- お役立ち記事
- Basics of heat treatment technology and defect prevention methods
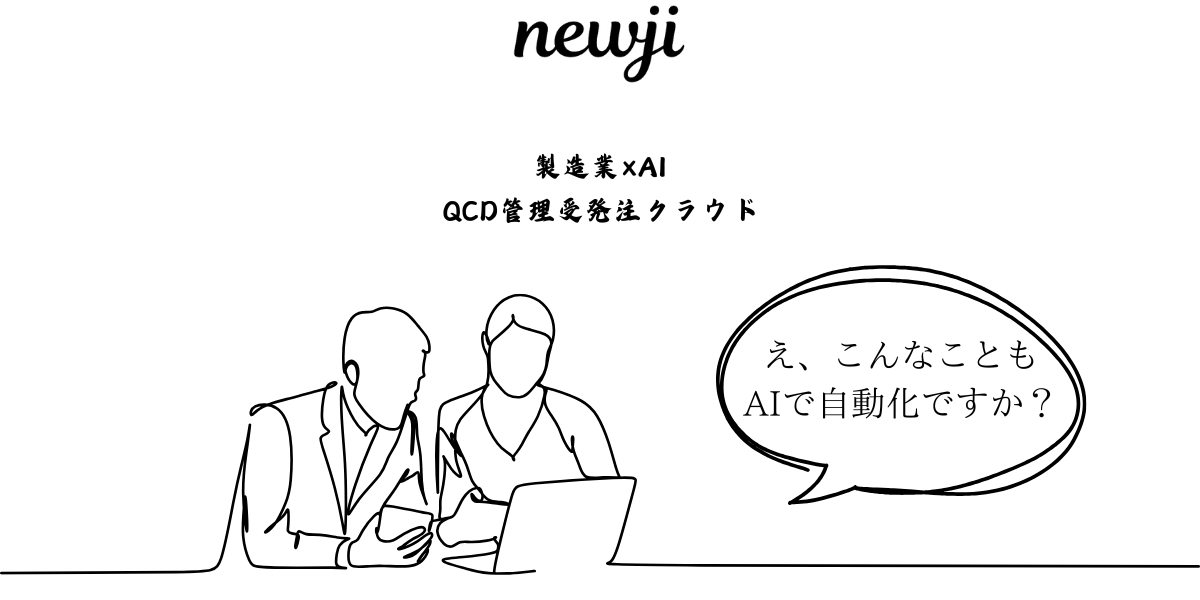
Basics of heat treatment technology and defect prevention methods
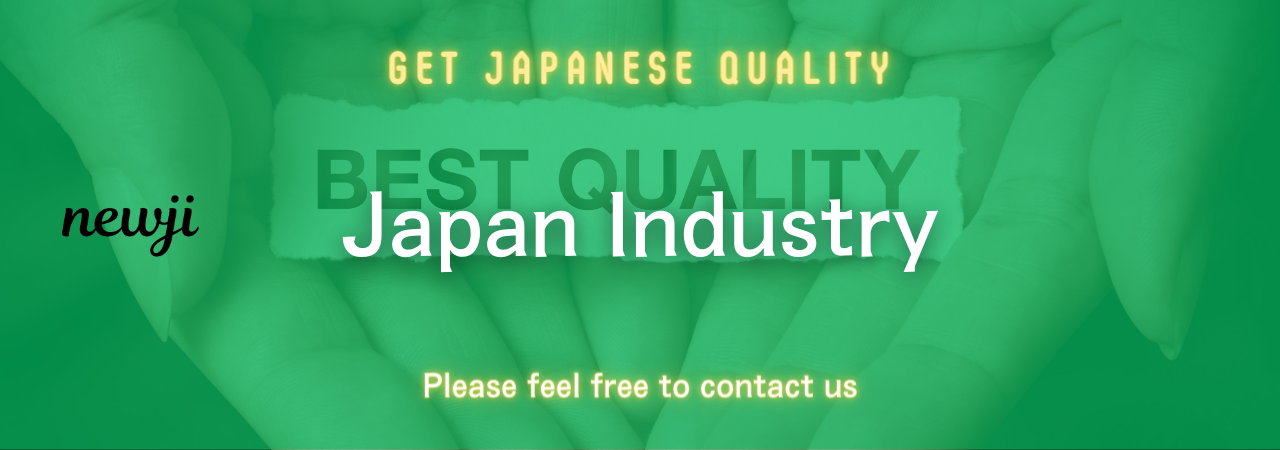
目次
Understanding Heat Treatment Technology
Heat treatment is a process in which metal materials are heated and cooled in a controlled manner to alter their physical and mechanical properties without changing the product shape.
It is a critical process in manufacturing to enhance the material’s properties such as hardness, strength, and elasticity, and in some cases, ductility.
Heat treatment involves various techniques, each tailored to achieve specific outcomes based on the type of metal and the desired properties.
The process has significant applications in industries ranging from automotive to aerospace, making it an essential subject for engineers and metallurgists.
Types of Heat Treatment Processes
There are several heat treatment processes, each with its unique characteristics and applications:
1. Annealing: This process is used to soften steel, improve machinability, and enhance the mechanical properties of the material.
In annealing, the metal is heated to a specific temperature and then slowly cooled.
This slow cooling removes internal stresses, making the metal more workable.
2. Quenching: Quenching involves rapid cooling of metal from a high temperature to set the structure and increase strength and hardness.
The sudden cooling typically occurs in water or oil.
This process is commonly used for tools and machinery parts to enhance wear resistance.
3. Tempering: Usually performed after quenching, tempering reduces the brittleness of metal while maintaining desirable properties like hardness.
The metal is heated to a lower temperature, then cooled, balancing toughness and strength.
4. Normalizing: This process involves heating steel slightly above its critical temperature, then allowing it to air cool.
Normalizing refines grain structure, improves machinability, and increases strength.
5. Case Hardening: A technique used primarily on steel, case hardening involves hardening the surface layer while maintaining a softer, ductile interior.
Methods include carburizing and nitriding, enhancing surface wear resistance.
Common Defects in Heat Treatment
While heat treatment can significantly improve material properties, improper execution can lead to defects.
Understanding these common issues and their prevention is essential for ensuring quality and performance.
1. Distortion
Distortion occurs when the metal warps or bends due to uneven heating or cooling rates.
It can be prevented by ensuring uniform heating and cooling throughout the process.
Using fixtures or supports during treatment can help maintain the structure’s intended shape.
2. Cracking
Cracking is a severe defect typically resulting from rapid cooling or high internal stresses.
It can occur during quenching or when there is insufficient tempering.
Prevention involves controlling cooling rates and adequately tempering the material to relieve internal stresses.
3. Decarburization
Decarburization refers to the loss of carbon from the surface of steel, weakening the material.
This defect is generally due to oxidation during heating.
Preventive measures include heating in controlled atmospheres or using protective coatings to shield the surface.
4. Scaling
Scaling occurs from the reaction of steel surface with oxygen at high temperatures, leading to material loss.
Preventing scaling involves using protective atmospheres or coatings and carefully controlling temperature and time during heating.
5. Grain Growth
Excessive grain size can lead to reduced toughness and strength.
It happens when the metal is exposed to high temperatures for prolonged periods.
To prevent it, maintain precise temperature controls and avoid overheating during treatment.
Preventive Measures and Best Practices
To achieve the desired results in heat treatment and prevent defects, professionals must adhere to best practices:
1. Controlled Environment: Utilize controlled atmospheres to minimize oxidation and decarburization.
Inert gases like argon or nitrogen are often used in furnace environments.
2. Precision in Temperature and Time: Ensure accurate temperature readings and timing to prevent issues like grain growth or distortion.
Modern furnaces equipped with sophisticated controls can help achieve precise conditions.
3. Understand Material Composition: Different materials have specific heat treatment requirements.
Understanding the material composition is crucial to selecting the appropriate treatment type and conditions.
4. Use Proper Fixtures: Support the material properly during heat treatment to prevent warping and maintain shape integrity.
5. Post-Treatment Assessment: Always conduct thorough inspections and tests post-treatment to verify material properties and identify any potential defects early on.
Conclusion
Grasping the fundamentals of heat treatment technology is crucial for enhancing the performance and longevity of metal components.
By understanding the types of heat treatments, recognizing potential defects, and employing best practices, manufacturers can optimize their processes and produce high-quality materials.
Ultimately, effective heat treatment relies on precise control, thorough knowledge of material science, and adherence to meticulously developed protocols.
資料ダウンロード
QCD調達購買管理クラウド「newji」は、調達購買部門で必要なQCD管理全てを備えた、現場特化型兼クラウド型の今世紀最高の購買管理システムとなります。
ユーザー登録
調達購買業務の効率化だけでなく、システムを導入することで、コスト削減や製品・資材のステータス可視化のほか、属人化していた購買情報の共有化による内部不正防止や統制にも役立ちます。
NEWJI DX
製造業に特化したデジタルトランスフォーメーション(DX)の実現を目指す請負開発型のコンサルティングサービスです。AI、iPaaS、および先端の技術を駆使して、製造プロセスの効率化、業務効率化、チームワーク強化、コスト削減、品質向上を実現します。このサービスは、製造業の課題を深く理解し、それに対する最適なデジタルソリューションを提供することで、企業が持続的な成長とイノベーションを達成できるようサポートします。
オンライン講座
製造業、主に購買・調達部門にお勤めの方々に向けた情報を配信しております。
新任の方やベテランの方、管理職を対象とした幅広いコンテンツをご用意しております。
お問い合わせ
コストダウンが利益に直結する術だと理解していても、なかなか前に進めることができない状況。そんな時は、newjiのコストダウン自動化機能で大きく利益貢献しよう!
(Β版非公開)