- お役立ち記事
- Basics of fractography/damage analysis and how to utilize them to prevent damage accidents.
Basics of fractography/damage analysis and how to utilize them to prevent damage accidents.
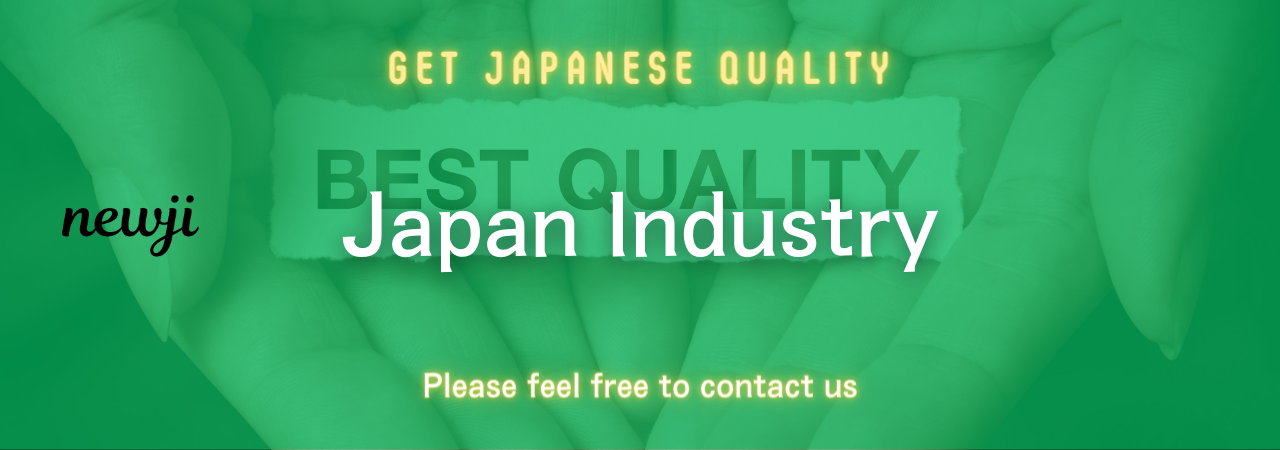
目次
Understanding Fractography and Its Importance
Fractography is the study of fracture surfaces of materials and components with the goal of understanding the causes of failure.
This scientific analysis plays a crucial role in determining the reasons for material failure and preventing future accidents.
Experts in fractography employ various techniques and equipment to examine fracture patterns and surfaces.
Their findings can then be used to improve material design, manufacturing processes, and maintenance protocols.
One of the primary reasons for conducting a fractographic analysis is to identify the failure mode.
Understanding whether a fracture was due to fatigue, overload, corrosion, or another factor is essential for developing solutions that enhance safety and reliability.
Fracture Mechanics: The Core Principle Behind Fractography
Fracture mechanics is a field that focuses on the behavior of cracked materials.
It is essential for understanding how and why materials break or fail.
This branch of engineering helps in assessing the conditions under which a material with an existing crack will fail.
Incorporating fracture mechanics principles into fractography allows for a more comprehensive analysis of fracture surfaces.
By examining the details of how cracks initiate and propagate, experts can pinpoint critical insights into the material’s behavior right before the failure.
This analysis can reveal whether the failure was due to inherent material properties, external loads, or environmental factors.
Fatigue Failure
One of the common failure modes studied in fractography is fatigue failure.
Fatigue failure occurs when a material is subjected to repeated or fluctuating loads over time, causing the formation and propagation of cracks.
This type of failure is often not apparent until the material ultimately breaks, making it challenging to detect early.
Indicators of fatigue failure on a fracture surface include beach marks or striations, which are repetitive patterns showing the progress of fatigue crack growth.
By identifying these patterns, engineers can trace the history of the loading conditions and develop measures to prevent similar failures in the future.
Corrosion-Induced Fracture
Another significant aspect of fractography is the analysis of corrosion-induced fractures.
Corrosion can severely weaken materials, leading to unforeseen breaks.
Different forms of corrosion, such as pitting or stress-corrosion cracking, can result in distinct fracture surfaces.
Through fractography, the presence of corrosion products, as well as the type and extent of corrosion damage, can provide essential clues about the cause of failure.
By identifying corrosion patterns on a fracture surface, strategies can be put in place to enhance material selection, coating systems, or environmental protection measures to prevent future corrosion-related failures.
Techniques and Tools in Fractography
Various tools and techniques are employed in fractography to inspect and analyze fracture surfaces.
These methods vary in complexity and magnification, with each offering unique insights into the fracture mechanics.
Optical Microscopy
Optical microscopy is a fundamental technique in fractography.
It provides an initial examination of the fracture surface at lower magnifications.
This technique aids in identifying general features like crack initiation points, direction of fracture propagation, and macroscopic fracture characteristics.
It is often the first step in a more detailed fractographic analysis.
Scanning Electron Microscopy (SEM)
For a more detailed examination, especially of microstructural features, scanning electron microscopy (SEM) is used.
SEM provides high-resolution, three-dimensional images of the fracture surface.
This technique is critical in identifying microscopic features such as dimples, striations, or intergranular fracture patterns.
These microscopic details can reveal much about the failure process, including whether the material experienced ductile or brittle fracture.
Energy Dispersive Spectroscopy (EDS)
Energy dispersive spectroscopy (EDS) is often attached to an SEM for elemental analysis of the fracture surface.
EDS helps identify any foreign materials or elemental compositions that might have contributed to the failure.
This information is vital for understanding if contamination or improper material use played a role in the fracture.
X-Ray Diffraction (XRD)
X-ray diffraction (XRD) is another powerful technique used to identify phases and determine residual stresses in the fracture surface.
In cases where materials have experienced phase changes due to high temperatures or other environmental factors, XRD can reveal these transformations and their impact on the fracture process.
Preventing Damage Accidents Through Fractography
The ultimate goal of fractography is not just to understand past failures but to prevent future ones.
By analyzing fracture surfaces and understanding the causes of failures, organizations can implement strategies that significantly reduce the risk of accidents.
One way fractography helps in accident prevention is through the improvement of design and material selection.
Design flaws often lead to stress concentrations, which can be identified and rectified to enhance the load-bearing capacity of materials.
Similarly, selecting materials that are less prone to fatigue, corrosion, or other failure modes based on fractographic insights ensures greater safety.
Moreover, fractography informs better maintenance practices and service life predictions.
Understanding the conditions that lead to failure allows for more accurate assessments of when components should be replaced or serviced.
Finally, the insights gained from fractographic studies can guide the development of new materials and technologies that inherently resist failure, improving the overall safety and reliability of systems and structures.
In conclusion, the field of fractography plays a crucial role in both understanding and preventing material failures.
Through a detailed analysis of fracture surfaces, engineers and scientists can uncover the underlying causes of accidents, leading to better design, material selection, and maintenance practices.
Utilizing these insights, industry professionals can significantly enhance safety, reduce costs associated with downtime and repairs, and boost the overall lifespan of components and systems.
資料ダウンロード
QCD調達購買管理クラウド「newji」は、調達購買部門で必要なQCD管理全てを備えた、現場特化型兼クラウド型の今世紀最高の購買管理システムとなります。
ユーザー登録
調達購買業務の効率化だけでなく、システムを導入することで、コスト削減や製品・資材のステータス可視化のほか、属人化していた購買情報の共有化による内部不正防止や統制にも役立ちます。
NEWJI DX
製造業に特化したデジタルトランスフォーメーション(DX)の実現を目指す請負開発型のコンサルティングサービスです。AI、iPaaS、および先端の技術を駆使して、製造プロセスの効率化、業務効率化、チームワーク強化、コスト削減、品質向上を実現します。このサービスは、製造業の課題を深く理解し、それに対する最適なデジタルソリューションを提供することで、企業が持続的な成長とイノベーションを達成できるようサポートします。
オンライン講座
製造業、主に購買・調達部門にお勤めの方々に向けた情報を配信しております。
新任の方やベテランの方、管理職を対象とした幅広いコンテンツをご用意しております。
お問い合わせ
コストダウンが利益に直結する術だと理解していても、なかなか前に進めることができない状況。そんな時は、newjiのコストダウン自動化機能で大きく利益貢献しよう!
(Β版非公開)