- お役立ち記事
- Basics of FTA in DR and measures to prevent quality problems
Basics of FTA in DR and measures to prevent quality problems
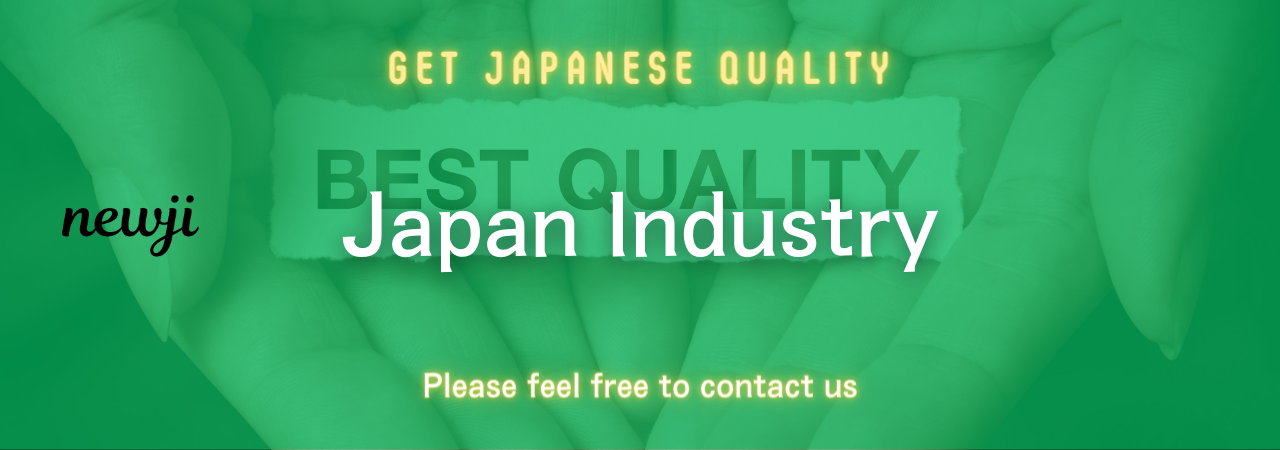
目次
Understanding Failure Mode and Effects Analysis (FTA)
In the realm of quality assurance and control, Failure Mode and Effects Analysis (FTA) plays a pivotal role.
FTA is a systematic approach used to identify potential failures in products or processes and assess their impact.
By understanding these failure modes, companies can devise strategies to mitigate risks and ensure that quality remains uncompromised.
An outcome-focused approach, FTA is designed to prioritize issues that could cause significant consequences if not addressed in advance.
It’s a preventive measure rather than a corrective one, which makes it an essential tool for companies aiming to maintain high standards and avoid costly setbacks.
The Importance of FTA in the Dominican Republic
In the Dominican Republic, industries such as manufacturing, automotive, electronics, and pharmaceuticals heavily rely on FTA.
The reason is simple: these sectors demand precision and reliability.
Any lapse in quality can lead not only to financial losses but also to damage to a company’s reputation and customer trust.
Implementing FTA in these industries helps to streamline operations by identifying weak links before they lead to serious failures.
Such proactive measures can significantly cut down on production costs and enhance overall efficiency.
Steps Involved in FTA
For those new to FTA, here is a simple breakdown of the steps involved:
1. Identify the Process
The first step is to clearly define the process or system that needs analysis.
This includes understanding every component of the system, its function, and how these components interact.
2. Identify Potential Failure Modes
List down all conceivable failure modes for each component of the system.
Failure modes are ways in which a process might fail, leading to an undesirable outcome.
3. Determine Effects of Each Failure Mode
Next, analyze the effects associated with each failure mode.
How does this failure impact the overall operation of the system?
Understanding these effects helps in assessing the severity of each potential failure.
4. Evaluate the Causes
Identify the root cause of each failure mode.
Understanding the cause is crucial for developing effective strategies for mitigation.
5. Prioritize the Failure Modes
Not all failure modes are equally threatening.
Prioritize them based on the severity of their effects, frequency of occurrence, and ease of detection.
This helps in allocating resources efficiently to address the most critical issues.
6. Develop Action Plans
Finally, establish action plans to mitigate or eliminate the potential failures.
Effective measures might include design changes, process alterations, or additional quality checks.
Common Quality Issues and Their Prevention
Even with FTA in place, some common quality issues can slip through.
Understanding these can help further tighten the preventive measures taken through FTA.
1. Human Error
Human error continues to be a leading cause of quality problems.
Training programs, clear work instructions, and regular audits can help minimize these errors.
Automation can also play a role in reducing reliance on human intervention for routine tasks.
2. Equipment Failure
Equipment failure often leads to production halts and defects.
Regular maintenance schedules, coupled with real-time monitoring systems, can help predict failures before they occur.
3. Material Defects
Defective raw materials can severely impact product quality.
Establishing stringent supplier quality assessments and frequent incoming material inspections can prevent such issues.
4. Process Variability
Variability in processes can lead to deviations from set quality standards.
Standardizing operations via machine calibrations and detailed control plans is essential to maintain consistent outputs.
Advantages of FTA Implementation
The successful implementation of FTA comes with numerous advantages that can set a company apart from its competitors.
1. Cost Savings
By identifying potential failures before they occur, companies can avoid significant costs associated with defects, recalls, and rework.
2. Improved Product Quality
Better product quality leads to enhanced customer satisfaction and increased trust in the brand.
Implementing FTA ensures products are reliable and meet set quality standards.
3. Enhanced Process Efficiency
When potential failures are managed effectively, processes become more streamlined.
This leads to improved productivity and faster turnaround times.
4. Regulatory Compliance
Meeting regulatory standards is a key concern for many industries.
FTA helps in ensuring compliance with relevant regulations and avoiding penalties.
Conclusion
Incorporating Failure Mode and Effects Analysis into the core of business operations, especially within the Dominican Republic’s pivotal industries, is not just beneficial but necessary.
Understanding the intricacies of FTA and adhering to its structured methodology ensures that businesses thrive by minimizing risks and enhancing quality.
By prioritizing preventive over corrective strategies, companies can carve a path towards long-term success, stability, and excellence.
資料ダウンロード
QCD調達購買管理クラウド「newji」は、調達購買部門で必要なQCD管理全てを備えた、現場特化型兼クラウド型の今世紀最高の購買管理システムとなります。
ユーザー登録
調達購買業務の効率化だけでなく、システムを導入することで、コスト削減や製品・資材のステータス可視化のほか、属人化していた購買情報の共有化による内部不正防止や統制にも役立ちます。
NEWJI DX
製造業に特化したデジタルトランスフォーメーション(DX)の実現を目指す請負開発型のコンサルティングサービスです。AI、iPaaS、および先端の技術を駆使して、製造プロセスの効率化、業務効率化、チームワーク強化、コスト削減、品質向上を実現します。このサービスは、製造業の課題を深く理解し、それに対する最適なデジタルソリューションを提供することで、企業が持続的な成長とイノベーションを達成できるようサポートします。
オンライン講座
製造業、主に購買・調達部門にお勤めの方々に向けた情報を配信しております。
新任の方やベテランの方、管理職を対象とした幅広いコンテンツをご用意しております。
お問い合わせ
コストダウンが利益に直結する術だと理解していても、なかなか前に進めることができない状況。そんな時は、newjiのコストダウン自動化機能で大きく利益貢献しよう!
(Β版非公開)