- お役立ち記事
- Basics of data analysis using AHP and effective practical usage methods in the manufacturing industry
月間76,176名の
製造業ご担当者様が閲覧しています*
*2025年3月31日現在のGoogle Analyticsのデータより
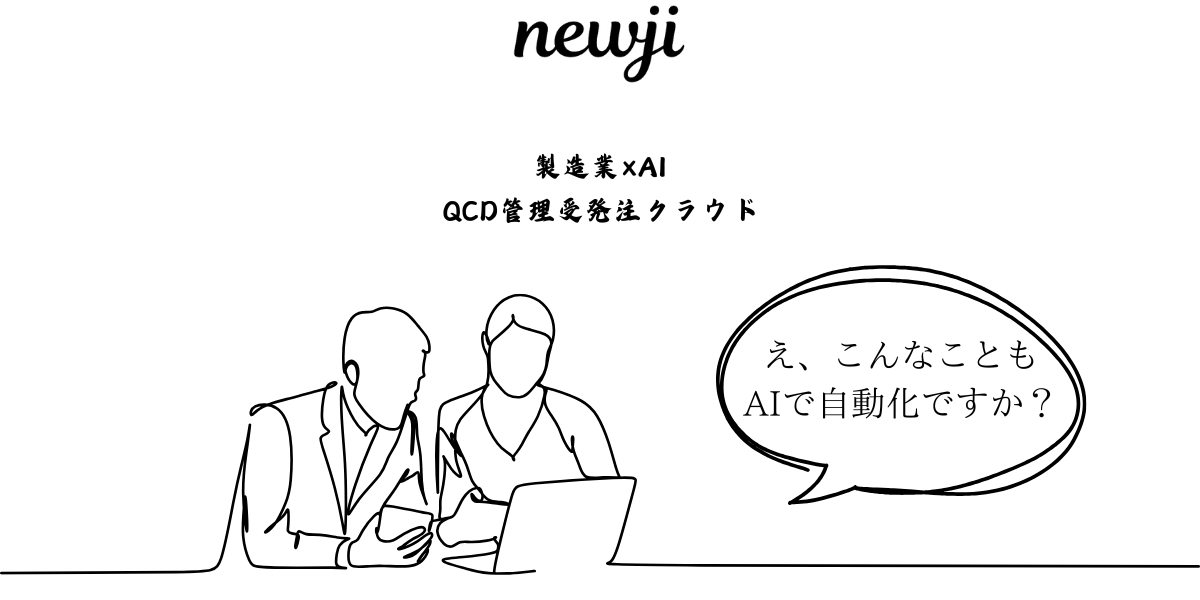
Basics of data analysis using AHP and effective practical usage methods in the manufacturing industry
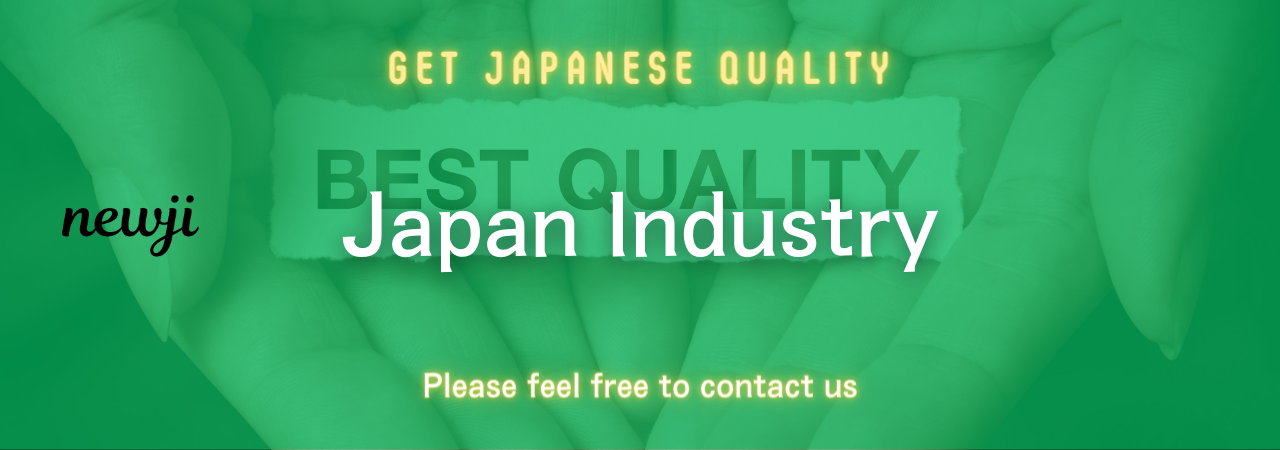
目次
Understanding AHP in Data Analysis
The Analytic Hierarchy Process, commonly known as AHP, is a powerful decision-making tool used in data analysis and various industries, including manufacturing.
The AHP methodology helps in organizing and analyzing complex decisions based on mathematics and psychology.
By breaking down the decision-making problem into smaller, more understandable parts, AHP allows organizations to streamline their processes and make informed choices.
In the backdrop of the manufacturing industry, where precision and efficiency are paramount, AHP serves as a critical element in data-driven decision-making.
What is AHP?
AHP was developed by Thomas L. Saaty in the 1970s.
It’s a structured technique for organizing and analyzing complex decisions.
Using AHP, decisions are broken down into a hierarchy of more easily comprehensible sub-problems, each of which can be analyzed independently.
The elements of this hierarchy can relate to any aspect of the decision, and they can include tangible or intangible criteria.
To simplify, think of AHP as a decision tree.
The top is the ultimate decision or goal, and each branch signifies a sub-factor influencing that choice.
Participants in the decision-making process rate the importance of each factor in comparison with others, usually on a scale.
Through these comparisons, AHP converts evaluations into numerical values that can be processed and compared over the entire range of the problem.
Benefits of Using AHP in Manufacturing
In the manufacturing industry, where strategic decisions can affect production efficiency, product quality, and profitability, AHP provides clarity and precision.
Some of the main benefits include:
1. **Improved Decision Accuracy**: Breaking down complex problems allows decision-makers to evaluate all the impacting factors, ensuring a comprehensive analysis.
2. **Increased Stakeholder Buy-In**: AHP’s structured approach involves multiple stakeholders in the decision-making process, fostering collaboration and consensus.
3. **Enhanced Prioritization**: It aids in identifying the most critical factors impacting decisions, allowing for more focused resource allocation.
4. **Consistency Across Evaluations**: AHP provides a standardized method to evaluate similar problems repeatedly, ensuring consistency in decision-making.
Implementing AHP in the Manufacturing Industry
Integrating AHP into the manufacturing process necessitates a clear understanding of both the tool itself and the specific challenges faced by the industry.
Below are practical steps to implement AHP effectively:
Step 1: Define the Problem
The first step in using AHP is clearly defining the problem.
In manufacturing, this might be deciding on a new production methodology, selecting suppliers, or optimizing the supply chain.
A clearly defined problem sets the groundwork for the entire decision-making process.
Step 2: Identify Criteria and Alternatives
Next, identify all the criteria affecting the decision.
For a manufacturer, these could include cost, quality, time, and supplier reliability.
Subsequently, identify potential alternatives or solutions to the problem.
For instance, if the problem is selecting a supplier, different companies would represent the alternatives.
Step 3: Structure a Hierarchy
Organize the decision criteria into a hierarchical model, from the most significant basis for decision-making to more detailed criteria.
The top level often reflects the ultimate goal or decision, with subsequent levels breaking down the contributing factors and alternatives.
Step 4: Pairwise Comparison
This critical step involves evaluating the relative importance of each element against others through pairwise comparisons.
Manufacturers rate options by comparing how much more one criterion (like cost) ranks over another (such as quality) when selecting a supplier.
These comparisons lead to a matrix that prioritizes criteria based on the judgments provided.
Step 5: Calculate Consistency
Check the consistency of the judgments made.
The AHP includes a consistency ratio that helps measure whether decisions are fully consistent.
Inconsistencies suggest reassessment or reevaluation is necessary, ensuring the decision framework remains reliable.
Step 6: Synthesize Results
Compile all the input from the pairwise comparisons to determine the weighted scoring for each alternative.
This score indicates the best course of action based on the evaluation of different criteria.
Practical Examples of AHP in Manufacturing
To better understand AHP’s application in the manufacturing industry, consider the following scenarios:
Supplier Selection
Suppose a manufacturing company must choose among several suppliers.
Using AHP, the company can prioritize criteria such as cost, quality, delivery time, and after-sales services.
By comparing suppliers against each other using these criteria, the final decision can be objective, well-rounded, and aligned with the company’s business goals.
Production Process Optimization
A manufacturer may use AHP to decide which production process improvements should be prioritized.
Evaluating factors such as cost-effectiveness, ease of implementation, expected return on investment, and impact on production efficiency helps identify the best improvements to apply.
Product Development
In product development, AHP can assist in deciding the features that should be part of a new product.
By considering customer preferences, cost implications, technological feasibility, and competitor offerings, companies can determine the most valuable product features that will drive consumer satisfaction and competitive advantage.
Conclusion
AHP provides a structured, objective method to improve decision-making within the manufacturing industry.
Its capability to simplify complex decisions into understandable components makes it a valuable tool for manufacturing managers who aim to make informed choices.
In essence, AHP enhances decision accuracy, ensures consistent evaluations, and ultimately leads to more strategic and effective operations within the manufacturing sector.
資料ダウンロード
QCD管理受発注クラウド「newji」は、受発注部門で必要なQCD管理全てを備えた、現場特化型兼クラウド型の今世紀最高の受発注管理システムとなります。
ユーザー登録
受発注業務の効率化だけでなく、システムを導入することで、コスト削減や製品・資材のステータス可視化のほか、属人化していた受発注情報の共有化による内部不正防止や統制にも役立ちます。
NEWJI DX
製造業に特化したデジタルトランスフォーメーション(DX)の実現を目指す請負開発型のコンサルティングサービスです。AI、iPaaS、および先端の技術を駆使して、製造プロセスの効率化、業務効率化、チームワーク強化、コスト削減、品質向上を実現します。このサービスは、製造業の課題を深く理解し、それに対する最適なデジタルソリューションを提供することで、企業が持続的な成長とイノベーションを達成できるようサポートします。
製造業ニュース解説
製造業、主に購買・調達部門にお勤めの方々に向けた情報を配信しております。
新任の方やベテランの方、管理職を対象とした幅広いコンテンツをご用意しております。
お問い合わせ
コストダウンが利益に直結する術だと理解していても、なかなか前に進めることができない状況。そんな時は、newjiのコストダウン自動化機能で大きく利益貢献しよう!
(β版非公開)