- お役立ち記事
- Basics of metal fatigue, fatigue life estimation method, and application to improving fatigue strength
Basics of metal fatigue, fatigue life estimation method, and application to improving fatigue strength
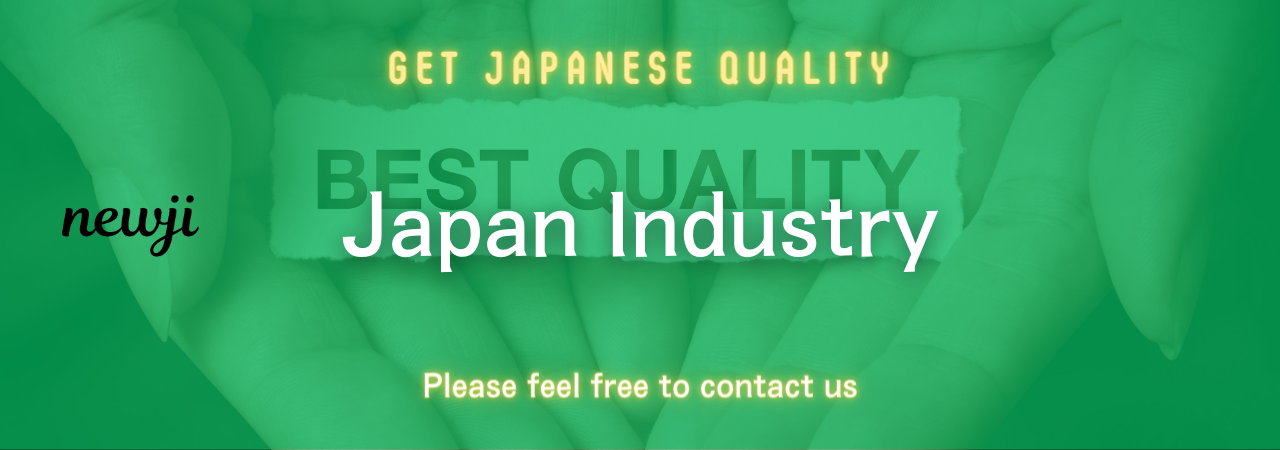
目次
Understanding Metal Fatigue
Metal fatigue is a phenomenon that affects various materials, particularly metals, where the structural integrity of a material deteriorates due to repetitive loading and unloading cycles.
This degradation occurs even when the applied stress levels are well below the material’s ultimate tensile strength.
Metal fatigue was first recognized during the industrial revolution when engineers began to notice unexpected failures in metals used in machinery and infrastructure.
The Science Behind Metal Fatigue
To comprehend metal fatigue, it is essential to understand the microscopic changes that occur within a material.
Each phase of loading adds to the tiny cracks that develop in the metal structure.
Initially, these micro-cracks are minuscule and cause no immediate danger to the structure’s integrity.
Over time and through repeated cycles, these micro-cracks can coalesce, leading to larger cracks that propagate through the material.
Eventually, this can result in a catastrophic failure, sometimes without prior visible warning, making it particularly dangerous in structural applications.
Metal fatigue can be influenced by several factors, including environmental conditions, material properties, surface finish, and the nature of the applied cyclic loading.
Moreover, fatigue failure often occurs at stress concentrations, such as notches or sharp corners, which makes it crucial to design components to minimize such stress risers.
Estimating Fatigue Life
The estimation of the fatigue life of a material or component is a critical aspect of engineering.
There are different approaches and methods to predict when a material might fail under cyclic loading.
One of the most common methods is known as the S-N curve (stress-number of cycles curve), which provides a graphical representation of the relationship between the applied stress and the number of cycles required to cause failure.
S-N Curve
The S-N curve is obtained by subjecting samples of material to different stress levels and recording the number of cycles they withstand before failure.
The resulting graph plots stress amplitude against the number of cycles to failure.
This helps engineers determine the fatigue limit of a metal – the stress level below which theoretically, the metal can endure an infinite number of cycles without failing.
Although this method is beneficial, it doesn’t account for all real-life variables, prompting the development of other approaches, such as the crack growth rate method.
Crack Growth Rate Method
This approach considers how pre-existing cracks in a material grow under cyclic loads.
It is more detailed than the S-N curve and uses principles of fracture mechanics to calculate the rate of crack propagation.
The crack growth rate can be predicted using Paris’ Law, which relates the rate of crack growth per cycle to the range of stress intensity factor during loading cycles.
This method enables engineers to predict when a crack might propagate to a critical size, leading to failure, and is particularly useful in the inspection and maintenance of materials where fatigue cracks are known to exist.
Improving Fatigue Strength
Enhancing the fatigue strength of a material is paramount for increasing its lifespan and ensuring safety.
There are several strategies engineers employ to achieve this, focusing on both material selection and design innovations.
Material Selection and Treatment
Choosing the appropriate material is the first step toward improving fatigue resistance.
High-strength alloys and composites often offer better fatigue performance.
Surface treatments such as shot peening and case hardening can enhance resistance by introducing compressive residual stresses on the surface, which help to counteract the tensile stresses induced during loading.
Additionally, thermal treatments can alter the microstructure of a material, improving its toughness and resistance to crack initiation and growth.
Design Considerations
The design phase is crucial in mitigating fatigue.
One effective approach is the reduction or elimination of stress concentrators such as sharp corners or abrupt changes in cross-section.
Designing components with smooth transitions can significantly reduce localized stresses.
Also, implementing redundant systems and using conservative safety factors in design criteria can avert potential fatigue failures.
Regular inspection and maintenance are further integral to ensuring that fatigue does not lead to sudden catastrophic failures.
Applications in Engineering
Understanding and managing metal fatigue is crucial in numerous engineering applications, ranging from aerospace and automotive industries to civil engineering and consumer electronics.
In the aerospace industry, managing metal fatigue is vital due to safety implications, with extensive testing and monitoring starting at the design phase, extending to regular maintenance schedules throughout an aircraft’s operational life.
In civil engineering, infrastructures like bridges and towers are constantly subjected to cyclic loads such as wind and traffic.
Accurate fatigue life estimations ensure these structures can support ongoing stresses over decades.
Similarly, in automotive engineering, metal fatigue knowledge ensures the longevity and reliability of vehicle components that experience repetitive loads, such as suspension systems and engine parts.
Conclusion
Understanding metal fatigue, its underlying mechanisms, and its prediction methods is essential in modern engineering.
Both the S-N curve and the crack growth rate method are valuable tools for estimating fatigue life.
By selecting appropriate materials, treating surfaces accordingly, and considering design modifications, engineers can significantly improve fatigue resistance, thereby enhancing the durability and safety of structures and components.
Continued research and technological advancements are necessary to further refine these methods and adapt them to increasingly complex engineering challenges.
資料ダウンロード
QCD調達購買管理クラウド「newji」は、調達購買部門で必要なQCD管理全てを備えた、現場特化型兼クラウド型の今世紀最高の購買管理システムとなります。
ユーザー登録
調達購買業務の効率化だけでなく、システムを導入することで、コスト削減や製品・資材のステータス可視化のほか、属人化していた購買情報の共有化による内部不正防止や統制にも役立ちます。
NEWJI DX
製造業に特化したデジタルトランスフォーメーション(DX)の実現を目指す請負開発型のコンサルティングサービスです。AI、iPaaS、および先端の技術を駆使して、製造プロセスの効率化、業務効率化、チームワーク強化、コスト削減、品質向上を実現します。このサービスは、製造業の課題を深く理解し、それに対する最適なデジタルソリューションを提供することで、企業が持続的な成長とイノベーションを達成できるようサポートします。
オンライン講座
製造業、主に購買・調達部門にお勤めの方々に向けた情報を配信しております。
新任の方やベテランの方、管理職を対象とした幅広いコンテンツをご用意しております。
お問い合わせ
コストダウンが利益に直結する術だと理解していても、なかなか前に進めることができない状況。そんな時は、newjiのコストダウン自動化機能で大きく利益貢献しよう!
(Β版非公開)