- お役立ち記事
- Basics of fretting wear and fatigue/damage countermeasures for machinery and equipment
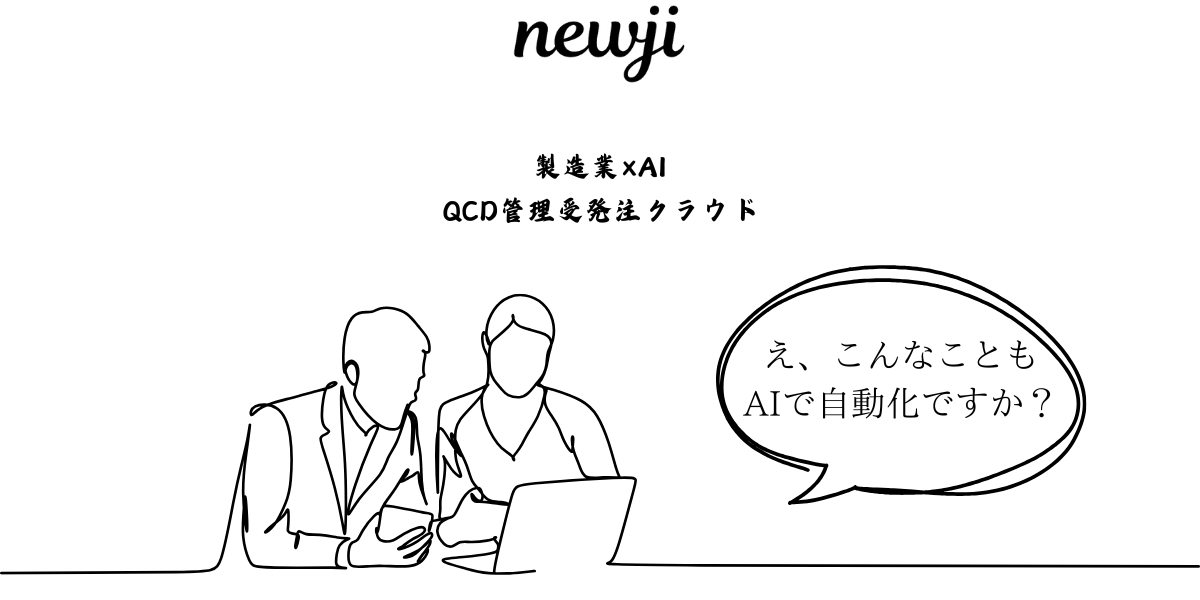
Basics of fretting wear and fatigue/damage countermeasures for machinery and equipment
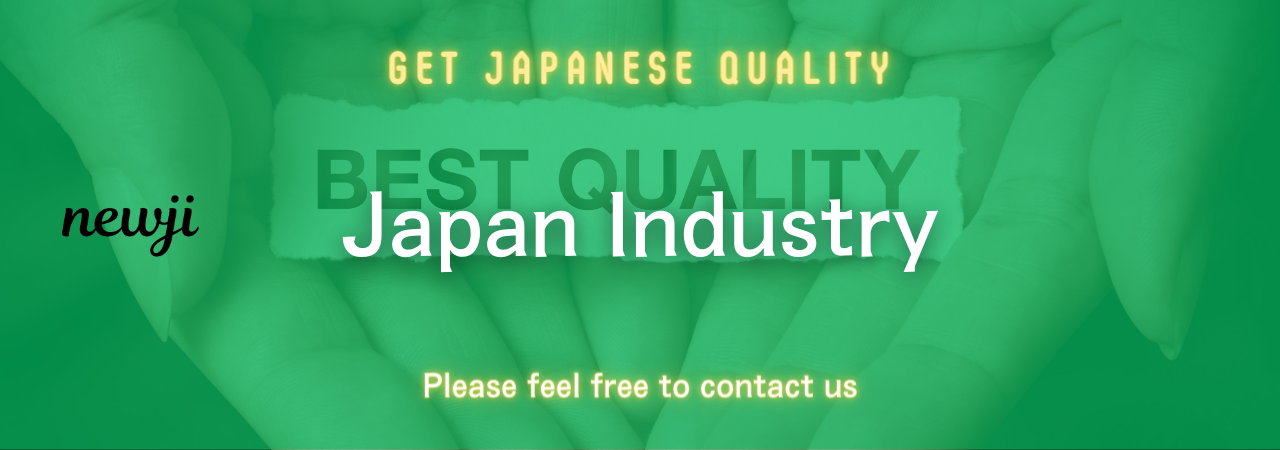
目次
Understanding Fretting Wear
Fretting wear is a phenomenon that occurs when two surfaces in contact experience small amplitude oscillatory movement.
This type of wear is common in many mechanical systems where parts are subjected to vibrations or repeated loading.
When components move against each other in a limited space, they can suffer from fretting wear, which can lead to significant damage over time.
Fretting wear is characterized by the formation of small debris particles that can further exacerbate the wear process.
This happens because microscopic asperities on the surface of materials interact during movement.
The repeated rubbing leads to local adhesion and then the small-scale removal of material, creating fine wear debris.
Common Areas Affected by Fretting Wear
Fretting wear can occur in various areas within machinery and equipment.
Some common examples include:
– **Bolted Joints**: Parts joined by bolts can experience micro-movements due to vibrations, resulting in fretting wear.
– **Bearings**: Although designed to reduce friction, the minute movements in bearings can still produce wear.
– **Splines and Shafts**: These parts often undergo rotational movements leading to surface degradation over time.
What is Fretting Fatigue?
Fretting fatigue is closely related to fretting wear but focuses on the weakening of the material that results in crack initiation.
While fretting wear leads to material removal on the surface, fretting fatigue can cause structural damage deep within components.
When the surface damage from fretting wear is extensive, cracks can form.
These cracks can propagate under cyclic loading conditions, eventually leading to mechanical failure.
This is particularly critical in components subject to high stress and cyclic loading, such as aerospace or automotive parts.
Factors Contributing to Fretting Fatigue
Several variables can influence fretting fatigue:
– **Material Properties**: Hardness, toughness, and ductility of the material affect its susceptibility to fatigue.
– **Environment**: Humidity, temperature, and presence of corrosive elements can accelerate wear.
– **Load**: The magnitude and frequency of the load affect the wear and fatigue rate.
– **Surface Finish**: Smoother surfaces generally demonstrate better resistance to fretting.
Countermeasures for Fretting Wear and Fatigue
Reducing fretting wear and fatigue involves several strategies directed at minimizing surface movement and enhancing material properties.
Design Improvements
One effective way to combat fretting wear and fatigue is through design innovations:
– **Tight Fitting**: Ensuring components fit tightly can reduce micro-movements, thus limiting wear.
– **Use of Lubricants**: Proper lubrication can form a protective layer that reduces the friction between surfaces.
Material Selection
Choosing the right material can significantly enhance resistance to fretting wear:
– **Hardening Treatments**: Surface treatments like carburizing can increase hardness.
– **Coatings**: Applying protective coatings such as nickel or chromium can prevent surface degradation.
Environmental Control
Controlling the operational environment can mitigate wear and fatigue:
– **Humidity and Temperature Control**: This helps in reducing the acceleration of wear due to harsh environmental conditions.
– **Corrosion Prevention**: Using corrosion inhibitors delays material degradation.
Regular Maintenance and Monitoring
Regular inspections and maintenance play a critical role in managing fretting wear and fatigue:
– **Condition Monitoring**: Techniques like vibration analysis can detect early signs of wear.
– **Predictive Maintenance**: Scheduling maintenance based on the actual condition of machinery instead of time-based intervals.
Role of Technology in Countermeasures
Modern technology offers advanced tools for tackling fretting issues:
– **Advanced Materials**: Development of alloy materials specifically designed to withstand fretting environments.
– **Monitoring Systems**: AI and IoT-based systems that continuously monitor machinery conditions and predict wear development.
Conclusion
Fretting wear and fatigue pose significant challenges in mechanical systems, often leading to costly repairs and downtime.
Understanding their mechanisms and implementing effective countermeasures is crucial in extending equipment life and ensuring operational efficiency.
By improving design, selecting appropriate materials, and maintaining regular equipment checks, industries can often mitigate these issues successfully.
Ultimately, technological advancements continue to offer promising solutions for the ongoing battle against fretting wear and fatigue in machinery and equipment.
資料ダウンロード
QCD調達購買管理クラウド「newji」は、調達購買部門で必要なQCD管理全てを備えた、現場特化型兼クラウド型の今世紀最高の購買管理システムとなります。
ユーザー登録
調達購買業務の効率化だけでなく、システムを導入することで、コスト削減や製品・資材のステータス可視化のほか、属人化していた購買情報の共有化による内部不正防止や統制にも役立ちます。
NEWJI DX
製造業に特化したデジタルトランスフォーメーション(DX)の実現を目指す請負開発型のコンサルティングサービスです。AI、iPaaS、および先端の技術を駆使して、製造プロセスの効率化、業務効率化、チームワーク強化、コスト削減、品質向上を実現します。このサービスは、製造業の課題を深く理解し、それに対する最適なデジタルソリューションを提供することで、企業が持続的な成長とイノベーションを達成できるようサポートします。
オンライン講座
製造業、主に購買・調達部門にお勤めの方々に向けた情報を配信しております。
新任の方やベテランの方、管理職を対象とした幅広いコンテンツをご用意しております。
お問い合わせ
コストダウンが利益に直結する術だと理解していても、なかなか前に進めることができない状況。そんな時は、newjiのコストダウン自動化機能で大きく利益貢献しよう!
(Β版非公開)