- お役立ち記事
- Basics of noise and vibration in fluid machinery and examples of countermeasures
月間77,185名の
製造業ご担当者様が閲覧しています*
*2025年2月28日現在のGoogle Analyticsのデータより
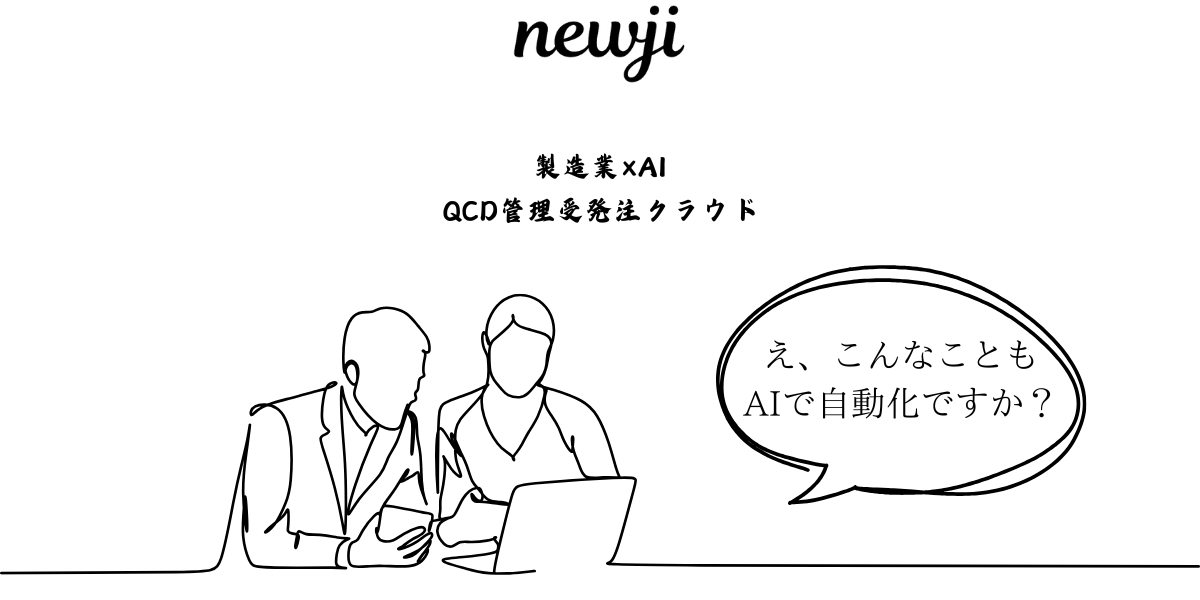
Basics of noise and vibration in fluid machinery and examples of countermeasures
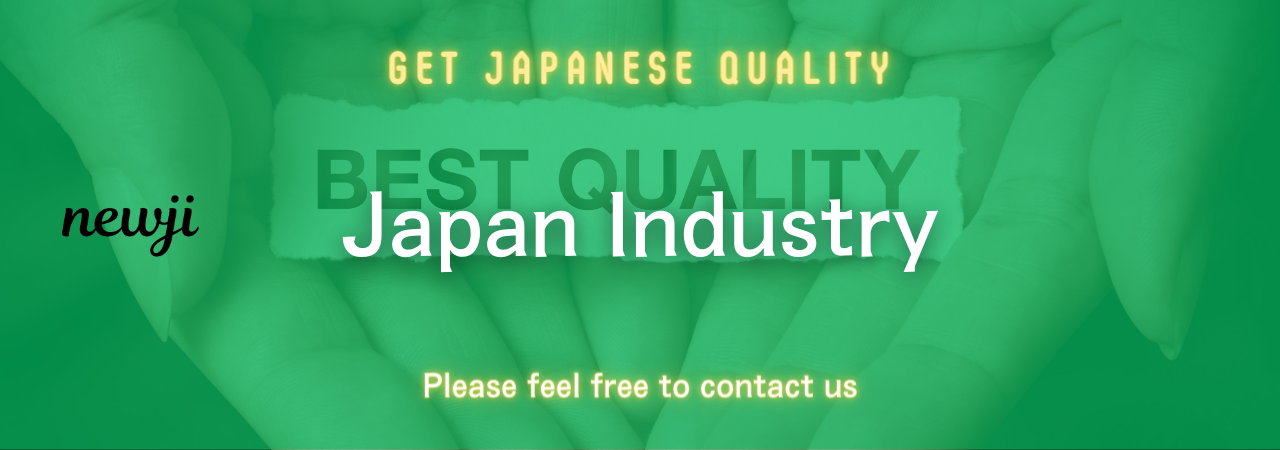
目次
Understanding Noise and Vibration in Fluid Machinery
Fluid machinery, such as pumps, compressors, and turbines, are pivotal in various industries, including manufacturing, water treatment, and energy production.
While these machines are essential for operations, they often produce noise and vibration during their functioning.
Understanding these phenomena is crucial for ensuring the machines’ efficient, safe, and long-lasting operation.
Noise and vibration in fluid machinery are often interrelated.
Noise is a byproduct of vibration, as the moving parts of the machinery interact with the fluids they manage.
The noise can range from a mild hum to a loud, disruptive clatter, affecting not only the machinery’s performance but also the working environment.
Vibration, on the other hand, refers to the oscillatory motion that results from unbalanced forces within the machine.
This motion can lead to excessive wear and tear, leading to maintenance issues and potentially costly downtimes.
Causes of Noise and Vibration in Fluid Machinery
The causes of noise and vibration in fluid machinery are often multifaceted, stemming from various mechanical, hydraulic, and aerodynamic factors.
Mechanical Causes
Mechanically, imbalance in the moving parts is a primary source of vibration.
Even a small deviation in the balance can result in substantial vibration, especially at high rotational speeds.
Misalignment of components, such as shafts and bearings, can also lead to noise and vibration.
Additionally, wear and damage over time may cause loosened parts to rattle or vibrate more significantly.
Hydraulic Causes
Hydraulically, phenomena like cavitation can contribute to noise and vibration.
Cavitation occurs when vapor bubbles form in the fluid due to pressure differences and collapse rapidly, creating a significant noise and impact on the machinery surfaces.
Sudden shifts in flow rate or pressure can also lead to turbulent water flows, which may increase vibration and the associated noise levels.
Aerodynamic Causes
Aerodynamic factors can include pressure pulsations and improper flow distributions.
In compressors and fans, the air or gas can cause repetitive vibrations if it does not flow evenly across blades or vanes, leading to increased noise levels.
Impact of Noise and Vibration
The impact of noise and vibration extends beyond the immediate concerns of machine efficiency and workplace comfort.
Operational Efficiency
Prolonged vibration can lead to inefficiencies, as the machine may require more power to perform its intended functions.
This inefficiency can increase operational costs in terms of both energy consumption and maintenance needs.
Structural Damage
Constant, unchecked vibration can also lead to structural damage over time.
This damage could result in cracked components, bearing failures, or even catastrophic machine failures if not properly managed.
Health and Safety Hazards
Finally, noise pollution can have considerable health impacts on workers, potentially leading to hearing loss if exposure is prolonged.
Additionally, excessive vibration can lead to safety risks if it affects the stability of the machinery or its mounting structure.
Countermeasures for Noise and Vibration
Implementing countermeasures to deal with noise and vibration is crucial for the longevity and effectiveness of fluid machinery.
Proper Maintenance Practices
Regular maintenance is perhaps the most straightforward approach to controlling noise and vibration.
Ensuring all components are aligned, balanced, and in good working condition is essential.
Periodic inspections can help detect early signs of wear or imbalance before they evolve into larger issues.
Design Improvements
Engineering the machinery with advanced designs can also help in reducing noise and vibration.
Features like dampers, flexible couplings, and insulated linings can significantly reduce transmission of vibrations through mechanical structures.
Additionally, computer-aided design (CAD) tools can simulate flow dynamics, enabling engineers to optimize for minimal vibration and noise.
Use of Vibration Isolators
Vibration isolators can be installed to physically separate the machinery from other structures, thereby reducing the transmission of vibration.
These isolators can be in the form of springs, rubber pads, or other flexible materials that absorb and dissipate vibratory energy.
Soundproof Enclosures
Using soundproof enclosures can also mitigate noise levels drastically.
These enclosures are designed to encapsulate the machinery, often using materials that absorb or block sound effectively.
Additionally, such designs can help in maintaining a controlled environment around the equipment, preserving it from dust and other potential contaminants.
Conclusion
Understanding and mitigating noise and vibration in fluid machinery is crucial for operational success.
It involves a comprehensive approach that includes maintenance, advanced design, and effective isolation measures.
By addressing these challenges, industries can enhance the efficiency, safety, and longevity of their equipment, leading to better performance and reduced operational costs.
資料ダウンロード
QCD管理受発注クラウド「newji」は、受発注部門で必要なQCD管理全てを備えた、現場特化型兼クラウド型の今世紀最高の受発注管理システムとなります。
ユーザー登録
受発注業務の効率化だけでなく、システムを導入することで、コスト削減や製品・資材のステータス可視化のほか、属人化していた受発注情報の共有化による内部不正防止や統制にも役立ちます。
NEWJI DX
製造業に特化したデジタルトランスフォーメーション(DX)の実現を目指す請負開発型のコンサルティングサービスです。AI、iPaaS、および先端の技術を駆使して、製造プロセスの効率化、業務効率化、チームワーク強化、コスト削減、品質向上を実現します。このサービスは、製造業の課題を深く理解し、それに対する最適なデジタルソリューションを提供することで、企業が持続的な成長とイノベーションを達成できるようサポートします。
製造業ニュース解説
製造業、主に購買・調達部門にお勤めの方々に向けた情報を配信しております。
新任の方やベテランの方、管理職を対象とした幅広いコンテンツをご用意しております。
お問い合わせ
コストダウンが利益に直結する術だと理解していても、なかなか前に進めることができない状況。そんな時は、newjiのコストダウン自動化機能で大きく利益貢献しよう!
(β版非公開)