- お役立ち記事
- Basics of DRBFM, problem prevention and practical points
月間77,185名の
製造業ご担当者様が閲覧しています*
*2025年2月28日現在のGoogle Analyticsのデータより
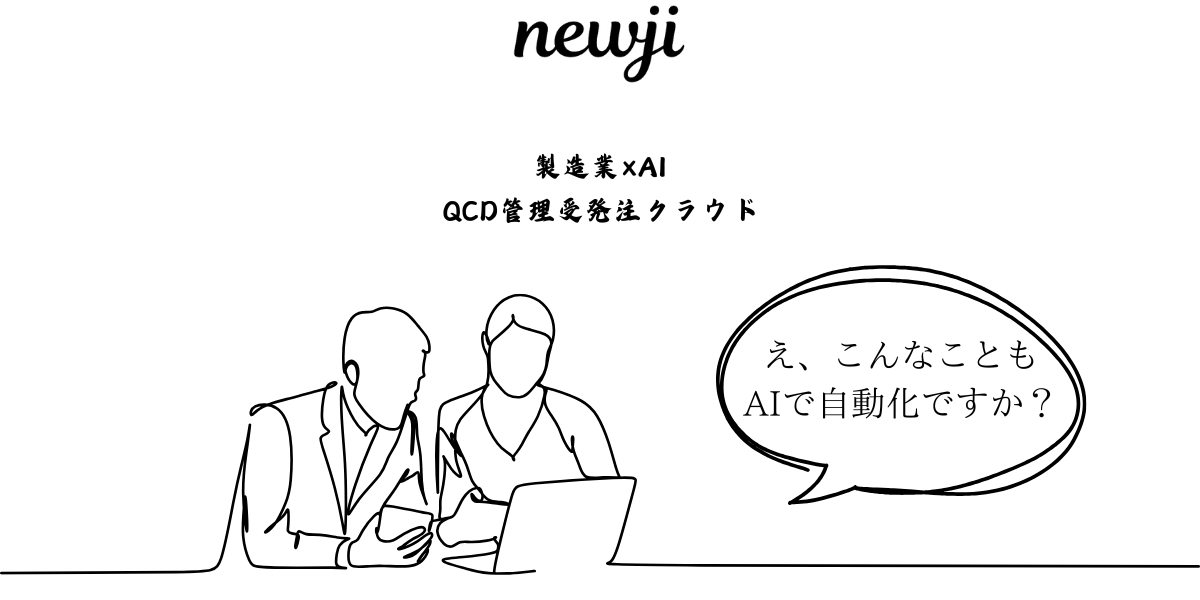
Basics of DRBFM, problem prevention and practical points
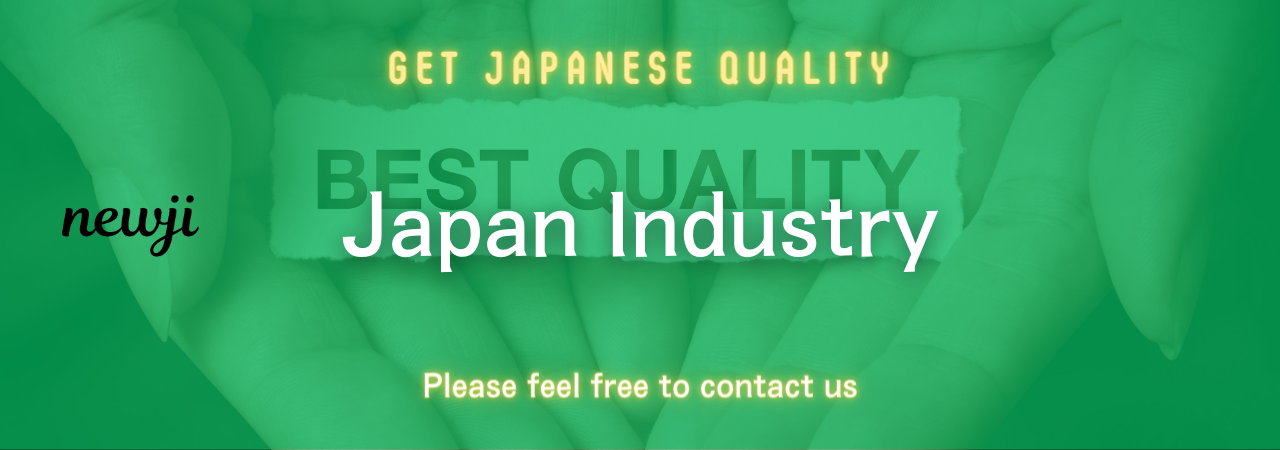
目次
What is DRBFM?
Design Review Based on Failure Mode (DRBFM) is a method used by engineers and designers to identify, analyze, and prevent potential problems in a product or process.
It emphasizes foreseeing potential failures and addressing them before they occur.
This approach is highly proactive, ensuring that the end product is of high quality and reliable.
The primary focus of DRBFM is to look at the changes in the design and examine them critically to predict any potential failures.
By doing so, it ensures that any change made does not introduce unforeseen problems that could impact the product’s performance or safety.
The Importance of DRBFM in Problem Prevention
One of the main reasons DRBFM is crucial is its ability to identify possible failure modes early in the design process.
By analyzing these potential issues, stakeholders can address them before they manifest in the final product.
This proactive approach not only prevents costly recalls and repairs but also enhances the overall reliability and durability of the product.
Another significant advantage of DRBFM is that it fosters collaboration among various departments.
By engaging multiple teams in this review process, different perspectives come into play, providing a comprehensive analysis of the design.
This collective effort contributes to a more robust and well-thought-out final product.
Step-by-Step Process of DRBFM
Though DRBFM can vary depending on the industry or specific application, its fundamental process usually involves several steps.
1. Identify Changes
The first step in DRBFM is to identify any changes made to the design.
These changes could range from minor tweaks to significant modifications.
Understanding these changes is crucial, as they might introduce potential failure modes that need to be addressed.
2. Conduct a Function Analysis
Once changes have been identified, the next step is to analyze their impact on the product’s functions.
This involves understanding how each change affects the design and functionality of the product.
The goal is to ensure that the change does not impair any critical function or introduce any new issues.
3. Identify Potential Failure Modes
During this phase, potential failure modes resulting from the changes are identified.
It is crucial to analyze these failure modes to understand their impact on the overall product.
Identifying these issues early can prevent them from affecting the final design.
4. Analyze the Effects of Each Failure Mode
After identifying potential failure modes, the next step is to analyze their effects.
This involves understanding the severity, occurrence, and detection of each failure mode.
By assessing these factors, designers can prioritize which potential issues need immediate attention.
5. Develop Action Plans
Once potential failure modes have been evaluated, action plans are developed to address them.
These plans typically involve changes to the design, operational processes, or manufacturing techniques.
The goal is to mitigate or eliminate the risks associated with each identified failure mode.
6. Implement Solutions
The final step involves implementing the solutions outlined in the action plans.
This might require cross-departmental collaboration to ensure that these solutions are integrated effectively into the design and manufacturing processes.
Practical Points to Consider in DRBFM
For DRBFM to be effective, several practical points must be taken into account.
Collaborative Effort
DRBFM is most successful when different teams come together to share their insights and perspectives.
By involving various departments such as design, manufacturing, and quality assurance, a more comprehensive review can be conducted, leading to a better assessment of potential failure modes.
Clear Documentation
Clear and detailed documentation is vital in DRBFM.
Every step, from identifying potential failure modes to developing action plans, should be meticulously documented.
This ensures transparency and provides a reference that teams can return to if issues arise in the future.
Continuous Improvement
DRBFM is not a one-time process but rather an ongoing effort.
As new changes are introduced to the design, the process should be revisited to ensure that these changes do not introduce new potential failure modes.
Continuous improvement helps keep the product reliable and up to date with the latest requirements.
Use of Tools
Employing specialized tools can be beneficial in the DRBFM process.
Software tools designed for failure mode analysis can help streamline the process and provide more precise results.
By leveraging technology, teams can conduct more thorough analyses and generate better insights.
Conclusion
DRBFM is an essential methodology in design and engineering for preventing problems before they occur.
Its proactive approach ensures that potential failure modes are identified and addressed early in the design process, leading to more reliable and high-quality products.
By fostering collaboration, maintaining clear documentation, and emphasizing continuous improvement, DRBFM can be a powerful tool for any organization looking to improve its design process and product reliability.
Whether you’re working on small-scale projects or large industrial designs, integrating these practices into your workflow can yield significant benefits in the long run.
資料ダウンロード
QCD管理受発注クラウド「newji」は、受発注部門で必要なQCD管理全てを備えた、現場特化型兼クラウド型の今世紀最高の受発注管理システムとなります。
ユーザー登録
受発注業務の効率化だけでなく、システムを導入することで、コスト削減や製品・資材のステータス可視化のほか、属人化していた受発注情報の共有化による内部不正防止や統制にも役立ちます。
NEWJI DX
製造業に特化したデジタルトランスフォーメーション(DX)の実現を目指す請負開発型のコンサルティングサービスです。AI、iPaaS、および先端の技術を駆使して、製造プロセスの効率化、業務効率化、チームワーク強化、コスト削減、品質向上を実現します。このサービスは、製造業の課題を深く理解し、それに対する最適なデジタルソリューションを提供することで、企業が持続的な成長とイノベーションを達成できるようサポートします。
製造業ニュース解説
製造業、主に購買・調達部門にお勤めの方々に向けた情報を配信しております。
新任の方やベテランの方、管理職を対象とした幅広いコンテンツをご用意しております。
お問い合わせ
コストダウンが利益に直結する術だと理解していても、なかなか前に進めることができない状況。そんな時は、newjiのコストダウン自動化機能で大きく利益貢献しよう!
(β版非公開)