- お役立ち記事
- Basics of DRBFM and its application to preventing quality problems
月間77,185名の
製造業ご担当者様が閲覧しています*
*2025年2月28日現在のGoogle Analyticsのデータより
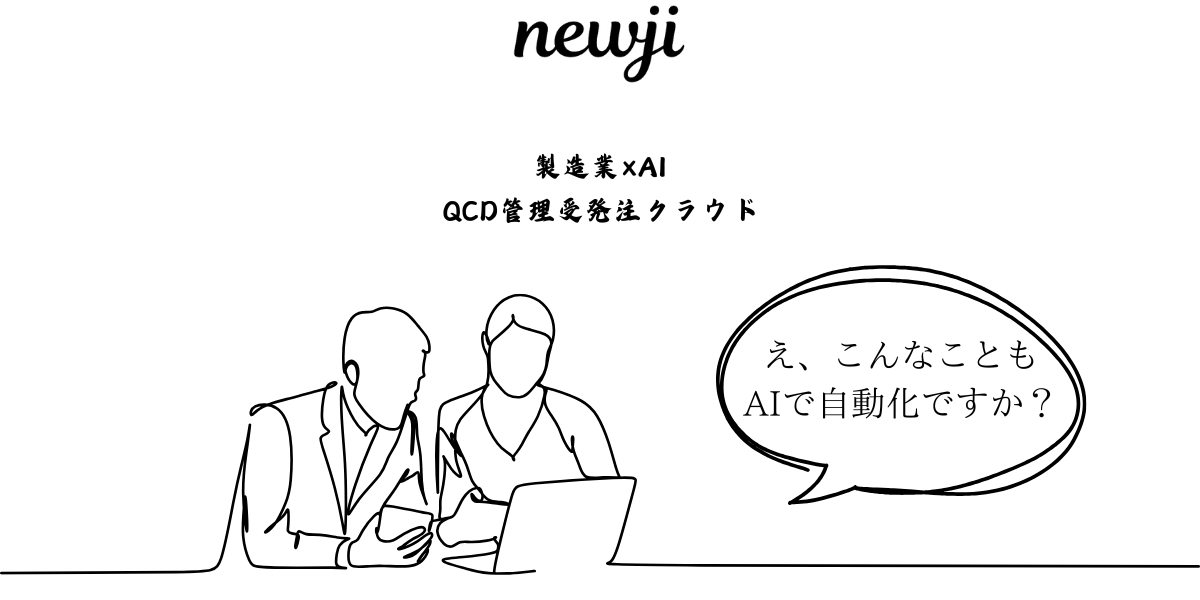
Basics of DRBFM and its application to preventing quality problems
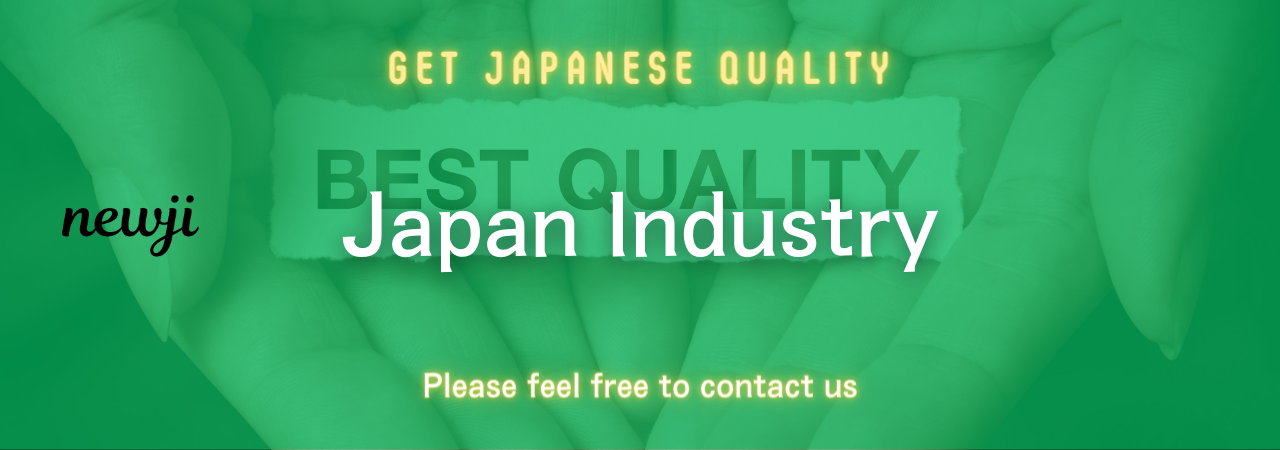
目次
Understanding DRBFM: A Quick Guide
Design Review Based on Failure Mode, commonly known as DRBFM, is a powerful methodology used in engineering and manufacturing to identify and mitigate potential quality issues before they arise.
The acronym DRBFM may sound complex, but its core principle is quite simple: focus on the changes.
By concentrating on variations and modifications in design or process, DRBFM aims to foresee potential failure modes and address them preemptively.
This proactive approach can significantly enhance the quality and reliability of products and systems.
The Birthplace of DRBFM
DRBFM was developed by Dr. Tatsuhiko Yoshimura at Toyota Motor Corporation.
Originating from the Japanese concept of “Genchi Genbutsu” or “go and see,” DRBFM emphasizes the importance of experiencing problems firsthand to fully understand and address them.
Toyota uses this method to dig deeper into changes, scrutinizing them thoroughly to predict and prevent potential issues.
Now, this efficient process has found its application across industries worldwide, helping teams maintain high standards of quality and performance.
The Core Principles of DRBFM
DRBFM stands on three fundamental pillars:
1. Good Design Practices
DRBFM encourages maintaining strong design principles.
It assumes that designs rooted in robust practices are less likely to face failures.
When changes arise, it’s critical to analyze how these modifications interact with established designs.
2. Focus on Change Points
Not all parts of a design or process need meticulous review—only those subjected to changes.
By isolating and examining adjustment points, teams can efficiently manage resources and time while ensuring thorough analysis.
3. Detailed Discussion
Dive deep into open discussions about potential implications of changes.
Effective communication among team members is crucial to anticipate and manage risks.
A collaborative environment fosters creativity in finding solutions and strengthens preventive measures.
How DRBFM Works
DRBFM involves a step-by-step approach to address changes and potential failures.
Step 1: Identify Changes
The first step in DRBFM is identifying and listing all design or process changes.
By recognizing what aspects have been altered, teams can focus their review efforts more effectively.
Step 2: Analyze Failure Modes
Once changes are identified, it’s time for a thorough examination of potential failure modes.
This means considering each modification individually and imaginatively thinking about how it might impact overall functionality.
Step 3: Evaluate the Effect of Changes
After pinpointing potential failure modes, assess how these changes might impact product quality and performance.
Consider both direct and indirect effects, looking at how one change could cascade into other areas.
Step 4: Develop Mitigation Plans
Once potential issues are identified, develop strategies to mitigate them.
These might include adjusting the design, enhancing material specifications, or changing production processes.
Create detailed action plans to address each identified risk.
Step 5: Implement and Monitor Solutions
With mitigation strategies in place, it’s time to implement them.
Follow up with continuous monitoring to ensure solutions are effective.
Refine approaches as necessary to enhance efficiency and address any new issues that arise.
The Benefits of DRBFM
DRBFM offers numerous advantages to organizations seeking to improve product quality and reliability.
Proactive Problem Solving
By focusing on potential problems before they occur, DRBFM helps in taking proactive measures.
This reduces downtime, minimizes defects, and ultimately saves costs related to rework and recalls.
Enhanced Communication
The DRBFM process fosters open discussions among team members.
This environment encourages knowledge sharing and collective problem-solving, often leading to innovative solutions.
Improved Product Reliability
Implementing DRBFM ensures that designs and processes account for potential problems, resulting in more reliable products with consistent performance.
Resource Efficiency
Focusing on change points enables teams to allocate resources efficiently.
This targeted approach ensures that time and effort are spent on areas that truly impact quality.
DRBFM in Action
Consider an automotive manufacturer implementing new technology in a vehicle model.
The DRBFM process would highlight changes such as new sensors or software updates.
By analyzing these changes, the team could anticipate potential failures, such as sensor malfunctions or software glitches.
Mitigation strategies could involve rigorous testing protocols or incorporating backup systems, thereby preventing costly defects and enhancing vehicle reliability.
Conclusion
Incorporating DRBFM into engineering and manufacturing processes is a strategic move towards achieving superior quality standards.
By focusing on changes and potential failure modes, teams can anticipate issues before they occur, saving time, resources, and reputational damage.
This method not only supports quality assurance but also promotes a culture of continuous improvement and innovation, essential for staying competitive in today’s fast-paced market.
Learning and applying the basics of DRBFM can build a robust preventive problem-solving approach, ensuring that quality remains a top priority in all product and process development endeavors.
資料ダウンロード
QCD管理受発注クラウド「newji」は、受発注部門で必要なQCD管理全てを備えた、現場特化型兼クラウド型の今世紀最高の受発注管理システムとなります。
ユーザー登録
受発注業務の効率化だけでなく、システムを導入することで、コスト削減や製品・資材のステータス可視化のほか、属人化していた受発注情報の共有化による内部不正防止や統制にも役立ちます。
NEWJI DX
製造業に特化したデジタルトランスフォーメーション(DX)の実現を目指す請負開発型のコンサルティングサービスです。AI、iPaaS、および先端の技術を駆使して、製造プロセスの効率化、業務効率化、チームワーク強化、コスト削減、品質向上を実現します。このサービスは、製造業の課題を深く理解し、それに対する最適なデジタルソリューションを提供することで、企業が持続的な成長とイノベーションを達成できるようサポートします。
製造業ニュース解説
製造業、主に購買・調達部門にお勤めの方々に向けた情報を配信しております。
新任の方やベテランの方、管理職を対象とした幅広いコンテンツをご用意しております。
お問い合わせ
コストダウンが利益に直結する術だと理解していても、なかなか前に進めることができない状況。そんな時は、newjiのコストダウン自動化機能で大きく利益貢献しよう!
(β版非公開)