- お役立ち記事
- Basics of mold design
月間76,176名の
製造業ご担当者様が閲覧しています*
*2025年3月31日現在のGoogle Analyticsのデータより
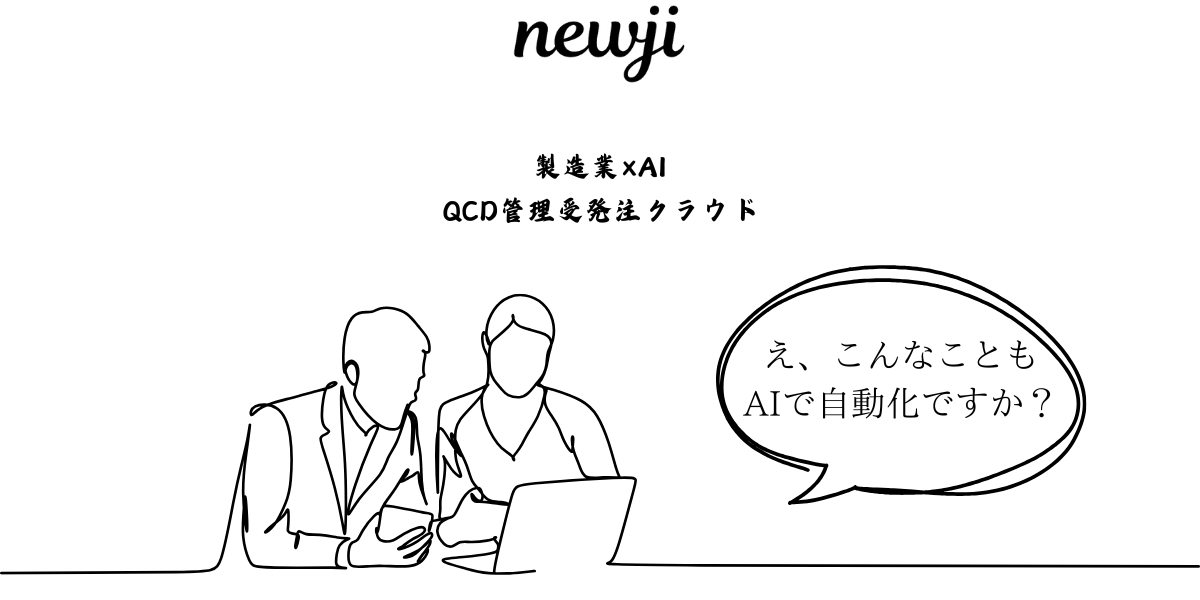
Basics of mold design
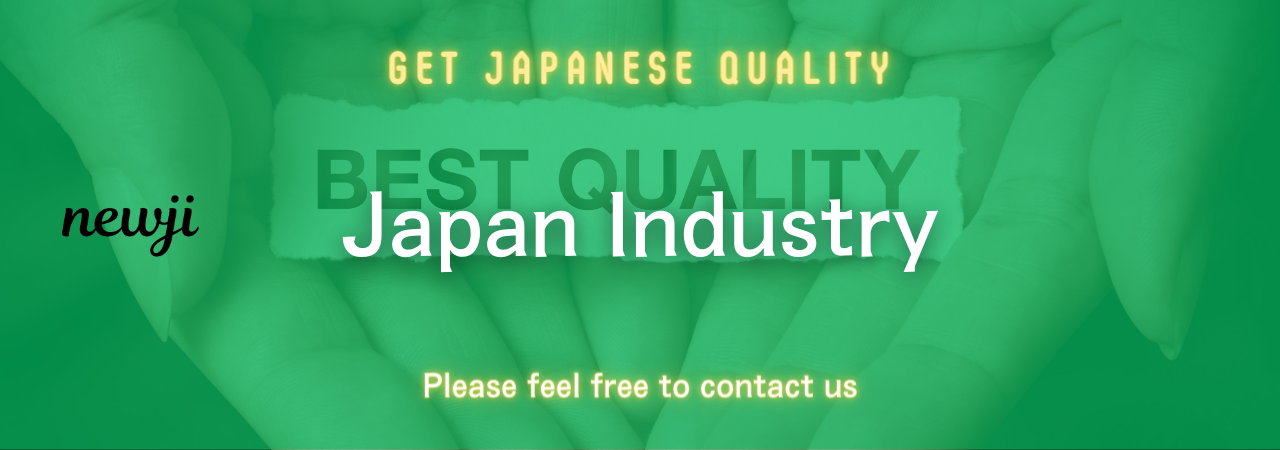
目次
Introduction to Mold Design
Mold design is a critical aspect of manufacturing that determines the efficiency, quality, and cost-effectiveness of producing various components.
Understanding the basics of mold design is essential for anyone involved in manufacturing, engineering, or product development.
In this guide, we’ll explore the fundamental concepts, processes, and considerations that go into successful mold design.
What is Mold Design?
Mold design refers to the process of designing molds, which are used to shape molten materials into specific forms.
These molds are integral in the production of plastic, metal, and other materials that need to be precisely shaped for various applications.
The primary goal of mold design is to ensure that the final product is of high quality, meets the required specifications, and is cost-effective to produce.
The Importance of Mold Design
Mold design is crucial for several reasons.
Firstly, it directly impacts the quality of the finished product.
A well-designed mold ensures that the product is free from defects and meets the required tolerances.
Secondly, efficient mold design can significantly reduce production costs by minimizing waste, speeding up the manufacturing process, and extending the life of the mold.
Finally, it can improve the overall efficiency of the production process by reducing the need for rework and corrections.
Key Components of Mold Design
Mold design involves several key components that must be carefully considered to ensure success.
Mold Material
The choice of mold material is critical as it affects the durability and performance of the mold.
Common materials include steel and aluminum, each with its advantages.
Steel molds are highly durable and can withstand high temperatures, making them ideal for high-volume production.
Aluminum molds, on the other hand, are lighter and more affordable, suitable for low to medium-volume production.
Mold Structure
The structure of the mold includes the mold base, cavity, and core, among other components.
The cavity is the part of the mold that shapes the exterior of the product, while the core forms the interior features.
The mold base holds everything together and provides support during the molding process.
Designing these components appropriately is crucial to ensure the mold functions correctly.
The Mold Design Process
The mold design process typically involves several steps, from initial concept to final production.
Conceptual Design
The first step in mold design is conceptualizing the product and determining the requirements for the mold.
This includes understanding the product’s dimensions, tolerances, and material properties.
At this stage, engineers create preliminary sketches and models to visualize the mold’s design.
CAD Modeling
Once the initial concept is created, designers use Computer-Aided Design (CAD) software to create detailed 3D models of the mold.
These models help in visualizing the mold’s components and identifying potential issues before physical production begins.
CAD allows for precise measurements and modifications, reducing the likelihood of errors.
Simulation and Analysis
Simulation tools are utilized to analyze how the mold will perform during the molding process.
This includes evaluating factors like material flow, cooling rates, and potential defects.
Simulation helps in making necessary adjustments to the design before fabrication, saving time and resources.
Prototype Development
After refining the design, a prototype of the mold is developed.
This prototype is tested to ensure it functions as intended and produces parts that meet the required specifications.
Any necessary changes are made during this stage to perfect the mold design.
Final Production
Once the prototype is approved, the final version of the mold is produced.
This mold will be used in the manufacturing process to create the final product.
Considerations in Mold Design
Several factors must be considered in mold design to optimize performance and efficiency.
Material Shrinkage
Different materials shrink at different rates as they cool, impacting the final dimensions of the product.
Designers must account for this shrinkage to ensure the product meets the required specifications.
Cooling Time
The cooling time of the material impacts production speed and quality.
Effective mold design includes planning for efficient cooling to optimize the production process and ensure consistent quality.
Ejection Mechanism
The ejection mechanism is responsible for removing the part from the mold without damaging it.
Designers must ensure that the mechanism is efficient and gentle enough to maintain product integrity.
Conclusion
Understanding the basics of mold design is essential for anyone involved in the manufacturing process.
From choosing the right materials and structures to simulating and testing the mold, each step plays a vital role in ensuring successful production.
By focusing on these fundamentals, manufacturers can produce high-quality products efficiently and cost-effectively.
資料ダウンロード
QCD管理受発注クラウド「newji」は、受発注部門で必要なQCD管理全てを備えた、現場特化型兼クラウド型の今世紀最高の受発注管理システムとなります。
ユーザー登録
受発注業務の効率化だけでなく、システムを導入することで、コスト削減や製品・資材のステータス可視化のほか、属人化していた受発注情報の共有化による内部不正防止や統制にも役立ちます。
NEWJI DX
製造業に特化したデジタルトランスフォーメーション(DX)の実現を目指す請負開発型のコンサルティングサービスです。AI、iPaaS、および先端の技術を駆使して、製造プロセスの効率化、業務効率化、チームワーク強化、コスト削減、品質向上を実現します。このサービスは、製造業の課題を深く理解し、それに対する最適なデジタルソリューションを提供することで、企業が持続的な成長とイノベーションを達成できるようサポートします。
製造業ニュース解説
製造業、主に購買・調達部門にお勤めの方々に向けた情報を配信しております。
新任の方やベテランの方、管理職を対象とした幅広いコンテンツをご用意しております。
お問い合わせ
コストダウンが利益に直結する術だと理解していても、なかなか前に進めることができない状況。そんな時は、newjiのコストダウン自動化機能で大きく利益貢献しよう!
(β版非公開)