- お役立ち記事
- Basics of delayed fracture and hydrogen embrittlement and points to prevent fracture accidents
Basics of delayed fracture and hydrogen embrittlement and points to prevent fracture accidents
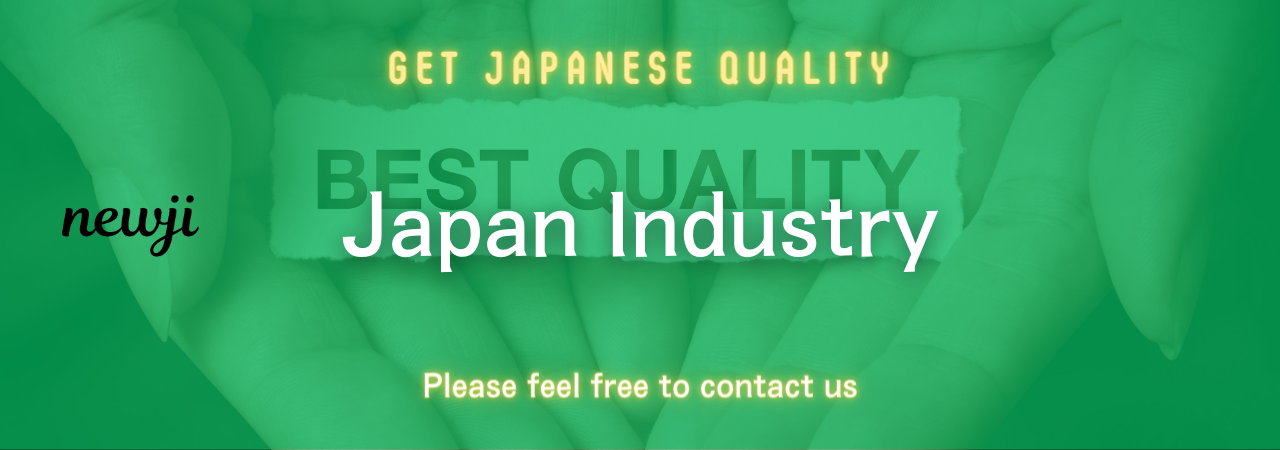
目次
What is Delayed Fracture?
Delayed fracture refers to a phenomenon where a material fails or fractures under stress after a period, instead of immediately.
This delay can range from hours to weeks after the application of stress.
The material might seem stable and intact initially but can suddenly fail without any visible warning signs.
This is particularly concerning in industries where materials are exposed to varying loads and environmental conditions.
In delayed fracture, the material undergoes microscopic changes before the final failure.
These changes, although often invisible, compromise the material’s strength and durability over time.
Delayed fracture is most commonly associated with metals, especially high-strength steels.
Understanding Hydrogen Embrittlement
Hydrogen embrittlement is a specific type of delayed fracture caused by the absorption of hydrogen into a material.
When hydrogen atoms diffuse into a metal, they can make the metal brittle and reduce its load-bearing capabilities.
Even very small amounts of hydrogen can have significant impacts on the material’s performance.
This embrittlement is concerning for industries that use metals in harsh environments where exposure to hydrogen is possible.
Processes like welding, corrosion, or being in contact with hydrogenated environments can all introduce hydrogen into metals.
When the embrittlement occurs, the metal loses its ductility, making it more prone to cracking under stress, even if that stress is within the material’s usual capabilities.
Causes of Hydrogen Embrittlement
There are several ways hydrogen can infiltrate metals:
1. **Environmental Exposure:** Metals exposed to acidic environments or moisture can undergo corrosion, producing hydrogen as a by-product.
2. **Manufacturing Processes:** Processes like plating, pickling, or annealing can introduce hydrogen into metals.
3. **Welding and Heat Treatments:** Hydrogen can enter metals during welding from the moisture in electrodes or from the atmosphere.
Understanding these causes is crucial as it helps in identifying potential risks and taking preventive actions.
Preventing Delayed Fracture and Hydrogen Embrittlement
While completely eliminating delayed fracture is challenging, several measures can significantly reduce risk:
Material Selection
Choose materials less susceptible to hydrogen diffusion or change the composition of the metal to mitigate embrittlement.
For example, using alloys with elements that trap hydrogen can provide resistance against embrittlement.
Surface Treatments
Apply coatings or platings that act as barriers to hydrogen entry.
This could include using specialized painting, anodizing, or applying sealants.
Controlled Processing
Ensure that manufacturing processes like welding are conducted in environments with low humidity to minimize hydrogen exposure.
Also, implement proper heat treatments to remove absorbed hydrogen from metals.
Stress Management
Design structures and components considering the stress factors, and avoid high-stress concentrations, which can lead to failure.
Regular maintenance and inspection can help detect early signs of stress-related issues.
Environmental Control
Manage exposure to corrosive and hydrogen-rich environments by employing inhibitors or protective barriers.
In industries like oil and gas, regularly monitor the atmosphere for chemical exposure risks.
Why Prevention is Key
Preventing delayed fracture and hydrogen embrittlement is crucial for several reasons:
1. **Safety:** Sudden material failure can lead to catastrophic accidents, posing severe risks to individuals and infrastructure.
2. **Cost Reduction:** Repairing or replacing failed components is expensive, especially if failure leads to extensive damage.
3. **Longevity:** By preventing delayed fracture, materials and components last longer, saving time and resources.
4. **Reputation:** Companies in critical industries such as aerospace, automotive, and construction must maintain a reputation for reliability and safety.
By addressing the root causes and implementing preventive measures, the risks associated with delayed fracture and hydrogen embrittlement can be significantly minimized.
Conclusion
Understanding the mechanics behind delayed fracture and hydrogen embrittlement is crucial for industries relying on metal components and structures.
While these phenomena pose significant challenges, by selecting appropriate materials, employing advanced processing techniques, and adhering to thorough maintenance protocols, the risks can be effectively managed.
Implementing these preventive strategies ensures not only safety and reliability but also enhances the efficiency and lifespan of metal structures.
Educating stakeholders, from engineers to onsite workers, about these issues is vital to ensure the well-being of operations and personnel.
By taking proactive measures, we pave the way for safer and more reliable engineering achievements, prominently signifying the importance of investing in quality, knowledge, and vigilance.
資料ダウンロード
QCD調達購買管理クラウド「newji」は、調達購買部門で必要なQCD管理全てを備えた、現場特化型兼クラウド型の今世紀最高の購買管理システムとなります。
ユーザー登録
調達購買業務の効率化だけでなく、システムを導入することで、コスト削減や製品・資材のステータス可視化のほか、属人化していた購買情報の共有化による内部不正防止や統制にも役立ちます。
NEWJI DX
製造業に特化したデジタルトランスフォーメーション(DX)の実現を目指す請負開発型のコンサルティングサービスです。AI、iPaaS、および先端の技術を駆使して、製造プロセスの効率化、業務効率化、チームワーク強化、コスト削減、品質向上を実現します。このサービスは、製造業の課題を深く理解し、それに対する最適なデジタルソリューションを提供することで、企業が持続的な成長とイノベーションを達成できるようサポートします。
オンライン講座
製造業、主に購買・調達部門にお勤めの方々に向けた情報を配信しております。
新任の方やベテランの方、管理職を対象とした幅広いコンテンツをご用意しております。
お問い合わせ
コストダウンが利益に直結する術だと理解していても、なかなか前に進めることができない状況。そんな時は、newjiのコストダウン自動化機能で大きく利益貢献しよう!
(Β版非公開)