- お役立ち記事
- Basics of non-destructive testing technology and its application to welded structures and points to keep in mind
月間77,185名の
製造業ご担当者様が閲覧しています*
*2025年2月28日現在のGoogle Analyticsのデータより
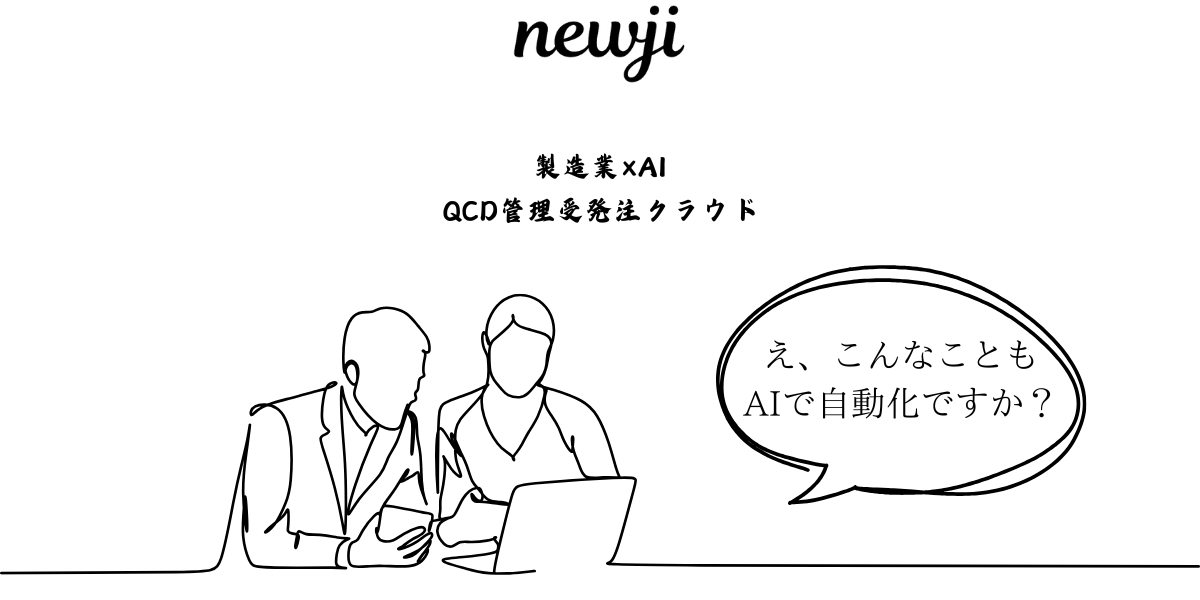
Basics of non-destructive testing technology and its application to welded structures and points to keep in mind
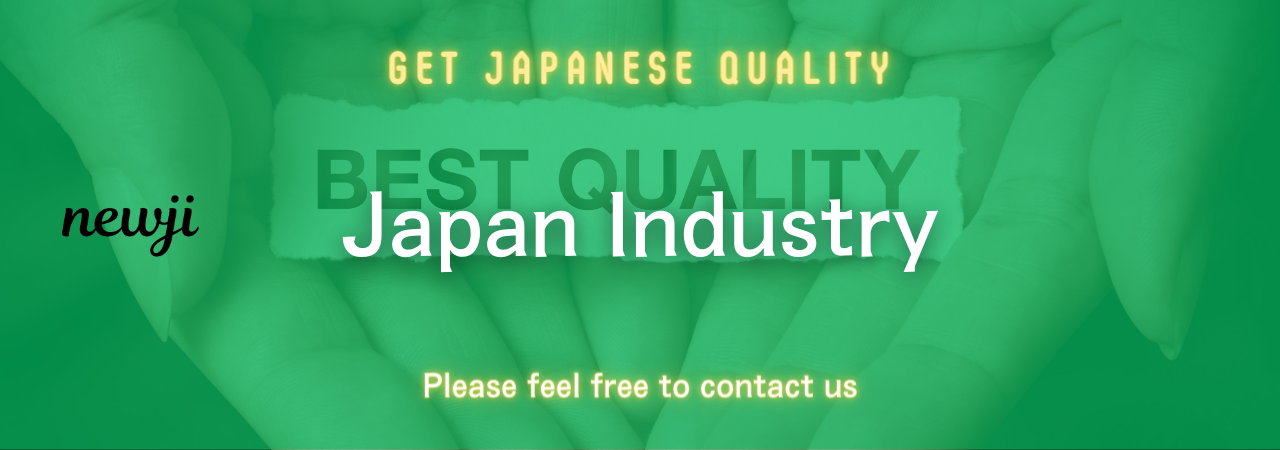
目次
Understanding Non-Destructive Testing
Non-destructive testing (NDT) is an essential approach in various industries, especially when it comes to ensuring the integrity and safety of welded structures.
Unlike destructive testing methods, NDT does not damage or alter the material being examined, making it an invaluable tool for quality assurance.
It uses various techniques to inspect, test, and evaluate materials, components, and assemblies for discontinuities, differences in material properties, and other imperfections without causing damage.
NDT plays a crucial role in maintaining the safety and reliability of structures and systems.
This testing is particularly important in the construction, manufacturing, and maintenance of welded structures, which are frequently subject to stress and wear.
Common Non-Destructive Testing Techniques
There are several NDT techniques employed depending on the material and the specific industrial requirements.
Here are some of the most commonly used methods:
Visual Inspection
Visual inspection is the simplest form of NDT.
It involves examining a structure or component with the naked eye or using magnifying lenses and other optical tools.
Though basic, it is an effective first step in identifying obvious defects or areas of concern.
Ultrasonic Testing
Ultrasonic testing involves sending high-frequency sound waves into a material to detect internal flaws or to characterize the material.
When these sound waves encounter a boundary inside the material, such as a crack or void, they are reflected back, allowing technicians to identify potential issues.
Radiographic Testing
Radiographic testing uses X-rays or gamma rays to produce an image of the interior structure of a component.
By examining the resulting images, technicians can detect a wide range of defects, such as cracks, voids, and inclusions.
Magnetic Particle Testing
This method is used to detect surface and near-surface defects in ferromagnetic materials.
The process involves magnetizing the specimen and applying ferrous particles to the surface.
Any discontinuity in the material will cause a disturbance in the magnetic field, attracting the particles and revealing the flaw.
Liquid Penetrant Testing
Liquid penetrant testing is used to detect surface-breaking defects in non-porous materials.
A penetrating liquid is applied to the surface, allowed to seep into cracks or other defects, and then removed.
A developer is then applied that draws out the penetrant trapped in the defects, making them visible.
Eddy Current Testing
Eddy current testing is used for the inspection of conductive materials.
This method employs electromagnetic induction to detect flaws and can also be used to measure material thickness and conductivity.
Applications in Welded Structures
Non-destructive testing is critical in the inspection of welded structures across various industries.
Here are some of the key areas where NDT is applied:
Quality Control and Assurance
NDT is used during and after the fabrication of welded structures to ensure that they meet required standards and specifications.
By detecting defects early, it helps in maintaining high quality and safety standards in construction and manufacturing.
Predictive Maintenance
Regular NDT inspections help in predicting potential failures in welded structures.
This predictive maintenance allows for repairs or replacements before a complete breakdown occurs, reducing downtime and saving on costs.
Safety and Compliance
By ensuring that welded structures are free from critical defects, NDT helps in complying with safety regulations and standards.
It helps in preventing accidents and ensuring the safety of both the structure and the people around it.
Points to Keep in Mind
While non-destructive testing offers numerous advantages, there are important considerations when using these techniques:
Choosing the Right Method
Different NDT methods are suited for different materials and types of defects.
It’s crucial to select the appropriate technique for the specific application to ensure accurate results.
Qualified Personnel
The accuracy and reliability of NDT results are highly dependent on the skill and experience of the technicians conducting the tests.
Personnel must be well-trained and certified in the specific NDT methods they are using.
Environmental Conditions
The environment in which NDT is conducted can affect the accuracy of the results.
Factors such as temperature, humidity, and the presence of contaminants should be considered and controlled where possible.
Limitations of Techniques
Each NDT method has its limitations and may not detect all types of defects.
Often, a combination of methods is used to achieve comprehensive inspection and evaluation.
Conclusion
Non-destructive testing is an indispensable part of modern industrial practices, especially for the inspection of welded structures.
Its ability to identify defects without causing damage ensures that components and assemblies meet safety and quality standards.
By understanding the different NDT techniques and their appropriate applications, industries can maintain high levels of efficiency, safety, and reliability in their operations.
資料ダウンロード
QCD管理受発注クラウド「newji」は、受発注部門で必要なQCD管理全てを備えた、現場特化型兼クラウド型の今世紀最高の受発注管理システムとなります。
ユーザー登録
受発注業務の効率化だけでなく、システムを導入することで、コスト削減や製品・資材のステータス可視化のほか、属人化していた受発注情報の共有化による内部不正防止や統制にも役立ちます。
NEWJI DX
製造業に特化したデジタルトランスフォーメーション(DX)の実現を目指す請負開発型のコンサルティングサービスです。AI、iPaaS、および先端の技術を駆使して、製造プロセスの効率化、業務効率化、チームワーク強化、コスト削減、品質向上を実現します。このサービスは、製造業の課題を深く理解し、それに対する最適なデジタルソリューションを提供することで、企業が持続的な成長とイノベーションを達成できるようサポートします。
製造業ニュース解説
製造業、主に購買・調達部門にお勤めの方々に向けた情報を配信しております。
新任の方やベテランの方、管理職を対象とした幅広いコンテンツをご用意しております。
お問い合わせ
コストダウンが利益に直結する術だと理解していても、なかなか前に進めることができない状況。そんな時は、newjiのコストダウン自動化機能で大きく利益貢献しよう!
(β版非公開)