- お役立ち記事
- Basics of corrosion and stress corrosion cracking and key points for damage prevention measures
月間76,176名の
製造業ご担当者様が閲覧しています*
*2025年3月31日現在のGoogle Analyticsのデータより
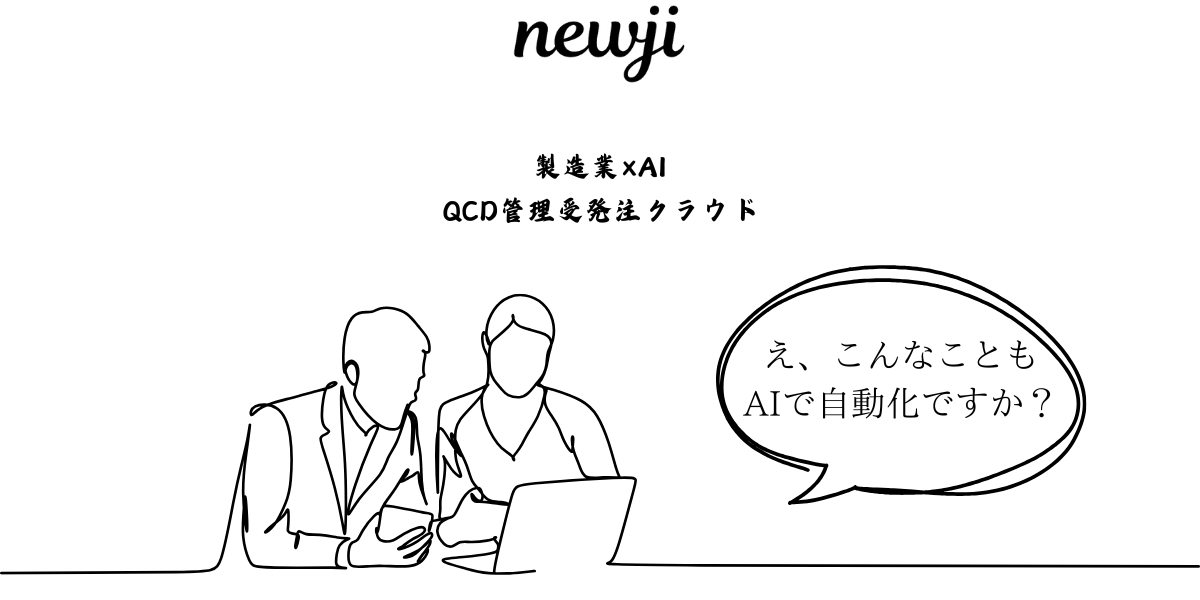
Basics of corrosion and stress corrosion cracking and key points for damage prevention measures
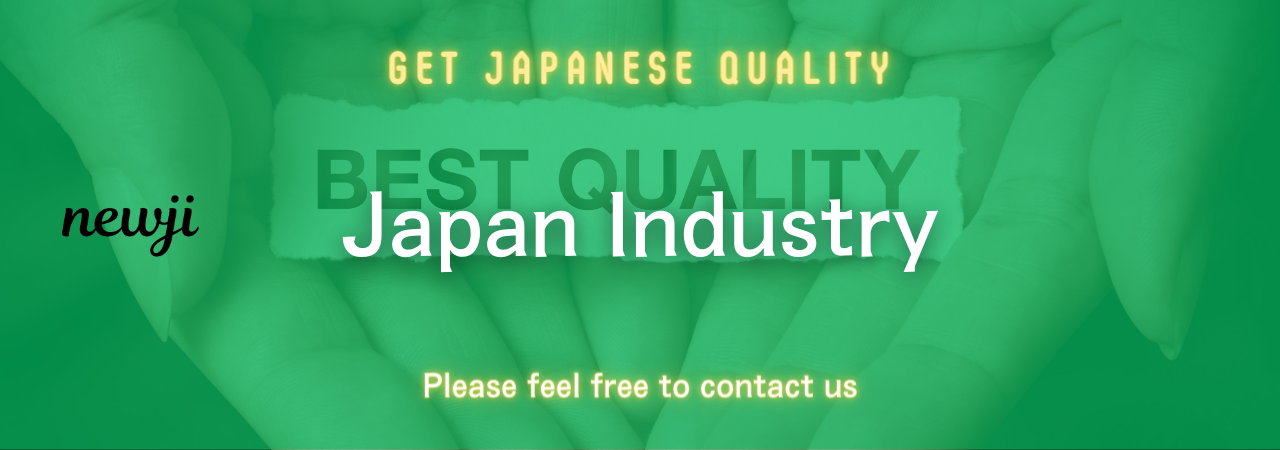
目次
Understanding Corrosion
Corrosion is a natural process that gradually destroys metals through chemical reactions with environmental elements.
Most often, this involves the interaction with oxygen in the presence of moisture, leading to the formation of oxides.
This process is primarily recognized as rust in iron and steel.
Corrosion can severely impact the longevity and structural integrity of materials used in various industries, from construction to transportation.
The rate of corrosion can vary depending on several factors such as temperature, humidity, and the presence of salts or acids.
In some cases, corrosion may occur uniformly across a metal’s surface.
In other scenarios, it may be localized, resulting in pits or cracks that can be catastrophic if not detected early.
Therefore, understanding and mitigating corrosion is crucial for ensuring the safety and durability of metallic structures and components.
What is Stress Corrosion Cracking?
Stress corrosion cracking (SCC) is a specialized form of corrosion that results in the formation of cracks in metals under tensile stress within a corrosive environment.
Unlike traditional corrosion that slowly erodes a metal’s surface, SCC can cause sudden and catastrophic failures without a significant loss of material.
The primary conditions for SCC to occur include a susceptible material, the presence of tensile stress, and a corrosive medium.
Common environments causing SCC are chloride, iodide, and sulfuric atmospheres, making certain metals such as stainless steel, aluminum alloys, and brass particularly vulnerable.
The process involves the slow propagation of cracks, often starting at surface defects or inclusions.
These cracks can rapidly evolve and compromise the structural integrity of the material.
Key Points for Damage Prevention Measures
Preventing corrosion and SCC requires a blend of strategic material selection, protective coatings, environmental modifications, and regular maintenance.
Material Selection
Choosing the right material is the first step in mitigating corrosion and SCC.
Materials that inherently resist corrosion such as stainless steels and certain nickel-based alloys can be excellent choices.
When selecting materials, it is essential to consider the specific environment in which they will be used.
For example, using materials with higher chromium content can enhance resistance to chloride-induced SCC.
Protective Coatings
Applying protective coatings can significantly reduce the exposure of metal surfaces to corrosive environments.
Coatings can be metallic, such as galvanization, or non-metallic, like paint or polymer layers.
These barriers help prevent moisture and corrosive agents from reaching the metal surface, thereby slowing down the corrosion process.
Periodic inspection and maintenance of these coatings are critical to ensure their effectiveness over time.
Cathodic Protection
Cathodic protection is an electrochemical method that prevents corrosion by converting the entire metal surface into the cathode of an electrochemical cell.
This process involves attaching a more easily corroded “sacrificial” metal to the metal needing protection.
The sacrificial metal corrodes instead of the protected metal, thus extending its longevity.
Common applications of cathodic protection include pipelines, ship hulls, and offshore platforms.
Stress Reduction Techniques
Since tensile stress is a primary factor in SCC, reducing or eliminating these stresses can help in prevention.
This can be done through proper design, material treatment, or stress relief annealing.
Designs that minimize abrupt changes in section size and avoid sharp corners can reduce stress concentrations.
Residual stresses caused by welding or machining can be relieved through processes like heat treatment.
Environmental Modifications
Changing the environment where the metal is used can also aid in preventing corrosion.
This can be as simple as dehumidification to reduce moisture levels or controlling the pH level of the surrounding medium.
In industrial settings, inhibitors may be added to corrosive substances to neutralize their effects.
Proper insulation and drainage systems can further prevent water accumulation on surfaces.
Regular Inspections and Maintenance
Routine inspections and maintenance are vital for early detection and prevention of both corrosion and stress corrosion cracking.
By identifying surface changes, pitting, or initial crack formations early on, corrective measures can be implemented before issues escalate.
Tools such as ultrasonics, radiography, and magnetic particle inspections can be employed for non-destructive testing of critical components.
Conclusion
Corrosion and stress corrosion cracking are significant concerns that can lead to the failure of metal structures and components.
Understanding the basics of these destructive processes allows industries to implement effective prevention strategies.
By focusing on material selection, protective measures, stress reduction, environmental control, and regular maintenance, the life span and functionality of metallic structures can be greatly enhanced.
Proactive approaches in design and maintenance not only protect investments but also ensure safety standards are met, thus preventing potential accidents and operational downtime.
資料ダウンロード
QCD管理受発注クラウド「newji」は、受発注部門で必要なQCD管理全てを備えた、現場特化型兼クラウド型の今世紀最高の受発注管理システムとなります。
ユーザー登録
受発注業務の効率化だけでなく、システムを導入することで、コスト削減や製品・資材のステータス可視化のほか、属人化していた受発注情報の共有化による内部不正防止や統制にも役立ちます。
NEWJI DX
製造業に特化したデジタルトランスフォーメーション(DX)の実現を目指す請負開発型のコンサルティングサービスです。AI、iPaaS、および先端の技術を駆使して、製造プロセスの効率化、業務効率化、チームワーク強化、コスト削減、品質向上を実現します。このサービスは、製造業の課題を深く理解し、それに対する最適なデジタルソリューションを提供することで、企業が持続的な成長とイノベーションを達成できるようサポートします。
製造業ニュース解説
製造業、主に購買・調達部門にお勤めの方々に向けた情報を配信しております。
新任の方やベテランの方、管理職を対象とした幅広いコンテンツをご用意しております。
お問い合わせ
コストダウンが利益に直結する術だと理解していても、なかなか前に進めることができない状況。そんな時は、newjiのコストダウン自動化機能で大きく利益貢献しよう!
(β版非公開)