- お役立ち記事
- Basics of metal fatigue and its application to fatigue life prediction and fatigue strength improvement technology
月間76,176名の
製造業ご担当者様が閲覧しています*
*2025年3月31日現在のGoogle Analyticsのデータより
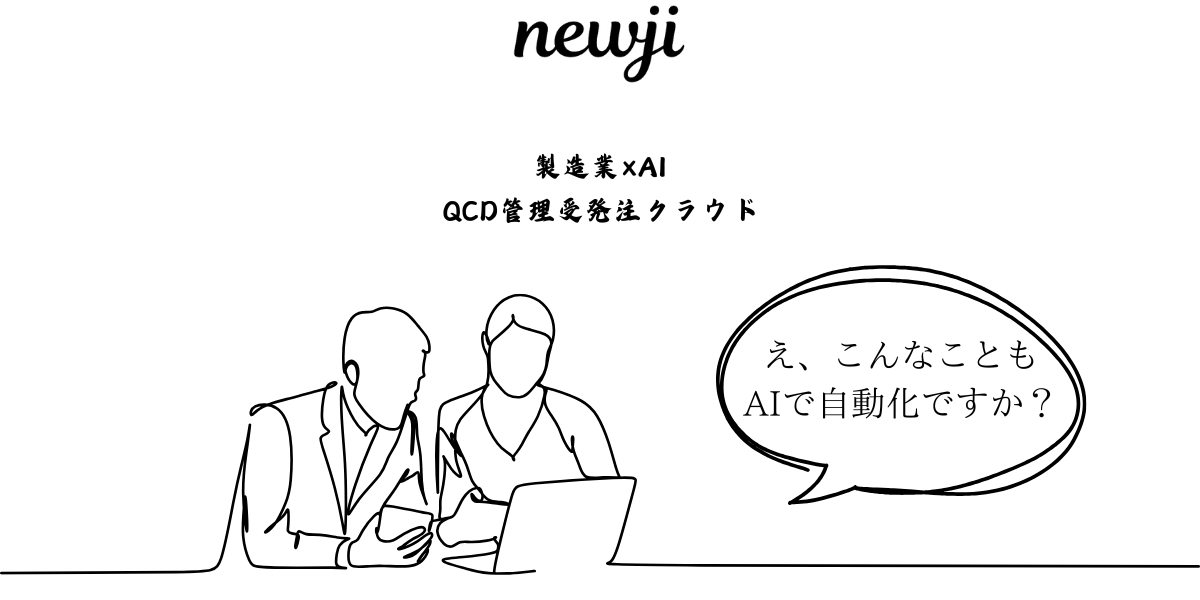
Basics of metal fatigue and its application to fatigue life prediction and fatigue strength improvement technology
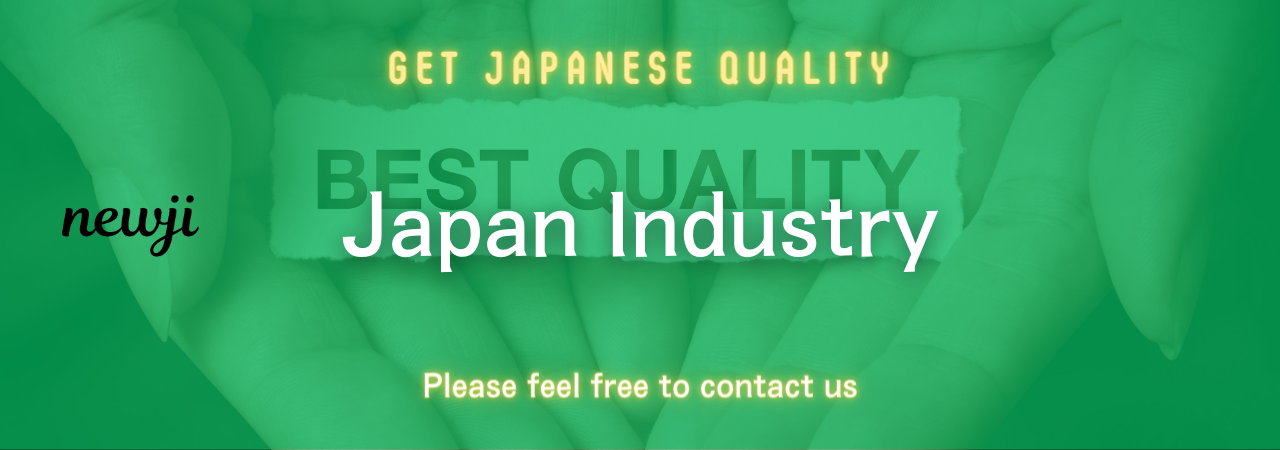
目次
Understanding Metal Fatigue
Metal fatigue is a phenomenon where a material progressively loses strength and structural integrity due to repeated stress and strain.
Think of metal fatigue as the gradual weakening of metal, much like how bending a paperclip back and forth eventually causes it to break.
This weakening manifests itself as tiny cracks in the material, which can then grow over time, leading to failure even if the stresses that caused the fatigue are well below the material’s original strength threshold.
It’s a critical consideration when engineering any structure or component that will be subject to regular load cycles, such as bridges, airplanes, and automobiles.
The Causes of Metal Fatigue
Metal fatigue occurs because of cyclic loading, which involves applying repeated loads or stresses over time.
These loads might be as simple as traffic crossing a bridge, wind blowing against a structure, or even the regular use of machinery.
There are generally three stages in the fatigue process: crack initiation, crack propagation, and sudden fracture.
The initiation phase is where microscopic cracks begin to form.
These usually occur at points of high stress concentrations, which can be caused by surface imperfections or material flaws.
They can also originate from small scratches, dents, or areas exposed to corrosion.
The propagation phase follows, where these microscopic cracks start to grow with each load cycle.
Finally, the sudden fracture phase is when the material can no longer withstand the stresses and breaks completely.
Techniques for Predicting Fatigue Life
Understanding and predicting fatigue life is crucial for ensuring the longevity and reliability of materials.
Several popular methods are used to determine the fatigue life of a material.
The S-N Curve Approach
One of the most traditional methods used is the S-N Curve approach.
‘S’ stands for stress, and ‘N’ represents the number of cycles to failure.
Engineers use this graph to predict the fatigue life of materials under specific loading conditions.
The basic idea is to subject a specimen of the material to repeated stress cycles at a constant amplitude until it fails, recording the number of cycles it can withstand.
The data from multiple tests can then be plotted on a graph – the S-N curve.
The curve demonstrates how many cycles a material can handle before it succumbs to fatigue.
Lower stress levels result in longer fatigue life (more cycles to failure), while higher stress levels typically lead to a shorter fatigue life.
Fracture Mechanics Method
Another approach is the fracture mechanics method, which focuses on the growth of cracks rather than the number of cycles.
This is crucial when small flaws exist in a material, and the aim is to predict how long it will take for these flaws to grow to a size that will cause failure.
Fracture mechanics involves analyzing the stress intensity factors and understanding how cracks grow under cyclic loading.
The process models the growth of cracks based on the material properties and the geometric configuration of the cracks.
It’s particularly useful for materials prone to brittle fracture rather than gradual failure, such as high-strength steel or the fuselage of aircraft.
Techniques to Improve Fatigue Strength
Improving fatigue strength is vital for enhancing the durability and service life of structures and components.
Several techniques can be employed to optimize fatigue strength.
Material Selection and Treatment
Choosing the right material is one of the first steps in enhancing fatigue strength.
Materials that exhibit high fracture toughness and resistance to crack growth are often preferred, such as titanium and certain grades of steel.
Incorporating surface treatments can also enhance fatigue resistance.
Processes such as shot peening introduce compressive stresses on the surface of the material, which helps to delay the initiation and growth of cracks.
Heat treatment techniques can also alter the microstructure of metals, enhancing their fatigue strength by redistributing internal stresses.
Design Optimization
The design phase plays a crucial role in mitigating metal fatigue.
Avoiding sharp corners, notches, and other elements that concentrate stress can significantly reduce fatigue risks.
If corners or notches are inevitable, gradual transitions and filleted edges can help distribute stress more evenly, minimizing potential crack initiation sites.
Designers often also include safety factors, ensuring that the component can withstand stresses well beyond the expected service loads.
Regular Maintenance and Inspection
Scheduled maintenance can play a pivotal role in detecting early signs of fatigue.
Routine inspections can identify small defects or cracks before they propagate to a critical size, allowing for repairs or replacements to be made proactively.
Non-destructive testing methods, like ultrasonic testing or radiography, can be used to detect subsurface cracks without causing any damage to the material.
Despite the best design and material choices, unexpected loading scenarios or environments can lead to unforeseen fatigue issues.
The Future of Fatigue Analysis
As technology progresses, the approach towards understanding and managing metal fatigue continues to evolve.
Advanced computational models, combined with real-time data from sensors embedded in material structures, allow for more precise fatigue life predictions.
Machine learning algorithms can analyze enormous datasets of operational stresses, learning to predict when and where fatigue might occur.
These technologies pave the way for smarter, safer, and more efficient designs, minimizing the risks associated with metal fatigue.
Understanding and managing metal fatigue is crucial for ensuring the safety and longevity of various structures and components.
With continuous advancements in technology and engineering practices, predicting fatigue life and enhancing fatigue strength remains a dynamic field, dedicated to safeguarding our infrastructure and innovations.
資料ダウンロード
QCD管理受発注クラウド「newji」は、受発注部門で必要なQCD管理全てを備えた、現場特化型兼クラウド型の今世紀最高の受発注管理システムとなります。
ユーザー登録
受発注業務の効率化だけでなく、システムを導入することで、コスト削減や製品・資材のステータス可視化のほか、属人化していた受発注情報の共有化による内部不正防止や統制にも役立ちます。
NEWJI DX
製造業に特化したデジタルトランスフォーメーション(DX)の実現を目指す請負開発型のコンサルティングサービスです。AI、iPaaS、および先端の技術を駆使して、製造プロセスの効率化、業務効率化、チームワーク強化、コスト削減、品質向上を実現します。このサービスは、製造業の課題を深く理解し、それに対する最適なデジタルソリューションを提供することで、企業が持続的な成長とイノベーションを達成できるようサポートします。
製造業ニュース解説
製造業、主に購買・調達部門にお勤めの方々に向けた情報を配信しております。
新任の方やベテランの方、管理職を対象とした幅広いコンテンツをご用意しております。
お問い合わせ
コストダウンが利益に直結する術だと理解していても、なかなか前に進めることができない状況。そんな時は、newjiのコストダウン自動化機能で大きく利益貢献しよう!
(β版非公開)