- お役立ち記事
- Basics of metal fatigue and its application to strength design
月間76,176名の
製造業ご担当者様が閲覧しています*
*2025年3月31日現在のGoogle Analyticsのデータより
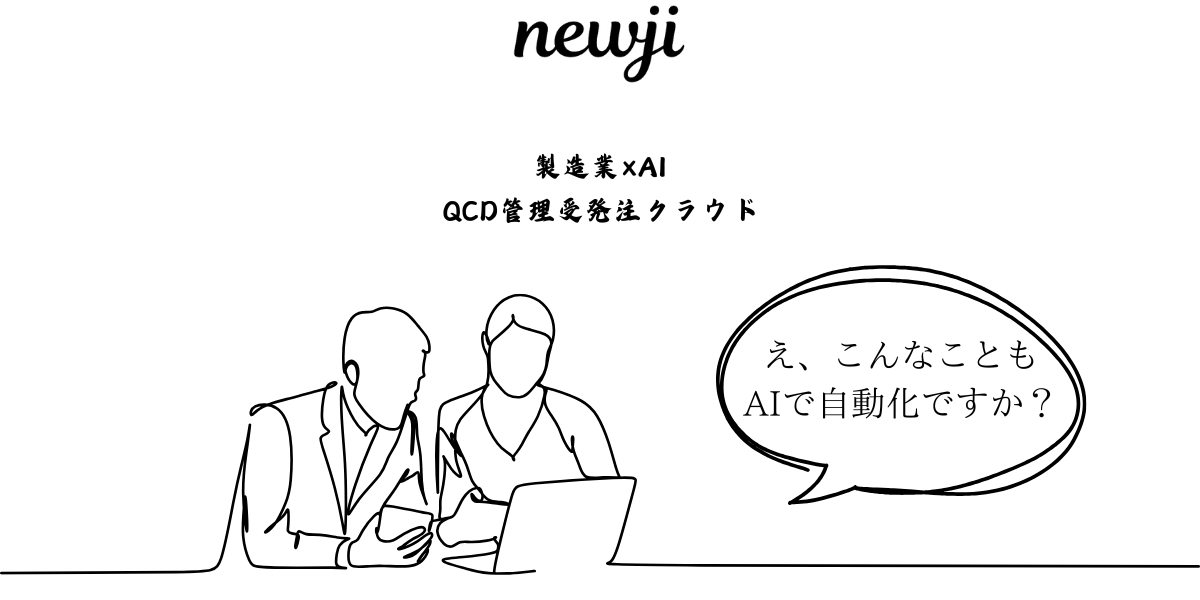
Basics of metal fatigue and its application to strength design
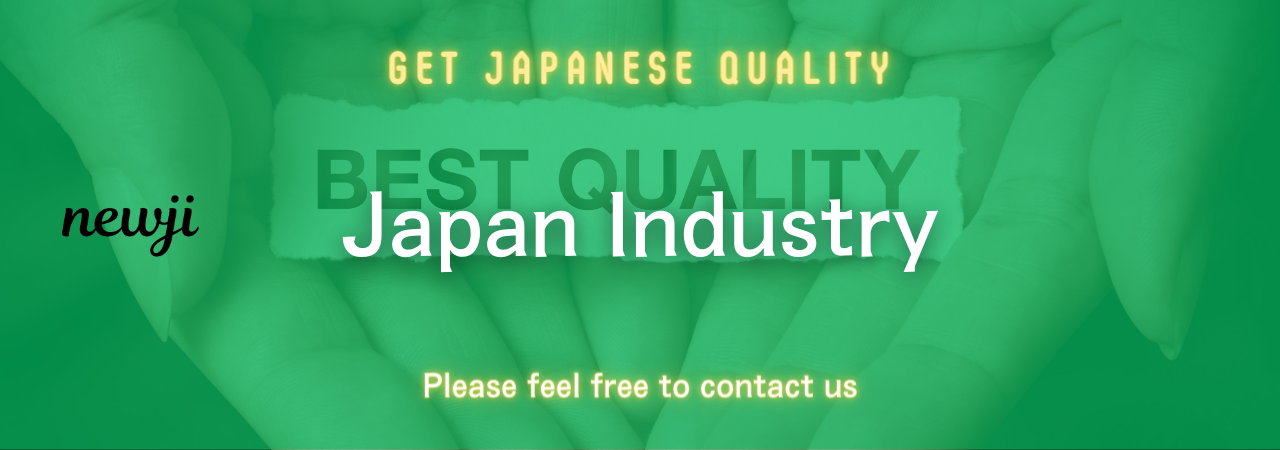
目次
Understanding Metal Fatigue
Metal fatigue is a critical concept in material science and engineering that refers to the weakening of a material caused by repeatedly applied loads.
This phenomenon can result in unexpected failures in metal structures, making it crucial for engineers to consider when designing components.
At its core, metal fatigue is the progressive and localized structural damage that occurs when a material is subjected to cyclic loading.
The material develops cracks when these loads exceed its endurance limit over numerous cycles.
Eventually, these cracks can grow over time and lead to catastrophic failure.
The Basics of Metal Fatigue
The process of metal fatigue can be broken down into three distinct stages: crack initiation, crack propagation, and sudden fracture.
In the first stage, tiny cracks begin to form at the surface of the material, often at sites of stress concentration such as notches, inclusions, or surface defects.
These initial cracks may be microscopic, but they are the starting point for further damage.
Crack propagation is the second stage, where these small cracks begin to grow incrementally with each cycle of stress.
The growth rate of a crack depends on several factors, including the material properties, the environment, and the magnitude of the applied stress.
It is during this stage that engineers can monitor and detect potential failures before they escalate.
The final stage is when the crack reaches a critical size, resulting in a sudden and often catastrophic fracture.
At this point, the material can no longer withstand the applied stress, leading to complete failure of the component.
To better understand and prevent metal fatigue, engineers rely on the S-N curve, which illustrates the relationship between cyclic stress (S) and the number of cycles to failure (N).
This curve helps in assessing how different materials respond to cyclic stresses over time.
Factors Affecting Metal Fatigue
Numerous factors can influence the fatigue life of a material.
Understanding these factors can help in designing components that are more resistant to fatigue.
Material Properties
The intrinsic properties of a material, such as its composition, microstructure, and surface finish, play a vital role in determining its fatigue strength.
For instance, materials with fine grain structures tend to have higher fatigue resistance.
Stress Concentration
Areas where stress is concentrated, such as sharp corners, holes, or notches, are more susceptible to crack initiation.
Designers often use techniques such as filleting or stress-relieving notches to reduce these concentrations.
Environmental Conditions
The environment in which a material operates can significantly impact its fatigue life.
Corrosive environments, high temperatures, and humidity can accelerate crack growth.
Protective coatings and regular maintenance can alleviate some of these effects.
Load and Stress Levels
The magnitude and frequency of applied loads are crucial in determining how quickly fatigue damage accumulates.
Loads closer to the yield strength of the material will result in faster crack growth.
Applications in Strength Design
Engineers apply the principles of metal fatigue to design structures and components that are safe, reliable, and long-lasting.
By accounting for fatigue in the design phase, they can prevent unexpected failures and enhance the performance of mechanical systems.
Designing for Fatigue
One of the primary objectives is to increase the fatigue life of a component.
This involves selecting materials with suitable properties, carefully designing geometries to minimize stress concentration, and applying surface treatments to enhance durability.
Predictive Modelling
Modern computational tools allow engineers to simulate the fatigue behavior of materials under various stresses.
These models help predict when a component is likely to fail and assist in planning maintenance schedules or redesigns.
Testing and Inspection
Non-destructive testing methods, such as ultrasonic and radiographic inspections, are employed to detect early signs of fatigue damage in critical components.
Regular inspections can prevent failure by identifying issues before they lead to catastrophic outcomes.
Conclusion
Understanding metal fatigue and its implications for strength design is essential in engineering.
By considering factors like material properties, stress concentrations, environmental conditions, and load levels, engineers can design safer and more reliable components.
The integration of advanced modelling techniques and regular inspection ensures early detection of potential failures.
By doing so, engineers minimize risks, enhancing the longevity and safety of metal structures and components in various applications.
資料ダウンロード
QCD管理受発注クラウド「newji」は、受発注部門で必要なQCD管理全てを備えた、現場特化型兼クラウド型の今世紀最高の受発注管理システムとなります。
ユーザー登録
受発注業務の効率化だけでなく、システムを導入することで、コスト削減や製品・資材のステータス可視化のほか、属人化していた受発注情報の共有化による内部不正防止や統制にも役立ちます。
NEWJI DX
製造業に特化したデジタルトランスフォーメーション(DX)の実現を目指す請負開発型のコンサルティングサービスです。AI、iPaaS、および先端の技術を駆使して、製造プロセスの効率化、業務効率化、チームワーク強化、コスト削減、品質向上を実現します。このサービスは、製造業の課題を深く理解し、それに対する最適なデジタルソリューションを提供することで、企業が持続的な成長とイノベーションを達成できるようサポートします。
製造業ニュース解説
製造業、主に購買・調達部門にお勤めの方々に向けた情報を配信しております。
新任の方やベテランの方、管理職を対象とした幅広いコンテンツをご用意しております。
お問い合わせ
コストダウンが利益に直結する術だと理解していても、なかなか前に進めることができない状況。そんな時は、newjiのコストダウン自動化機能で大きく利益貢献しよう!
(β版非公開)