- お役立ち記事
- Basics of grinding and key points for high precision and high efficiency
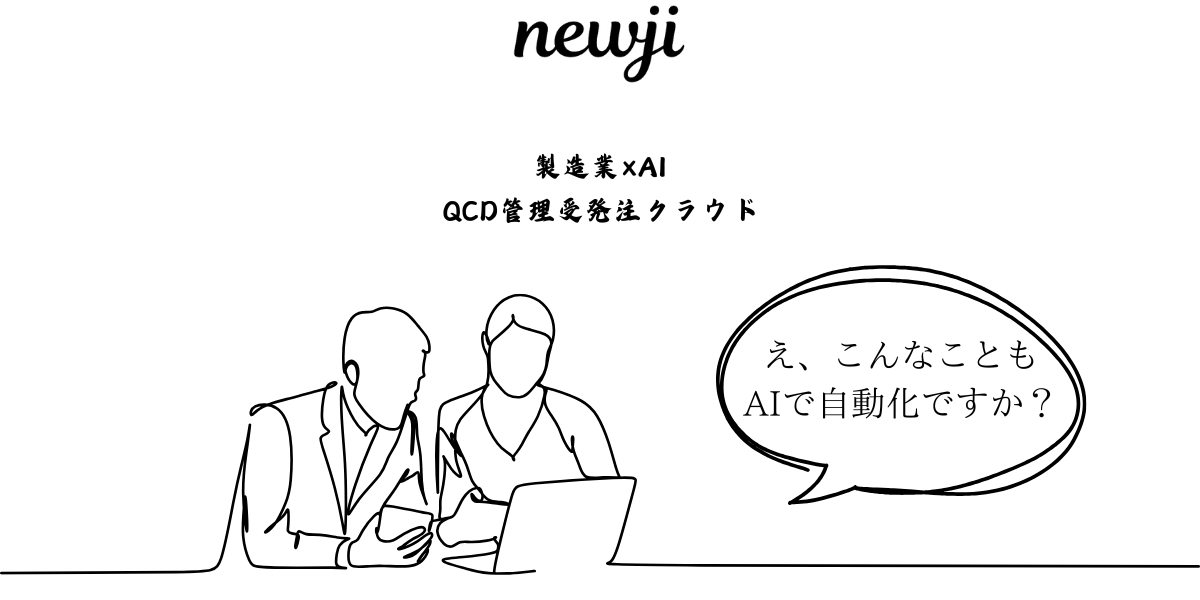
Basics of grinding and key points for high precision and high efficiency
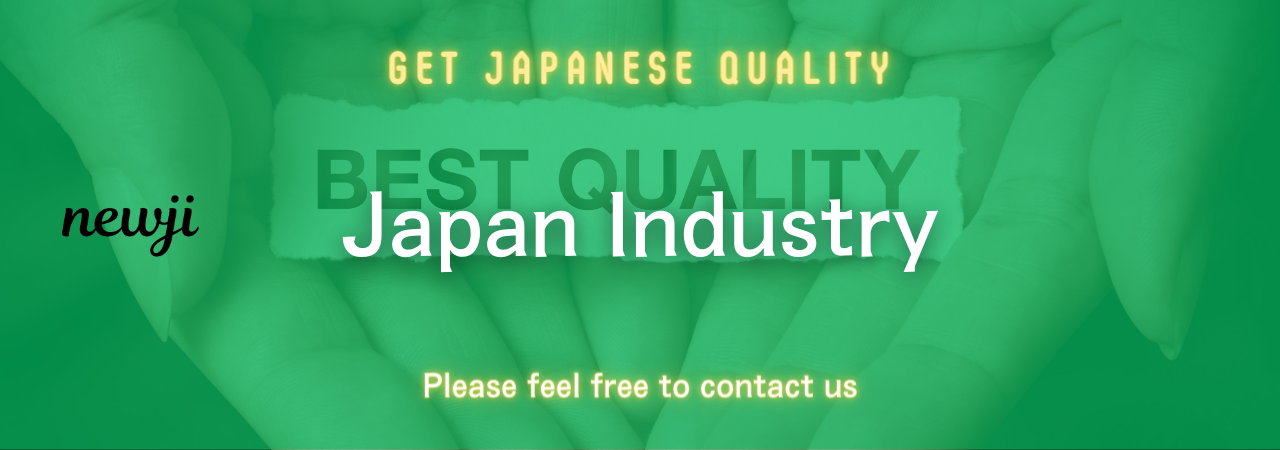
目次
Understanding the Basics of Grinding
Grinding is a fundamental process in manufacturing and mechanical engineering, crucial for achieving precision and efficiency.
At its core, grinding involves the removal of excess material from a workpiece using abrasive wheels.
This technique is deployed across various industries, from automotive to aerospace, where high precision and surface finish are paramount.
The process starts with selecting the appropriate grinding wheel, which is a disc composed of abrasive particles bound together.
These particles are responsible for the removal of material from the surface of the workpiece.
There are different types of grinding wheels, each suited for specific tasks based on their grain size, bond type, and abrasive material.
Types of Grinding Processes
There are several types of grinding processes, each with its own specific purpose and application.
Understanding the differences is crucial to ensure the correct method is employed for a given task.
– **Surface Grinding**: This involves grinding the surface of a workpiece to produce a smooth finish.
It is typically used for flat surfaces and is common in the production of metal sheets.
– **Cylindrical Grinding**: Used primarily for cylindrical surfaces, this process provides smooth and precise finishes.
It is often employed in the automotive industry for axle and bearing production.
– **Centerless Grinding**: This technique involves grinding without the need for clamping the workpiece, which allows for high throughput and is ideal for mass production.
– **Internal Grinding**: Focused on the interior surfaces of holes, bores, or cylinders, this is essential for creating precise internal diameters.
Key Points for High Precision Grinding
Achieving high precision in grinding is a critical goal for manufacturers.
Precision grinding ensures that each part manufactured meets exact specifications, which is especially important in industries with strict quality standards.
Choosing the right grinding wheel is pivotal.
A wheel’s grit size influences the finish and possible level of precision.
Finer grit sizes are suited for detailed, precision work, while coarser grit sizes are more appropriate for rougher operations.
Consistency in speed is another significant factor.
Grinding at a consistent speed maintains uniformity and precision.
Fluctuations in speed can lead to imbalances in material removal, resulting in defects.
Optimizing Grinding Wheel Performance
To achieve high precision grinding, the performance of the grinding wheel itself must be optimized.
– **Wheel Balancing**: Proper balancing of the grinding wheel is crucial.
An imbalanced wheel can cause vibrations that affect precision and can even lead to equipment damage.
– **Dressing and Truing**: Regular dressing and truing of the wheel ensure it maintains its sharpness and shape.
This not only enhances precision but also extends the wheel’s service life.
– **Coolant Use**: Using appropriate coolants efficiently removes heat, avoiding thermal damage to the workpiece and helping maintain tolerance levels.
Maximizing Efficiency in Grinding
For manufacturers, efficiency is just as critical as precision.
A more efficient grinding process can reduce costs and increase production speed.
Here are some strategies to maximize grinding efficiency:
Use of Advanced Materials
Innovative materials, such as superabrasives, can vastly enhance grinding efficiency.
These materials, like cubic boron nitride (CBN) and diamond, offer significantly higher wear resistance and grinding capabilities compared to traditional abrasives.
Automation and Advanced Technologies
Incorporating automation into grinding operations can significantly boost efficiency.
Automated grinding systems reduce human error, enhance consistency, and facilitate 24/7 operations without the need for breaks.
Additionally, advanced computer numerical control (CNC) machines allow for intricate and precise controls over grinding parameters, leading to more efficient operations.
Process Optimization
Optimizing process parameters, like feed rate, depth of cut, and wheel speed, can dramatically affect the efficiency of grinding operations.
Conducting trials and adjustments to find the optimal combination for specific workpieces and machines will yield the best results.
Regular maintenance of grinding machines ensures they operate at peak performance, reducing downtime and prolonging equipment life.
Conclusion
Understanding the basics of grinding and applying strategies for precision and efficiency is essential for any manufacturing process.
It requires selecting the right tools, understanding different grinding methods, and optimizing processes.
With the right focus on precision and efficiency, manufacturers can achieve outstanding quality in their products, ensuring adherence to standards and customer satisfaction.
Investing in advanced technologies and continuous improvement efforts will pay dividends in the form of enhanced precision, efficiency, and profitability.
資料ダウンロード
QCD調達購買管理クラウド「newji」は、調達購買部門で必要なQCD管理全てを備えた、現場特化型兼クラウド型の今世紀最高の購買管理システムとなります。
ユーザー登録
調達購買業務の効率化だけでなく、システムを導入することで、コスト削減や製品・資材のステータス可視化のほか、属人化していた購買情報の共有化による内部不正防止や統制にも役立ちます。
NEWJI DX
製造業に特化したデジタルトランスフォーメーション(DX)の実現を目指す請負開発型のコンサルティングサービスです。AI、iPaaS、および先端の技術を駆使して、製造プロセスの効率化、業務効率化、チームワーク強化、コスト削減、品質向上を実現します。このサービスは、製造業の課題を深く理解し、それに対する最適なデジタルソリューションを提供することで、企業が持続的な成長とイノベーションを達成できるようサポートします。
オンライン講座
製造業、主に購買・調達部門にお勤めの方々に向けた情報を配信しております。
新任の方やベテランの方、管理職を対象とした幅広いコンテンツをご用意しております。
お問い合わせ
コストダウンが利益に直結する術だと理解していても、なかなか前に進めることができない状況。そんな時は、newjiのコストダウン自動化機能で大きく利益貢献しよう!
(Β版非公開)