- お役立ち記事
- Basics of inventory management and practical course for cost reduction
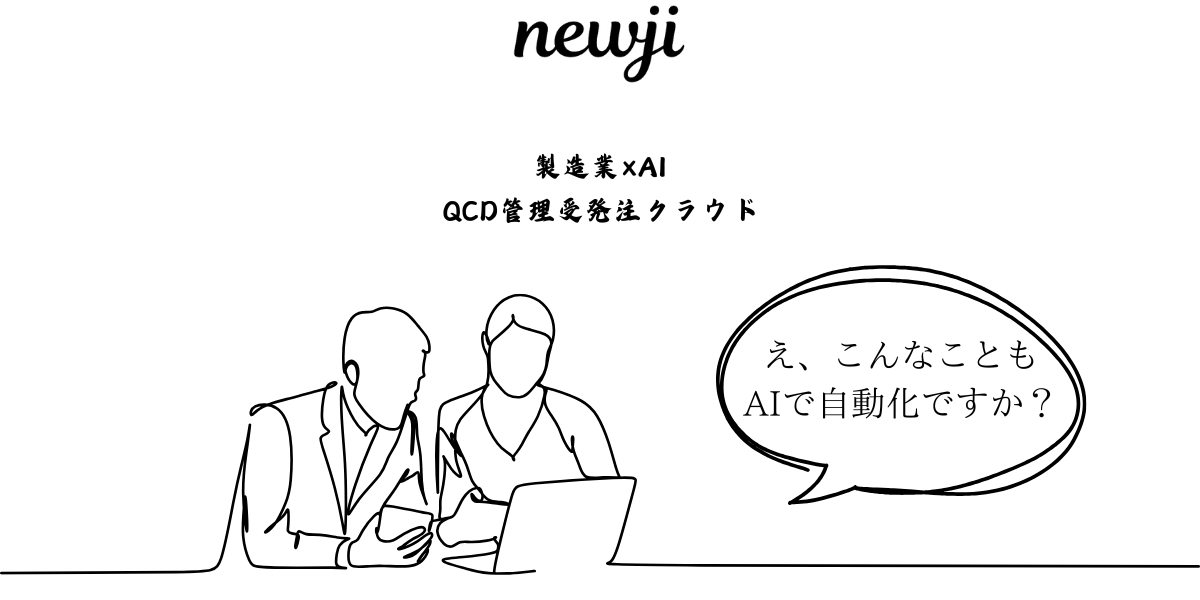
Basics of inventory management and practical course for cost reduction
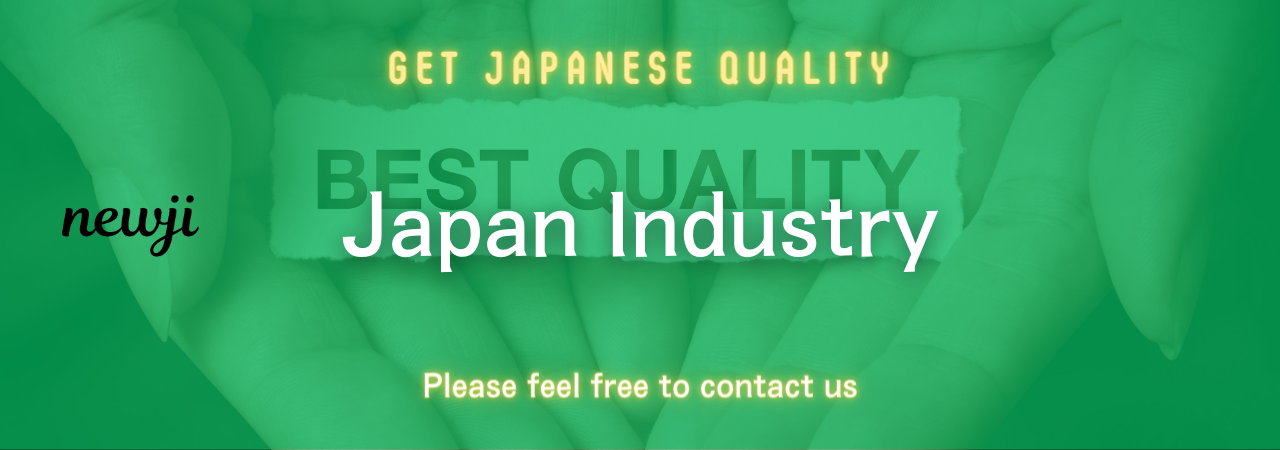
目次
Introduction to Inventory Management
Inventory management is a crucial aspect of running a successful business.
It involves overseeing the ordering, storing, and using of a company’s inventory, which includes both raw materials and finished products.
Effective inventory management ensures that a business has the right products in the right quantity for sale, at the right time.
In addition, it plays a significant role in cost reduction, helping companies increase efficiency and profitability.
Importance of Inventory Management
Proper inventory management aids in minimizing costs while maximizing profits.
It prevents overstocking and stockouts, ensuring that a business can meet customer demand without unnecessary expenses.
Additionally, maintaining optimal inventory levels reduces storage costs and mitigates the risk of obsolete stock.
Effective inventory management can also enhance customer satisfaction by improving the reliability and speed of fulfilling orders.
Types of Inventory
Inventory can be categorized into three main types:
1. **Raw Materials**: These are the basic components used to produce goods.
Proper management of raw materials ensures a smooth production process without delays.
2. **Work-In-Progress (WIP)**: This refers to products that are partially completed.
Effective monitoring of WIP inventory helps to identify bottlenecks and improve production efficiency.
3. **Finished Goods**: These are products ready for sale to customers.
Managing finished goods inventory ensures that orders can be fulfilled promptly.
Inventory Management Techniques
Several techniques can be employed to manage inventory effectively.
Here are some popular ones:
Just-In-Time (JIT) Inventory
The Just-In-Time inventory method aims to minimize inventory levels by producing or acquiring goods only as needed.
This technique reduces holding costs and waste.
However, it requires precise demand forecasting and a reliable supply chain to be successful.
Economic Order Quantity (EOQ)
EOQ is a mathematical model that helps determine the optimal order quantity, minimizing the total costs of inventory.
This includes ordering costs and holding costs.
It strikes a balance between the costs associated with ordering inventory and the costs of storing it.
ABC Analysis
ABC analysis is a technique used to categorize inventory into three classes:
– **Class A**: High-value items with low sales frequency.
These items require tight control and accurate record-keeping.
– **Class B**: Moderate value items with moderate sales frequency.
These require periodic reviews.
– **Class C**: Low-value items with high sales frequency.
These require simpler controls and record-keeping.
ABC analysis helps prioritize resources and management efforts on the most critical items.
Strategies for Cost Reduction
There are several strategies businesses can employ to reduce inventory costs effectively:
Improve Demand Forecasting
Accurate demand forecasting allows businesses to order precisely what is required, minimizing excess and obsolete inventory.
Utilizing advanced analytics and historical sales data can enhance the precision of demand forecasting.
Optimize Order Quantities
Finding the balance between ordering too much and too little is key to cost reduction.
Employing techniques like EOQ and reviewing supplier agreements can result in better order quantity decisions and lower costs.
Enhance Supplier Relationships
Building strong relationships with suppliers can lead to better terms and faster response times.
Negotiating discounts for bulk orders and shorter lead times can contribute to cost savings.
Implementing Technology
Leveraging technology, such as inventory management software, can significantly enhance accuracy and efficiency.
These tools provide real-time inventory tracking, automate reordering processes, and offer insights for improved decision-making.
Challenges in Inventory Management
Despite its importance, inventory management can present numerous challenges:
– **Demand Variability**: Changes in customer demand can result in overstocking or stockouts, affecting profitability.
– **Accuracy**: Maintaining accurate inventory records is essential, but can be challenging without appropriate systems in place.
– **Lead Time Variability**: Unpredictable supplier lead times can disrupt inventory levels and complicate order fulfillment.
– **Cost Constraints**: Striking a balance between cost reduction and maintaining sufficient inventory levels can be complex.
Conclusion
Mastering inventory management practices is essential for businesses aiming to optimize efficiency and reduce costs.
By understanding the basics, employing effective techniques, and leveraging technology, companies can maintain the right inventory levels while boosting profitability.
Addressing challenges diligently and continuously refining processes will ensure effective inventory management and sustained business success.
資料ダウンロード
QCD調達購買管理クラウド「newji」は、調達購買部門で必要なQCD管理全てを備えた、現場特化型兼クラウド型の今世紀最高の購買管理システムとなります。
ユーザー登録
調達購買業務の効率化だけでなく、システムを導入することで、コスト削減や製品・資材のステータス可視化のほか、属人化していた購買情報の共有化による内部不正防止や統制にも役立ちます。
NEWJI DX
製造業に特化したデジタルトランスフォーメーション(DX)の実現を目指す請負開発型のコンサルティングサービスです。AI、iPaaS、および先端の技術を駆使して、製造プロセスの効率化、業務効率化、チームワーク強化、コスト削減、品質向上を実現します。このサービスは、製造業の課題を深く理解し、それに対する最適なデジタルソリューションを提供することで、企業が持続的な成長とイノベーションを達成できるようサポートします。
オンライン講座
製造業、主に購買・調達部門にお勤めの方々に向けた情報を配信しております。
新任の方やベテランの方、管理職を対象とした幅広いコンテンツをご用意しております。
お問い合わせ
コストダウンが利益に直結する術だと理解していても、なかなか前に進めることができない状況。そんな時は、newjiのコストダウン自動化機能で大きく利益貢献しよう!
(Β版非公開)