- お役立ち記事
- Basics of control engineering/PID control, gain tuning technology, and its key points that even beginners can understand
月間77,185名の
製造業ご担当者様が閲覧しています*
*2025年2月28日現在のGoogle Analyticsのデータより
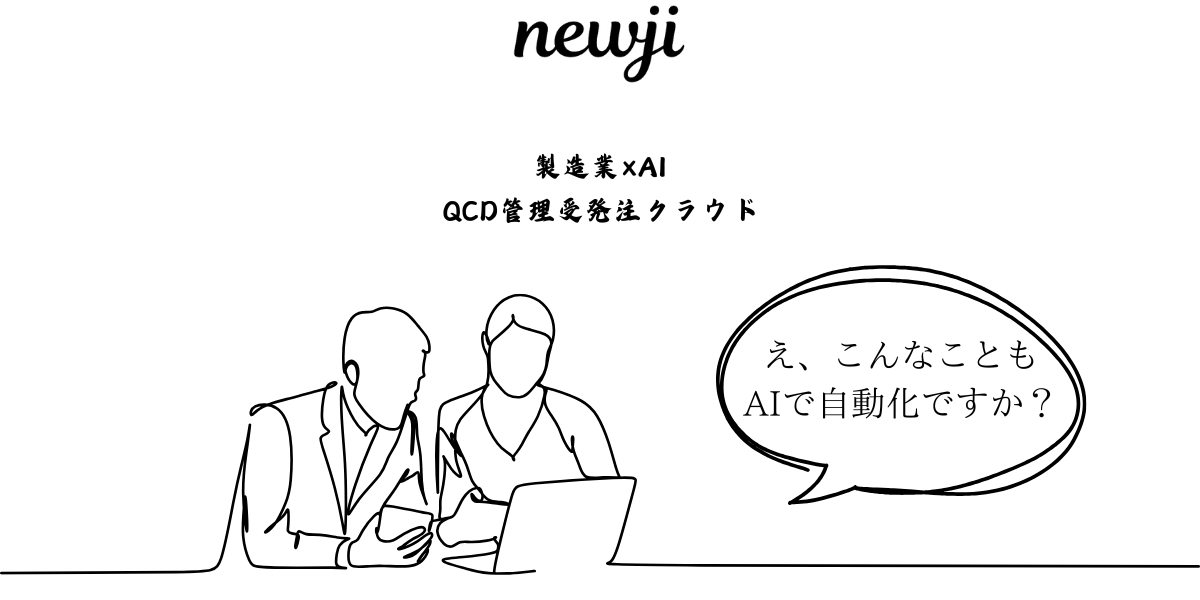
Basics of control engineering/PID control, gain tuning technology, and its key points that even beginners can understand
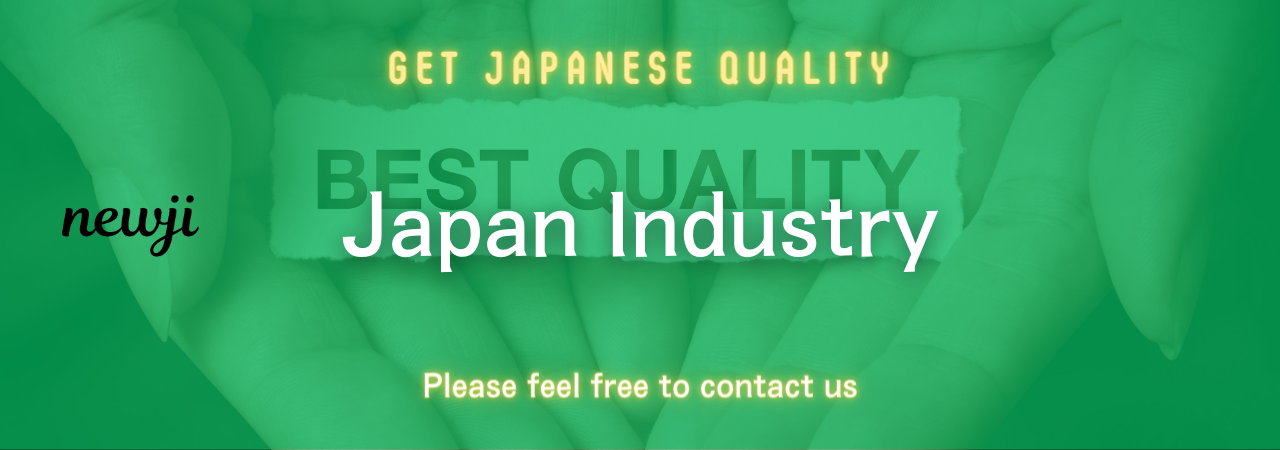
目次
What is Control Engineering?
Control engineering is a branch of engineering that applies control theory to design systems with desired behaviors.
It plays a crucial role in various fields, including automotive, aerospace, manufacturing, and robotics.
Essentially, control engineering involves managing and regulating the operations of systems to achieve specific performance criteria.
Control systems are everywhere, from the cruise control in your car to the climate control in your home.
These systems work by maintaining a desired output even in the presence of disturbances or changes in the environment.
Understanding PID Control
One of the most common control strategies used in control engineering is PID control.
PID stands for Proportional-Integral-Derivative.
This method uses a control loop feedback mechanism to control process variables and is widely used in industrial control systems.
The PID controller calculates an error value as the difference between a desired setpoint and a measured process variable.
It then applies a correction based on proportional, integral, and derivative terms.
Proportional Control
The proportional component of a PID controller reacts to the current error.
It provides an output that is proportional to the input error.
If the error is large, the proportional response will be large as well.
However, one downside to proportional control is that it may not eliminate the error entirely.
This can result in a steady-state error where the system stabilizes but not at the desired setpoint.
Integral Control
The integral component addresses the steady-state error issue that can occur with proportional control.
By integrating the error over time, it accumulates past errors, effectively summing them for correction.
This allows the system to eliminate the steady-state error and bring the process variable to the desired setpoint.
Derivative Control
The derivative component predicts future behavior by considering the rate of change of the error.
It provides a damping effect and reduces the overshoot introduced by the integral component.
Derivative control helps stabilize the system and improves the overall dynamic response.
Gain Tuning in PID Control
Gain tuning is the process of setting the optimal values for the proportional, integral, and derivative gains in a PID controller.
Proper gain tuning is vital to achieving system stability and desired performance.
Manual Tuning
One method of gain tuning is manual tuning.
It involves adjusting the gains based on the system’s response while observing its behavior.
The process starts by setting the integral and derivative gains to zero.
The proportional gain is then increased until the system oscillates, identifying the critical gain.
At this point, the integral gain is adjusted to eliminate the steady-state error, and the derivative gain is used to fine-tune the response, reducing overshoot and oscillations.
Manual tuning is straightforward, but it requires experience and time to achieve satisfactory results.
Ziegler-Nichols Tuning
The Ziegler-Nichols method is a more systematic approach to gain tuning.
This method involves increasing the proportional gain while keeping the integral and derivative gains at zero until the system begins to oscillate steadily.
The gain at which this occurs is called the ultimate gain, and the period of oscillation is the ultimate period.
Based on these parameters, the Ziegler-Nichols table provides recommended PID gain values to achieve a desired response.
While this method is easier than manual tuning, it may not always provide optimal results for all systems.
Auto-Tuning
Auto-tuning is a modern approach where advanced algorithms automatically calculate the optimal PID gains.
This method uses data and models to adjust the gains based on system performance and desired criteria.
Auto-tuning is especially useful in complex systems where manual tuning is challenging.
It saves time and ensures consistent results.
Key Points to Remember
Understanding the basics of control engineering and PID control is essential for optimizing system performance.
Here are key points to consider:
– **System Analysis**: Before implementing a PID controller, analyze the system’s dynamics and behavior to determine the best control strategy.
– **Gain Tuning**: Properly tune the PID gains to ensure stability and achieve the desired response.
– **Testing and Validation**: After tuning, rigorously test the system under various conditions to validate its performance.
– **Continuous Improvement**: Control systems should be regularly updated and adjusted based on performance data and changing conditions.
By mastering these fundamentals, beginners can effectively utilize control engineering principles and PID control to enhance the efficiency and stability of various systems.
資料ダウンロード
QCD管理受発注クラウド「newji」は、受発注部門で必要なQCD管理全てを備えた、現場特化型兼クラウド型の今世紀最高の受発注管理システムとなります。
ユーザー登録
受発注業務の効率化だけでなく、システムを導入することで、コスト削減や製品・資材のステータス可視化のほか、属人化していた受発注情報の共有化による内部不正防止や統制にも役立ちます。
NEWJI DX
製造業に特化したデジタルトランスフォーメーション(DX)の実現を目指す請負開発型のコンサルティングサービスです。AI、iPaaS、および先端の技術を駆使して、製造プロセスの効率化、業務効率化、チームワーク強化、コスト削減、品質向上を実現します。このサービスは、製造業の課題を深く理解し、それに対する最適なデジタルソリューションを提供することで、企業が持続的な成長とイノベーションを達成できるようサポートします。
製造業ニュース解説
製造業、主に購買・調達部門にお勤めの方々に向けた情報を配信しております。
新任の方やベテランの方、管理職を対象とした幅広いコンテンツをご用意しております。
お問い合わせ
コストダウンが利益に直結する術だと理解していても、なかなか前に進めることができない状況。そんな時は、newjiのコストダウン自動化機能で大きく利益貢献しよう!
(β版非公開)