- お役立ち記事
- Basics of PID Control and Practical Design with Simulink
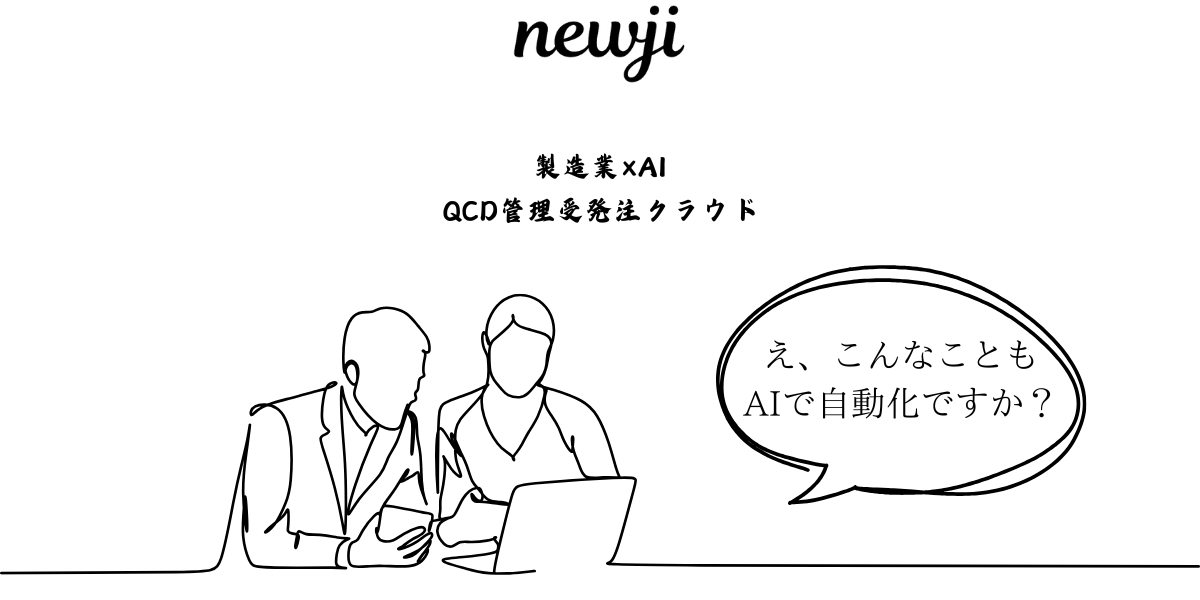
Basics of PID Control and Practical Design with Simulink
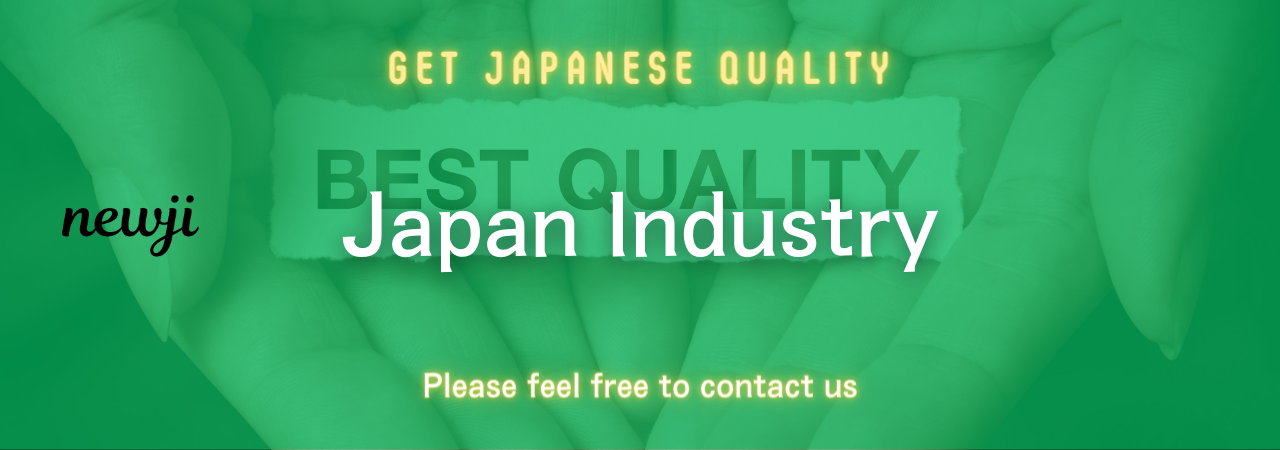
目次
Understanding PID Control
PID control is a fundamental concept in control systems engineering, playing a crucial role in maintaining stability and optimizing the performance of various mechanical and electronic systems.
PID stands for Proportional-Integral-Derivative, which are three distinct types of control used to maintain desired levels in processes or systems.
Proportional Control
The proportional component of PID control helps to reduce the overall system error.
It calculates the error by measuring the difference between a setpoint (desired level) and the current process variable (actual level).
The controller then multiplies this error by a pre-determined proportional gain to modify the output.
The primary advantage of proportional control lies in its ability to respond quickly to changes.
However, it may not completely eliminate the error, often resulting in a steady-state offset.
Integral Control
Integral control addresses the limitation of the proportional component by eliminating the steady-state error.
It integrates the error over time and adjusts the output accordingly.
This means that even small errors, accumulated over time, will eventually be corrected.
Integrating the error helps bring the system to a precise setpoint, although it may introduce instability if not properly tuned.
The integral gain needs careful adjustment to avoid oscillations or slow responses.
Derivative Control
The derivative component predicts future system behavior by calculating the rate of change of the error.
By understanding the trend of the error, derivative control can apply corrective measures preemptively.
This helps dampen potential oscillations and provides a quicker response to sudden changes.
However, derivative control can introduce a noise sensitivity issue, as it amplifies high-frequency signals due to its nature of differentiating signals.
Designing PID Controllers
When designing a PID controller, it is essential to find the appropriate balance between proportional, integral, and derivative gains to ensure the system performs optimally.
This process, known as tuning, can be quite complex and requires careful experimentation and analysis.
Tuning Methods
1. **Manual Tuning**: This involves manually adjusting the PID parameters until the desired performance is achieved.
This method requires intuition and experience but can be effective in simple systems.
2. **Ziegler-Nichols Method**: This popular method involves setting the integral and derivative gains to zero and gradually increasing the proportional gain until the system exhibits consistent oscillations.
The ultimate gain and period are then used to calculate the other PID parameters.
3. **Software Tools**: Modern software like MATLAB and Simulink offer built-in tools and algorithms for automatic tuning, providing accurate results with less trial and error.
Considerations for Effective PID Control
– **System Dynamics**: Understanding the dynamics of the system you are controlling is critical for successful PID design.
This includes knowing how the system responds to changes in input and how disturbances affect it.
– **Sampling Rate**: The rate at which the controller samples input data can impact its performance. A higher sampling rate may improve accuracy but requires more processing power.
– **Controller Limitations**: Real-world controllers have limitations such as actuator saturation and sensor noise. These should be considered during design to avoid unrealistic expectations.
Practical Design with Simulink
Simulink, an environment for multidomain simulation and Model-Based Design, is an excellent tool for designing and testing PID controllers.
It offers several features that simplify the process and enhance understanding.
Modeling with Simulink
Simulink allows you to create a visual representation of the system you want to control.
This involves building block diagrams that consist of mathematical models representing different components of the system.
You can simulate the process behavior, giving you valuable insights into how the PID controller will respond to various conditions.
PID Block in Simulink
The PID Controller block in Simulink provides an interface to configure and tune the controller easily.
It supports tuning of PID parameters using various methods and allows real-time adjustments during simulations.
Interactive Tuning
Simulink’s interactive tuning feature lets you adjust controller parameters on the fly, observing how changes impact system performance in real-time.
This is particularly useful for understanding the system’s response to different tuning strategies without restarting the simulation each time.
Testing and Validation
Once the PID controller is designed, you can validate its performance against different scenarios, such as setpoint changes or disturbances.
Simulink enables you to test the robustness of the controller, ensuring it can handle real-world challenges.
Conclusion
Mastering PID control is essential for anyone involved in control systems engineering, and practical design with tools like Simulink can significantly simplify this process.
By understanding the components of PID control and employing effective tuning methods, engineers can create systems that operate efficiently and accurately.
Simulink enhances this capability by offering a flexible and intuitive environment for modeling, simulating, and optimizing PID controllers, leading to better control solutions in industrial and academic applications.
With a properly tuned PID controller, systems can achieve desired performance, ensuring stability and reliability across various applications.
資料ダウンロード
QCD調達購買管理クラウド「newji」は、調達購買部門で必要なQCD管理全てを備えた、現場特化型兼クラウド型の今世紀最高の購買管理システムとなります。
ユーザー登録
調達購買業務の効率化だけでなく、システムを導入することで、コスト削減や製品・資材のステータス可視化のほか、属人化していた購買情報の共有化による内部不正防止や統制にも役立ちます。
NEWJI DX
製造業に特化したデジタルトランスフォーメーション(DX)の実現を目指す請負開発型のコンサルティングサービスです。AI、iPaaS、および先端の技術を駆使して、製造プロセスの効率化、業務効率化、チームワーク強化、コスト削減、品質向上を実現します。このサービスは、製造業の課題を深く理解し、それに対する最適なデジタルソリューションを提供することで、企業が持続的な成長とイノベーションを達成できるようサポートします。
オンライン講座
製造業、主に購買・調達部門にお勤めの方々に向けた情報を配信しております。
新任の方やベテランの方、管理職を対象とした幅広いコンテンツをご用意しております。
お問い合わせ
コストダウンが利益に直結する術だと理解していても、なかなか前に進めることができない状況。そんな時は、newjiのコストダウン自動化機能で大きく利益貢献しよう!
(Β版非公開)