- お役立ち記事
- Basics of fracture surface observation of metal materials and fracture surface numerical analysis method for estimating the cause of damage
月間76,176名の
製造業ご担当者様が閲覧しています*
*2025年3月31日現在のGoogle Analyticsのデータより
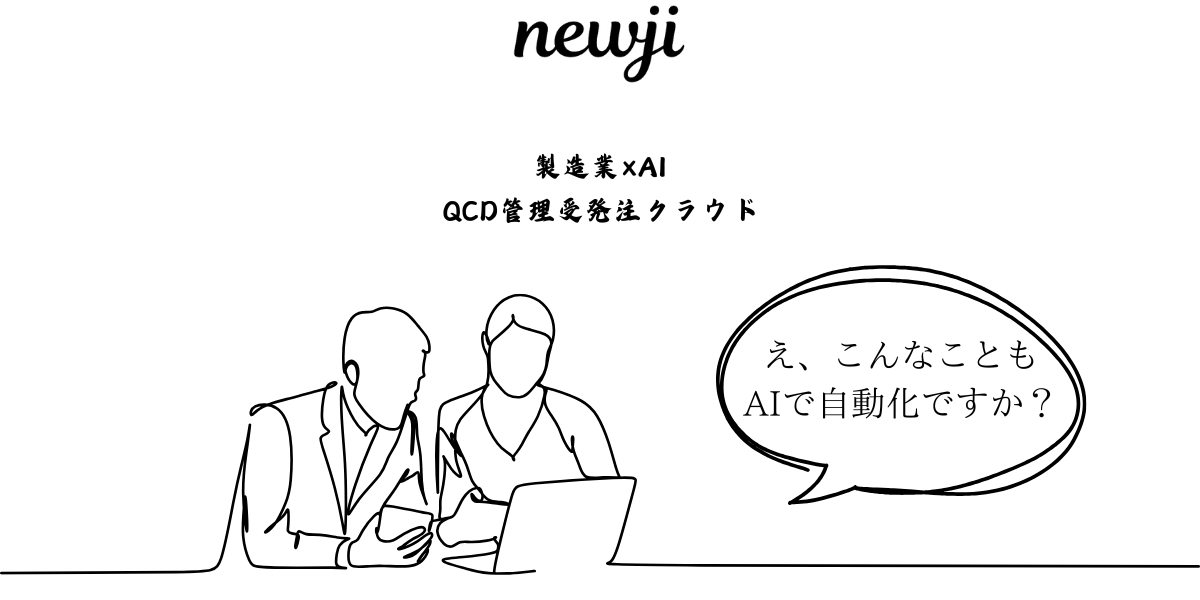
Basics of fracture surface observation of metal materials and fracture surface numerical analysis method for estimating the cause of damage
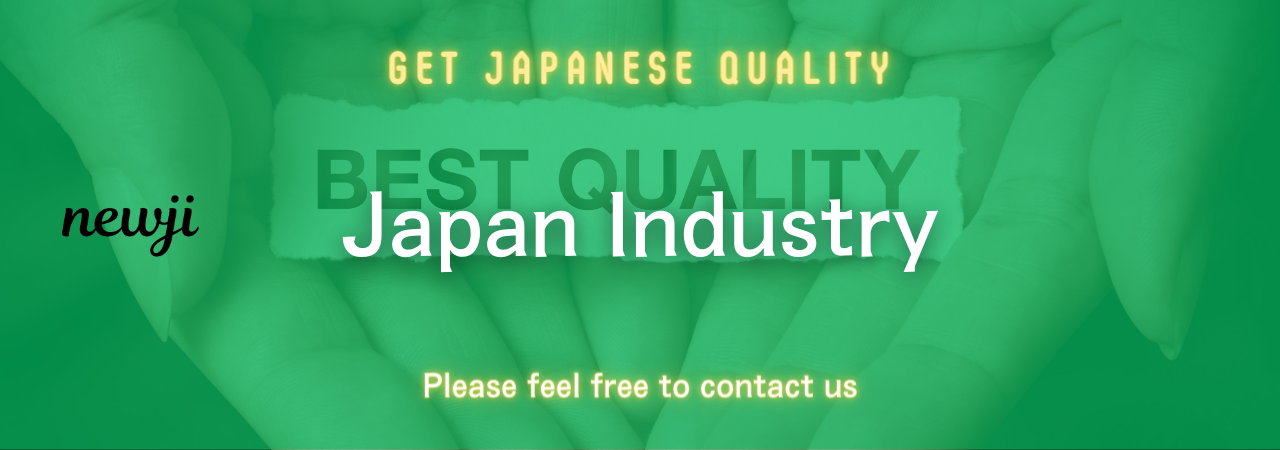
目次
Understanding Fracture Surface Observation
Fracture surface observation is a critical technique used to examine the causes and progression of damage in metal materials.
It involves studying the broken surface of a metal to deduce how and why the material failed.
By observing the fracture surface, scientists and engineers can gather crucial information about the type of fracture and the conditions that led to the failure.
Types of Fractures
The fracture surfaces of metals typically fall into two broad categories: brittle and ductile fractures.
Brittle Fractures: These occur without significant plastic deformation and often happen suddenly.
Brittle fractures are characterized by their shiny, crystalline appearance, often with little warning before failure.
Examples of materials prone to brittle fractures include cast iron or high-strength steels at low temperatures.
Ductile Fractures: Unlike brittle fractures, ductile fractures involve a significant amount of plastic deformation before the final rupture.
This type of fracture is identified by a dull and fibrous appearance, usually showing signs that the material stretched or necked down at the point of fracture.
Observation Techniques
To effectively observe and analyze fracture surfaces, several techniques are employed:
Visual Inspection: A straightforward and initial step, visual inspection under good lighting conditions often provides valuable information.
Aspects like the shape, color, and texture of the fracture surface can hint at how the fracture occurred.
Photographic Documentation: High-resolution images are invaluable for documenting features observed on the fracture surface.
Photographs taken at various angles can capture the details necessary for later analysis.
Microscopy: When more detail is needed, light microscopy or electron microscopy is used to observe tiny features that are not visible to the naked eye.
Scanning Electron Microscopy (SEM) allows for a highly magnified view of the fracture surface, revealing otherwise invisible elements like fracture patterns and micro-cracks.
Numerical Analysis for Estimating Damage Causes
Beyond direct observation techniques, numerical analysis is a powerful tool for estimating the cause of damage.
This method uses data and mathematical models to simulate the conditions and forces leading to material failure.
Finite Element Analysis (FEA)
Finite Element Analysis is a computational method used extensively in engineering.
FEA models a part or assembly as a system of discrete elements to study how they react to stresses and strains.
In the context of fracture analysis, FEA helps predict how cracks initiate and propagate through the material.
Engineers can input various material properties and environmental conditions into the model, allowing simulations to replicate real-world scenarios.
By adjusting variables and comparing the simulated fracture surfaces to those observed, the underlying causes of damage can be hypothesized.
Fracture Mechanics
Fracture mechanics is a field of study focusing on the behavior of cracks in materials.
It combines principles of mechanical engineering and materials science to understand and predict failure.
The study involves parameters such as stress intensity factors, energy release rates, and crack propagation paths.
Through numerical methods, fracture mechanics can estimate the critical load under which a material will fail, providing insights into preventative measures.
Data Analysis and Machine Learning
With advancements in technology, data analysis, and machine learning play increasingly vital roles in fracture surface analysis.
Machine learning algorithms can process large datasets of fracture surface images, identifying patterns and correlations that might be overlooked through manual inspection.
These technologies can help predict the failure events by recognizing specific features or conditions recorded in previous failures.
As more data becomes available, machine learning models become more precise, offering more reliable predictions.
Why is Fracture Surface Observation Important?
Understanding the fracture behavior of metal materials is crucial for various industries, including aerospace, automotive, construction, and beyond.
Every failure carries the potential for costly damage, loss of life, or catastrophic events, making thorough analyses imperative.
Preventative Measures
Through fracture surface observation and numerical analysis, engineers can identify weaknesses in material design or application.
This insight guides changes in manufacturing processes, material selection, or structural design to prevent future failures.
Improving Safety
Safety is a primary concern in industries relying on metal structures.
By thoroughly understanding how metals fail, safer products and infrastructures can be developed, minimizing the risk to human life and property.
Cost Efficiency
Predicting possible points of failure allows for strategic maintenance and inspection schedules, reducing the chance of unexpected failures and associated costs.
Conclusion
Fracture surface observation and numerical analysis are indispensable tools for understanding and preventing material failure.
By combining observational expertise with cutting-edge technology, engineers can not only identify past problems but also anticipate and mitigate future risks.
Through these methods, industries ensure not just the longevity of materials, but also the safety and efficiency of their applications.
In continuing to develop these methods, the future promises even more reliability and understanding in the complex world of materials science.
資料ダウンロード
QCD管理受発注クラウド「newji」は、受発注部門で必要なQCD管理全てを備えた、現場特化型兼クラウド型の今世紀最高の受発注管理システムとなります。
ユーザー登録
受発注業務の効率化だけでなく、システムを導入することで、コスト削減や製品・資材のステータス可視化のほか、属人化していた受発注情報の共有化による内部不正防止や統制にも役立ちます。
NEWJI DX
製造業に特化したデジタルトランスフォーメーション(DX)の実現を目指す請負開発型のコンサルティングサービスです。AI、iPaaS、および先端の技術を駆使して、製造プロセスの効率化、業務効率化、チームワーク強化、コスト削減、品質向上を実現します。このサービスは、製造業の課題を深く理解し、それに対する最適なデジタルソリューションを提供することで、企業が持続的な成長とイノベーションを達成できるようサポートします。
製造業ニュース解説
製造業、主に購買・調達部門にお勤めの方々に向けた情報を配信しております。
新任の方やベテランの方、管理職を対象とした幅広いコンテンツをご用意しております。
お問い合わせ
コストダウンが利益に直結する術だと理解していても、なかなか前に進めることができない状況。そんな時は、newjiのコストダウン自動化機能で大きく利益貢献しよう!
(β版非公開)