- お役立ち記事
- Basics of parts design applying fluid mechanics that new employees in the design department of the precision machinery industry should know.
Basics of parts design applying fluid mechanics that new employees in the design department of the precision machinery industry should know.
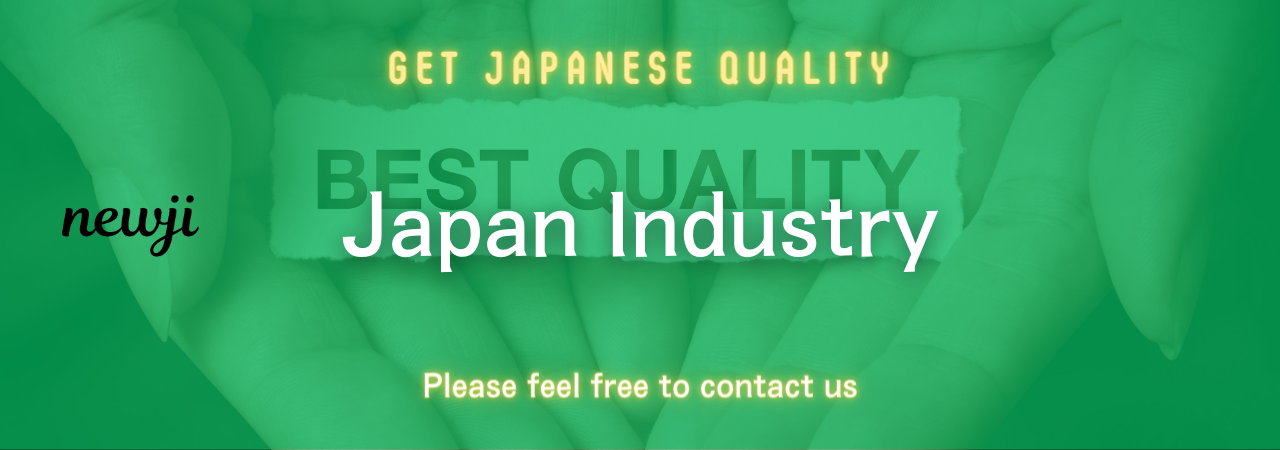
Understanding Fluid Mechanics in Precision Machinery Design
Fluid mechanics is a fundamental aspect of precision machinery design.
For new employees in the design department, grasping the basics of how fluids behave and interact with various components is crucial.
This knowledge will enable them to design more efficient and effective parts, contributing significantly to the overall performance of machinery.
What is Fluid Mechanics?
Fluid mechanics is the study of fluids (liquids and gases) and the forces acting on them.
In the context of precision machinery, it involves understanding how these fluids move through and around components.
This can affect the performance, efficiency, and durability of the machinery.
There are two primary branches of fluid mechanics:
Hydrodynamics, which deals with the motion of fluids, and Hydrostatics, which focuses on fluids at rest.
Both are crucial in designing machinery components that will operate seamlessly under various conditions.
Why Fluid Mechanics Matters in Design
Fluid mechanics is vital in designing machinery parts for several reasons.
First, it helps in optimizing performance by ensuring that components interact efficiently with fluids, thus reducing energy losses.
Second, it enhances the durability of components by minimizing wear and tear caused by fluid flow.
Finally, understanding fluid mechanics is crucial for ensuring the safety and reliability of machinery, as it helps prevent issues such as cavitation and fluid-induced vibration.
Key Concepts in Fluid Mechanics
To effectively apply fluid mechanics in design, new employees should become familiar with several key concepts:
1. **Viscosity**: This refers to a fluid’s resistance to flow.
In precision machinery, selecting fluids with appropriate viscosities is critical for minimizing friction and wear.
2. **Density**: The mass of a fluid per unit volume.
Designers must account for fluid density when calculating fluid forces and pressures within components.
3. **Flow Rate**: The volume of fluid passing through a component per unit time.
Optimizing flow rates can enhance machinery performance and efficiency.
4. **Pressure**: The force exerted by a fluid per unit area.
Designers must ensure components can withstand the expected pressures to avoid failures.
5. **Reynolds Number**: A dimensionless number that helps predict flow patterns in different fluid flow situations.
It distinguishes between laminar and turbulent flow, which can significantly impact component design.
Applying Fluid Mechanics in Parts Design
When designing parts for precision machinery, incorporating fluid mechanics involves several steps:
1. **Analyzing Fluid Requirements**: Determine the type of fluid the machinery will encounter, such as air, water, or oil.
Understanding the fluid’s properties is essential for selecting suitable materials and designing effective components.
2. **Simulating Fluid Flow**: Use computational fluid dynamics (CFD) software to model how fluid will flow through and around components.
This can help predict potential issues and optimize design before actual manufacturing.
3. **Testing Prototypes**: Create and test physical prototypes to validate CFD simulations and ensure the design performs as expected under real-world conditions.
4. **Iterating Design Based on Feedback**: Use data from simulations and testing to refine the design, ensuring it meets performance, efficiency, and durability requirements.
Challenges in Applying Fluid Mechanics
While fluid mechanics is crucial for designing effective machinery parts, it also presents several challenges:
1. **Complex Calculations**: Fluid dynamics involves complex mathematical equations, making it difficult for new designers to grasp initially.
Utilizing software tools and seeking guidance from experienced colleagues can help mitigate this challenge.
2. **Balancing Competing Requirements**: Designers often need to balance performance, efficiency, and durability requirements, which can be difficult when incorporating fluid mechanics.
3. **Adapting to New Technologies**: As technology evolves, designers must stay updated with the latest tools and techniques in fluid mechanics to remain competitive.
Conclusion
Understanding the basics of fluid mechanics is essential for new employees in the design department of the precision machinery industry.
By mastering key concepts and applying them effectively in parts design, they can create machinery that is efficient, durable, and reliable.
While challenges exist, leveraging tools like CFD software and learning from experienced colleagues can make the process more manageable.
Through continuous learning and adaptation, new designers can significantly impact the industry, contributing to the development of cutting-edge machinery and components.
資料ダウンロード
QCD調達購買管理クラウド「newji」は、調達購買部門で必要なQCD管理全てを備えた、現場特化型兼クラウド型の今世紀最高の購買管理システムとなります。
ユーザー登録
調達購買業務の効率化だけでなく、システムを導入することで、コスト削減や製品・資材のステータス可視化のほか、属人化していた購買情報の共有化による内部不正防止や統制にも役立ちます。
NEWJI DX
製造業に特化したデジタルトランスフォーメーション(DX)の実現を目指す請負開発型のコンサルティングサービスです。AI、iPaaS、および先端の技術を駆使して、製造プロセスの効率化、業務効率化、チームワーク強化、コスト削減、品質向上を実現します。このサービスは、製造業の課題を深く理解し、それに対する最適なデジタルソリューションを提供することで、企業が持続的な成長とイノベーションを達成できるようサポートします。
オンライン講座
製造業、主に購買・調達部門にお勤めの方々に向けた情報を配信しております。
新任の方やベテランの方、管理職を対象とした幅広いコンテンツをご用意しております。
お問い合わせ
コストダウンが利益に直結する術だと理解していても、なかなか前に進めることができない状況。そんな時は、newjiのコストダウン自動化機能で大きく利益貢献しよう!
(Β版非公開)