- お役立ち記事
- Basics of CAN communication technology, application to in-vehicle electronic control network development, and troubleshooting measures
Basics of CAN communication technology, application to in-vehicle electronic control network development, and troubleshooting measures
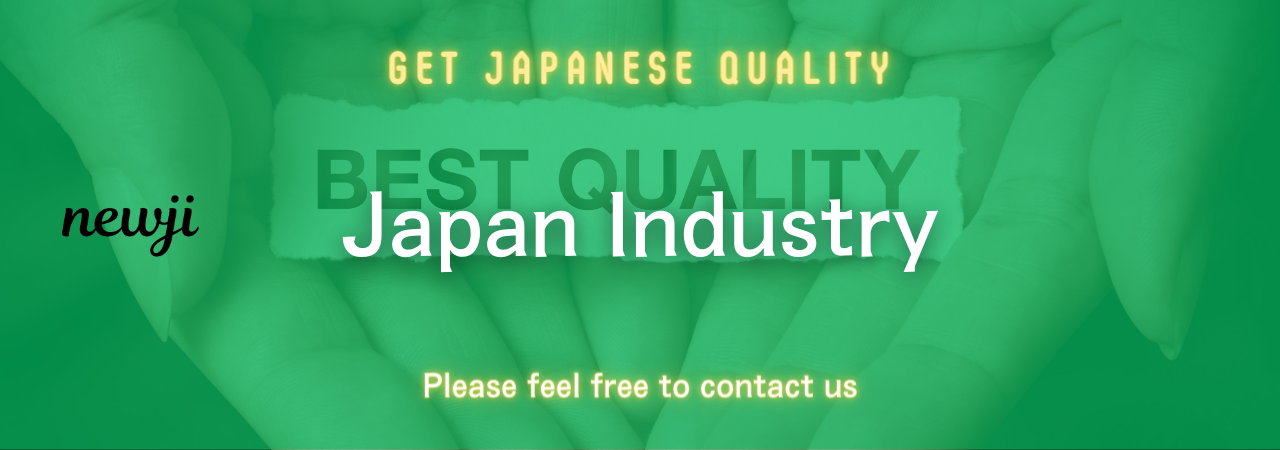
目次
Understanding CAN Communication Technology
Controller Area Network, commonly referred to as CAN, is a robust communication protocol aptly suited for in-vehicle electronic control networks.
It was originally developed by Bosch in the 1980s to enable microcontrollers and devices to communicate with each other without needing a host computer.
Given the complex nature of modern vehicles, which incorporate numerous electronic control units (ECUs), CAN has become an essential backbone for communication within automotive systems.
Why CAN is Important in Vehicles
The importance of CAN communication technology lies in its efficiency and reliability.
It provides a simplified two-wire bus that reduces wiring complexity and cost.
This reduction in wiring not only makes vehicles lighter but also minimizes potential points of failure.
Moreover, CAN can handle the noisy environment of an automobile, ensuring that data transmission is resilient and reliable.
It allows multiple ECUs in a vehicle to communicate with one another, enabling more efficient and coordinated operation.
Basic Components of CAN Communication
Understanding the basics of CAN communication involves familiarizing oneself with its core components:
1. **Nodes**: These are the devices or ECUs connected to the CAN.
Each node is capable of sending and receiving messages.
2. **Bus**: This refers to the medium that transfers information between nodes.
The bus can incorporate two wires, namely CAN High and CAN Low, forming a differential pair that enhances resilience against electromagnetic interference.
3. **Messages**: CAN communication is message-based, with each message holding a unique identifier that determines its priority on the network.
Messages are transmitted within data frames.
4. **Frames**: CAN uses different types of frames, such as data, remote, overload, and error frames, to structure the communication process.
Data frames contain the actual transmitted data.
Applications in Vehicle Electronic Control Network Development
CAN communication plays a significant role across multiple automotive applications.
It helps manage data traffic between various ECUs, ensuring vital operations such as engine control, transmission, antilock braking, airbag system deployment, and infotainment systems are seamlessly integrated.
Furthermore, CAN technology is pivotal in developing advanced driver-assistance systems (ADAS), which are essential for modern vehicle safety enhancements.
These applications rely on real-time data exchange to allow features like adaptive cruise control and collision avoidance to function effectively.
Troubleshooting CAN Communication Issues
Despite its robustness, CAN systems may still encounter issues, particularly during initial network setup or when hardware components experience wear or damage.
Troubleshooting these problems efficiently is vital to ensure optimal vehicle performance.
1. **Check Physical Connections**: Start by ensuring that all connections within the CAN network are secure.
Loose wiring or faulty connectors can lead to communication errors or complete transmission failures.
Inspect the bus lines for damage and verify that termination resistors are correctly installed.
2. **Analyze Error Frames**: Error frames are a key diagnostic tool in identifying issues within the CAN network.
Through these frames, the system detects and reports transmission errors, helping isolate problematic areas.
Using a CAN analyzer tool can facilitate this process by providing detailed insights into the network’s current state.
3. **Verify Node Configuration**: Ensure that each node within the network is correctly configured.
Misconfigured nodes can cause conflicts or idiosyncratic behaviors that lead to communication disturbances.
Cross-verification with initial setup parameters or ECUs’ technical documents can resolve such issues.
4. **Monitor Signal Quality**: Signal integrity is crucial in CAN communication.
Poor signal quality often results from voltage level fluctuations, electrical noise, or incorrect bit timings.
Utilize an oscilloscope to observe the waveform on the CAN bus and ensure it conforms with the expected voltage standards.
5. **Software and Firmware Updates**: Outdated software or firmware could impede network performance.
Ensure that all nodes have the latest updates, as enhancements in software often address known bugs or security vulnerabilities that impact communication.
Advancements in CAN Technology
As vehicle technology advances, CAN has also evolved to meet new demands.
Enhanced versions like CAN FD (Flexible Data-rate) and CAN XL have been developed to support higher data rates and larger payloads.
These developments are crucial for supporting modern vehicle functions that demand faster and more data-intensive communication.
Automotive developers and engineers should remain informed about these advancements to effectively implement and leverage new capabilities in their designs.
Conclusion
CAN communication technology is foundational to the development and operation of modern vehicle electronic control systems.
Its reliable, efficient, and robust nature ensures the seamless interaction between various ECUs, enabling sophisticated automotive functionalities.
By understanding the basics, applications, and troubleshooting techniques, engineers and technicians can effectively integrate and maintain CAN networks within vehicles, ultimately leading to enhanced vehicle performance and innovation.
資料ダウンロード
QCD調達購買管理クラウド「newji」は、調達購買部門で必要なQCD管理全てを備えた、現場特化型兼クラウド型の今世紀最高の購買管理システムとなります。
ユーザー登録
調達購買業務の効率化だけでなく、システムを導入することで、コスト削減や製品・資材のステータス可視化のほか、属人化していた購買情報の共有化による内部不正防止や統制にも役立ちます。
NEWJI DX
製造業に特化したデジタルトランスフォーメーション(DX)の実現を目指す請負開発型のコンサルティングサービスです。AI、iPaaS、および先端の技術を駆使して、製造プロセスの効率化、業務効率化、チームワーク強化、コスト削減、品質向上を実現します。このサービスは、製造業の課題を深く理解し、それに対する最適なデジタルソリューションを提供することで、企業が持続的な成長とイノベーションを達成できるようサポートします。
オンライン講座
製造業、主に購買・調達部門にお勤めの方々に向けた情報を配信しております。
新任の方やベテランの方、管理職を対象とした幅広いコンテンツをご用意しております。
お問い合わせ
コストダウンが利益に直結する術だと理解していても、なかなか前に進めることができない状況。そんな時は、newjiのコストダウン自動化機能で大きく利益貢献しよう!
(Β版非公開)