- お役立ち記事
- Basics of PID control and application and practice to PID control system design using Simulink
月間77,185名の
製造業ご担当者様が閲覧しています*
*2025年2月28日現在のGoogle Analyticsのデータより
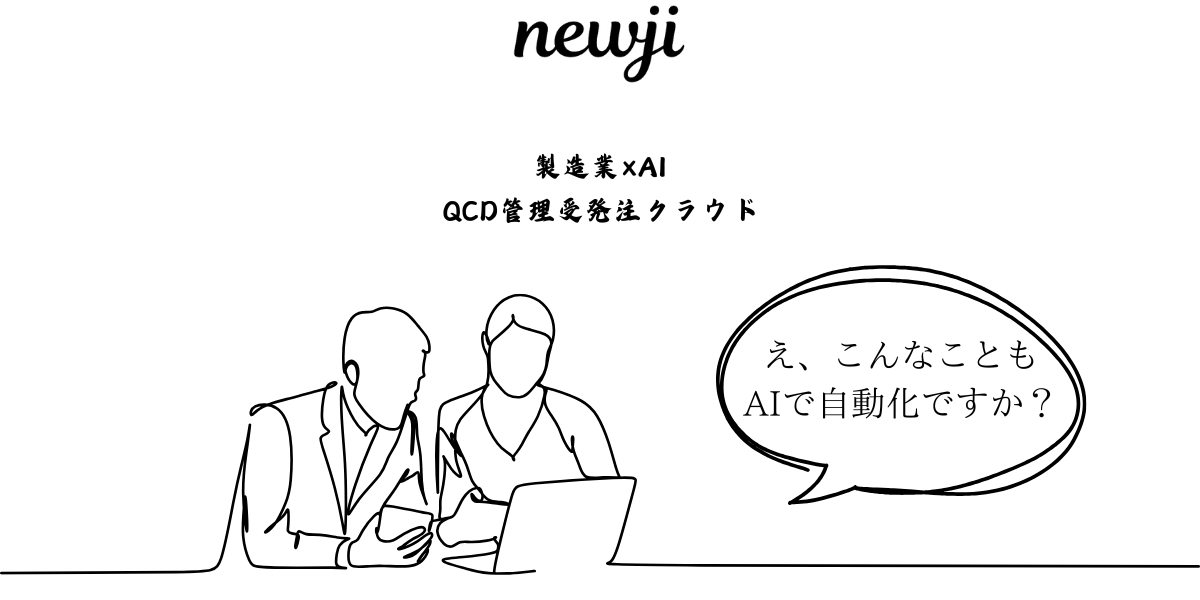
Basics of PID control and application and practice to PID control system design using Simulink
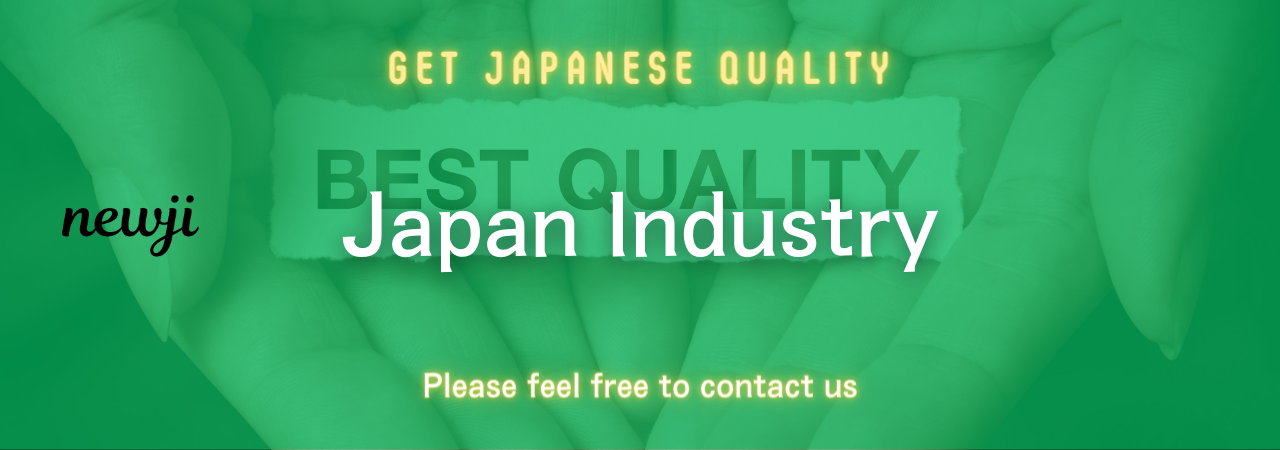
目次
Understanding PID Control
PID control stands for Proportional-Integral-Derivative control, a control loop mechanism that uses feedback to maintain the desired process state.
It is widely used in industrial control systems to maintain the desired process output level by adjusting control inputs.
The three components of PID control work together to achieve this goal.
The proportional component deals with present values of the error, the integral sums up past errors, and the derivative predicts future errors.
This combination allows PID controllers to provide stable and accurate control in a variety of applications.
Components of PID Control
The three components of a PID controller serve distinct functions and are tuned to work harmoniously.
– **Proportional (P) Control:** The proportional component gives a control signal directly proportional to the error, which is the difference between a setpoint and a process variable.
The gain factor, known as the proportional gain, determines the magnitude of the correction applied.
– **Integral (I) Control:** The integral component considers the cumulative sum of past errors over time.
It focuses on eliminating the residual steady-state error that the proportional control alone cannot eliminate.
By applying corrections based on the area under the error graph, integral control brings the process to its desired state over time.
– **Derivative (D) Control:** The derivative component anticipates future errors based on the rate of change of error.
By reacting to the trend of the error, it stabilizes the controller and reduces the overshoot.
Derivative control can be especially useful in systems where sudden changes occur or where quick stabilization is required.
How PID Control is Used
PID controllers are deployed in various industries, from simple household appliances to complex industrial processes.
Their ability to accurately maintain control makes them indispensable in numerous applications.
Industrial Automation
In manufacturing, PID controllers help automate processes such as temperature control in furnaces, controlling conveyor belt speeds, and regulating liquid levels in tanks.
A PID controller ensures that these processes remain efficient and consistent, leading to higher productivity and reduced waste.
Robotics
Robotic systems use PID control to regulate motor positions and speed.
By maintaining precise control over these parameters, robots can perform complex tasks with high accuracy and repeatability.
Aerospace
Control systems in aerospace engineering, such as those responsible for aircraft flight stability and autopilot functions, frequently rely on PID controllers.
Here, precision is critical to ensure safe and smooth operation under varying conditions.
Automotive Applications
PID control systems are integral to modern automotive technologies, including cruise control, anti-lock braking systems, and engine management systems.
These applications require exacting control to achieve optimal performance.
Designing a PID Control System with Simulink
Simulink, a MATLAB-based graphical programming environment, offers powerful tools for designing and tuning PID control systems.
Simulink Environment
Simulink allows engineers to model, simulate, and analyze dynamic systems.
Its block-based design interface makes it accessible, especially for beginners, while offering advanced features for seasoned engineers.
Building the Control Model
To begin designing a PID control system in Simulink, users can drag and drop blocks to represent the system’s components.
These might include plant models, input signals, and feedback loops.
The software provides a PID Controller block, making it straightforward to incorporate PID control into any model.
Tuning the PID Controller
Tuning involves adjusting the proportional, integral, and derivative coefficients to achieve desired system behavior.
Simulink offers automated tuning features that utilize optimization algorithms to find the best parameters quickly.
Users can also manually tune the controller by simulating the system and adjusting the values to observe the effects on system response.
Applications and Practice
Getting proficient at using PID controllers, particularly through simulation tools like Simulink, elevates one’s capability to manage and optimize industrial processes.
Experimentation and Learning
Practicing with Simulink enables learners to intuitively understand the impacts of each controller component. They can experiment by simulating different scenarios and observing system behaviors.
This practice expands one’s ability to design effective control strategies across various applications.
Real-World Problem Solving
Simulating PID control applications helps in refining skills for real-world problem-solving. As students and professionals practice, they gain insights that can be applied directly to real machinery and operations.
This translates into improved system designs and efficiencies that greatly benefit industries reliant on precise process control.
In summary, understanding and implementing PID control is pivotal for those involved in dynamic system design. Through tools like Simulink, the intricacies of PID control become more accessible, facilitating better system design and optimization across countless applications.
資料ダウンロード
QCD管理受発注クラウド「newji」は、受発注部門で必要なQCD管理全てを備えた、現場特化型兼クラウド型の今世紀最高の受発注管理システムとなります。
ユーザー登録
受発注業務の効率化だけでなく、システムを導入することで、コスト削減や製品・資材のステータス可視化のほか、属人化していた受発注情報の共有化による内部不正防止や統制にも役立ちます。
NEWJI DX
製造業に特化したデジタルトランスフォーメーション(DX)の実現を目指す請負開発型のコンサルティングサービスです。AI、iPaaS、および先端の技術を駆使して、製造プロセスの効率化、業務効率化、チームワーク強化、コスト削減、品質向上を実現します。このサービスは、製造業の課題を深く理解し、それに対する最適なデジタルソリューションを提供することで、企業が持続的な成長とイノベーションを達成できるようサポートします。
製造業ニュース解説
製造業、主に購買・調達部門にお勤めの方々に向けた情報を配信しております。
新任の方やベテランの方、管理職を対象とした幅広いコンテンツをご用意しております。
お問い合わせ
コストダウンが利益に直結する術だと理解していても、なかなか前に進めることができない状況。そんな時は、newjiのコストダウン自動化機能で大きく利益貢献しよう!
(β版非公開)