- お役立ち記事
- Basics of FSW (Friction Stir Welding) and its application to joining dissimilar materials
月間77,185名の
製造業ご担当者様が閲覧しています*
*2025年2月28日現在のGoogle Analyticsのデータより
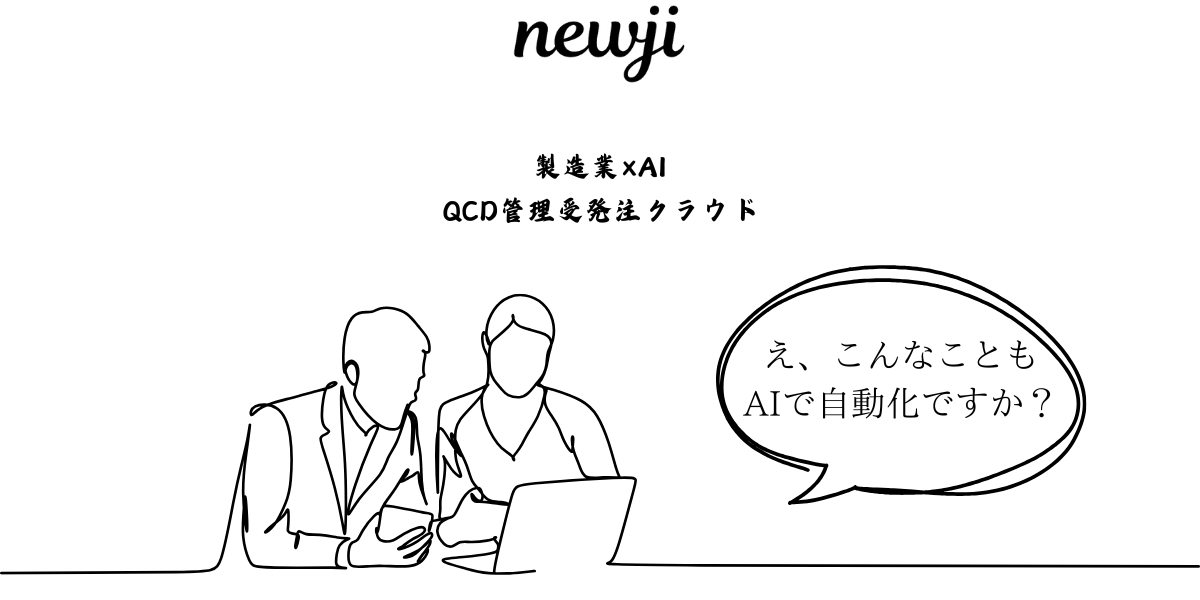
Basics of FSW (Friction Stir Welding) and its application to joining dissimilar materials
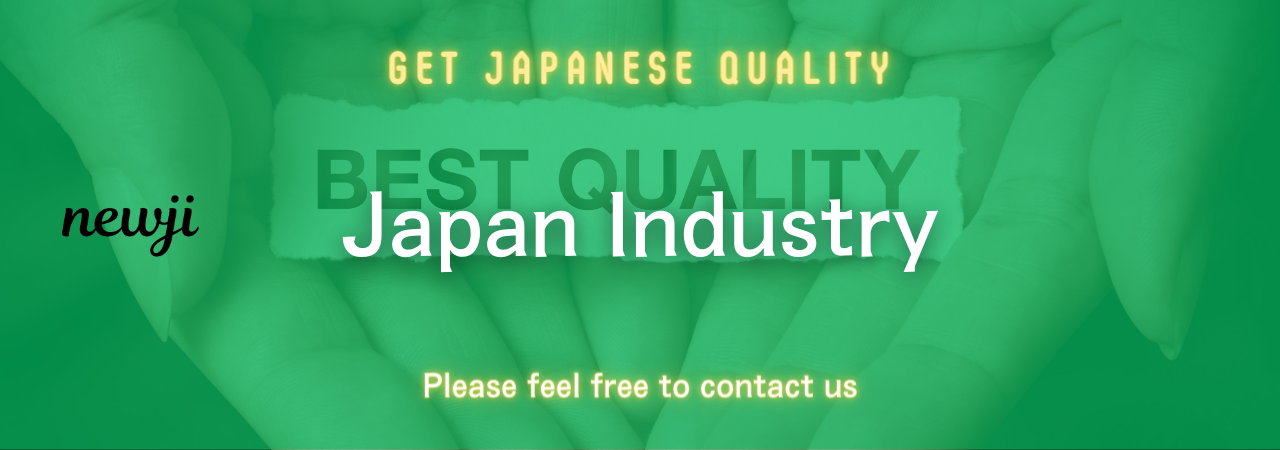
目次
Introduction to Friction Stir Welding
Friction Stir Welding (FSW) is a cutting-edge technology widely used in various industries for joining materials.
It was invented in 1991 at The Welding Institute (TWI) in the UK.
This solid-state joining process uses a non-consumable tool to join two facing workpieces.
The tool rotates and moves along the joint line, creating frictional heat which softens the material without melting it.
As a result, FSW provides a high-quality joint by mechanical mixing of the material around the tool pin.
This method is particularly valuable for applications where traditional welding techniques might struggle, such as joining dissimilar materials.
How Does Friction Stir Welding Work?
Friction Stir Welding involves a simple, yet highly effective process.
A specially designed cylindrical tool with a profiled pin rotates and slowly plunges into the joining area between two fixed components.
The rotation of the tool generates heat due to friction between the tool and the materials.
As the temperature rises, the materials become plasticized, though they do not reach the melting point.
The mechanical movement of the tool stirs the softened material around the pin, and as the tool advances, it leaves behind a solid-phase weld.
Once the tool passes, the materials cool down and merge to form a robust and seamless joint.
These features make FSW a superb method for products that need strong and consistent joints.
FSW Equipment and Tooling
The efficiency of FSW heavily depends on the appropriate equipment and tooling.
The FSW machine is typically a CNC machine with a strong framework to apply adequate downward force and maintain stability.
The tool design varies depending on the type of materials and the thickness being welded.
Key components of the FSW tool include:
– **Shoulder:** Provides the heat through friction.
– **Pin (or Probe):** Mixes the material and moves the plasticized region along.
The selection of the correct dimensions and materials for the tool is crucial for a successful weld.
Advantages of Friction Stir Welding
Friction Stir Welding offers numerous advantages over traditional welding methods:
– **No Melting:** Since materials don’t melt, issues like porosity or solidification cracks are minimized.
– **Environmental Benefits:** The process doesn’t require consumables such as electrodes or welding gases.
– **Superior Strength:** The joints are often stronger and more reliable compared to fusion welds.
– **Low Distortion:** Low heat input means less thermal distortion in the welded components.
Applications in Joining Dissimilar Materials
FSW is particularly advantageous for joining dissimilar materials, a common requirement in modern manufacturing industries.
These applications range from aerospace to automotive and shipbuilding industries.
Aerospace Industry
In the aerospace sector, FSW is favored for producing lightweight yet strong components.
It allows for the joining of aluminum to titanium or magnesium, leading to weight reduction and enhanced fuel efficiency.
Automotive Industry
FSW is widely used in the automotive industry to join different metals like aluminum and steel.
This approach helps manufacture lightweight bodies leading to better fuel economy and lower emissions.
Shipbuilding
For shipbuilding, FSW enables manufacturers to create hulls with sections of different materials, enhancing performance and reducing weight.
This application proves ideal for meeting stringent maritime construction standards.
Technological Innovations in FSW
Continuous innovations are driving the widespread adoption of FSW.
Advanced technologies such as robotic FSW and laser-assisted FSW are expanding the operational capabilities, enabling more precise and efficient welds.
Robotic platforms increase the flexibility of FSW applications in complex or large structures.
Laser-assisted FSW uses a laser to preheat materials, reducing tool wear and increasing welding speed.
These advancements highlight the potential of FSW to transform material joining processes across industries.
Challenges and Considerations
Despite its advantages, FSW is not without challenges.
Tool wear, especially when dealing with hard materials, can be significant, affecting the process’s economic viability.
Material adaptability is crucial, as not all alloys are suitable for FSW.
Successful implementation requires thorough understanding and careful control of parameters such as tool rotation speed, travel speed, and downward force.
Developing FSW processes for new material combinations often necessitates research and development efforts.
Conclusion
Friction Stir Welding is a revolutionary method in the field of materials joining.
It offers numerous benefits such as superior joint strength and environmental advantages.
Its application in joining dissimilar materials opens doors to innovative manufacturing processes and products.
As technology progresses, further innovations and developments in FSW will continue to enhance its efficiency and broaden its scope.
Industries show increasing interest in this technique as it consistently proves its value in demanding applications.
The future of FSW is promising, with its potential to redefine how industries approach the challenge of joining different materials.
資料ダウンロード
QCD管理受発注クラウド「newji」は、受発注部門で必要なQCD管理全てを備えた、現場特化型兼クラウド型の今世紀最高の受発注管理システムとなります。
ユーザー登録
受発注業務の効率化だけでなく、システムを導入することで、コスト削減や製品・資材のステータス可視化のほか、属人化していた受発注情報の共有化による内部不正防止や統制にも役立ちます。
NEWJI DX
製造業に特化したデジタルトランスフォーメーション(DX)の実現を目指す請負開発型のコンサルティングサービスです。AI、iPaaS、および先端の技術を駆使して、製造プロセスの効率化、業務効率化、チームワーク強化、コスト削減、品質向上を実現します。このサービスは、製造業の課題を深く理解し、それに対する最適なデジタルソリューションを提供することで、企業が持続的な成長とイノベーションを達成できるようサポートします。
製造業ニュース解説
製造業、主に購買・調達部門にお勤めの方々に向けた情報を配信しております。
新任の方やベテランの方、管理職を対象とした幅広いコンテンツをご用意しております。
お問い合わせ
コストダウンが利益に直結する術だと理解していても、なかなか前に進めることができない状況。そんな時は、newjiのコストダウン自動化機能で大きく利益貢献しよう!
(β版非公開)