- お役立ち記事
- Basics of CAN communication technology, application to in-vehicle electronic control network development, and its key points
月間77,185名の
製造業ご担当者様が閲覧しています*
*2025年2月28日現在のGoogle Analyticsのデータより
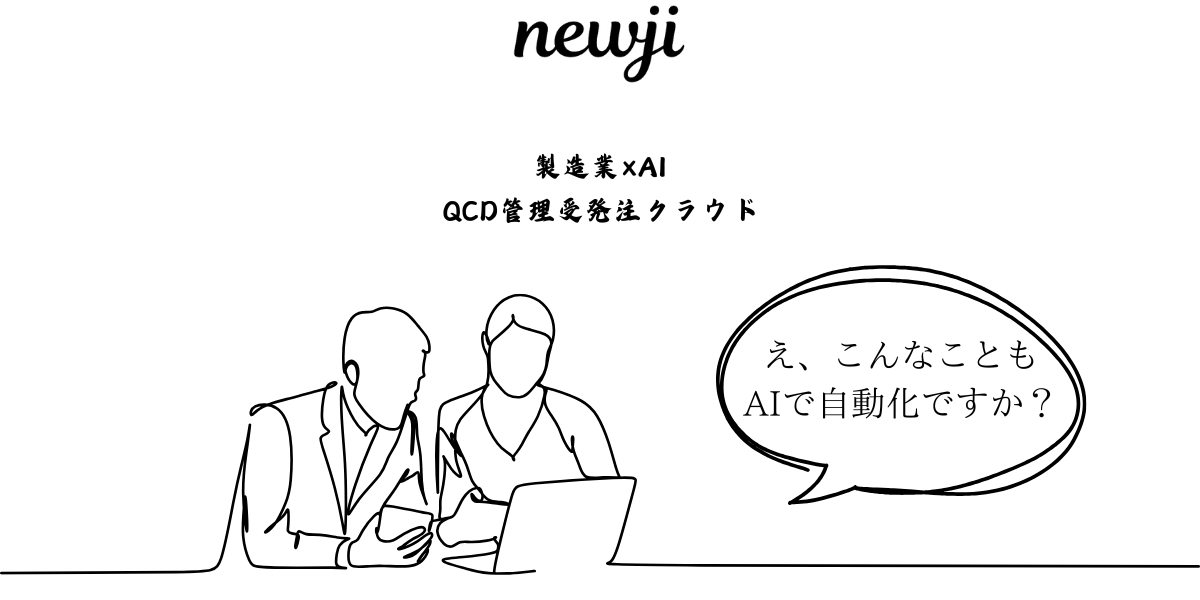
Basics of CAN communication technology, application to in-vehicle electronic control network development, and its key points
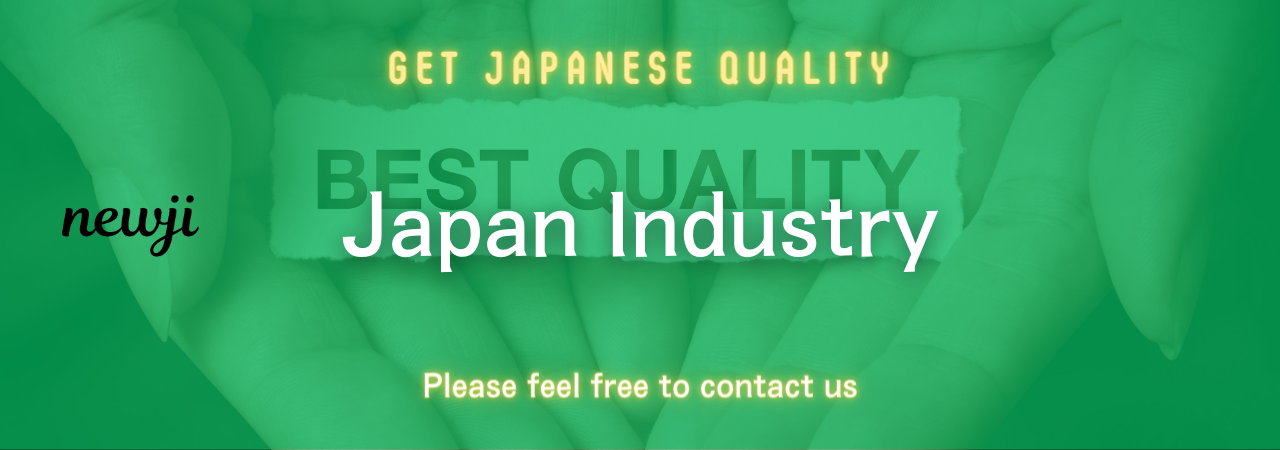
目次
Understanding CAN Communication Technology
CAN, which stands for Controller Area Network, is a robust vehicle bus standard designed to allow microcontrollers and devices to communicate with each other in a vehicle without a host computer.
Originally developed by Bosch in the mid-1980s, CAN was created to address the growing complexity of electronic systems in automobiles, providing a more efficient means of transmitting data.
Core Principles of CAN
CAN operates on a shared bus mechanism, meaning that all nodes or devices are connected to the same physical medium or wire.
This configuration allows any device to send a message, which is then distributed to all other nodes in the network.
The message is utilized or discarded based on its relevance to each specific node.
CAN prioritizes messages via a unique identifier system, where the priority of a message is inversely related to its identifier value.
This means that a message with a lower numerical identifier has a higher priority.
Additionally, CAN includes error detection and data integrity mechanisms, which improve the reliability of data transmission, even in noisy environments.
Advantages of CAN Communication
One of the key advantages of CAN communication is its real-time capability.
With a high communication efficiency, CAN allows for synchronized device operations, which is critical for real-time applications like automotive systems.
CAN also provides high reliability and robustness due to its built-in error-checking and fault-confinement protocols.
Furthermore, CAN’s scalability allows it to be used in both small, simple networks as well as in complex, large system architectures.
Its flexibility makes it suitable for a variety of applications beyond automotive, including industrial automation, marine electronics, and medical equipment.
Applications of CAN in Vehicle Electronic Control Networks
In modern automobiles, CAN technology plays a crucial role in managing the complex web of electronic control systems.
These systems oversee everything from engine management, transmission, and anti-lock braking systems (ABS), to more recent advancements such as electronic stability control, climate control, and infotainment systems.
Engine Management Systems
CAN facilitates data exchanges among various sensors and actuators in an engine management system.
This includes transmitting information such as engine speed, throttle position, and exhaust oxygen levels.
The central control unit uses this information to optimize fuel injection, spark timing, and other engine parameters, thus improving performance and reducing emissions.
Transmission Control
For automatic transmissions, CAN lines convey signals for gear changes and provide feedback on the transmission system’s status.
This allows for smoother gear shifts and better overall vehicle performance.
Driver Assistance Systems
Advanced driver-assistance systems (ADAS) heavily rely on data exchange enabled by CAN networks.
These systems use input data from various sensors to assist with braking, accelerating, steering, and even parking.
Key Points in Developing CAN-Based Networks
While CAN technology offers numerous benefits, certain key considerations must be taken into account when developing CAN-based networks for automotive applications.
Network Architecture and Design
The design of a CAN network needs to accommodate future expansions and updates.
This means developers should consider the physical layout of the network, including the number of nodes, their locations, and the potential for additional devices.
Proper design ensures that the network remains flexible and scalable.
Prioritization and Message Handling
Developers must carefully allocate message identifiers to prioritize critical functions over less crucial ones.
This prioritization ensures that essential data gets transmitted even during peak network load.
Efficient message handling protocols are also necessary to minimize latency and guarantee real-time operation.
Error Handling and Fault Tolerance
A robust error-handling strategy is vital to maintain the integrity of data within a CAN network.
By implementing proper fault-tolerant techniques, such as redundancy and error-correcting codes, developers can enhance the system’s resilience to faults and ensure reliable operation.
Testing and Validation
Before deploying a CAN network in a vehicle, extensive testing and validation are required.
This involves simulating various driving conditions and fault scenarios to verify the network’s performance and reliability.
Conducting rigorous testing helps identify potential issues early, reducing the likelihood of failures in the field.
Conclusion
CAN communication technology continues to be an essential backbone for modern automotive electronics.
Its efficiency, reliability, and simplicity make it an ideal choice for in-vehicle communication networks.
By understanding the fundamentals of CAN technology and carefully considering key development aspects, engineers can effectively design robust and scalable networks that meet the growing demands of today’s vehicles.
As technology evolves, so will CAN’s role in facilitating advanced automotive innovations.
資料ダウンロード
QCD管理受発注クラウド「newji」は、受発注部門で必要なQCD管理全てを備えた、現場特化型兼クラウド型の今世紀最高の受発注管理システムとなります。
ユーザー登録
受発注業務の効率化だけでなく、システムを導入することで、コスト削減や製品・資材のステータス可視化のほか、属人化していた受発注情報の共有化による内部不正防止や統制にも役立ちます。
NEWJI DX
製造業に特化したデジタルトランスフォーメーション(DX)の実現を目指す請負開発型のコンサルティングサービスです。AI、iPaaS、および先端の技術を駆使して、製造プロセスの効率化、業務効率化、チームワーク強化、コスト削減、品質向上を実現します。このサービスは、製造業の課題を深く理解し、それに対する最適なデジタルソリューションを提供することで、企業が持続的な成長とイノベーションを達成できるようサポートします。
製造業ニュース解説
製造業、主に購買・調達部門にお勤めの方々に向けた情報を配信しております。
新任の方やベテランの方、管理職を対象とした幅広いコンテンツをご用意しております。
お問い合わせ
コストダウンが利益に直結する術だと理解していても、なかなか前に進めることができない状況。そんな時は、newjiのコストダウン自動化機能で大きく利益貢献しよう!
(β版非公開)