- お役立ち記事
- Basics of grinding, optimal processing methods, and troubleshooting
月間77,185名の
製造業ご担当者様が閲覧しています*
*2025年2月28日現在のGoogle Analyticsのデータより
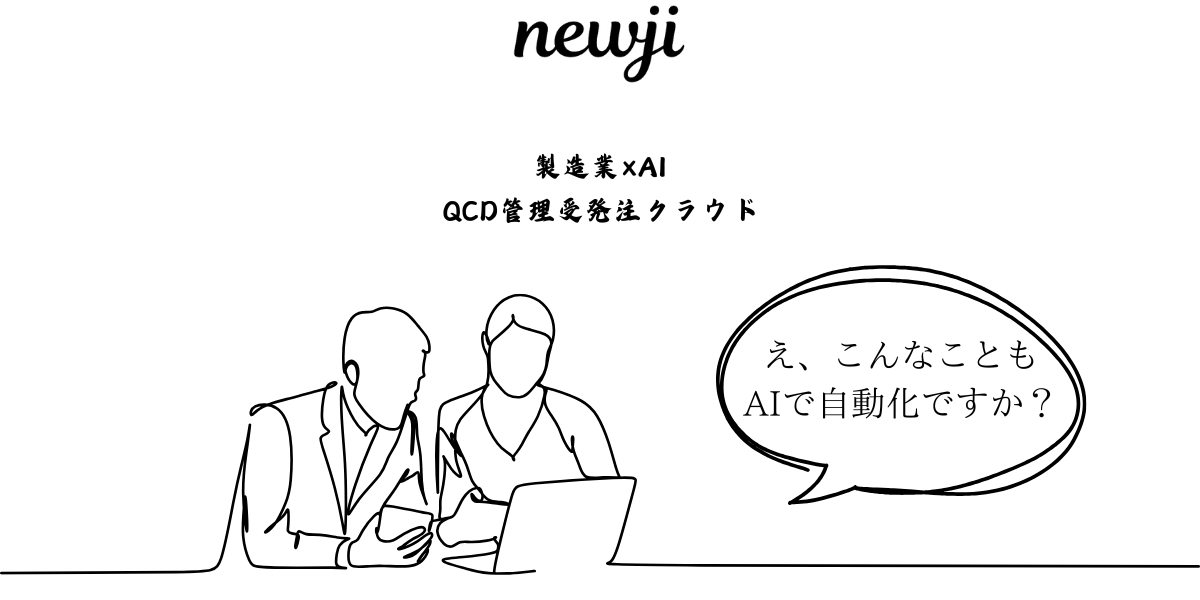
Basics of grinding, optimal processing methods, and troubleshooting
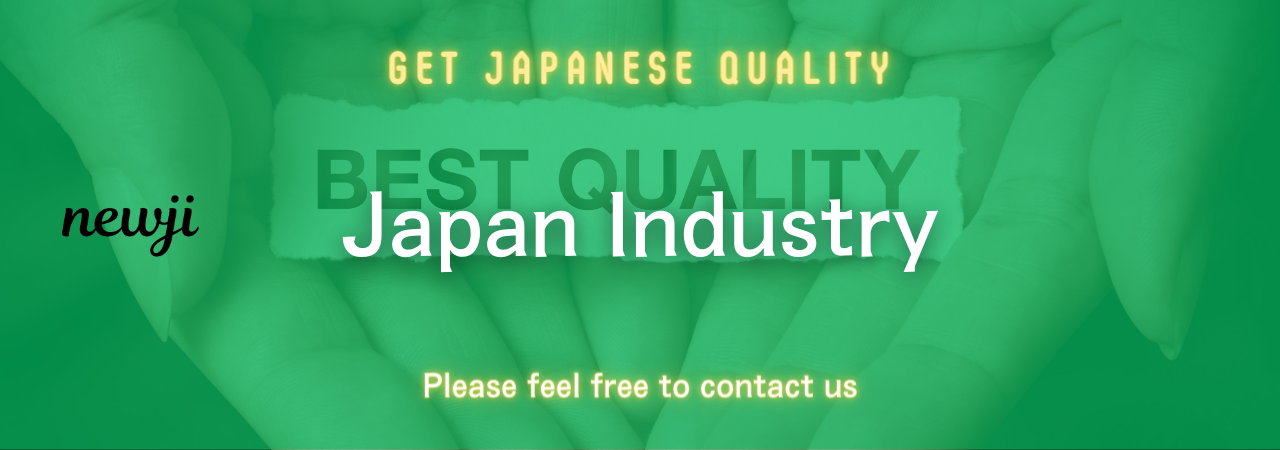
目次
Understanding the Basics of Grinding
Grinding is a machining process that utilizes an abrasive wheel as the cutting tool to remove material from the surface of a workpiece.
It’s one of the key processes used in manufacturing to create a smooth finish on flat surfaces or to achieve the desired dimensions in a part.
In grinding, tiny abrasive particles on the wheel’s surface act as single-point cutting edges.
Despite their small size, they can chip away at the material, effectively sculpting and refining the workpiece surface.
There are various types of grinding processes, such as surface grinding, cylindrical grinding, centerless grinding, and internal grinding.
Each type is suited to specific applications and offers its own benefits and limitations.
Understanding these processes is crucial for selecting the right methods for your manufacturing needs.
Optimal Processing Methods in Grinding
To achieve the best results in grinding, consider the following optimal processing methods.
Selecting the Right Grinding Wheel
The choice of grinding wheel significantly affects the process outcome.
Wheels come in different types, each suitable for specific materials and finishes.
For example, softer wheels are ideal for hard materials because they wear out faster and reduce heat generation.
Conversely, harder wheels work best on softer materials.
The wheel’s grit size also plays a critical role in determining the desired surface finish and material removal rate.
Maintaining Proper Wheel Speed
Wheel speed is another critical factor in grinding operations.
The speed determines the cutting efficiency and can impact surface quality.
Operating at the recommended speed not only ensures effective grinding but also prolongs the wheel’s life.
Ensure the wheel is balanced and operates within the manufacturer’s specifications to avoid excessive vibrations that can lead to poor finish quality.
Implementing Adequate Coolant Supply
Coolants are essential in grinding to reduce heat generated from friction.
Excessive heat can damage both the grinding wheel and the workpiece, leading to poor finish and accuracy.
Using an appropriate coolant and maintaining the right flow rate ensures the grinding area stays cool.
This prevents thermal damage and extends the lifespan of the grinding tool.
Setting the Correct Feed Rate
The feed rate in grinding determines how quickly a wheel grinds away material.
A slower feed rate can result in a finer surface finish, while a faster feed rate can increase material removal rate but might compromise the surface finish.
Adjust the feed rate according to the material being processed and the desired finish to achieve optimal results.
Troubleshooting Common Grinding Issues
Despite careful preparation, grinding issues can still arise.
Here are common problems and their potential solutions.
Wheel Loading
Wheel loading occurs when the grinding wheel gets clogged with material.
This can lead to inefficient grinding and poor surface finish.
To prevent this, use the correct wheel specification for the material, and ensure that washing and cleaning processes are integrated into the operation.
Burning or Surface Burn
Surface burn is caused by excessive heat from grinding, leading to discoloration and surface damage.
This can be addressed by reducing feed rates, increasing the coolant supply, or selecting a softer wheel that generates less heat.
Chatter
Chatter manifests as a wavy pattern on the workpiece surface due to excessive vibration during grinding.
To resolve this, ensure the grinding wheel is balanced and free from defects, and verify that all machine components are properly secured.
Adjusting the spindle speed and using vibration dampening accessories can also help mitigate this issue.
Excessive Wheel Wear
Excessive wheel wear can lead to frequent replacements, impacting production costs.
Selecting a wheel suited to the material, controlling the grinding speed, and employing adequate coolants can reduce wear.
Moreover, regular dressing of the wheel can help maintain its sharpness and efficiency.
Conclusion
Grinding is an essential process in manufacturing, influencing the final quality and precision of a product.
By understanding the basics of grinding, choosing optimal processing methods, and knowing how to troubleshoot common issues, manufacturers can maximize efficiency and achieve superior surface finishes.
Continual evaluation and adjustments to the grinding process ensure consistent performance and product quality.
Whether you’re a beginner or experienced machinist, mastering these fundamentals is key to successful grinding operations.
資料ダウンロード
QCD管理受発注クラウド「newji」は、受発注部門で必要なQCD管理全てを備えた、現場特化型兼クラウド型の今世紀最高の受発注管理システムとなります。
ユーザー登録
受発注業務の効率化だけでなく、システムを導入することで、コスト削減や製品・資材のステータス可視化のほか、属人化していた受発注情報の共有化による内部不正防止や統制にも役立ちます。
NEWJI DX
製造業に特化したデジタルトランスフォーメーション(DX)の実現を目指す請負開発型のコンサルティングサービスです。AI、iPaaS、および先端の技術を駆使して、製造プロセスの効率化、業務効率化、チームワーク強化、コスト削減、品質向上を実現します。このサービスは、製造業の課題を深く理解し、それに対する最適なデジタルソリューションを提供することで、企業が持続的な成長とイノベーションを達成できるようサポートします。
製造業ニュース解説
製造業、主に購買・調達部門にお勤めの方々に向けた情報を配信しております。
新任の方やベテランの方、管理職を対象とした幅広いコンテンツをご用意しております。
お問い合わせ
コストダウンが利益に直結する術だと理解していても、なかなか前に進めることができない状況。そんな時は、newjiのコストダウン自動化機能で大きく利益貢献しよう!
(β版非公開)