- お役立ち記事
- Basics of FMEA/DRBFM and efficient and effective interviews How to use FMEA and its key points
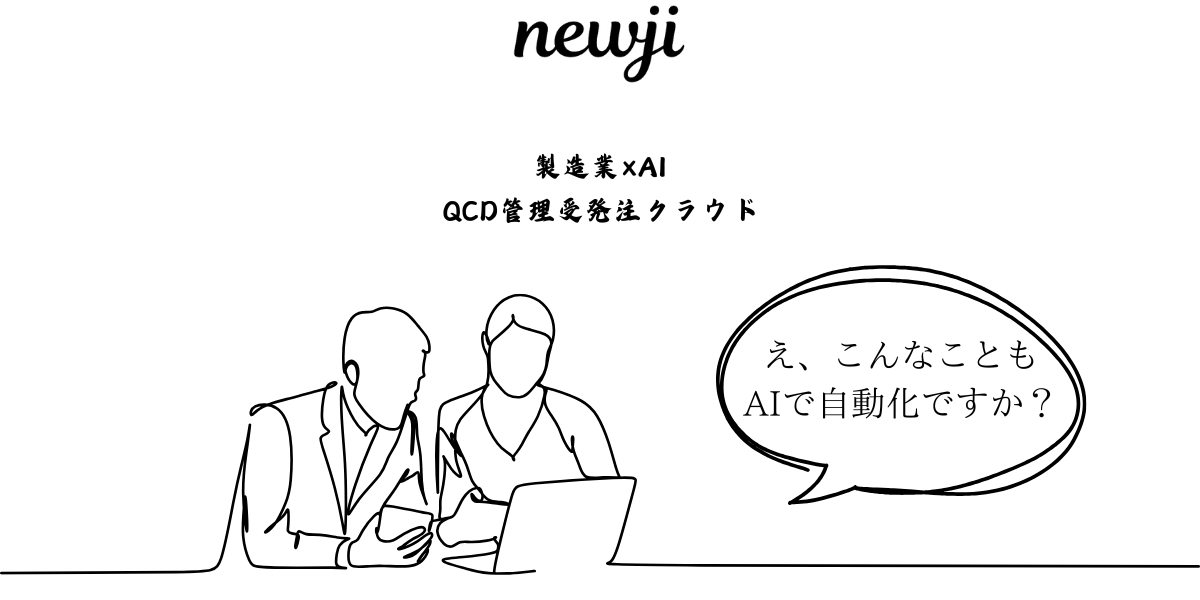
Basics of FMEA/DRBFM and efficient and effective interviews How to use FMEA and its key points
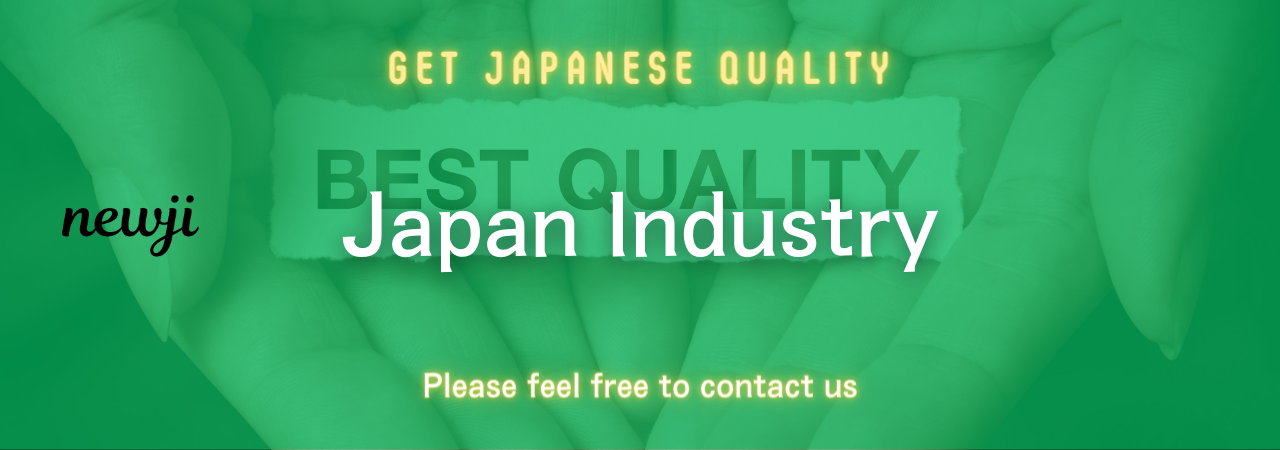
目次
Understanding FMEA: The Basics
FMEA, or Failure Modes and Effects Analysis, is a systematic approach used in various industries to identify potential failure points in a product or process.
It helps to evaluate the risks associated with these failures and prioritize them for corrective action.
Originally developed for the aerospace industry, FMEA has now become a cornerstone method in manufacturing, automotive sectors, healthcare, and more.
To effectively apply FMEA, teams typically start by creating a detailed flow diagram of the process or product in question.
This includes listing all the components or steps involved.
Each component is then analyzed to identify possible failure modes, which are the ways in which something might go wrong.
The Goals of FMEA
The primary objective of FMEA is to improve products and processes by anticipating potential failures before they occur.
This proactive approach helps to minimize risk, reduce costs associated with product recalls or defects, and ensure customer satisfaction.
By systematically identifying potential problems, teams can implement corrective actions to mitigate these risks effectively.
Another goal of FMEA is to facilitate continuous improvement.
As teams conduct FMEA on their processes regularly, they develop a deeper understanding of their systems, which aids in long-term optimization and innovation.
Getting Started with FMEA
Implementing FMEA requires assembling a cross-functional team with expertise in the areas under review.
These teams often consist of engineers, quality assurance experts, manufacturing specialists, and other relevant personnel.
The FMEA process can be broken down into several key steps:
1. **Define the Scope**: Determine the boundaries of the analysis, such as specific components, systems, or processes that require evaluation.
2. **Identify Potential Failure Modes**: For each component or step in the process, brainstorm potential ways it might fail.
3. **Determine the Effects of Failure**: Assess the impact that each failure mode could have on the overall system or process.
4. **Assess the Severity, Occurrence, and Detection**: Using a scoring system, evaluate the severity of the failure mode’s effects, the likelihood of its occurrence, and the probability of detecting the failure before it causes harm.
5. **Prioritize Failure Modes**: Calculate a Risk Priority Number (RPN) for each failure mode by multiplying the severity, occurrence, and detection scores.
Focus corrective actions on failure modes with the highest RPN.
6. **Implement Corrective Actions**: Develop and execute plans to address high-priority failure modes.
7. **Review and Update**: Continuously monitor and update the FMEA as changes are made to the process or new information becomes available.
Effective Use of DRBFM
DRBFM, or Design Review Based on Failure Mode, is an offshoot of FMEA that focuses specifically on design changes.
Created by Toyota, DRBFM encourages thorough discussion and consideration of potential failure points introduced by these changes.
Whereas FMEA is often broad, examining entire processes or products, DRBFM centers on what, when, and how a design will change.
DRBFM Process Steps
1. **Plan**: The DRBFM process starts by outlining the scope and purpose of the design change.
This phase involves gathering all relevant data and defining design parameters.
2. **Think and Discuss**: Teams come together to discuss the potential impact of proposed changes.
Every change is examined through the lens of potential failure modes.
3. **Analyze**: Identify the failure modes associated with the design change, much like in FMEA.
Focus on how the changes affect existing systems and processes.
4. **Evaluate and Document**: Document the analysis and outcomes, emphasizing potential risks and failure modes.
This documentation helps create a clear plan for moving forward.
5. **Make Decisions and Implement Changes**: Based on the DRBFM analysis, decide on the best course of action and implement necessary changes.
6. **Review**: After implementation, review the effectiveness of the change to ensure no new failure modes have been introduced.
Conducting Interviews for FMEA and DRBFM
Interviews play a crucial role in gathering the necessary information for FMEA and DRBFM analyses.
Talking to people with hands-on experience offers insights that might not be apparent in data alone.
Preparation for Interviews
Before conducting interviews, prepare structured questions that cover the scope of the analysis.
Understand the roles of the interviewees and tailor questions that tap into their expertise.
Questions should be open-ended to encourage detailed responses.
Key Points for Effective Interviews
1. **Listen Actively**: Pay attention to what the interviewees are saying and probe deeper with follow-up questions as needed.
This helps in uncovering vital information that may not be obvious initially.
2. **Encourage Openness**: Create an environment where participants feel comfortable sharing their insights, concerns, and suggestions openly.
3. **Capture the Details**: Document all relevant points discussed during the interview.
The data collected will be integral to conducting thorough FMEA and DRBFM.
4. **Seek Clarification**: If any points are unclear, ask for examples or elaboration to ensure full understanding.
5. **Summarize and Confirm**: At the end of the interview, summarize the key points and confirm them with the interviewee to ensure accurate information has been captured.
Conclusion
FMEA and DRBFM are powerful tools for risk management and quality assurance.
They help organizations anticipate potential problems and make informed decisions to improve product and process reliability.
By following systematic steps and leveraging detailed interviews, teams can effectively prioritize and address potential failures.
As industries continue to evolve, the importance of these methodologies remains steadfast, making them essential components of any robust quality management system.
資料ダウンロード
QCD調達購買管理クラウド「newji」は、調達購買部門で必要なQCD管理全てを備えた、現場特化型兼クラウド型の今世紀最高の購買管理システムとなります。
ユーザー登録
調達購買業務の効率化だけでなく、システムを導入することで、コスト削減や製品・資材のステータス可視化のほか、属人化していた購買情報の共有化による内部不正防止や統制にも役立ちます。
NEWJI DX
製造業に特化したデジタルトランスフォーメーション(DX)の実現を目指す請負開発型のコンサルティングサービスです。AI、iPaaS、および先端の技術を駆使して、製造プロセスの効率化、業務効率化、チームワーク強化、コスト削減、品質向上を実現します。このサービスは、製造業の課題を深く理解し、それに対する最適なデジタルソリューションを提供することで、企業が持続的な成長とイノベーションを達成できるようサポートします。
オンライン講座
製造業、主に購買・調達部門にお勤めの方々に向けた情報を配信しております。
新任の方やベテランの方、管理職を対象とした幅広いコンテンツをご用意しております。
お問い合わせ
コストダウンが利益に直結する術だと理解していても、なかなか前に進めることができない状況。そんな時は、newjiのコストダウン自動化機能で大きく利益貢献しよう!
(Β版非公開)