- お役立ち記事
- Basics of Compression Molding and Its Applications for SMEs
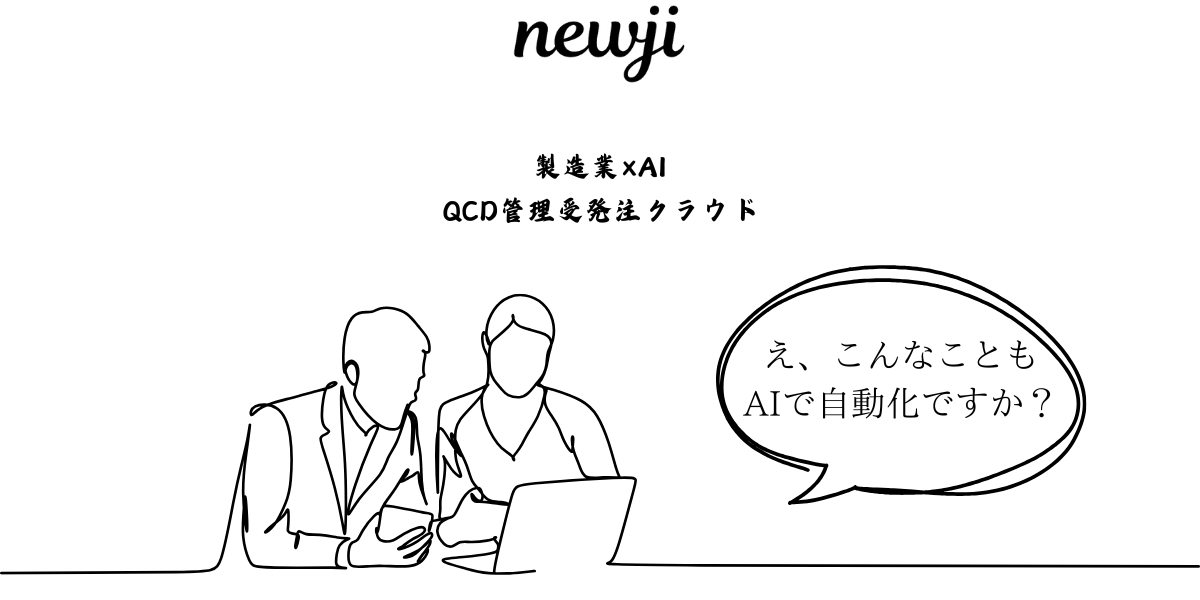
Basics of Compression Molding and Its Applications for SMEs
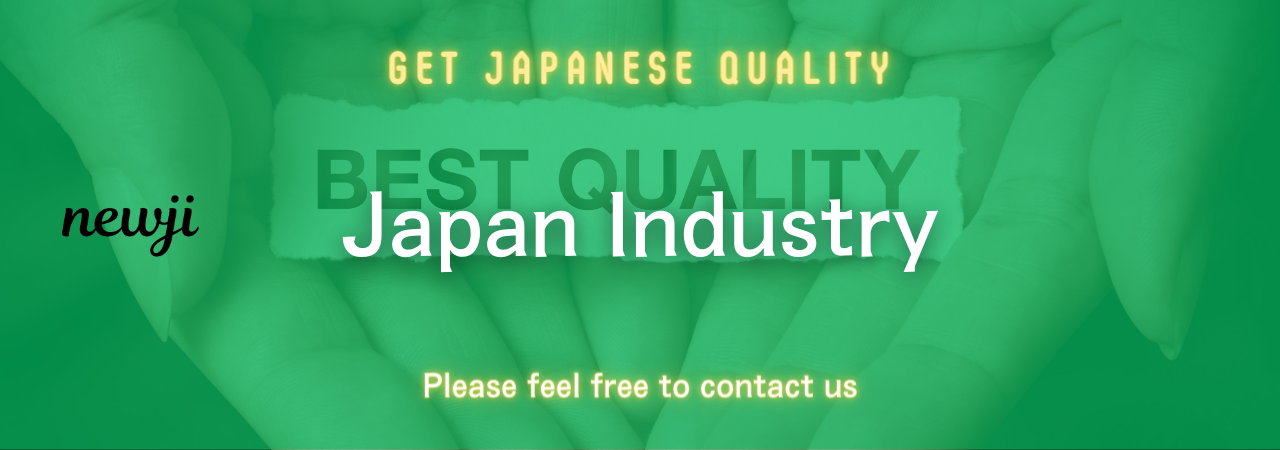
目次
Understanding Compression Molding
Compression molding is a popular manufacturing process used to shape various materials into desired forms by applying heat and pressure.
This process involves placing a material, often a thermosetting resin or rubber, into a heated mold cavity.
As the material heats, it softens and is forced into the shape of the mold by applying pressure.
Once the material has cured and cooled, it solidifies, and the molded part can be ejected from the mold.
This technique is widely used in the production of large and simpler parts, leveraging its ability to produce high-quality products with minimal waste.
Compression molding is especially efficient for high-volume manufacturing runs, making it a viable solution for small and medium-sized enterprises (SMEs) looking to optimize production and reduce costs.
The Process of Compression Molding
The compression molding process can be broken down into several key steps:
1. **Material Preparation**: First, the raw material must be measured and prepared.
This material, which could be in a preform or granular form, is often preheated to reduce curing time and ensure an even distribution in the mold.
2. **Loading the Mold**: The preheated material is loaded into a heated mold cavity.
This mold has been designed based on the specific dimensions and requirements of the part to be produced.
3. **Applying Heat and Pressure**: The mold is closed, and heat and pressure are applied.
This causes the material to flow and fill the mold cavity, taking on its shape.
Pressure must be maintained to prevent the formation of voids and ensure a uniform product.
4. **Curing and Cooling**: The material is allowed to cure, usually under continued pressure and heat.
Once the curing is complete, the mold is cooled so that the material can solidify.
5. **Ejecting the Part**: Once the part has cooled and solidified, it is ejected from the mold.
Materials Used in Compression Molding
Compression molding can accommodate a wide range of materials, each with unique properties suitable for different applications:
– **Thermosetting Plastics**: These materials undergo an irreversible chemical reaction when cured.
Common thermosetting plastics used in compression molding include phenolics, melamine, and epoxy resins.
– **Rubber Compounds**: Often used in the automotive industry, rubber compounds can be precisely shaped through compression molding, making them ideal for tires, seals, and other flexible components.
– **Fiberglass and Other Composites**: Composites combine multiple materials to enhance strength and durability.
Fiberglass sheets and other composites are frequently used in applications that require lightweight yet tough materials.
Advantages of Compression Molding for SMEs
For small and medium-sized enterprises, compression molding offers several advantages, making it a preferred manufacturing process:
Cost-Effectiveness
Compression molding is generally less costly than other molding techniques, like injection molding.
This cost efficiency is due in part to the relatively low cost of the molds and materials.
SMEs can thus benefit from lower production expenses while still producing high-quality parts.
Reduced Waste
The process is designed to make the most of the raw materials, with minimal waste produced during molding.
Any excess material can often be reused, which is not only environmentally friendly but also reduces costs associated with handling waste.
Ability to Mold Large Parts
Unlike some other manufacturing processes, compression molding can produce relatively large parts in one sequence, which is essential for reducing assembly time and costs.
This is particularly beneficial for industries like automotive and aerospace, where larger components are common.
Versatility
Compression molding is versatile and can be used for various applications, suitable for producing a wide range of products.
This flexibility means that SMEs can utilize the same basic process across multiple product lines, streamlining production and simplifying inventory management.
Applications of Compression Molding
The versatility of compression molding means it finds applications across diverse industries:
Automotive Industry
Compression molding is widely used in the automotive industry to produce components such as brake pads, gaskets, bumpers, and dashboards.
The process allows for the production of durable yet lightweight parts that meet the stringent safety and quality standards required for automotive use.
Electronics and Electrical Industry
In the electronics industry, compression molding is employed to make components like connectors, switches, and housing for electronic devices.
Thermosetting plastics are particularly suited for these applications due to their insulating properties and resistance to heat.
Consumer Goods
Everyday items like kitchenware, toys, and appliance parts can be efficiently manufactured using compression molding.
The process ensures durable and aesthetically appealing products, crucial for maintaining customer satisfaction.
Aerospace Industry
In aerospace, components require materials that provide high strength-to-weight ratios and are capable of withstanding extreme conditions.
The use of composites such as fiberglass in compression molding meets these demands, making it a valuable process for producing aerospace parts.
Conclusion
For small and medium-sized enterprises, understanding the basics of compression molding and its applications is crucial for optimizing production efficiency, reducing costs, and ensuring high-quality output.
The flexibility offered by this manufacturing process allows SMEs to compete in various markets, from automotive to consumer goods.
As sustainability continues to influence manufacturing decisions, the reduced waste and cost-effectiveness of compression molding present additional incentives for its adoption.
By leveraging the strengths of compression molding, SMEs can enhance their competitive edge and drive growth in an ever-evolving industrial landscape.
資料ダウンロード
QCD調達購買管理クラウド「newji」は、調達購買部門で必要なQCD管理全てを備えた、現場特化型兼クラウド型の今世紀最高の購買管理システムとなります。
ユーザー登録
調達購買業務の効率化だけでなく、システムを導入することで、コスト削減や製品・資材のステータス可視化のほか、属人化していた購買情報の共有化による内部不正防止や統制にも役立ちます。
NEWJI DX
製造業に特化したデジタルトランスフォーメーション(DX)の実現を目指す請負開発型のコンサルティングサービスです。AI、iPaaS、および先端の技術を駆使して、製造プロセスの効率化、業務効率化、チームワーク強化、コスト削減、品質向上を実現します。このサービスは、製造業の課題を深く理解し、それに対する最適なデジタルソリューションを提供することで、企業が持続的な成長とイノベーションを達成できるようサポートします。
オンライン講座
製造業、主に購買・調達部門にお勤めの方々に向けた情報を配信しております。
新任の方やベテランの方、管理職を対象とした幅広いコンテンツをご用意しております。
お問い合わせ
コストダウンが利益に直結する術だと理解していても、なかなか前に進めることができない状況。そんな時は、newjiのコストダウン自動化機能で大きく利益貢献しよう!
(Β版非公開)