- お役立ち記事
- Basics of modal analysis and vibration countermeasures that new employees in the design department of the precision machinery industry should learn
Basics of modal analysis and vibration countermeasures that new employees in the design department of the precision machinery industry should learn
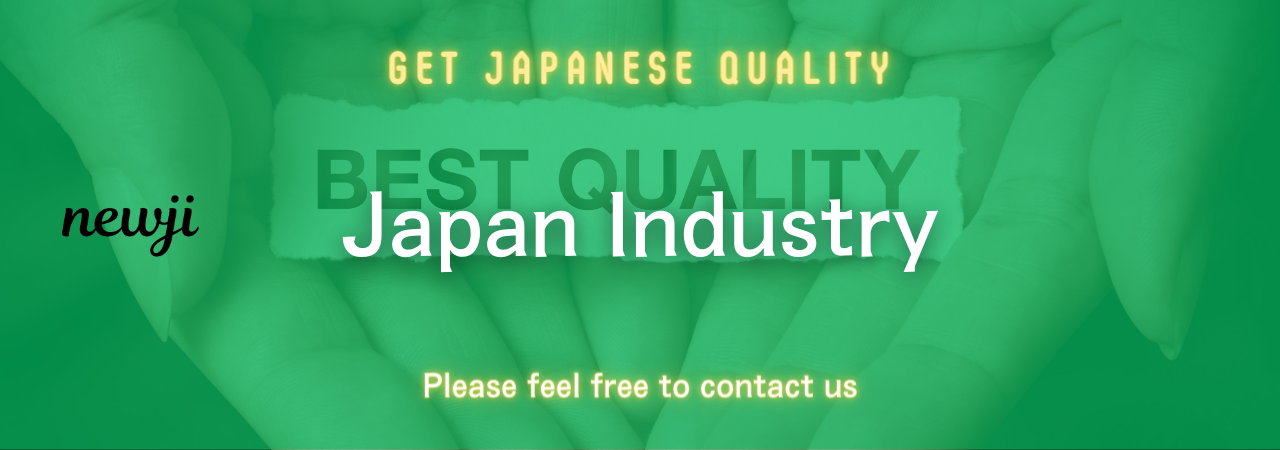
目次
Understanding Modal Analysis
Modal analysis is a technique used to study and understand the dynamic properties of structures.
In the precision machinery industry, where accurate and stable performance is crucial, knowing how these structures behave under different conditions is essential.
Modal analysis helps engineers identify natural frequencies, mode shapes, and damping factors of a system.
These parameters provide insights into how the structure will respond to vibrations and other dynamic forces.
For new employees in the design department, gaining a foundational understanding of modal analysis is crucial.
This knowledge allows them to work on projects with a focus on reducing unwanted vibrations and enhancing product performance.
Modal analysis involves both analytical and experimental methods.
Both approaches contribute to understanding a system’s behavior.
Natural Frequencies and Mode Shapes
A core concept in modal analysis is the natural frequency of a system.
This is the frequency at which a system tends to vibrate when disturbed.
Understanding natural frequencies is crucial because if a machine or structure operates at a frequency close to its natural frequency, it may experience resonance.
Resonance can cause excessive vibrations, leading to wear and tear or even failure.
Thus, identifying these frequencies helps engineers design systems that avoid operational failure.
Mode shapes describe the deformation or pattern of motion a system undergoes at a particular natural frequency.
By understanding mode shapes, engineers can pinpoint areas susceptible to high stress or deformation and make necessary design alterations.
The Role of Damping
Damping is another important factor in modal analysis.
It refers to the mechanism through which a system dissipates energy, thereby reducing vibrations.
Different materials and designs possess varying levels of damping.
Understanding damping helps engineers improve a structure’s ability to handle vibrations without compromising stability.
Choosing materials with appropriate damping properties and incorporating dampers into a design can help mitigate vibration issues.
The goal is to enhance durability and ensure that the machine performs optimally under various conditions.
Experimental Modal Analysis Techniques
When conducting modal analysis, engineers often use experimental techniques to obtain accurate data about a system’s dynamic behavior.
The process usually involves exciting the structure with a known force and measuring its response using sensors.
The data collected provides insights into natural frequencies, mode shapes, and damping ratios.
One common method used in experimental modal analysis is the Impact Hammer Test, where a known force is applied using a hammer with a sensor attached to measure the force.
Vibration responses are captured by accelerometers placed around the structure.
Another technique is the Shaker Test, which involves using an electromechanical shaker to provide continuous, controlled excitation.
Applications in Precision Machinery
In the precision machinery industry, modal analysis plays a key role in ensuring products meet strict performance standards.
Whether designing high-speed machining equipment or delicate measurement tools, engineers need to consider dynamic behavior.
By understanding modal properties, engineers can address potential vibration issues during the design phase.
This proactive approach helps in minimizing design changes during later stages, saving both time and resources.
Reducing Unwanted Vibrations
Vibration countermeasures are an essential aspect of design in the precision machinery industry.
Taking measures to reduce vibrations can result in improved accuracy, longevity, and user satisfaction.
One effective strategy is to design structures with appropriate stiffness.
Increased stiffness can help shift natural frequencies away from operational ranges, reducing the impact of resonant vibrations.
Using composite materials that absorb and dissipate energy better than traditional materials is another option.
Additionally, incorporating isolation mounts, dampers, or absorbers can help manage and mitigate vibrations.
Several tools and equipment are available for conducting modal analysis. Common tools include: 1. **Spectrum Analyzers**: These devices capture and analyze vibration data, helping engineers identify natural frequencies and mode shapes. 2. **Vibration Sensors**: These include accelerometers and velocity sensors that measure how a structure reacts to excitations. 3. **Computational Software**: Software like finite element analysis (FEA) tools aid in simulating the dynamic behavior of structures, allowing engineers to predict vibration issues early on. As technologies evolve, staying updated with the latest developments in modal analysis is vital for professionals in the precision machinery industry. Engaging with the broader engineering community can also be beneficial. Understanding the basics of modal analysis and vibration countermeasures is crucial for new employees in the design department of the precision machinery industry.
Understanding the capabilities and limitations of these tools is crucial for new employees in the design department.Importance of Continuous Learning
Workshops, seminars, and online courses can provide additional learning opportunities.
Networking with colleagues and attending industry conferences provide access to the latest research findings and best practices.Conclusion
By mastering these concepts, they can contribute to creating high-quality products with reduced risk of failure due to vibrations.
A focus on continuous learning will help them stay abreast of emerging techniques and tools, ensuring their skills remain relevant as industry demands evolve.
資料ダウンロード
QCD調達購買管理クラウド「newji」は、調達購買部門で必要なQCD管理全てを備えた、現場特化型兼クラウド型の今世紀最高の購買管理システムとなります。
ユーザー登録
調達購買業務の効率化だけでなく、システムを導入することで、コスト削減や製品・資材のステータス可視化のほか、属人化していた購買情報の共有化による内部不正防止や統制にも役立ちます。
NEWJI DX
製造業に特化したデジタルトランスフォーメーション(DX)の実現を目指す請負開発型のコンサルティングサービスです。AI、iPaaS、および先端の技術を駆使して、製造プロセスの効率化、業務効率化、チームワーク強化、コスト削減、品質向上を実現します。このサービスは、製造業の課題を深く理解し、それに対する最適なデジタルソリューションを提供することで、企業が持続的な成長とイノベーションを達成できるようサポートします。
オンライン講座
製造業、主に購買・調達部門にお勤めの方々に向けた情報を配信しております。
新任の方やベテランの方、管理職を対象とした幅広いコンテンツをご用意しております。
お問い合わせ
コストダウンが利益に直結する術だと理解していても、なかなか前に進めることができない状況。そんな時は、newjiのコストダウン自動化機能で大きく利益貢献しよう!
(Β版非公開)