- お役立ち記事
- Basics of cold forging technology and points for improving forming quality and productivity and troubleshooting
月間77,185名の
製造業ご担当者様が閲覧しています*
*2025年2月28日現在のGoogle Analyticsのデータより
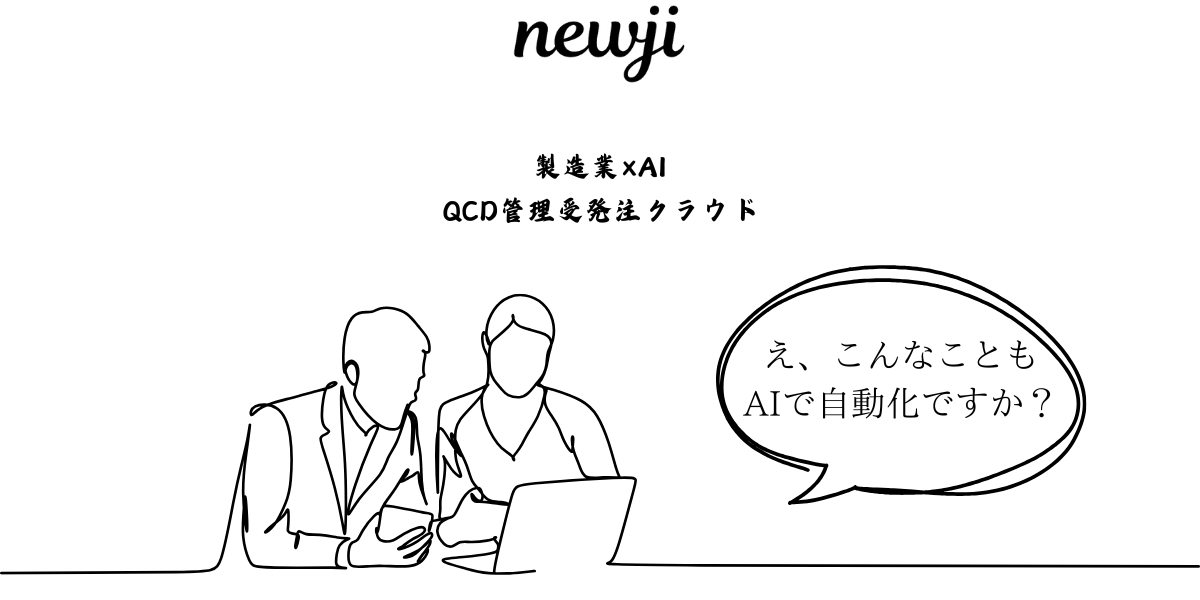
Basics of cold forging technology and points for improving forming quality and productivity and troubleshooting
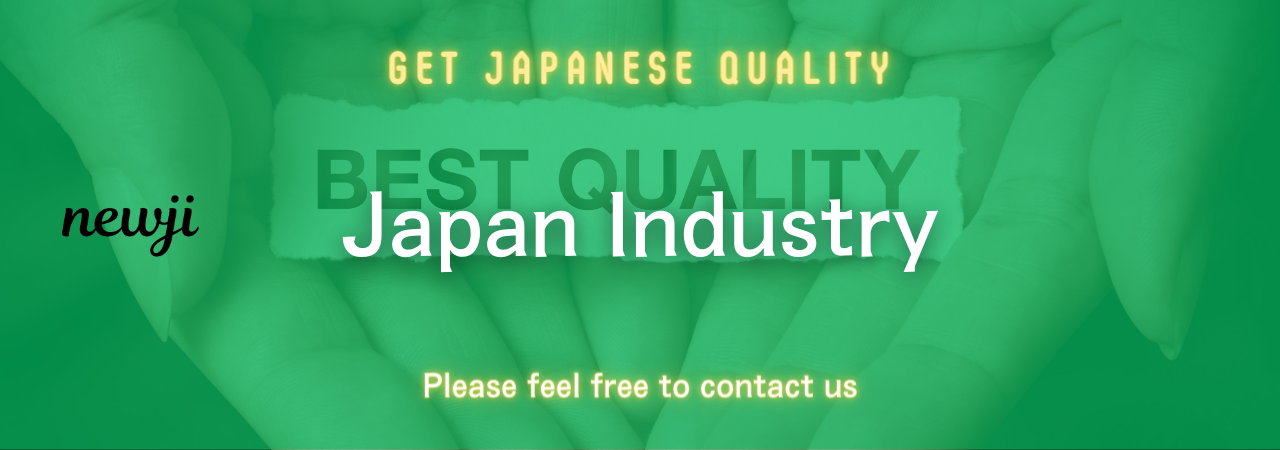
目次
Understanding Cold Forging Technology
Cold forging is a metal shaping process that involves the deformation of metal blanks into desired shapes at room temperature.
This advanced manufacturing technique is preferred in various industries, such as automotive, aerospace, and machinery, due to its efficiency in producing high-strength, precise parts.
Advantages of Cold Forging
One of the main advantages of cold forging is its ability to produce parts with enhanced mechanical properties.
The process increases the strength of the material by refining its grain structure.
Moreover, cold forging minimizes material waste and reduces the need for machining, resulting in cost savings.
Another benefit is that cold forging allows for high production speeds.
This is particularly advantageous in mass production, where time efficiency is crucial.
The process also offers excellent repeatability and dimensional accuracy, which ensures consistency in manufacturing.
Basic Steps in Cold Forging
The cold forging process typically begins with the selection of appropriate materials.
Commonly used metals include aluminum, steel, copper, and alloys, chosen based on the application’s requirements.
The selected metal blank is placed in a die, a tool that imparts the desired shape.
Pressure is applied using a punch or a machine to deform the metal without heating it.
The extreme forces cause the metal to fill the contours of the die, forming the precise shape.
Improving Forming Quality in Cold Forging
Achieving optimal forming quality in cold forging involves several crucial considerations.
Material Selection
Choosing the right material is essential for improving forming quality.
Factors such as ductility, hardness, and tensile strength influence how the metal will behave under pressure.
Metals with high ductility are preferred as they are more likely to undergo deformation without cracking.
Tool Design
The design and quality of the tooling used in cold forging are paramount for accuracy and longevity.
Designs should ensure even distribution of stress to prevent tool wear and extend lifespan.
Precision in tool manufacturing enhances the dimensional accuracy of the final product.
Lubrication
Proper lubrication is critical to reduce friction between the metal and the tooling surfaces.
It prevents tool wear and improves the finish of the forged part.
The right lubricants can also facilitate the flow of material, ensuring better fill of the die and reducing the risk of defects.
Enhancing Productivity in Cold Forging
Productivity improvements in cold forging are vital for meeting market demands effectively.
Automation
Integrating automation in cold forging processes speeds up production and enhances precision.
Robotic systems can handle repetitious tasks, reducing human error and increasing output consistency.
Automation also allows for better monitoring of processes, enabling quick adjustments to maintain quality.
Maintenance Strategies
Scheduled maintenance and timely inspection of equipment ensure that the machinery operates at peak efficiency.
Preventive maintenance can reduce unexpected downtimes, thereby boosting productivity and extending the life of tooling and machines.
Lean Manufacturing Techniques
Adopting lean manufacturing principles can streamline processes and eliminate waste.
Implementing continuous improvement practices such as Kaizen fosters an environment where efficiency improvements are regularly sought.
This approach not only boosts productivity but also enhances product quality.
Troubleshooting Common Issues in Cold Forging
Despite its advantages, cold forging can present challenges that require effective solutions.
Surface Defects
Surface defects like cracks and scratches can occur, often due to incorrect material choice or inadequate lubrication.
Ensuring that lubricants are aptly applied and selecting suitable materials can mitigate these issues.
Regular tool inspection and maintenance also play a crucial role in preventing surface imperfections.
Dimensional Inaccuracies
Achieving the right dimensions is critical, yet sometimes parts may not meet the required specifications.
This can stem from tool wear or improper alignment.
Regular calibration of tools and machinery ensures parts stay within tolerance levels.
Tool Wear
Tool wear is a common issue that can adversely affect product quality and increase production costs.
Hardening and coating tools can enhance their durability.
Frequent inspection and maintenance practices, coupled with proper material and lubrication choices, help minimize wear.
Conclusion
Cold forging technology remains a pivotal technique in manufacturing, offering numerous benefits in terms of strength, precision, and efficiency.
Understanding the process and focusing on material selection, tool design, and lubrication can significantly enhance forming quality.
Embracing productivity improvements through automation, maintenance, and lean principles ensures competitiveness and operational success.
By troubleshooting common issues effectively, manufacturers can maximize the advantages of cold forging, delivering high-quality products consistently.
資料ダウンロード
QCD管理受発注クラウド「newji」は、受発注部門で必要なQCD管理全てを備えた、現場特化型兼クラウド型の今世紀最高の受発注管理システムとなります。
ユーザー登録
受発注業務の効率化だけでなく、システムを導入することで、コスト削減や製品・資材のステータス可視化のほか、属人化していた受発注情報の共有化による内部不正防止や統制にも役立ちます。
NEWJI DX
製造業に特化したデジタルトランスフォーメーション(DX)の実現を目指す請負開発型のコンサルティングサービスです。AI、iPaaS、および先端の技術を駆使して、製造プロセスの効率化、業務効率化、チームワーク強化、コスト削減、品質向上を実現します。このサービスは、製造業の課題を深く理解し、それに対する最適なデジタルソリューションを提供することで、企業が持続的な成長とイノベーションを達成できるようサポートします。
製造業ニュース解説
製造業、主に購買・調達部門にお勤めの方々に向けた情報を配信しております。
新任の方やベテランの方、管理職を対象とした幅広いコンテンツをご用意しております。
お問い合わせ
コストダウンが利益に直結する術だと理解していても、なかなか前に進めることができない状況。そんな時は、newjiのコストダウン自動化機能で大きく利益貢献しよう!
(β版非公開)