- お役立ち記事
- Basics of PID control and design practice using Simulink
月間76,176名の
製造業ご担当者様が閲覧しています*
*2025年3月31日現在のGoogle Analyticsのデータより
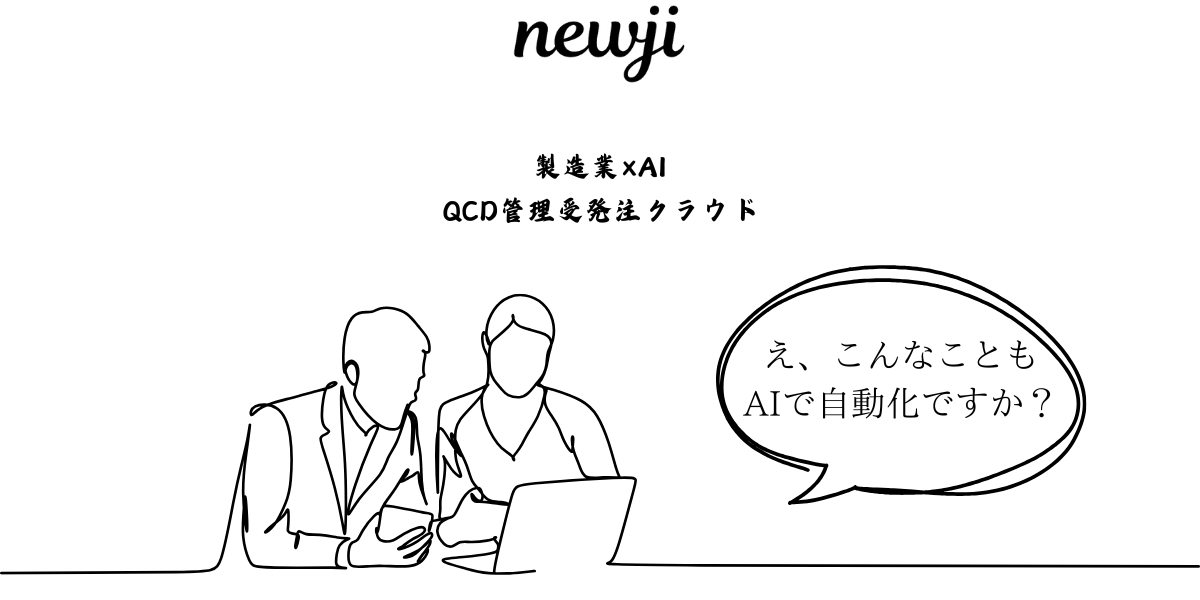
Basics of PID control and design practice using Simulink
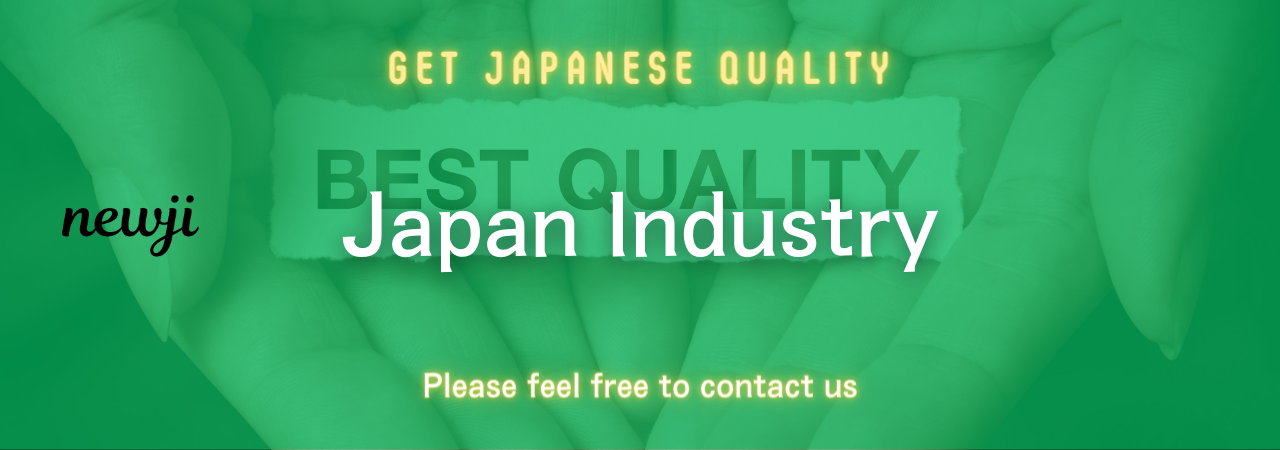
目次
Understanding PID Control
PID control is an essential concept in the field of control systems.
It stands for Proportional-Integral-Derivative control, which are the three fundamental operations used to maintain a desired setpoint in a dynamic system.
PID controllers are widely used in industrial control systems to manage processes such as temperature, speed, and flow.
The proportional component of PID control refers to the correction applied in proportion to the error.
The error is the difference between the desired setpoint and the actual value.
The proportional control generates an output that is directly proportional to this error, which helps to correct the deviation.
The integral component addresses the issue of accumulated past errors.
By integrating the error over time, this component eliminates the steady-state error and ensures the system reaches the setpoint.
Finally, the derivative component predicts future errors based on the rate of change.
It creates a damping effect by counteracting rapid changes, improving system stability and reducing overshoot.
Why Use PID Control?
PID control offers several advantages, making it a popular choice for various applications.
Its simplicity allows for easy implementation in different systems.
PID controllers are adaptable to different requirements and can be fine-tuned for optimal performance.
Additionally, PID control provides precise control with a balance between response time and stability.
This control method is ideal for systems that require steady-state accuracy and prompt response to changes.
Designing PID Controllers with Simulink
Simulink, a part of MATLAB, is a powerful simulation tool for designing, testing, and implementing control systems like PID controllers.
It provides an interactive graphical environment to model dynamic systems.
To design a PID controller in Simulink, begin by constructing a model of your process.
This typically involves representing your system with transfer functions or state-space models.
Simulink’s extensive library offers predefined blocks that can help model various components of your system.
Step-by-Step Guide to PID Design Using Simulink
1. **Set Up Your Simulink Model:** Open Simulink and start a new model.
Add blocks representing your system, including inputs, outputs, and any necessary system dynamics.
2. **Include the PID Controller Block:** From the Simulink library, drag and drop the PID controller block into your model.
This block allows you to configure the proportional, integral, and derivative parameters.
3. **Define Your System Parameters:** Identify and configure the parameters of your system, such as sensors, actuators, and the process being controlled.
Provide the necessary details for Simulink to accurately simulate system behavior.
4. **Open Loop Response Analysis:** Test your system’s open-loop response to understand how it reacts without any control.
This analysis helps determine the initial tuning of the PID parameters.
5. **Tuning the PID Parameters:** The key to effective PID control is tuning the parameters.
Begin with heuristic methods like Ziegler-Nichols or trial-and-error to set initial values for proportional, integral, and derivative gains.
Simulink offers tools such as PID Tuner that can assist with tuning by automatically adjusting parameters based on system response.
6. **Simulate Closed Loop Response:** Once the PID parameters are set, run a closed-loop simulation.
Simulink provides detailed plots of system responses, enabling you to analyze how well the PID controller maintains the setpoint.
7. **Refinement and Testing:** Refine the PID settings based on simulation results to ensure optimal performance.
Test the controller under various conditions and disturbances to verify its robustness and stability.
Benefits of Using Simulink for PID Design
Simulink offers a multitude of benefits for designing PID controllers.
Its user-friendly interface allows for efficient model creation and easy adjustments to system parameters.
The visual representation of models helps in understanding the interaction between different components.
Moreover, the real-time feedback from simulations provides insights into system performance, facilitating quick modifications.
Simulink’s integration with MATLAB enables access to comprehensive data analysis and visualization tools, further enhancing design accuracy.
Real-World Applications of PID Control
PID control can be found in various sectors due to its adaptability and effectiveness.
In the automotive industry, it is used for cruise control systems, enabling vehicles to maintain a constant speed despite changes in terrain.
Manufacturing processes benefit from PID control in maintaining optimal temperatures and pressures, ensuring product quality.
In the aerospace sector, PID controllers help regulate altitude and stabilize aircraft during flight.
Process industries like chemical and pharmaceutical manufacturing use PID control for precise regulation of chemical reactions.
Challenges and Limitations of PID Control
Despite its advantages, PID control has some limitations.
It requires an accurate model of the system being controlled, which can be complex and time-consuming to develop.
Systems that are highly non-linear or have rapidly changing dynamics may not perform well with PID control.
Furthermore, without proper tuning, PID controllers can lead to overshoot, oscillations, or instability.
Hence, continuous monitoring and adjustment are necessary to maintain desired performance.
In conclusion, understanding the principles of PID control and leveraging tools like Simulink are crucial for designing effective control systems.
The adaptability and precision of PID controllers make them an indispensable tool in various industries, offering solutions to complex control challenges.
資料ダウンロード
QCD管理受発注クラウド「newji」は、受発注部門で必要なQCD管理全てを備えた、現場特化型兼クラウド型の今世紀最高の受発注管理システムとなります。
ユーザー登録
受発注業務の効率化だけでなく、システムを導入することで、コスト削減や製品・資材のステータス可視化のほか、属人化していた受発注情報の共有化による内部不正防止や統制にも役立ちます。
NEWJI DX
製造業に特化したデジタルトランスフォーメーション(DX)の実現を目指す請負開発型のコンサルティングサービスです。AI、iPaaS、および先端の技術を駆使して、製造プロセスの効率化、業務効率化、チームワーク強化、コスト削減、品質向上を実現します。このサービスは、製造業の課題を深く理解し、それに対する最適なデジタルソリューションを提供することで、企業が持続的な成長とイノベーションを達成できるようサポートします。
製造業ニュース解説
製造業、主に購買・調達部門にお勤めの方々に向けた情報を配信しております。
新任の方やベテランの方、管理職を対象とした幅広いコンテンツをご用意しております。
お問い合わせ
コストダウンが利益に直結する術だと理解していても、なかなか前に進めることができない状況。そんな時は、newjiのコストダウン自動化機能で大きく利益貢献しよう!
(β版非公開)