- お役立ち記事
- Basics of metal fracture surface analysis (fractography) and its application to estimating fracture mechanisms and causes of damage
Basics of metal fracture surface analysis (fractography) and its application to estimating fracture mechanisms and causes of damage
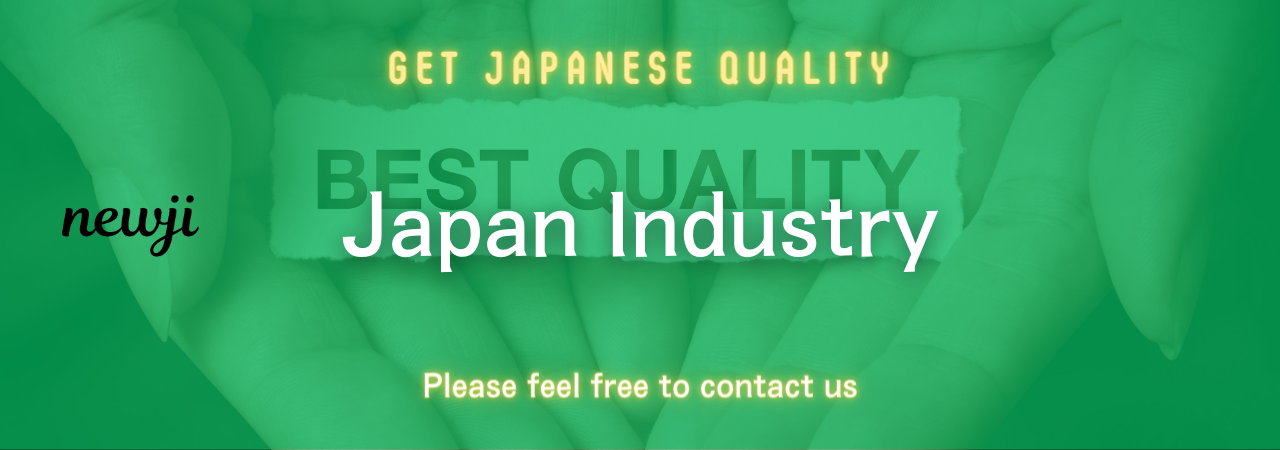
目次
Understanding Metal Fracture Surface Analysis
Fractography is the study of fracture surfaces of materials, primarily metals, to understand the causes and mechanisms of failure.
This technique plays a crucial role in materials science and engineering, helping experts diagnose why a component failed and how future failures can be prevented.
In simple terms, fráctography tells the story of why a metal broke.
What is a Fracture Surface?
When a metal breaks, the surface where the break occurs is known as the fracture surface.
It’s like reading a fingerprint—it holds unique clues about how and why the metal failed.
Fracture surfaces can reveal information about the load conditions, the environment, and the intrinsic properties of the material that led to the failure.
Tools and Techniques for Fractography
Fractography relies on various tools and techniques to analyze the fracture surface.
Visual Inspection
The first step in fractography is often a simple visual inspection.
With the naked eye or a magnifying glass, experts look for obvious patterns or irregularities on the fracture surface.
This initial view can help identify cracks, corrosion, or other tell-tale signs of the material’s journey to failure.
Optical Microscopy
For a more detailed inspection, optical microscopy is employed.
An optical microscope allows scientists to magnify the fracture surface, revealing features like striations and micro-cracks.
These features can help determine whether the fracture was a slow, progressive failure or a sudden, catastrophic break.
Scanning Electron Microscopy (SEM)
SEM provides even greater detail than optical microscopy.
Utilizing electrons to illuminate the specimen, SEM produces high-resolution images that can magnify the surface by thousands of times.
SEM is invaluable in identifying fracture modes, such as ductile or brittle fracture, which are critical clues to understanding the failure process.
X-ray Diffraction (XRD)
XRD is used to identify the crystalline structure of materials.
By analyzing diffraction patterns, this technique helps determine the material’s phase composition and any changes that might have contributed to the failure.
Energy Dispersive X-Ray Spectroscopy (EDX)
Often used in tandem with SEM, EDX analyzes the elemental composition of the fracture surface.
It can detect impurities or alloying elements that may have influenced the material’s performance.
Common Types of Fracture
Understanding the types of fractures is key to interpreting the fracture surface.
Ductile Fracture
A ductile fracture is characterized by a significant amount of plastic deformation before failure.
The fracture surface typically reveals dimple patterns, indicating the material stretched before breaking.
Ductile fractures generally indicate that the material was subjected to a steady load over time.
Brittle Fracture
In contrast, a brittle fracture occurs with little to no plastic deformation.
This type of failure usually results in a smooth, flat fracture surface.
Brittle fractures are often caused by sharp impacts or stress concentrations and reveal less about the loading conditions.
Fatigue Fracture
Fatigue fractures result from repeated loading and unloading cycles, even if those loads are below the material’s ultimate strength.
The fracture surface exhibits striations or ripples, marking the progressive crack growth over time.
Fatigue is a common failure mode in machinery and structural components subject to fluctuating stresses.
Stress Corrosion Cracking (SCC)
SCC is a failure mechanism driven by the combined effect of tensile stress and a corrosive environment.
The fracture surface may display branched cracks and corrosion products, indicating chemical interaction played a significant role in the failure.
Applications of Fractography
Fractography has wide-ranging applications across industries.
Aerospace
In the aerospace industry, understanding why a component failed is crucial for safety.
Fractography helps identify material defects or design issues in aircraft parts, preventing potential accidents.
Automotive
Analyzing fracture surfaces in the automotive field facilitates the improvement of vehicle designs and the development of more durable materials, contributing to safer and more reliable vehicles.
Construction
In construction, fractography aids in determining the causes of structural failures, influencing building codes and material selection to prevent similar occurrences.
Manufacturing
Manufacturers use fractography to troubleshoot machine part failures, leading to improved product quality and reliability.
Estimating Fracture Mechanisms and Causes of Damage
The ultimate goal of fractography is to estimate the mechanisms and causes of metal failure.
By understanding the fracture mode and examining the history of the fracture surface, experts can infer critical details such as the loading history, material flaws, or environmental conditions that led to the failure.
Failure Analysis
Failure analysis is a systematic investigation to determine why a component failed.
Fractography is a vital part of this process, providing visual and analytical data necessary for thorough evaluation.
Preventive Measures
With insights gained from fractography, engineers can design better materials and components, taking preemptive measures to avoid future failures.
This includes altering material specifications, redesigning parts, or changing manufacturing processes.
In summary, the basics of metal fracture surface analysis or fractography offer a window into the life and untimely end of a material.
Through detailed examination and advanced techniques, this field aids in understanding failure mechanisms and preventing future occurrences.
By learning from fractures, industries can create safer, more dependable products and structures.
資料ダウンロード
QCD調達購買管理クラウド「newji」は、調達購買部門で必要なQCD管理全てを備えた、現場特化型兼クラウド型の今世紀最高の購買管理システムとなります。
ユーザー登録
調達購買業務の効率化だけでなく、システムを導入することで、コスト削減や製品・資材のステータス可視化のほか、属人化していた購買情報の共有化による内部不正防止や統制にも役立ちます。
NEWJI DX
製造業に特化したデジタルトランスフォーメーション(DX)の実現を目指す請負開発型のコンサルティングサービスです。AI、iPaaS、および先端の技術を駆使して、製造プロセスの効率化、業務効率化、チームワーク強化、コスト削減、品質向上を実現します。このサービスは、製造業の課題を深く理解し、それに対する最適なデジタルソリューションを提供することで、企業が持続的な成長とイノベーションを達成できるようサポートします。
オンライン講座
製造業、主に購買・調達部門にお勤めの方々に向けた情報を配信しております。
新任の方やベテランの方、管理職を対象とした幅広いコンテンツをご用意しております。
お問い合わせ
コストダウンが利益に直結する術だと理解していても、なかなか前に進めることができない状況。そんな時は、newjiのコストダウン自動化機能で大きく利益貢献しよう!
(Β版非公開)