- お役立ち記事
- Basics of impact stress/impact load, impact force reduction/impact energy absorption and its methods, and application to strength design
月間76,176名の
製造業ご担当者様が閲覧しています*
*2025年3月31日現在のGoogle Analyticsのデータより
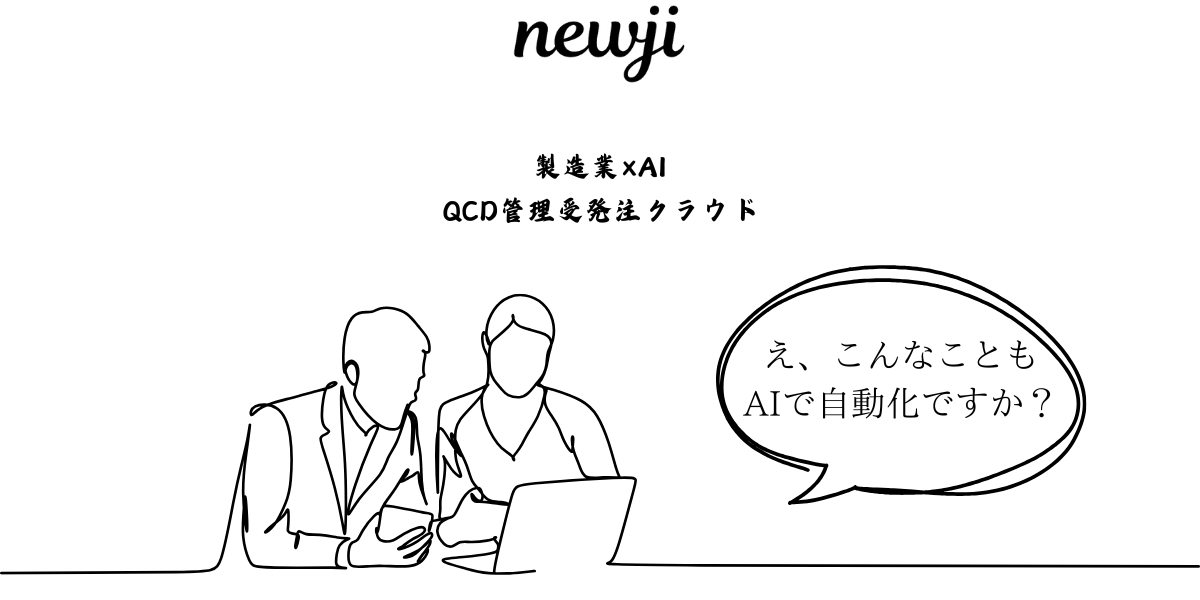
Basics of impact stress/impact load, impact force reduction/impact energy absorption and its methods, and application to strength design
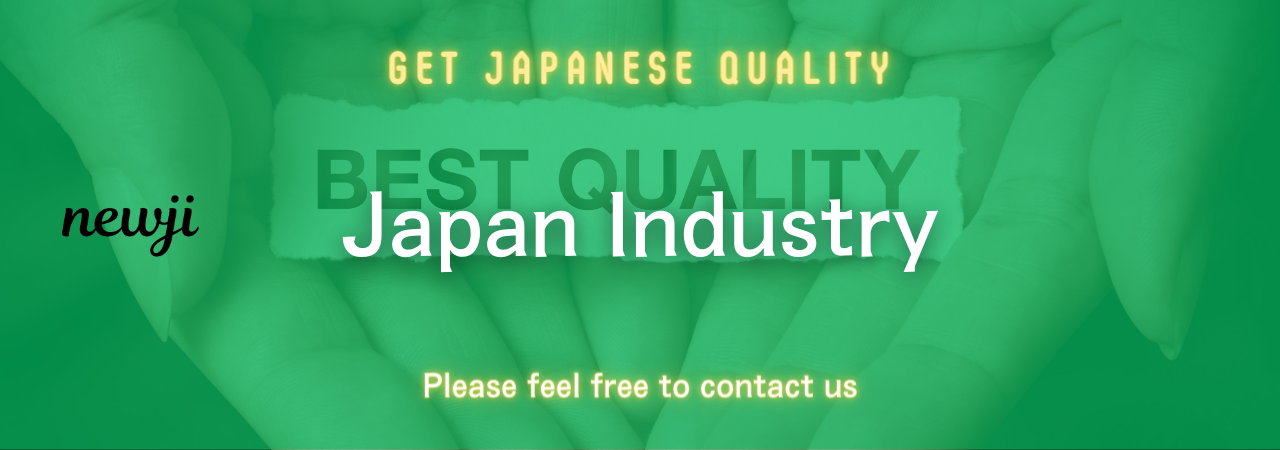
目次
Understanding Impact Stress and Impact Load
Impact stress and impact load are fundamental concepts in engineering and materials science.
Understanding these concepts is crucial for designing structures and products that can withstand sudden forces or shocks.
In simple terms, impact stress refers to the force applied per unit area when an object hits or collides with another surface.
Impact load, on the other hand, is the actual force exerted on an object during such a collision.
Both terms are often used interchangeably but have distinct meanings.
When designing materials or structures, engineers must consider the potential for impact stress and load.
This consideration is essential to prevent failure or damage that could result from impacts.
The ability of a material or structure to endure such forces without permanent deformation or failure is known as its impact strength.
By analyzing impact forces, engineers can anticipate how a material behaves under different scenarios.
Impact stress calculations often involve assessing the velocity and mass of the impacting object and the properties of the impacted surface.
How Impact Force is Mitigated
To prevent damage from impact stress, engineers employ various methods to mitigate the force.
One common approach involves designing materials and structures that can absorb or dissipate energy during a collision.
Here are some effective methods for reducing impact force:
Material Properties and Design
The selection of materials with inherent toughness and resilience can significantly reduce the impact force on a structure.
Materials such as rubber or composite materials can absorb significant amounts of energy, thus reducing stress concentrations.
Design features like rounded edges, ridges, or channels can also help distribute impact forces more evenly.
This distribution reduces localized stress and minimizes potential damage.
Use of Shock Absorbers
Shock absorbers are devices designed to dissipate kinetic energy from impacts effectively.
They can take various forms, such as hydraulic dampers, elastomeric pads, or pneumatic systems.
Shock absorbers convert the energy from an impact into controlled motion or deformation, thereby reducing the force transmitted through a structure.
Cushioning and Padding
In situations where impact forces must be managed, cushioning materials offer an excellent solution.
Foams, gels, and similar materials are used to create buffers that absorb impacts, thereby reducing stress on the objects or structures they protect.
This approach is especially common in packaging where delicate items need protection during transport.
Impact Energy Absorption Techniques
The goal of impact energy absorption is to prevent damage by managing how energy is transferred through a structure.
Several techniques are used to absorb and dissipate energy effectively:
Viscoelastic Materials
Viscoelastic materials are those that exhibit both viscous and elastic characteristics when undergoing deformation.
These materials can absorb energy and return to their original state slowly, unlike purely elastic materials that return more quickly.
This time-dependent deformation helps distribute and dissipate impact energy efficiently.
Crashworthy Structures
In automotive design, “crashworthiness” refers to a structure’s ability to protect occupants during a collision.
Engineered crumple zones are designed to deform in a controlled way upon impact, absorbing energy that might otherwise be transmitted to the passenger compartment.
This feature reduces the force experienced by occupants, thereby decreasing the risk of injury.
Layered and Composite Structures
Layered materials, such as laminates and composites, can absorb more energy than single-material structures due to their combined properties.
The interaction between layers upon impact provides additional pathways for energy dissipation.
This design method is often seen in safety gear like helmets and body armor.
Applying Impact Study in Strength Design
When incorporating impact stress considerations into strength design, engineers must perform comprehensive analyses to ensure safety and reliability under various conditions.
Finite Element Analysis (FEA)
One of the primary tools used in strength design is Finite Element Analysis.
FEA models complex geometries and material behaviors under simulated impact conditions to predict stress and deformation accurately.
This analysis enables engineers to identify potential weak points and optimize structural design for greater impact resistance.
Material Testing and Selection
Selecting the right materials is a critical step in any strength design process.
Through rigorous testing, materials are evaluated for their impact resistance and energy absorption capabilities.
Testing might include drop tests, pendulum impacts, or other standardized assessments to provide data on material performance under stress.
Safety Standards and Compliance
Many industries have specific safety standards that dictate how products should perform under impact conditions.
Adhering to these standards ensures that designs are not only effective but also legally compliant.
Engineers must stay abreast of these standards when designing products and structures to ensure they meet all required benchmarks.
The Future of Impact Stress and Load Management
Advancements in materials science continually improve the ability to manage impact stress and load.
Novel materials such as smart polymers and nanocomposites offer the potential for even greater energy absorption and distribution capabilities.
As technology advances, the use of sophisticated simulation tools in tandem with innovative materials will likely lead to safer, more resilient designs across industries.
Understanding and addressing impact stress and load are vital for developing durable, safe, and efficient products and structures.
By employing various methods to absorb and reduce impact energy, engineers can create designs that meet the challenges of both everyday use and extreme conditions.
資料ダウンロード
QCD管理受発注クラウド「newji」は、受発注部門で必要なQCD管理全てを備えた、現場特化型兼クラウド型の今世紀最高の受発注管理システムとなります。
ユーザー登録
受発注業務の効率化だけでなく、システムを導入することで、コスト削減や製品・資材のステータス可視化のほか、属人化していた受発注情報の共有化による内部不正防止や統制にも役立ちます。
NEWJI DX
製造業に特化したデジタルトランスフォーメーション(DX)の実現を目指す請負開発型のコンサルティングサービスです。AI、iPaaS、および先端の技術を駆使して、製造プロセスの効率化、業務効率化、チームワーク強化、コスト削減、品質向上を実現します。このサービスは、製造業の課題を深く理解し、それに対する最適なデジタルソリューションを提供することで、企業が持続的な成長とイノベーションを達成できるようサポートします。
製造業ニュース解説
製造業、主に購買・調達部門にお勤めの方々に向けた情報を配信しております。
新任の方やベテランの方、管理職を対象とした幅広いコンテンツをご用意しております。
お問い合わせ
コストダウンが利益に直結する術だと理解していても、なかなか前に進めることができない状況。そんな時は、newjiのコストダウン自動化機能で大きく利益貢献しよう!
(β版非公開)