- お役立ち記事
- Basics of FMEA and DRBFM, how to proceed, and how to utilize them to prevent problems from occurring
Basics of FMEA and DRBFM, how to proceed, and how to utilize them to prevent problems from occurring
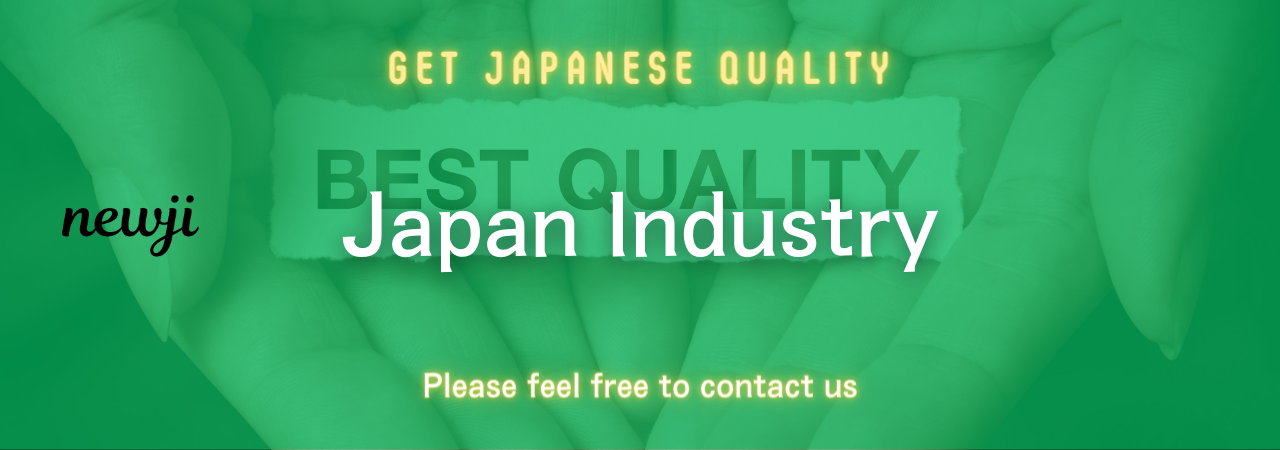
Failure Modes and Effects Analysis (FMEA) and Design Review Based on Failure Mode (DRBFM) are methodologies helping organizations prevent problems in products and processes before they occur.
Rooted in risk management, these techniques have become crucial in various industries for enhancing reliability, safety, and quality.
Understanding how to implement and utilize FMEA and DRBFM can make significant differences in product development and operational efficacy.
目次
What is FMEA?
Failure Modes and Effects Analysis, or FMEA, is a structured approach used to identify potential failure modes within a system, product, or process and analyze their causes and effects.
The primary objective of FMEA is to anticipate potential problems, assess their severity, and prioritize actions to mitigate or eliminate risks.
By systematically reviewing components, assemblies, and subsystems, organizations can proactively address areas of concern before they can lead to costly failures.
There are two main types of FMEA: Design FMEA (DFMEA) and Process FMEA (PFMEA).
DFMEA focuses on potential failures related to product design, whereas PFMEA examines failures that might occur in the manufacturing or production process.
Steps in Conducting an FMEA
1. **Identify the Scope**: Clearly define the system, subsystem, or process in focus.
2. **Assemble a Cross-disciplinary Team**: Engage team members with relevant expertise and experience.
3. **List Potential Failure Modes**: Determine how each component could potentially fail.
4. **Evaluate Effects of Failures**: Analyze what impact each failure mode could have on the system or end user.
5. **Determine Potential Causes**: Identify reasons why these failures could occur.
6. **Assess the Current Controls**: Review existing methods or controls that remove or mitigate the risk of failure.
7. **Calculate Risk Priority**: Use Risk Priority Numbers (RPNs), derived from the severity, occurrence, and detection ratings, to prioritize failure modes.
8. **Suggest and Implement Actions**: Develop strategies to address high-risk areas and implement them accordingly.
What is DRBFM?
Design Review Based on Failure Mode, or DRBFM, is a methodology that focuses on detailed reviews of areas where changes have been made in a design.
Developed by Toyota, this approach emphasizes the importance of questioning design changes thoroughly to avoid introducing new failure modes.
Unlike traditional design reviews, which might only evaluate a new design as a whole, DRBFM involves diving deep into specific modifications.
Key Principles of DRBFM
1. **Think Before Changes**: Always question the ‘why’ behind each change, identifying potential issues that the modifications might present.
2. **Own the Change**: The team involved in making the modifications should be responsible for addressing and solving any issues that arise.
3. **Deep Dive Discussions**: Encourage open dialogues and debates about what could go wrong with the change, exploring every potential failure mode.
4. **Formalize the Review Process**: Record and document every discussion, failure mode, and potential resolution plan for accountability.
Steps in Conducting DRBFM
1. **Preparation**: Establish the scope and purpose of the DRBFM, including a list of changes.
2. **Review the Design Changes**: Examine the design alternations closely and determine why they were made.
3. **Identify Potential Failure Modes**: Analyze what could go wrong with each of these changes and how these failures might impact the larger system.
4. **Facilitate Team Discussions**: Engage the team in discussions, encouraging diverse perspectives on potential failures.
5. **Evaluate and Document Findings**: Document all insights, potential risks, and mitigating actions.
6. **Implement Risk Mitigation Strategies**: Deploy strategies to address identified risks and track their effectiveness.
Utilizing FMEA and DRBFM to Prevent Problems
Both FMEA and DRBFM serve as proactive tools for organizational improvement, guiding teams to preemptively address potential issues.
While FMEA offers a broad view across systems and processes, DRBFM focuses on specific changes within a product design.
Integrating Both Approaches
1. **Holistic Overview and Specific Focus**: Use FMEA to gain an overall risk assessment of your system and DRBFM to hone in on specific changes that could introduce risks.
2. **Collaboration Across Disciplines**: Engage teams from different departments to bring together a wide range of expertise, experiences, and viewpoints, thereby enhancing understanding and problem-solving capabilities.
3. **Continuous Improvement and Feedback**: Implement regular reviews and updates to both FMEAs and DRBFMs to reflect changes in design and processes.
4. **Data-Driven Decision Making**: Rely on past data and predictive analyses to inform the updates to your risk management strategies.
Benefits of Implementing FMEA and DRBFM
By investing the time and resources into FMEA and DRBFM, organizations benefit from improved quality assurance and higher reliability of products and processes.
Predicting and mitigating risks beforehand reduces the likelihood of costly recalls and customer dissatisfaction, saving time and resources in the long run.
Both approaches help create a culture of proactive problem-solving and continuous improvement, fostering a commitment to achieving excellence in design and operations.
In today’s competitive marketplace, the strategic application of FMEA and DRBFM remains essential for organizations determined to maintain operational excellence and product integrity.
資料ダウンロード
QCD調達購買管理クラウド「newji」は、調達購買部門で必要なQCD管理全てを備えた、現場特化型兼クラウド型の今世紀最高の購買管理システムとなります。
ユーザー登録
調達購買業務の効率化だけでなく、システムを導入することで、コスト削減や製品・資材のステータス可視化のほか、属人化していた購買情報の共有化による内部不正防止や統制にも役立ちます。
NEWJI DX
製造業に特化したデジタルトランスフォーメーション(DX)の実現を目指す請負開発型のコンサルティングサービスです。AI、iPaaS、および先端の技術を駆使して、製造プロセスの効率化、業務効率化、チームワーク強化、コスト削減、品質向上を実現します。このサービスは、製造業の課題を深く理解し、それに対する最適なデジタルソリューションを提供することで、企業が持続的な成長とイノベーションを達成できるようサポートします。
オンライン講座
製造業、主に購買・調達部門にお勤めの方々に向けた情報を配信しております。
新任の方やベテランの方、管理職を対象とした幅広いコンテンツをご用意しております。
お問い合わせ
コストダウンが利益に直結する術だと理解していても、なかなか前に進めることができない状況。そんな時は、newjiのコストダウン自動化機能で大きく利益貢献しよう!
(Β版非公開)