- お役立ち記事
- Basics of micro bonding technology/mounting technology and points of fracture surface analysis/reliability evaluation
月間76,176名の
製造業ご担当者様が閲覧しています*
*2025年3月31日現在のGoogle Analyticsのデータより
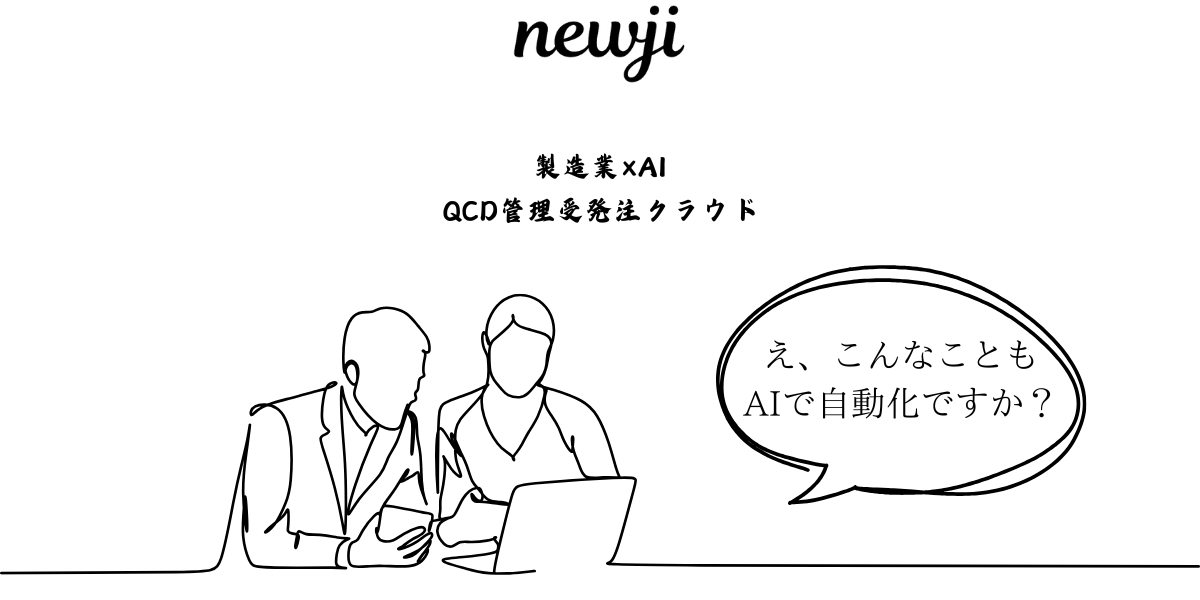
Basics of micro bonding technology/mounting technology and points of fracture surface analysis/reliability evaluation
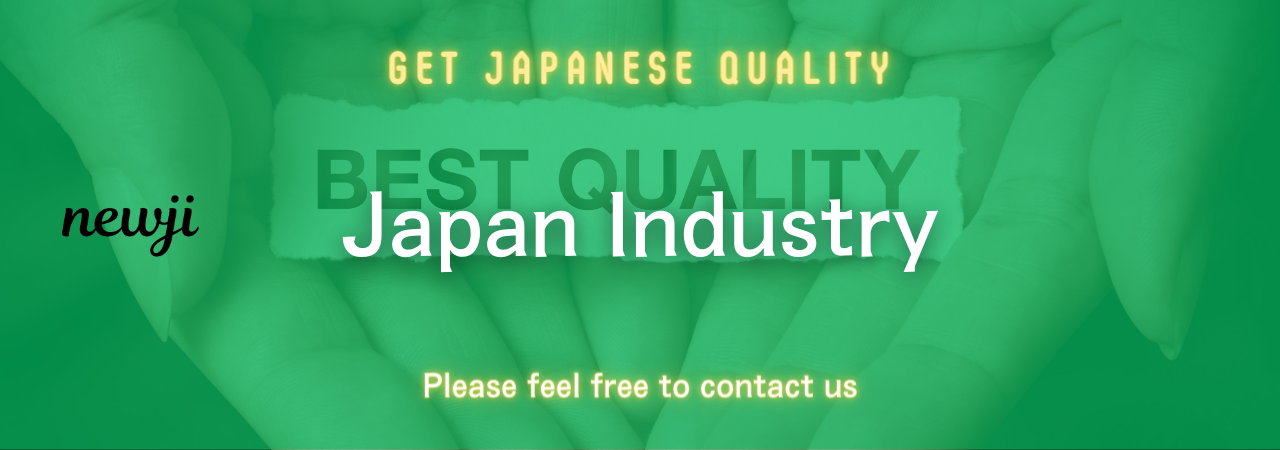
目次
Introduction to Micro Bonding Technology
Micro bonding technology plays a crucial role in today’s advanced electronics manufacturing processes.
This technology involves the joining of small components at a microscopic scale, allowing for high-precision connectivity essential for complex electronic devices.
With the growing demand for smaller, faster, and more reliable devices, understanding micro bonding technology is essential for anyone involved in the tech industry.
What is Micro Bonding?
Micro bonding refers to the precise connecting of tiny components like circuits, wires, and chips in electronic devices.
Techniques in micro bonding can vary, but they all aim to ensure robust electrical and mechanical connections.
Typical methods include ultrasonic bonding, thermosonic bonding, and laser bonding, each chosen based on application needs and material properties.
Mounting Technology: The Backbone of Electronics
Mounting technology is another critical aspect of modern electronics, involving the placement and attachment of components onto a substrate or circuit board.
This process is vital for the functionality and efficiency of devices, ensuring that all parts work in harmony.
Mounting technology can be categorized into two main types: surface-mount technology (SMT) and through-hole technology (THT).
Surface-Mount Technology (SMT)
Surface-mount technology involves placing components directly onto the surface of printed circuit boards (PCBs).
SMT is essential for modern electronics due to its efficiency and space-saving capabilities.
It allows for smaller, lighter devices while maintaining high performance and reliability.
Through-Hole Technology (THT)
Through-hole technology, on the other hand, requires inserting component leads through holes in the PCB.
While less space-efficient than SMT, THT provides stronger mechanical bonds and is often used in applications where durability is a priority.
Fracture Surface Analysis
Despite the precision in micro bonding and mounting technology, failures can occur.
Fracture surface analysis becomes essential to understand the causes of these failures and to enhance the reliability of the components.
Understanding Fracture Surfaces
Fracture surface analysis examines the broken surfaces of components to determine the mode and cause of failure.
By studying the patterns and features of fractures, engineers can identify manufacturing defects, material weaknesses, or improper bonding techniques.
Techniques in Fracture Surface Analysis
Several techniques are used in fracture surface analysis, including:
– Scanning Electron Microscopy (SEM): Provides detailed images of fracture surfaces at a microscopic level.
– Energy Dispersive X-ray Spectroscopy (EDX): Works in conjunction with SEM to analyze the composition of materials.
– Optical Microscopy: Offers a less detailed but faster analysis compared to SEM.
These techniques help in pinpointing the exact causes of failure, which is critical for preventing future issues and enhancing product reliability.
Reliability Evaluation in Micro Bonding
Reliability is a core concern in electronics, as even minor failures can lead to significant consequences.
Evaluating the reliability of micro bonding processes ensures that devices meet high standards of quality and performance.
Factors Affecting Reliability
Several factors can impact the reliability of micro bonded joints, including:
– Material properties: Different materials have varying strengths, conductivities, and thermal expansion characteristics.
– Bonding conditions: Temperature, pressure, and time during bonding all influence the quality of the joint.
– Environmental factors: Conditions like humidity, temperature cycles, and mechanical stress can affect long-term performance.
Testing and Evaluation Methods
To assess reliability, various testing methods are employed, such as:
– Environmental testing: Simulates real-world conditions to assess how components handle stress and environmental factors.
– Mechanical testing: Evaluates the physical strength and durability of the bonds.
– Electrical testing: Checks the electrical performance and integrity of connections to ensure proper functionality.
Conclusion
Micro bonding and mounting technologies are fundamental to the production of reliable, efficient electronic devices.
Understanding these techniques, along with thorough fracture surface analysis and reliability evaluation, is crucial for anyone involved in the electronics field.
As technology continues to evolve, advancing these processes will be pivotal in meeting the demands of future innovations.
資料ダウンロード
QCD管理受発注クラウド「newji」は、受発注部門で必要なQCD管理全てを備えた、現場特化型兼クラウド型の今世紀最高の受発注管理システムとなります。
ユーザー登録
受発注業務の効率化だけでなく、システムを導入することで、コスト削減や製品・資材のステータス可視化のほか、属人化していた受発注情報の共有化による内部不正防止や統制にも役立ちます。
NEWJI DX
製造業に特化したデジタルトランスフォーメーション(DX)の実現を目指す請負開発型のコンサルティングサービスです。AI、iPaaS、および先端の技術を駆使して、製造プロセスの効率化、業務効率化、チームワーク強化、コスト削減、品質向上を実現します。このサービスは、製造業の課題を深く理解し、それに対する最適なデジタルソリューションを提供することで、企業が持続的な成長とイノベーションを達成できるようサポートします。
製造業ニュース解説
製造業、主に購買・調達部門にお勤めの方々に向けた情報を配信しております。
新任の方やベテランの方、管理職を対象とした幅広いコンテンツをご用意しております。
お問い合わせ
コストダウンが利益に直結する術だと理解していても、なかなか前に進めることができない状況。そんな時は、newjiのコストダウン自動化機能で大きく利益貢献しよう!
(β版非公開)