- お役立ち記事
- Basics of knapping technology and its role in manufacturing
Basics of knapping technology and its role in manufacturing
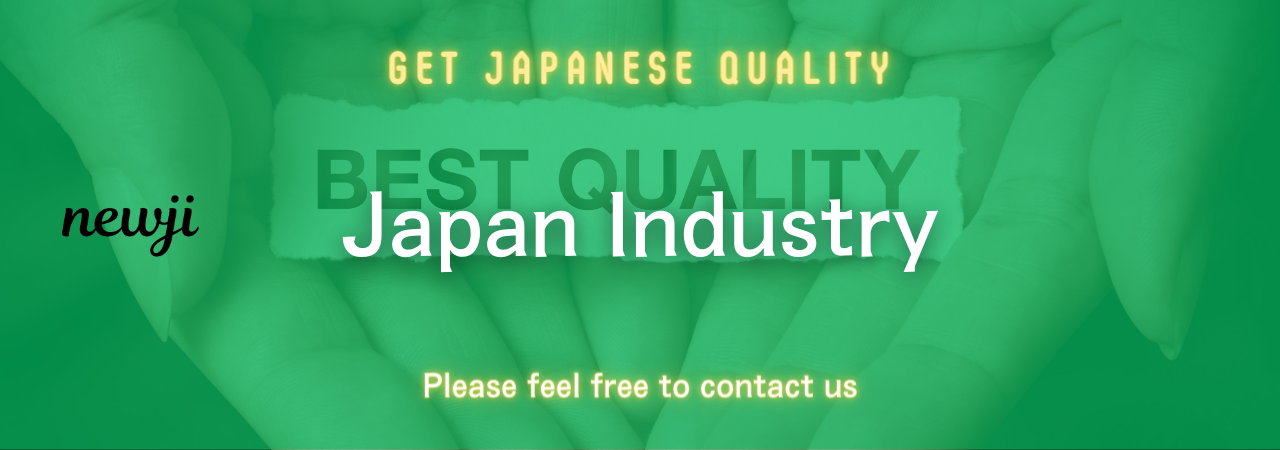
Knapping technology has been around for thousands of years, long before the advent of modern machinery and tools.
This fascinating process involves shaping stones into tools or flakes by striking them with another object.
Over time, knapping techniques have evolved, playing a crucial role in manufacturing.
Let’s explore the basics of knapping technology and how it still influences manufacturing today.
目次
Understanding Knapping Technology
Knapping refers to the craft of striking stones to create sharp edges and shapes, typically for making tools or weapons.
This method dates back to prehistoric times when early humans crafted tools from flint, chert, and obsidian.
The two main techniques are direct percussion and indirect percussion.
Direct Percussion
In direct percussion, a hammerstone is used to strike the core stone directly.
This method is straightforward and involves hitting the stone at precise angles to create sharp flakes.
Indirect Percussion
Indirect percussion, on the other hand, involves using an intermediary tool, such as a punch, to apply force to the core stone.
The punch is struck with a hammerstone, allowing for more controlled and varied flake production.
Both methods require considerable skill and an understanding of material properties to achieve the desired results.
The Evolution Of Knapping Techniques
As human civilization progressed, so did the techniques and materials used in knapping.
Early knappers primarily used flint because of its conchoidal fracture, which allows it to break predictably.
Over time, other materials like quartz and jasper were also utilized.
Pressure Flaking
One significant advancement was the development of pressure flaking.
This technique, which came into prominence during the Neolithic period, involves applying steady pressure with a pointed tool to remove small flakes from the core stone.
Pressure flaking allows for more precise shaping and finer tools compared to percussion methods.
Heat Treatment
Another notable evolution is heat treatment.
Knappers discovered that heating stones like chert and flint made them easier to flake and shape.
By carefully controlling temperature, they could produce superior tools with minimal effort.
Knapping Technology In Modern Manufacturing
While knapping might seem like an ancient, outdated technique, its principles are still relevant in modern manufacturing processes.
Today’s industries use knapping-inspired methods to create tools and components with high precision.
Controlled Fracture Techniques
One modern application is the use of controlled fracture techniques in manufacturing.
For instance, glass and ceramics industries employ similar methods to shape brittle materials.
By understanding the principles of stress and fracture, manufacturers can create intricate designs with minimal waste.
High-Precision Cutting Tools
Furthermore, the concept of pressure application in knapping has translated to high-precision cutting tools.
Industries such as aerospace and automotive heavily rely on precision in crafting components.
Tools like diamond-tipped drills and cutters are designed to apply pressure and create clean cuts, much like pressure flaking in knapping.
The Importance Of Material Properties
One crucial aspect of knapping that remains relevant today is the understanding of material properties.
In knapping, choosing the right stone was paramount to successfully crafting tools.
The same principle applies in modern manufacturing: selecting the appropriate material is essential for achieving desired results.
Brittle vs. Ductile Materials
Brittle materials, such as glass and ceramics, fracture in a manner similar to knapped stones.
Manufacturers must consider this when designing and producing brittle components.
On the other hand, ductile materials, like metals, behave differently and require appropriate techniques for cutting and shaping.
Composite Materials
The rise of composite materials in modern manufacturing also echoes ancient practices.
Just as early humans combined different types of stones to enhance tool performance, today’s industries blend materials to create products with superior properties.
Composite materials offer strength, flexibility, and durability, fulfilling specific requirements in various applications.
Conclusion
The basics of knapping technology and its role in manufacturing reveal a remarkable continuity of human ingenuity.
From ancient tool-making to modern precision engineering, the fundamental principles of shaping and fracturing materials remain vital.
Understanding these techniques not only honors our historical roots but also drives innovation in contemporary manufacturing.
As technology continues to evolve, the lessons learned from knapping will undoubtedly influence future advancements, ensuring that this ancient craft remains relevant for generations to come.
資料ダウンロード
QCD調達購買管理クラウド「newji」は、調達購買部門で必要なQCD管理全てを備えた、現場特化型兼クラウド型の今世紀最高の購買管理システムとなります。
ユーザー登録
調達購買業務の効率化だけでなく、システムを導入することで、コスト削減や製品・資材のステータス可視化のほか、属人化していた購買情報の共有化による内部不正防止や統制にも役立ちます。
NEWJI DX
製造業に特化したデジタルトランスフォーメーション(DX)の実現を目指す請負開発型のコンサルティングサービスです。AI、iPaaS、および先端の技術を駆使して、製造プロセスの効率化、業務効率化、チームワーク強化、コスト削減、品質向上を実現します。このサービスは、製造業の課題を深く理解し、それに対する最適なデジタルソリューションを提供することで、企業が持続的な成長とイノベーションを達成できるようサポートします。
オンライン講座
製造業、主に購買・調達部門にお勤めの方々に向けた情報を配信しております。
新任の方やベテランの方、管理職を対象とした幅広いコンテンツをご用意しております。
お問い合わせ
コストダウンが利益に直結する術だと理解していても、なかなか前に進めることができない状況。そんな時は、newjiのコストダウン自動化機能で大きく利益貢献しよう!
(Β版非公開)