- お役立ち記事
- Basics of metal fatigue and its application to fatigue strength design
月間77,185名の
製造業ご担当者様が閲覧しています*
*2025年2月28日現在のGoogle Analyticsのデータより
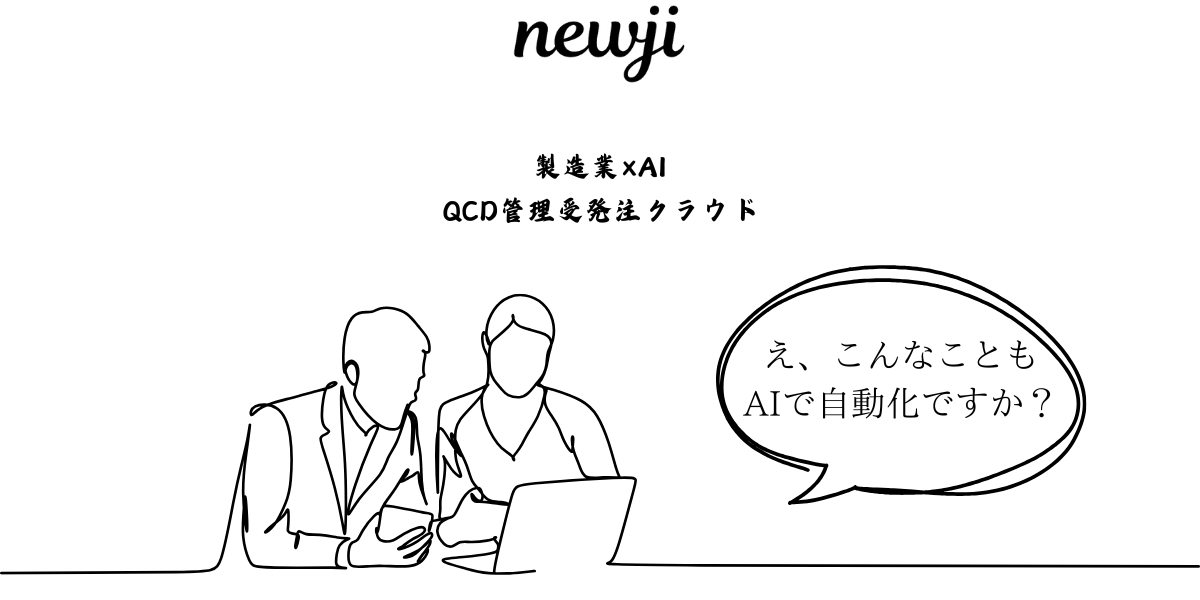
Basics of metal fatigue and its application to fatigue strength design
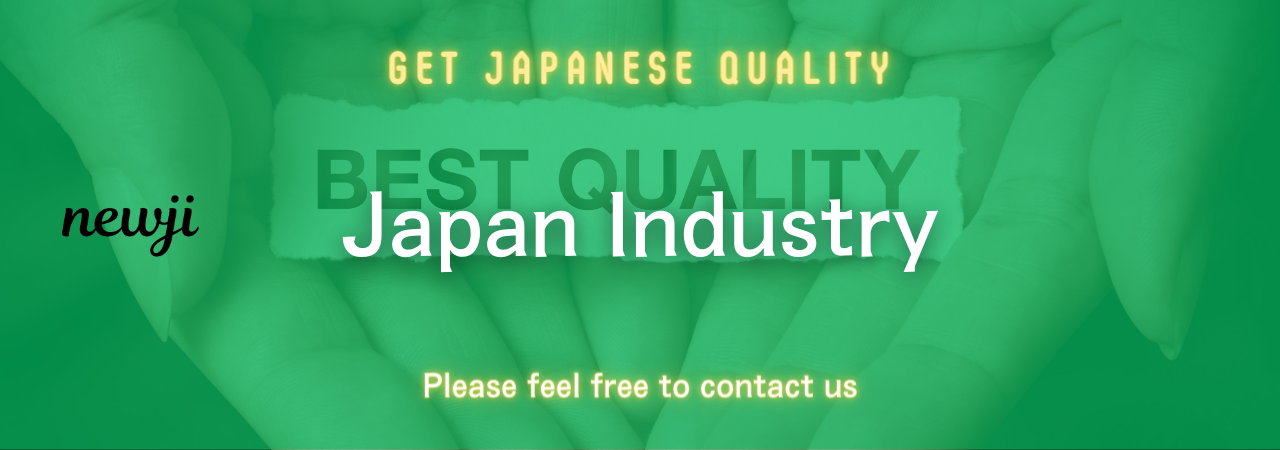
目次
Understanding Metal Fatigue
Metal fatigue is an important concept to grasp, especially for those involved in engineering and design.
It refers to the weakening of a metal due to repeated stress cycles.
Over time, even materials considered strong can develop cracks and eventually fail if subjected to continuous loading and unloading.
This phenomenon is critical in various fields, including aerospace, automotive, and civil engineering.
Understanding metal fatigue helps ensure that structures and machinery remain safe and functional over extended periods.
Causes of Metal Fatigue
The primary cause of metal fatigue is cyclic loading.
When a metal is exposed to repeated stress, microscopic cracks can form.
These cracks may start small but can grow over time with additional stress cycles.
There are a few factors that can influence fatigue in materials.
One significant factor is the magnitude of the load applied to the material.
Higher loads can increase the rate at which damage occurs.
Additionally, the frequency with which the load is applied plays a role.
Materials subjected to rapid cycles may experience fatigue faster than those with lower cycle rates.
Another factor to consider is the operating environment.
Corrosive environments, for example, can exacerbate fatigue by further weakening the material structure.
Temperatures, whether high or low, can also impact metal durability.
Stages of Metal Fatigue
Metal fatigue generally occurs in three stages.
The first stage is the initiation phase.
In this phase, small cracks start forming on the metal surface.
These cracks are often microscopic and might not be visible to the naked eye.
The second stage is the crack propagation phase.
Once a crack has formed, it begins to grow with each additional stress cycle.
The rate at which the crack grows can be influenced by factors such as load magnitude and environmental conditions.
The final stage is the failure stage.
Once the crack has reached a critical size, the metal can no longer withstand the stress and breaks suddenly.
This failure often occurs without any visible warning, making it a critical safety concern in engineering design.
Detecting and Monitoring Metal Fatigue
Engineers use a variety of methods to detect and monitor metal fatigue.
Nondestructive testing (NDT) techniques, such as ultrasound or radiography, are often employed to identify cracks before they lead to failure.
These techniques allow engineers to examine materials without causing further damage.
Regular maintenance and inspection regimes are also crucial in managing metal fatigue.
By scheduling routine checks, potential problems can be identified and addressed early, preventing catastrophic failures.
Designing for Fatigue Strength
To design against metal fatigue, engineers must consider fatigue strength, which is the resistance of a material to crack growth under cyclic loading.
A key aspect of fatigue strength design is understanding the S-N curve, also known as the Wöhler curve.
This curve plots the stress (S) against the number of cycles to failure (N).
Materials with a higher fatigue strength will show a higher number of cycles before reaching failure at a given stress level.
Choosing Suitable Materials
Selecting the right material is foundational in fatigue strength design.
Materials like steel and titanium are often favored for their high fatigue strength.
Engineers must consider not only the material’s inherent strength but also its behavior under specific environmental conditions.
Corrosion resistance and temperature stability are crucial factors in some applications.
Load Management
One of the primary objectives of fatigue strength design is to manage and mitigate loads effectively.
This can be achieved by distributing loads across multiple components or incorporating design features like fillets and rounded edges to minimize stress concentrations.
Avoiding sharp corners and sudden changes in cross-section can significantly reduce fatigue risk.
Surface Treatments
Applying surface treatments can enhance fatigue resistance.
Processes like shot peening or surface hardening introduce compressive stresses on the material surface, counteracting the tensile stresses that promote crack initiation.
Such treatments can extend the lifespan of components under cyclic loading.
Applications of Fatigue Strength Design
Understanding and applying fatigue strength design principles are vital in numerous industries.
In the automotive sector, components like suspension systems, engine parts, and chassis rely on fatigue design to withstand the demands of daily driving.
Designers must ensure that each part can endure the stresses of rough roads and high-speed maneuvers.
In aerospace, fatigue design is critical for the safety and reliability of aircraft.
Components like wings and fuselage structures are carefully designed to handle the stress cycles of each flight.
The aerospace industry also employs sophisticated testing methods to validate fatigue designs.
In civil engineering, structures like bridges and buildings must account for fatigue, especially in areas prone to seismic activity or heavy traffic.
Fatigue strength design ensures these structures remain safe and operational under varying loads and environmental conditions.
Conclusion
Metal fatigue is a critical concept in engineering, affecting everything from simple mechanical components to complex structural designs.
Understanding its principles and applying effective fatigue strength design can prevent failures and extend the lifespan of materials and structures.
By considering factors like material selection, load management, and environmental conditions, engineers can create safer and more durable designs.
This knowledge is not just theoretical but has real-world applications in various industries, making fatigue strength design an essential aspect of engineering practice.
資料ダウンロード
QCD管理受発注クラウド「newji」は、受発注部門で必要なQCD管理全てを備えた、現場特化型兼クラウド型の今世紀最高の受発注管理システムとなります。
ユーザー登録
受発注業務の効率化だけでなく、システムを導入することで、コスト削減や製品・資材のステータス可視化のほか、属人化していた受発注情報の共有化による内部不正防止や統制にも役立ちます。
NEWJI DX
製造業に特化したデジタルトランスフォーメーション(DX)の実現を目指す請負開発型のコンサルティングサービスです。AI、iPaaS、および先端の技術を駆使して、製造プロセスの効率化、業務効率化、チームワーク強化、コスト削減、品質向上を実現します。このサービスは、製造業の課題を深く理解し、それに対する最適なデジタルソリューションを提供することで、企業が持続的な成長とイノベーションを達成できるようサポートします。
製造業ニュース解説
製造業、主に購買・調達部門にお勤めの方々に向けた情報を配信しております。
新任の方やベテランの方、管理職を対象とした幅広いコンテンツをご用意しております。
お問い合わせ
コストダウンが利益に直結する術だと理解していても、なかなか前に進めることができない状況。そんな時は、newjiのコストダウン自動化機能で大きく利益貢献しよう!
(β版非公開)