役立ち記事
- Basics of CAE analysis and usage points for fatigue strength design and design optimization
Basics of CAE analysis and usage points for fatigue strength design and design optimization
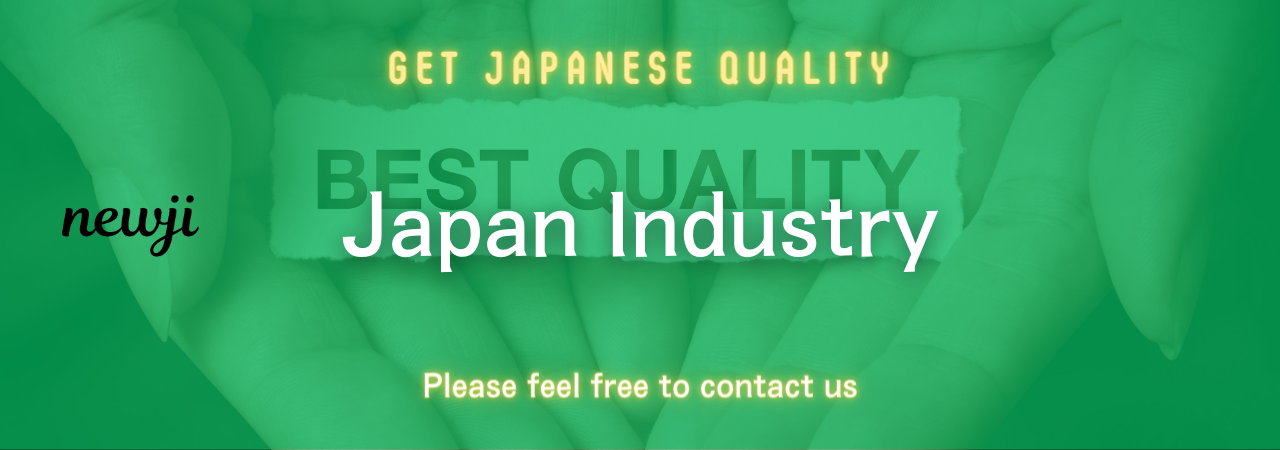
目次
Understanding CAE Analysis
CAE, or Computer-Aided Engineering, refers to the utilization of computer software to aid in the analysis, design, and simulation of products and engineering systems.
This technology enables engineers to evaluate and enhance product designs, ensuring efficiency, safety, and performance before they are manufactured.
CAE encompasses a range of tools and processes, including finite element analysis (FEA), computational fluid dynamics (CFD), and multibody dynamics (MBD).
Each of these plays a crucial role in understanding how a product will behave under various conditions, thus reducing the need for multiple physical prototypes.
Incorporating CAE early in the design process can lead to more innovative products that reach the market faster and with fewer defects.
The Role of CAE in Engineering
The primary role of CAE in engineering is to simulate physical behaviors such as stress, heat transfer, and fluid flow.
This aids in predicting how a product will react to real-world forces, vibrations, or thermal impacts.
For instance, using finite element analysis, an engineer can determine how pushing, pulling, or twisting will affect an object.
Similarly, computational fluid dynamics can predict how liquids or gases flow around a product design, crucial for automotive, aerospace, and many other industries.
By simulating these conditions, CAE helps engineers identify potential weaknesses or failures, thus allowing for design adjustments to prevent costly errors and ensure product longevity.
Fatigue Strength Design
Fatigue strength refers to a material’s ability to withstand repeated loading and unloading cycles without failing.
Understanding this is critical, as many engineering failures are due to fatigue rather than a single overload condition.
To design for fatigue strength, engineers must consider the number of cycles the material will experience, the magnitude of the stress, and environmental factors like temperature and corrosion.
CAE tools can simulate various stress conditions, helping engineers predict how long a product will last under specific repetitive applications.
This is crucial in industries like automotive and aerospace, where components are often subjected to varying and repeated stresses.
Correctly designing for fatigue strength means ensuring that the product will perform reliably over its intended lifespan, avoiding unexpected failures.
Incorporating Fatigue Analysis in CAE
Integrating fatigue analysis into CAE simulations provides a more comprehensive understanding of a product’s durability.
Engineers can use these analyses to predict the lifecycle of a component by considering different material properties and stress scenarios.
The benefit of CAE fatigue analysis is that it can quickly handle complex variables and multiple load conditions to provide a broader picture of potential material fatigue.
This capability reduces the trial-and-error approach and yields more accurate predictions, steering the design towards more sustainable and resilient solutions.
Industries that create components exposed to high-stress variations, such as the automotive or aeronautical sectors, find fatigue analysis an invaluable tool in their design process.
Design Optimization Using CAE
Design optimization refers to improving a product so that it meets all function and performance requirements with the least possible weight, cost, and environmental impact.
CAE plays an essential role in this process by allowing designers to simulate and analyze different design scenarios rapidly.
This can include variations in shape, material, and the overall structure to find the most efficient design without sacrificing performance or safety.
Design optimization using CAE isn’t limited to the current state of a product but can be explored for future improvements, allowing companies to stay ahead in their markets.
Overall, CAE aids in reducing material usage, lowering manufacturing costs, and enhancing product performance, thus making it an invaluable tool for sustainable and economical product development.
Techniques for Achieving Design Optimization
Several techniques employed in CAE help achieve design optimization.
One of the popular methods is topology optimization, which involves the use of CAE tools to identify the most efficient material distribution within a given design space.
Other techniques include parametric optimization, where engineers make fine adjustments to a product’s geometry or material properties to achieve the best possible outcome.
These approaches allow designers to manage constraints while pushing boundaries in terms of performance enhancements.
Additionally, CAE helps minimize weight while considering structural strength, an essential factor in transportation industries where efficiency directly impacts performance and environmental footprint.
Advantages of CAE in Modern Engineering
The advantages of CAE in modern engineering are manifold.
By significantly reducing the time and costs associated with physical prototyping and testing, CAE allows engineers to focus on innovation.
This simulation-based approach also supports the rapid prototyping of complex geometries that traditional techniques might struggle to replicate.
The precision of CAE models reduces design errors, leading to better overall product quality and reliability.
Additionally, CAE enhances collaboration across teams, as simulations and results can be easily shared and interpreted, ensuring everyone is aligned with the design goals.
Most importantly, optical design brought by CAE helps organizations to create environmentally sustainable products that meet global standards and consumer expectations.
In summary, CAE is no longer just an optional tool but a fundamental component in the engineering toolbox, enhancing the way products are conceived, tested, and brought to market.
資料ダウンロード
QCD調達購買管理クラウド「newji」は、調達購買部門で必要なQCD管理全てを備えた、現場特化型兼クラウド型の今世紀最高の購買管理システムとなります。
ユーザー登録
調達購買業務の効率化だけでなく、システムを導入することで、コスト削減や製品・資材のステータス可視化のほか、属人化していた購買情報の共有化による内部不正防止や統制にも役立ちます。
NEWJI DX
製造業に特化したデジタルトランスフォーメーション(DX)の実現を目指す請負開発型のコンサルティングサービスです。AI、iPaaS、および先端の技術を駆使して、製造プロセスの効率化、業務効率化、チームワーク強化、コスト削減、品質向上を実現します。このサービスは、製造業の課題を深く理解し、それに対する最適なデジタルソリューションを提供することで、企業が持続的な成長とイノベーションを達成できるようサポートします。
オンライン講座
製造業、主に購買・調達部門にお勤めの方々に向けた情報を配信しております。
新任の方やベテランの方、管理職を対象とした幅広いコンテンツをご用意しております。
お問い合わせ
コストダウンが利益に直結する術だと理解していても、なかなか前に進めることができない状況。そんな時は、newjiのコストダウン自動化機能で大きく利益貢献しよう!
(Β版非公開)